_fmt.png)
Within the waste and recycling industry, moving floors play a critical role in unloading bulk loads of materials from trailers. The benefit of a moving floor trailer comes from its ability to move large amounts of material without the need for additional tools or extensive operator assistance.
Trailers equipped with a moving floor unload materials using a series of slats or planks that are powered by hydraulic cylinders. These systems come in variations with slats of different thicknesses, each suited to applications involving certain kinds of material and can move municipal solid waste (MSW), single-stream recyclables, cardboard, wood chips, mulch and compost, among other materials.
To ensure the optimal use of a moving floor, haulers must be aware of maintenance measures and the wear and tear that some materials can have on these systems.
Moving floor benefits

Richard Moffitt, vice president of sales and marketing for Hallco Industries, says three primary types of trailers are used for transporting waste and recyclables: belt trailers, tipper trailers and moving-floor trailers.
Hallco is a Tillamook, Oregon-based company that makes its own brand of moving floors called Live Floors.
Belt trailers contain a belt in the center that pulls materials out the back, while a tipper can be tilted up by a hydraulic ram to dump materials.
Compared with a belt trailer, a moving-floor trailer has greater capacity and can accommodate a broader range of materials, Moffitt says. For tippers, it often takes a considerable amount of time to secure the trailer, and safety issues can be a concern.
Mike Robinson, sales director at Madras, Oregon-based moving-floor producer Keith Manufacturing, says many landfills do not have the tipper device needed to lift trailers. A tipper device and the trailer itself also could fall over if the landfill ground is unstable. Moving floors do not experience this risk because the trailer stays horizontal on the ground.
“I think it’s a more stable system to use with limited chances of actually tipping over,” Moffitt says. “[There is] greater capacity, so you can haul 20 to 27 percent more material than you can in a belt trailer.”
He adds that trailers equipped with moving floors also can haul a variety of bulk material types. “So, one day you can haul trash, the next day you could haul auto fluff, the day after that you’re hauling recyclables. The trailer is just that versatile.”
Robinson says trailers equipped with Keith’s brand of moving floor, the Walking Floor system, are not hindered by delays from other material handling equipment and can unload in different locations.
Tarps can be added to a moving-floor system for cleaning purposes as found in Keith’s CleenSweep System. The CleenSweep system can be powered hydraulically or electrically. The hydraulic version often is built into trailers that have a Walking Floor installed, and Robinson says it is the more powerful of the two versions while being low maintenance, though it is more difficult to install if not purchased at the time the trailer is being manufactured. He says the electric version is popular in aftermarket sales because of the ease of installation.
Robinson says that while the CleenSweep System is not necessary for all waste handling applications because a Walking Floor can clean most MSW products without a tarp, it is helpful when unloading other materials, such as C&D debris, food waste and byproducts of mulch and compost.
Moving floor selection
Moffitt says choosing a moving floor system requires a hauler to consider the type of material it will most commonly handle and how it will be loaded. This is often done with a compactor or by top loading using a wheel loader or material handler, for instance. A thick floor with high-impact resistance works well when hauling C&D debris, whereas a flatter floor works well for hauling lighter recyclables.
In most moving floor systems, every third slat is connected to a cross drive, with eight to nine slots per cross drive. Cross drivers are connected to the hydraulic drivers (cylinders) underneath the hydraulic module. To unload, the moving floor system pushes all slats toward the trailer’s rear at once, and it also can reverse the direction to load material into the trailer.
The slats must retract in a pattern to break stack friction. To move a pile of materials, two-thirds of the floor must stay still while one-third retracts. Once all three sections retract, the floor moves again, bringing the pile along.
Moffitt says most moving floor slats are made of aluminum because it has a greater coefficient for friction, meaning it pulls the material out of the trailer more efficiently.
Maintenance considerations
In terms of preventive maintenance for moving floors, haulers should tighten all bolts, including deck bolts and drive bolts, and check lug nuts.

Moffitt says problems pertaining to hydraulic oil can be detrimental to these systems. Running a high-pressure filter and a return filter into the hydraulic tank helps filter small particles and contaminants that could otherwise pass through and cut hydraulic seals. It is important, Moffitt says, to run enough clean oil through the system, too. He recommends 30 gallons per minute at 3,000 psi, typical parameters for moving floors. Running more than this will shake the system and wear parts prematurely.
Operators also should keep an eye on the rear slats because the back half of the trailer sees 100 percent of the load going across it, while the front half does not see as much of the load, Moffitt says. Checking for wear on the slat legs is necessary as they hold the slats down. To address this wear, haulers can flip the slats front to back, potentially doubling their lives.
Monthly maintenance recommendations for Keith’s Running Floor II, the drive system for its Walking Floor, include checking for hydraulic leaks, checking operating temperature, torquing cylinder barrel clamp bolts and pressure washing the drive unit, subdeck and slats. For six-month service, Keith recommends changing the oil filters, cycling the system briefly in both directions to observe proper operation and inspecting components for wear.
The lifespan of a moving floor primarily depends on the number of loads per day and the type of material being unloaded. An abrasive product, such as single-stream recyclables with glass mixed in, can erode a floor faster than a material such as cardboard, Moffitt says. Given the right treatment, a moving floor trailer that is hauling municipal waste could last seven to 10 years. A trailer that hauls mostly cardboard or other light materials could last longer than 10 years. Sand, gravel, glass and auto fluff are most likely to wear down not only the moving floor but also the whole trailer. Moving floors with thicker designs are better for handling these materials, and an overlapping floor will help protect floor slat seals.
