Gypsum drywall is a major component of modern buildings, yet it is often one of the least likely components of debris from building construction, demolition or renovation to be recycled.
Gypsum drywall typically makes up 5 percent to 25 percent of the weight of debris from building-related C&D activities. A typical rule of thumb for drywall generation from construction activities is one pound of drywall per cubic foot of construction.
The amount of post-consumer drywall generated in Florida C&D debris in 2000 was estimated at nearly 500,000 tons. Most of this was disposed in unlined landfills. Recovery and recycling is always desired in place of land-filling when feasible, but several environmental factors (odor, groundwater contamination) create added incentive for recycling drywall.
While several gypsum drywall recycling operations exist in North America at the current time, in many areas (Florida for example) drywall recycling is relatively nonexistent. This paper describes some of the issues facing the C&D debris industry and summarizes the current state of gypsum drywall recycling in North America.
DRYWALL BASICS
Gypsum drywall, often referred to as gypsum wallboard or sheet rock, replaced gypsum plaster as the major interior wall surface because of its ease of installation and its fire resistant properties.
Gypsum drywall consists of approximately 90 percent gypsum and 10 percent paper facing and backing. Gypsum is a mineral composed of calcium sulfate (CaSO4) and water (H2O). Drywall comes in many different types and sizes to meet specific construction needs. Several specialty products are manufactured including moisture resistant drywall (greenboard) and Type X drywall. Type X drywall contains small glass fibers designed to increase the board’s ability to withstand high temperatures from fires for a longer period of time.
Drywall enters the waste stream in several different locations, including the manufacturing facility, construction sites, renovation activities, building demolitions and manufactured housing plants. At the construction site, drywall is sometimes mixed in with the rest of the debris. In other cases, the drywall subcontractors are required to manage the debris themselves. Most drywall from construction is produced during a very short period of time, a positive trait from a separation and recovery standpoint. Because of its friable nature, gypsum wallboard is very difficult to recover from mixed debris resulting from standard demolition practices. It is certainly possible (and sometimes practiced) to first strip a structure of drywall (and other building materials) prior to the demolition of structural components. Drywall is in many cases the largest component of the waste stream at a manufactured housing plant; several drywall recycling companies have developed in the vicinity of these facilities.
AT THE LANDFILL
When gypsum drywall is disposed in landfills, a series of biological and chemical reactions can occur that have the potential for adverse environmental impacts. When drywall in a landfill gets wet, some of the sulfate from the gypsum dissolves into the water. If this "leachate" reaches the groundwater, contamination with sulfate may result. Granted, sulfate is not a risk on the same magnitude as chemicals such as lead or arsenic, but high sulfate concentrations do impart negative qualities to the water.
The U.S. federal secondary drinking water standard for sulfate is 250 mg/L. Concentrations above this level have been observed in the groundwater at unlined C&D debris landfills. The sulfate also contributes to the high total dissolved solids (TDS) concentrations observed in groundwater at many C&D debris landfills.
Another issue results form the biological conversion of dissolved sulfate to hydrogen sulfide (H2S). H2S is a foul-smelling gas (often compared to rotten eggs). It is produced under wet, anaerobic conditions, such as those that often occur in landfills.
The presence of organic matter such as yard trash or cardboard is needed for the microorganisms to thrive, but even the paper on the drywall itself provides enough organic matter for the biological reactions to occur. H2S has been observed over a tremendously large concentration range at C&D debris landfills.
The human nose can detect H2S at relatively low concentrations (<0.1 part per million or ppm). H2S concentrations have commonly been measured in this range in the air above and surrounding C&D debris landfills, thus odor complaints are a common problem. Concentrations in pockets within the landfill have been measured at lethal levels (>250 ppm).
Usually by the time the gas reaches the atmosphere, it is diluted to below most currently accepted safety concentrations. Landfill operators should exercise extreme caution, however, any time undiluted C&D debris landfill gases might come in contact with a worker (e.g. excavation activities, confined spaces).
