
When Dem-Con Cos., Shakopee, Minnesota, opened its material recovery facility (MRF) in 2013, the company wanted to ensure it incorporated the latest equipment to optimize recovery and recycling for customers. The company says it intended to serve customers from within a 1,000-mile radius of the MRF.
“We had been evaluating a MRF in our market area for several years, but there was enough capacity serving the market area prior to 2013,” says Bill Keegan, president of Dem-Con. “By 2013, we felt that the demand for processing in our market area was significant enough to warrant construction of our MRF.”
The company purchased all new equipment to use in the single-stream MRF, which officially began operating in November 2013. Almost every year since, Dem-Con has made upgrades to various areas of the MRF to keep up with the latest technology available. It added a glass cleanup system in 2015 and enhanced that system to be able to fractionate the material in 2016. Dem-Con installed a Cirrus near-infrared optical sorter from Nashville, Tennessee-based MSS, a division of the San Diego-based CP Group, on its container line to remove fiber and added an Amp Cortex Robot from Amp Robotics, Denver, to sort cartons and high-density polyethylene (HDPE) in 2017. Last year, the company installed two MSS FiberMax optical sorters to help control fiber quality.
This July, Dem-Con plans to upgrade its original MSS Aladdin optical sorter for containers to an MSS PlasticMax. “Technology is advancing very quickly,” Keegan adds. “The optical sorter we put in six years ago now is so out of date that we’re updating it.”
While the company has made tweaks and upgrades to a good deal of its equipment, two machines that haven’t changed at all are its patented IPS Conquest auto-tie baler for fiber and its patented IPS two-ram baler for containers.
Lonnie Pauly, director of MRF operations at Dem-Con, says both balers were installed when the MRF was built six years ago. He adds that neither machine has had any notable complications since the installs.
“When we bought [the balers], we sized them for growth. We knew we would grow in a two-to-five-year period.” – Bill Keegan, president, Dem-Con Cos.
“As long as you’re watching them, relining them, and you’re not doing any structural damage to them, [they will last] indefinitely,” he says of the balers.
Traditionally, balers only need replaced if capacity grows significantly or if maintenance is neglected. Keegan says the company made sure it bought balers large enough to grow with the company.
“When we bought [the balers], we sized them for growth,” Keegan adds. “We knew we would grow in a two-to-five-year period. You can also grow by staffing more hours on the baler and working more hours on it.
“Something that’s really key to the success of that baler and the longevity is the maintenance that Lonnie and his team do,” he says. “They self-perform 90-plus percent of all maintenance themselves. They really get to know the balers and can see problems coming on and fix them before they become major problems.”
Buy a baler to last
When Dem-Con was starting its single-stream MRF, the company looked at several different vendors for all the equipment that it would install—including its balers. After looking into options, Keegan says the company felt CP Group offered a good selection of equipment for the best value. (At the time, CP Group owned IPS. Avis Industrial Corp. purchased IPS from CP in 2014, and the line is now part of Harris, Cordele, Georgia.)
“It made sense to keep everything with one provider,” Keegan says of the company’s decision to purchase the IPS balers. “We liked a one-stop shop for all of our equipment needs, and we trusted our sales representatives. When looking at upgrades, we prefer to keep equipment from the same provider if possible, but we are also willing to use other providers if they can integrate their system, and if it adds a unique benefit, capability or value.”
The company uses a two-ram IPS baler for its containers and a single-ram auto-tie IPS baler for its fiber. Keegan says the single-ram auto-tie baler is faster and has more production capacity than the two-ram baler.
“The auto-tie baler has faster cycle times than a two-ram baler, especially on OCC (old corrugated containers), which was needed to meet our design capacity for the facility,” Keegan says.
Pauly says a local vendor and service provider is only 15 minutes away if the company needs anything for its balers.
Keegan adds that it’s important for Dem-Con to maintain good relationships with its equipment providers. He says the company also ensures its operators have a good understanding of the equipment.
“We believe that to have a truly successful facility, you need to work on your own equipment, understand the system and ultimately perform much of your own maintenance and repairs,” he says. “It is also important to maintain a relationship with other MRF managers in your market area and use them as a support network for maintenance and processing needs.”

