
Benchmarking is defined as measuring something against a standard. For material recovery facilities (MRFs), how do operators ensure the equipment and workers who help to sort and move materials through the facility are working to the best of their abilities? Prior to any installation or upgrade, what types of conversations should operators, managers and stakeholders have to guarantee such a move is necessary?
These are the types of questions Nat Egosi answers daily. As president and CEO of RRT Design & Construction, a Melville, New York-based consulting firm with significant experience in the MRF design sector, Egosi has helped hundreds of companies complete their projects over the last 25 years. (Egosi will serve as a moderator at the second annual MRF & Recycling Plant Operations Forum in Chicago Oct. 10.)
The following Q&A is an edited version of a conversation in which Egosi talks about today’s MRFs.
Recycling Today (RT): RRT has designed and completed more multimaterial recycling and MRF systems than any other firm in North America. What types of conversations are important when first considering a MRF installation/upgrade?
Nat Egosi (NE): The type of conversations in my mind immediately go right to cost justifications. The scheduled time frame of when would this installation upgrade be done. What are the specific goals and objectives? I would spend a lot of time on goals and objectives by identifying as many of the goals as possible, as many of the objectives as possible, to make sure they’re all included
After that exercise, then I’m always looking for somebody to answer the questions, “Why is this necessary?” and “What are the risks and consequences?” In other words, the inverse of what we’re trying to accomplish and what if we don’t. What are the risks with going forward with this and what are the consequences? Is there potential cost overrun? Is it a scheduling issue? What do we do with the people in the plant? And so on.
We also would like to have a conversation: What are the factors that are outside your control, “your control” meaning the person we’re having this conversation with, which may be the plant operator, the plant owner, maybe the head of maintenance, maybe the head regional maintenance manager, maybe a business development manager. What items are outside of control and what can be done to minimize their impact?
_fmt.png)
When we’re all done, we sit down and say, OK, what is the actual scope of work? What are we actually going to do? We want that to be very clear and be very comprehensive, so we can drill down to the details of do we need fire sprinkler modifications or don’t we? Do we need to get a building permit or don’t we? Do we need extra lighting or don’t we? That’s the kind of level of detail we want to get at the lowest level. At the highest level, it is what is this going to cost? How long is it going to take? And what do we expect it to do?
At the end of all that, one should step back and say, Who are the stakeholders in this effort? We are having a conversation. Maybe RRT and one or two other people. No one else is in the room. Who else are all the stakeholders? Let’s identify them all and when we should get them involved.
Finally, the last piece is what are the boundaries around this project so we don’t have a “creep factor.” Oftentimes with these installation upgrades, you start off with what you want to do and then suddenly, before you know it, other things get added, and you get what is called a creep factor. That creep factor doesn’t necessarily align with the goals and objectives, it doesn’t align with the schedule, and you get off course. It’s very important to define those boundaries in a way that they’re so clear that anybody who suggests adding anything or changing something that is on the other side of that boundary line, that would be a different project for a different day and a different time. And if it shouldn’t be on this side of the line but it is, then you didn’t do a good job defining the project.
RT: How can MRF operators ensure the equipment and processes in each section of the MRF are working efficiently from day to day? How do you ensure workers are efficient?
NE: Managers and supervisors need to walk the floor with a sole purpose. Oftentimes, managers and supervisors are tasked with doing a lot of reports, going to meetings and conference calls; they’re not walking the floor. When they do walk the floor, they’re not walking the floor with that purpose in mind, which is assessing: Is my equipment and are my people efficient today at this moment that I’m walking by them? They’re walking the floor for a different reason. They’re walking the floor to go talk to somebody or walking the floor to go check on something and literally just walking by. It’s no different than if you walk
Many managers and supervisors do exactly what I said, but there are many managers and supervisors who don’t. They’re on the floor, but they’re not there with the sole purpose of looking to see whether the workers are working efficiently.
RT: In what ways are safety and maintenance improving in facility operations?
NE: Safety has improved with better lighting and housekeeping, as well as with supervision,
An example of teamwork is telling your buddy, “Don’t do that.” Awareness is understanding by example when somebody does something that it’s likely to be a safety problem, so you want to correct it.
Maintenance has improved through the addition of better access to be able to perform maintenance and better lighting, as well as with training and awareness.
There’s quite a bit of similarity on the improvements for safety and maintenance.
There also are excellent contractors now available for outsourcing. Years ago, that wasn’t the case. The only people who knew how to fix the facilities were the people working in the facilities themselves. Now there’s just a lot of expertise out there that’s available for outsourcing.
I would also say that the failure points in a facility are well-known to an operator. Within their own facilities, they can identify the four or five trouble spots that are known to break or fail and, therefore, they can apply what’s called predictive maintenance techniques.
You’ve heard of the term preventive maintenance, where you do things to prevent failure. But there’s also a higher level of maintenance management technique, which is called predictive maintenance, where you remove something or replace something before it fails because you know if you don’t do it, it’s going to fail at some point, and that point in time may not be convenient for you. If a tire is going to wear out, you can keep putting air in the tire and checking it out, that’s preventive maintenance, but at some
You just know you need to do certain things at a certain time. And those failure points, which are known to the operator, are identified and put on the schedule and can actually be replaced, modified or fixed before they fail.
RT: What work can MRF operators do to suppress noise and dust generation?