The odor problem alone has been enough to result in strict actions being required on the part of some landfill operators. Some C&D debris landfill operators have been required to install gas collection and recovery systems, and others have resorted to placing odor masking agents around their sites. In the Vancouver area, gypsum drywall was banned from disposal in landfills as a result of odor problems.
It is also worth noting for C&D debris recycling facility operators that the presences of gypsum drywall particles in the fines screened from C&D debris could on occasion also result in H2S production. Several operators have reported that odors are present when deep piles of C&D debris fines are disturbed. Care should be taken to reuse fines only in areas where they are not prone to getting wet in the future.
RECYCLING MARKETS
Several different markets have been proposed for recycling gypsum drywall. The primary markets that are reviewed here are the ones most commonly practiced in North America: in the manufacture on new drywall, as an ingredient in Portland cement manufacture, as a soil amendment and in compost.
|
The most established recycling operations are in the Northwestern U.S. and Southwestern Canada, and these rely on the new drywall manufacturing market. Other recycling operations are scattered across the country, with many of these relying on land application and compost addition as the major end uses. It is important to note that most recycling activities have focused on scrap drywall from new construction activities. It is certainly feasible to recycle drywall from demolition projects, but several quality and environment factors must be considered.
New Drywall Manufacture. Scrap drywall can be recycled back into the manufacture of new drywall. This is currently practiced by many wallboard manufacturers with their own post-manufacturer scrap. While a small amount of paper is tolerable, the majority must be removed. Typical recycled amounts range 10 percent to 20 percent. Recycling of post consumer gypsum wallboard into new drywall manufacture is currently being practiced in several areas of North America. Of note is the New West Gypsum company in the Northwest U.S. and Southwest Canada. In some areas, new drywall is manufactured with synthetic gypsum, a waste product of air pollution control technology at coal-fired power plants. This, along with the recycling of post-manufacturer scrap, could limit the ability (or desire) of some plants to recycle post-consumer scrap drywall.
Portland Cement Manufacture. Gypsum is an ingredient in the manufacture of portland cement, added to control the setting time of the concrete. Gypsum is added to the cement clinker from the kiln and is processed to a fine powder. Typical gypsum contents in portland cement range from 5 percent to 10 percent. Mined gypsum rock is typically used by the cement kilns, and the different physical form of processed drywall may necessitate adjustment of the plants material feeding system. The purity of gypsum in the wallboard is a major concern. Paper should be removed, and care should be taken during the collection of the wallboard to minimize the amount of impurities, such as soil, that are introduced.
Application to Soil. Gypsum is a common soil amendment, and has historically been applied for several different purposes. Gypsum provides a source of calcium and sulfur for plants; it is commonly applied to peanut crops in the Southeast U.S. as a source of calcium at rates of 600 to 800 pounds per acre. Many vegetables, including potatoes and corn, have been shown to benefit from gypsum application. Unlike lime, gypsum does raise the pH of soils, and it is thus preferred for crops that require calcium, but where the soils are already alkaline (and cannot accommodate pH adjustment). Gypsum has also been found to be useful for reclaiming very salty soils. The calcium in the gypsum substitutes for the sodium in the soils, allowing the sodium to leach away. Gypsum has the ability to flocculate clayey soils that have drainage problems. The processing requirements for gypsum drywall that is applied to soil may differ somewhat from the industrial processes cited above. While foreign materials, such as nails and corner beads, should be removed, agricultural uses can tolerate some ground paper in the mixture. The presence of trace components (such as lead from lead-based paint) might be of greater concern when land applied (relative to the industrial uses) because of the potential for human contact and soil or groundwater contamination. The method of gypsum application will control the size of the material and the degree of processing needed. With some application techniques, larger pieces of drywall may cause damage to plants as thrown from the spreader at high velocities. If the drywall is being tilled into the soil, large sizes may be permissible, as size reduction will also occur during the application process, and plant damage from application is not a concern. While some recyclers have marketed bagged gypsum products for soil and plant application, the largest uses are the bulk applications by farmers.
