
Automobile shredder operators are seeking new and innovative ways to obtain a premium ferrous shred that yields a higher value per ton and meets the most stringent steel mill standards. That goal was particularly top of mind at Tri-State Iron & Metal Co., Texarkana, Arkansas, as the owners were considering how to supply a high-grade ferrous product to steel mills while also reducing the amount of picking labor required to do so.
Established in 1947, Tri-State Iron & Metal is a third-generation family business that still is located at its original location in Texarkana. The business has grown rapidly over six decades and has the capacity, experience
Setting higher goals
Tri-State set a goal to increase its profits by supplying a high-grade ferrous shred to steel mill customers and—at the same time—to reduce the amount of hand-picking on its line. To meet that goal, the company researched and ultimately purchased a Shred1 Ballistic Separator from Erie, Pennsylvania-based Eriez.
The Shred1, designed to separate iron-rich ferrous from the mixed metals and waste material in the

“We had a few objectives when we were looking at the Shred1,” recalls Adam Glick, vice president at Tri-State Iron & Metal. “We needed our ferrous shred to contain less than 2 percent copper. Previously, we were between 2.4 percent to 2.6 percent copper content. We also wanted to reduce our hand-picking labor cost with a more efficient way of handling this process. Ideally, we were looking to use technology rather than labor to increase our profit margins.”
Yielding more value
The Shred1 uses magnetics and ballistics to separate materials into two distinct fractions: a premium low-copper ferrous No. 1 shred that contains less than 2 percent copper and a traditional No. 2 shred. The first fraction is a high-value, low-copper-content ferrous product. The second fraction represents less than 25 percent of the material flow and contains mostly mixed metals: copper and aluminum with steel housings or cores.
That 25 percent, the No. 2 shred product, goes through a hand-picking station at Tri-State Iron & Metal. Fewer pickers are required on that line because of the lower volume of No. 2 shred produced by the addition of the ballistic separator. They also are more efficient at the task because of the reduced material flow.
The first fraction is worth considerably more than a No. 2 shredded scrap grade, and demand for this No. 1 grade is increasing.
The more ferrous recovered from the shred, the greater the profit for the operator in terms of higher quality ferrous scrap and increased copper pickings that can be marketed separately.
Selling a premium,
Scrap processors also can see additional revenue by reselling the residual copper from the No. 2 fraction, which is worth considerably more per pound than the ferrous scrap fraction.
Sponsored Content
Labor that Works
With 25 years of experience, Leadpoint delivers cost-effective workforce solutions tailored to your needs. We handle the recruiting, hiring, training, and onboarding to deliver stable, productive, and safety-focused teams. Our commitment to safety and quality ensures peace of mind with a reliable workforce that helps you achieve your goals.
“Interest in the Shred1 continues to intensify as scrap processors like Tri-State Iron & Metal seek greater value in a premium ferrous product,” says Chris Ramsdell, recycling product manager for Eriez. “The ferrous premium combined with the increased copper pickings and reduced labor helps the Shred1 quickly pay for itself in three different ways.”
Improved recovery
The unit’s ballistics enable Tri-State to automatically produce a premium No. 1 low-copper ferrous product. Its high-speed processing sends clean high-grade ferrous on a different trajectory than mixed metals, such as meatballs and wire harnesses, which also contain copper or other nonferrous metals.
These mixed metals degrade the ferrous product and often limit the frag to low-value uses, such as rebar production. On the other hand, the premium low-copper ferrous is highly valued by most steel mills; it is that sort of product that Tri-State can now deliver to its regional customer base.
Tri-State sees economical and operational returns from this installation. Glick says the company reduced its pickers from four to two and has experienced a higher recovery rate by implementing this technology. “We looked at different solutions to pull more copper out of the ferrous, even adding more pickers,” he says. “But we decided to invest in the technology and had Eriez demonstrate the unit. Eriez answered all our questions before we put it online,” he says.
Get curated news on YOUR industry.
Enter your email to receive our newsletters.
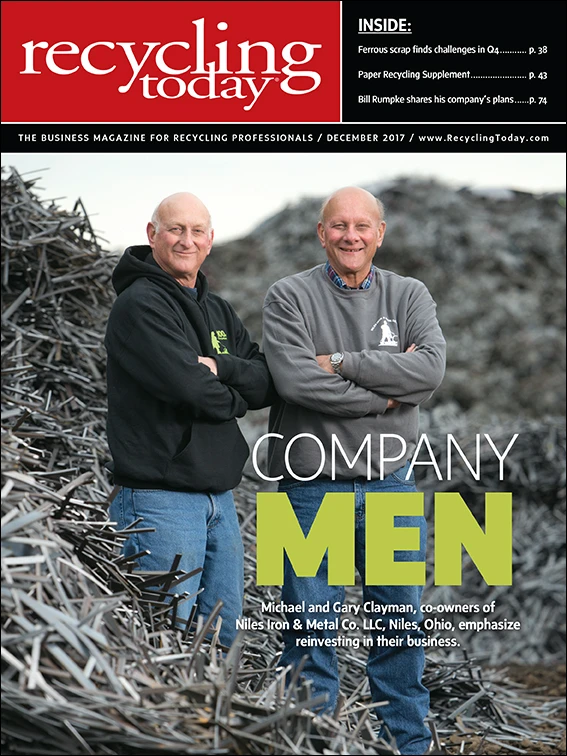
Explore the December 2017 Issue
Check out more from this issue and find your next story to read.
Latest from Recycling Today
- Athens Services terminates contract with San Marino, California
- Partners develop specialty response vehicles for LIB fires
- Sonoco cites OCC shortage for price hike in Europe
- British Steel mill’s future up in the air
- Tomra applies GAINnext AI technology to upgrade wrought aluminum scrap
- Redwood Materials partners with Isuzu Commercial Truck
- The push for more supply
- ReMA PSI Chapter adds 7 members