Moffitt says selecting and using moving floors involves balancing cost and weight with longevity, noting that “you can buy a thinner floor that gives you less weight in the trailer, so you can haul more payload, but you’re going to have to replace floor slats sooner because you’re sacrificing early to get payback.”
Moffitt says building a relationship with a nearby dealer is key to quickly obtaining spare parts for moving-floor systems. He adds that this could be more beneficial than end users trying to maintain their own spare parts inventory because haulers likely will not need spare parts for seven to 10 years.
Robinson says, though, that it is best for moving floor owners to have at least a check valve, switching valve and hydraulic cylinder on hand in case the system malfunctions.
Get curated news on YOUR industry.
Enter your email to receive our newsletters.
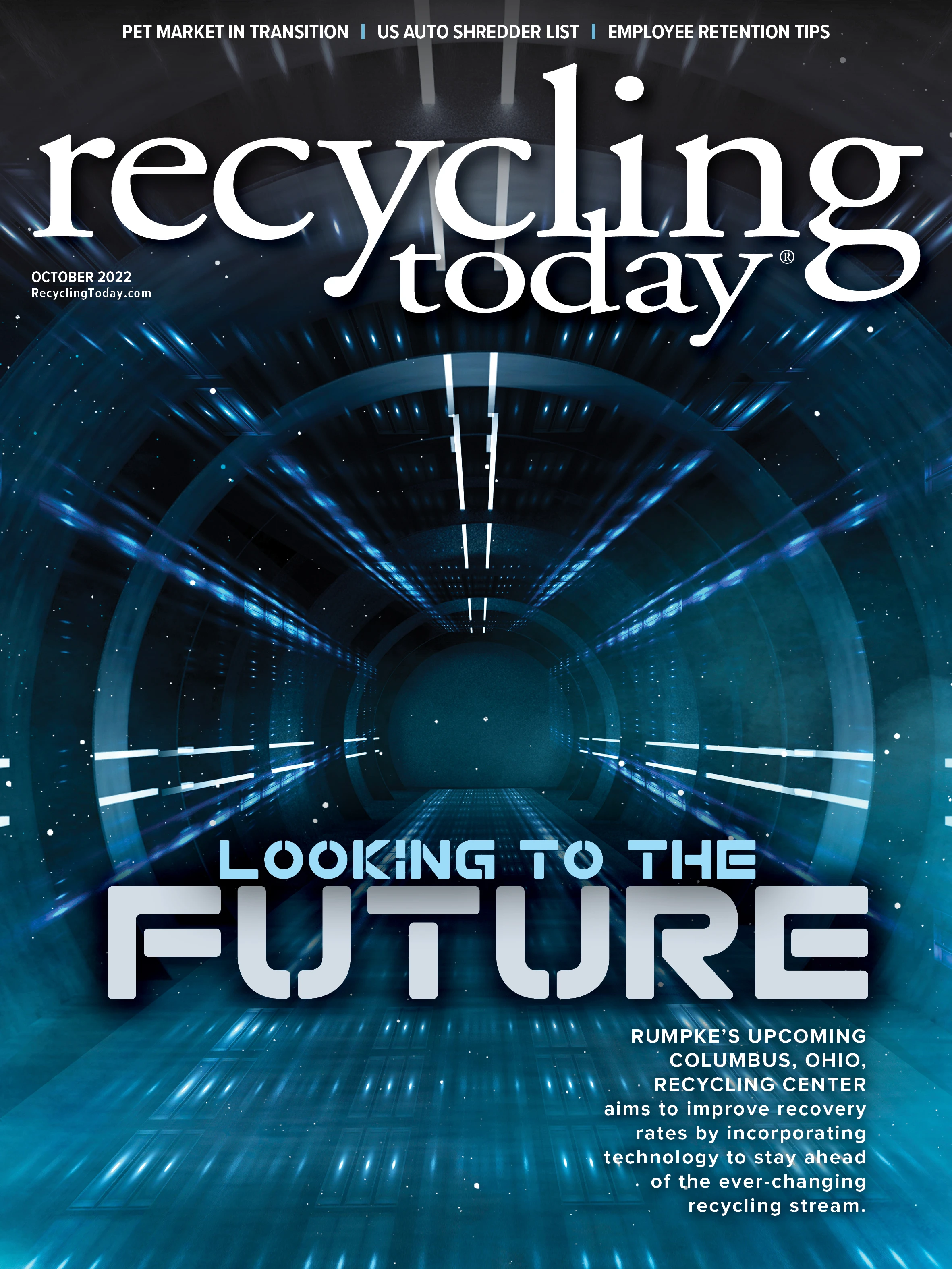
Explore the October 2022 Issue
Check out more from this issue and find your next story to read.
Latest from Recycling Today
- Fenix Parts acquires Assured Auto Parts
- PTR appoints new VP of independent hauler sales
- Updated: Grede to close Alabama foundry
- Leadpoint VP of recycling retires
- Study looks at potential impact of chemical recycling on global plastic pollution
- Foreign Pollution Fee Act addresses unfair trade practices of nonmarket economies
- GFL opens new MRF in Edmonton, Alberta
- MTM Critical Metals secures supply agreement with Dynamic Lifecycle Innovations