Use in Compost. Scrap gypsum drywall is currently added to composting systems in a number of locations. Many of these systems are located at waste processing sites that already have compost operations in progress. While the paper fraction of the drywall can certainly biodegrade as part of the compost, it is important to note that the gypsum itself will not biodegrade to any major extent and will instead be incorporated into the final compost product. The results is a calcium- and sulfur-rich compost, which may have a benefit for some crops (as described above). Gypsum also offers the potential to bind up odors associated with ammonia. On the other hand, if the composting system is not kept aerobic, anaerobic microorganisms can result in the production of hydrogen sulfide, a foul smelling gas. The application of gypsum wall board to mechanically agitated compost systems (e.g. a windrow turner) tends to work better than static systems (e.g. a forced air static pile) because the mixing and breakup of the gypsum that occurs.
PROCESSING SYSTEMS
Several processing methods have been utilized for preparing gypsum drywall for recycling. The two major objectives of processing are separation of gypsum from the paper and the size reduction of the gypsum.
A big issue associated with drywall processing is dust. This is addressed by containing (placing in doors) as much of the processing system as possible or by providing water in the form of a mist to minimize emissions. Drywall processing systems will in many cases require an air permit (appropriate regulatory authorities should be contacted). Several vendors market self-contained drywall processing equipment.
Many of these operators use some type of grinder followed by a screening system. A dust collection system is typically included. Standard size-reduction devices found at many waste processing sites (e.g. tub grinders, horizontal mills) can be used to process drywall. Dust issues may need to be addressed, and screening will normally be necessary. Trommel screens are frequently used screening devices, and, in fact, trommel screens have been used as stand-alone operations where drywall is both separated from the paper and size reduced.
A preliminary size-reduction step, such as using a loader or compactor to provide rough size reduction, is useful for increasing efficiency. A recent development is the use of small grinders directly at the construction site. The idea is to apply size-reduced gypsum directly at the site.
ENVIRONMENTAL CONSIDERATIONS
As with the recycling of most construction materials, environmental and human safety issues must be addressed. Questions have been raised concerning the glass fibers found in Type X drywall.
Wisconsin researchers have reported that Type X drywall was not harmful to soil organisms (earthworms). Concerns have also been raised about the possible impact of the glass fibers on the human respiratory system. The size of the fibers might be too large to have an impact; however, this issue is currently being investigated further. When dealing with drywall from demolition projects, several other issues must be explored. The presence of lead-based paint could limit the recycling of wallboard, especially for soil application purposes.
Asbestos was used by relatively few wall board manufacturers in the past, but may be encountered in the joint compound associated with the wallboard installation. Mercury was used as a fungicide by some wallboard manufacturers in the past and may be encountered. While these health and environmental issues do certainly require added attention, with proper care, testing and removal procedures, much of the drywall removed from demolition projects should be able to be recycled.
The author is an associate professor of environmental engineering sciences at the University of Florida in Gainesville, Fla. He can be reached at ttown@ufl.edu.
Get curated news on YOUR industry.
Enter your email to receive our newsletters.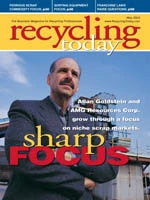
Explore the May 2003 Issue
Check out more from this issue and find your next story to read.
Latest from Recycling Today
- ReMA opposes European efforts seeking export restrictions for recyclables
- Fresh Perspective: Raj Bagaria
- Saica announces plans for second US site
- Update: Novelis produces first aluminum coil made fully from recycled end-of-life automotive scrap
- Aimplas doubles online course offerings
- Radius to be acquired by Toyota subsidiary
- Algoma EAF to start in April
- Erema sees strong demand for high-volume PET systems