NE: Noise is a difficult issue in a factory environment, and I use the word factory because that’s essentially what we’re doing here: We’re bringing a raw material, modifying it, changing it and then producing products that we can sell. More equipment means more noise. You want less noise, have less equipment. The equipment is all inside a building that has sheet metal walls, steel
With regard to dust, the root source of dust
How do we suppress dust? You look at any equipment that creates
I visualize taking a piece of carpet outside and knocking it with a broom to knock the dust off.
The screens that separate the paper from the containers have hundreds of stars and discs. If you look at them, they’re slapping the paper at several hundred revolutions per minute. They are the major source of dust generation. They tear, scratch, rub, scrape, rip, pull, scuff all the fibers that are on the sheet of paper. The paper is nice and smooth, but if you keep rubbing it, scuffing it and scratching it, you start loosening the fibers.
The discs themselves are intentionally designed not to be smooth but rather to be rough and irregular, and that’s how they get the containers and the paper separate.
These screens should be enclosed with negative airflow to a dust collection system, thereby limiting the dust leaving the surrounding area of the screen in an uncontrolled manner.
The alternative to all of this would be better paper separation technology.
RT: How have audits of inbound quality affected MRFs? What are they doing with this information?
NE: A variety of things. In some cases, they collect information, and they don’t know what to do with it. It’s information overload. Arriving loads are inspected, they’re sorted and the information is recorded on a piece of paper or a tablet. What the information is used for in a positive way is to educate the collector as well as to enforce the restrictions to the incoming materials. With that data, they can tell the collector, “Look, this is the data I found. This is what my incoming material requirements are; you’re not meeting my requirements, so I can now enforce a restriction to you unless you fix your problem.” And the collector now knows what they need to do because they now have the information.
The data also are used to understand the production requirements of the facility. For example, if the incoming material has a higher percentage of corrugated or contamination than what was generally expected or seen in prior time periods, then one could look at how to change the facility in such a way so it can still operate efficiently and produce the outgoing quality that’s necessary for the markets or use this information to justify capital projects, whether they need a piece of equipment or technology or they need to do a modification. That’s where this information has been helpful.
RT: New technologies are creating new market opportunities for businesses—what potential for MRFs do you see related to new equipment?
NE: The biggest potential for MRFs related to new equipment is that the commodity composition is changing dramatically, and it has continued to change since the very beginning but continues to change now with the lightening of the tons. The technology that today is in those facilities was really developed some 15, 20 years ago and, in some cases, one would say it’s not really appropriate for the next 15 to 20 years. And in as much that manufacturers talk about the new and
RT: Would you like to make a comment at all on robotics?
NE: My comment on robotics is it’s an interesting technology that is being tested in various facilities. Certain manufacturers have adopted that as part of their strategic growth area, while some other manufacturers have not. Overall, it will take many years for this technology to evolve such that the operators are really satisfied with the end results when they compare what the cost of this equipment is to not only install but also to maintain and they consider the fact that incoming material keeps changing. So, if you could justify this expense based on today, would it still be justified tomorrow if the composition of the material changes and if also you don’t hit all of those goals and objectives that you had initially.
Since there are so many questions around this, and because this industry has so little profit
RT: Talk about processing contracts and how MRFs should implement a processing fee system.
NE: This is an opinion. In my opinion, operators need to be paid for their services, which includes every aspect of their work, whatever they’re doing. The value of the incoming materials fluctuates for all the reasons. This value belongs to the collector or to the agency that controls the collection. The agency or the collector can use that value to provide for correct incentives, education to the generators and to help to defray its program costs. The operator does not need to share in that value. In reality, the operator is providing a service to convert the nonmarketable materials that are being delivered into salable commodities. So that’s my thought.
Get curated news on YOUR industry.
Enter your email to receive our newsletters.
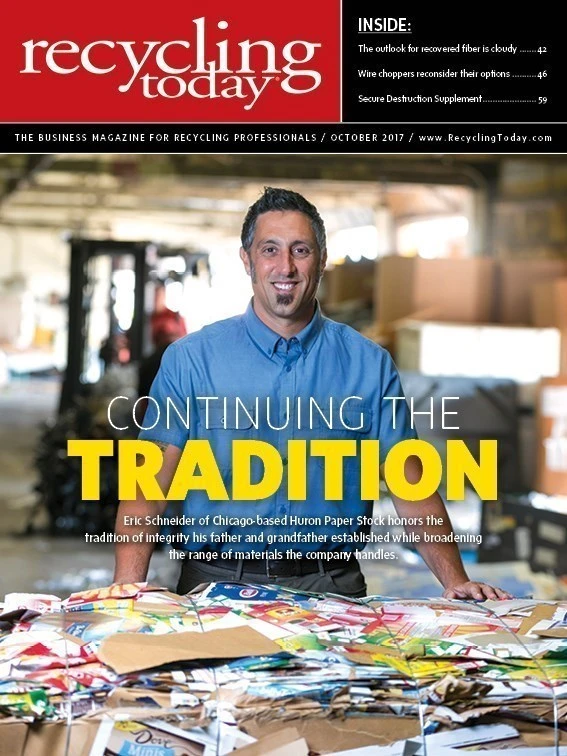
Explore the October 2017 Issue
Check out more from this issue and find your next story to read.
Latest from Recycling Today
- Joe Ursuy elected to NWRA Hall of Fame
- RRS adds to ownership team
- S3 Recycling Solutions acquires Electronics Recycling Solutions
- Nextek, Coveris to recycle food-grade plastic film
- Recyclekaro expands recycling capacity
- USTR hears comments on port fee proposal
- C&D World 2025 hits record attendance and exhibitor numbers
- Denali now offers mobile depackaging service