Reline responsibly
When it comes to balers, Pauly says relines are one of the most important aspects of maintenance. For Dem-Con’s two balers, he says keeping up to date on relines has been the MRF’s biggest expense for the machines thus far.
Because Dem-Con’s MRF runs two full shifts, the company relines its balers a bit more frequently than MRFs that are only running a single shift.
“It goes back to the operator being vigilant on doing preventive maintenance, visually inspecting the steel and welds,” Pauly says. “If the operator notices something, we have done ultrasounds on the steel to check thickness or drilled a test hole. If the liner is getting thin, we will schedule either a partial or full reline.
“If you are not relining the balers when they need it,” he explains, “you could start wearing into the framework and structure of the baler and cause extensive damage to that and other moving parts of the baler along with extra downtime.”
For relines, Dem-Con will do some work in-house and some work through outside contractors, depending on how much manpower is needed for the job and how much downtime it can afford. Pauly says his team could do the job, but it would take much longer and would create downtime. He says, “Other maintenance we handle on our own, but with relines, that’s when you call in reinforcements to get it accomplished in a reasonable time frame.”

Maintaining and training
In addition to keeping up on relines, routine maintenance is key to making sure a baler lasts a long time. Pauly says regularly greasing the machine, filtering hydraulic oils and cleaning the tanks are important. Other considerations are sharpening and changing the shear knives and making sure operators change hold-down bars for the gathering ram as needed. Operators also must watch the machine to check for worn or cracked hydraulic hoses.
Pauly says his team must ensure it’s readily stocked on parts. He says his team can’t afford downtime, so the company has extra hydraulic pumps, motor couplers, twister hooks and knives stocked. Pauly says Dem-Con forecasts when it will need new liners as they’re more expensive.
One mistake Pauly says he sees happen with balers is either overfeeding or underfeeding the machine. With underfeeding, the machine doesn’t receive the capacity it’s designed to bale. With overfeeding, materials can jam up.
“Feeding it at even, consistent depth” is the way to go, he says. “It’s a less-is-more scenario with these balers. Let them do their thing, and they’ll perform the way you hope they will. Follow steps to a T with balers.”
Pauly says his entire team at Dem-Con has good knowledge of the balers. “The plant manager, the warehouse manager and line supervisor have all run the baler and know it inside and out,” he says. “We have three minds on-site—if they don’t know what a problem is, chances are that no one else does!”
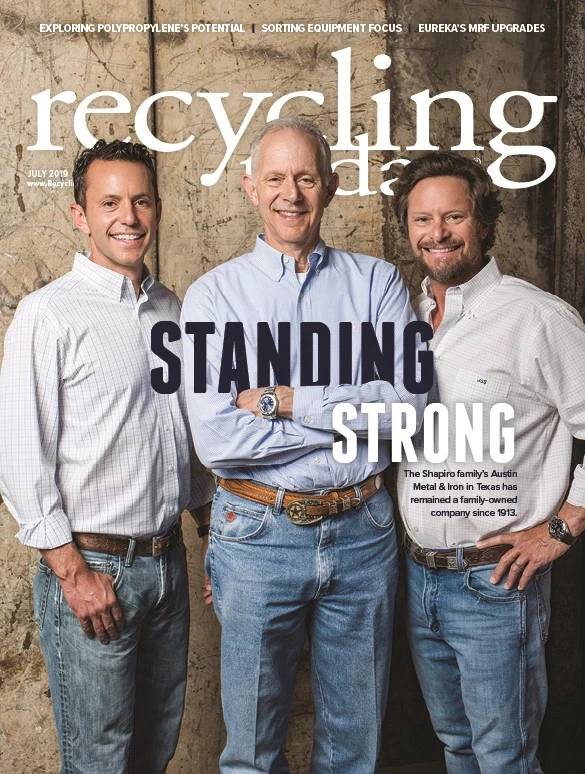
Explore the July 2019 Issue
Check out more from this issue and find your next story to read.
Latest from Recycling Today
- Ball links up with JV partner for aluminum cup operations
- Electrolux commits to recycled content
- Duesenfeld system targets battery cell scrap
- Hyundai says it will make steel in the US
- APR announces Recycling Leadership Award winners
- Glass Half Full opens glass recycling facility in Louisiana
- AmpUp partners with Roundtrip EV
- Global Recycling Day event supports Pittsburgh school's recycling efforts