
Makers of aseptic packaging and other coated paperboard beverage cartons (and the brand owners that use them) have long recognized that finding viable and cost-effective recycling end markets can help protect their market share.
Polymer-based protective layers and, in some cases, attached aluminum can be problematic when it comes to affordably recycling discarded cartons. Working in their favor, however, is the existence of desirable fibers sought by recycled-content paper mills.
Efforts to establish sustained end markets are ongoing for the Texas-based Carton Council of North America and several of its members.
This year, the Ontario-based Carton Council of Canada (CCC) announced details from research into another potential end market for cartons: facilities that produce molded pulp, a form of packaging that can accept recycled materials as feedstock and that could be poised for a market share growth spurt.
A market with possibilities

Molded pulp, like glass, aluminum and some metals in packaging and food service applications, has been competing against plastic—and often losing ground—in terms of global market share.
The rules of that struggle have changed in the past several years, however, as the debate has intensified regarding the recyclability of plastic and its tie to the fossil fuels sector.
“Molded fiber products have been growing very well as replacements for plastic items, growing 5-plus percent per year for the last five years,” says Bill Moore of Atlanta-based consulting firm Moore & Associates.
The Massachusetts-based International Molded Fiber Association (IMFA) says that growth is tied to “paperization,” or what the creators of that term perceive as a shift from plastics to fiber-based packaging in many parts of the world.
The term paperization was used this August in an online report from by Oumar Fofana for Packaging Gateway. Fofana writes in part that regulatory measures are compelling companies to seek alternative packaging solutions and that fiber-based packaging, derived from renewable resources like wood pulp, is biodegradable and recyclable.
While virgin wood pulp can be one source of feedstock for molded pulp producers, IMFA says the material typically is made from recycled paperboard and/or newsprint and used widely for packaging solutions. Also used, according to IMFA, are agricultural byproducts, such as bagasse (sugar cane husks).
Although the past decade has seen plastics recycling investments ramping up, IMFA lists environmental advantages for molded pulp that contrast the material with discarded plastic.
“Molded fiber products are recyclable along with other [scrap] paper and are biodegradable and compostable where facilities are available,” according to the organization. “They can also be incinerated without damaging incinerators. Both fiber and water are recycled and reused in manufacturing, resulting in almost zero waste. There are no toxic or hazardous waste materials expelled into the environment.”
IMFA consistently publicizes examples where molded pulp has replaced plastic in a visible or high-volume application, with a recent one being packaging for the Google Pixel smartphone line. A trade journal report IMFA cites describes molded pulp used inside current Pixel boxes as being partly made from recycled old newspapers (ONP).
ONP has long been a feedstock welcomed by molded pulp producers; but, as material recovery facility (MRF) operators and scrap paper traders can attest, that grade has diminished greatly in volume just as molded pulp is regaining market share.
Competing for fiber
The CCC effort seeks to connect a recyclable paper grade seeking additional end markets (cartons) with a consuming market with encouraging growth prospects (molded pulp).
In a presentation Moore prepared for an IMFA event this September, the longtime consultant reviews the state of fiber supply for molded pulp producers in North America.
It includes unfortunate but, at this point, old news about newsprint production and ONP recovery in the United States, with Moore saying the “decline over the last 25 years has been staggering—over 90 percent.”
While that decline is “moderating,” he says, the United States could experience further declines in the use of newsprint over the next five years of about 3 percent per year.
Isabelle Faucher, managing director of the CCC, says molded pulp producers are keenly aware of the situation.
“Manufacturers of recycled fiber-based packaging and containers are facing a lack of their traditional raw materials and high prices due to the decline in newspaper and office paper volumes and the increase in demand for corrugated cardboard boxes,” she tells Recycling Today.
In his presentation, Moore says some molded pulp producers have turned to double-lined kraft (DLK) box and board mill trimmings because of its good quality and widespread availability.
However, he adds, mill operators and recovered paper buyers also recognize that same high quality.
“Paperboard mills value this quality fiber to ensure consistent production and finished paper quality and also use it to increase production,” Moore says in his IMFA presentation, noting that the material “runs” faster.
The DLK grade can be acutely difficult to source when recovered fiber prices are rising, he adds.
“When old corrugated containers [OCC] prices are high, the integrated producers have a tendency to internalize the DLK they may have been selling to other users,” he says. “Mills also value DLK inventory as a backup if their cleaning systems go down—they can run high-quality DLK, bypassing parts of their stock prep systems.”
Regarding OCC, the largest volume of all recovered fiber grades, Moore says some molded pulp producers will buy the No. 11 and No. 12 grades, but the global containerboard sector tends to absorb generated material and keep the price higher than what molded pulp makers wish to pay.
The situation leaves the door open to alternative fiber sources, which the CCC suggests should include discarded beverage cartons and aseptic packaging.
In the mix (but not literally)

According to Faucher, cartons contain some of the highest-quality fibers in the recycling supply chain—long, bleached fibers. The testing conducted on behalf of the CCC by Québec-based Innofibre “confirmed that recycled carton fiber pulp has similar mechanical and physical properties to virgin kraft pulp,” she adds.
Despite the quality, Moore tells Recycling Today most discarded cartons entering MRFs in the U.S. wind up in mixed paper. That, he says, is not a grade molded fiber producers can use.
Moore says the Carton Council of North America has attempted to incentivize MRF operators to positively sort cartons.
“At one time, a number of MRFs separated cartons (grade No. 52). But, over the years, making the separate carton grade has plummeted, [and now] less than 20 percent do it.”
He adds that the cost to sort cartons is high, while the resulting volume is low, prompting most discarded cartons in the U.S. to be included with mixed paper.
Acording to Faucher, using cartons as feedstock also could involve changes or at least adjustments at the mill.
“From CCC’s experience, we know that it is very possible to adapt the equipment that a mill already has in order to pulp cartons,” she says. “New or dedicated equipment is not necessarily required.
“Since fiber in cartons requires separation from [its] nonfiber components (plastic and aluminum), mills will need to play with parameters such as agitation time, pH levels and water temperature. Once the hydropulping process is completed, the fiber (in the form of pulp) is taken through a series of cleaning steps involving screens and other equipment.”
As another possibility, Faucher says, some mills could opt to cut up cartons into small pieces with a shredder prior to placing them in the hydrapulper, which can accelerate the process and help to extract more fiber.
The Innofibre and the CCC research can be considered an initial step in connecting cartons to molded fiber production rather than a completed process, and Faucher says it has led to several follow-up conversations.
“We have reached out to several leading paper mills who consume recycled fibers and manufacturers of molded fiber products to offer a one-on-one presentation on the study, its outcomes and the support Carton Council can provide,” she says. “So far, we have had meetings with four of them.”
Faucher says the door is open.
“Any other molded pulp manufacturer or mill in the U.S. or Canada interested in exploring the possibilities offered by recycled carton pulp are welcome to get in touch with us,” she says, adding that pulp mills and product makers have options ahead.
“Among other steps, manufacturers would presumably want to conduct their own internal R&D phase and have discussions with their pulp supplier if they don’t produce their own,” Faucher says. “Carton Council is ready to collaborate on all the steps in this decision process, and we’ll move as fast as the manufacturer is willing to.”
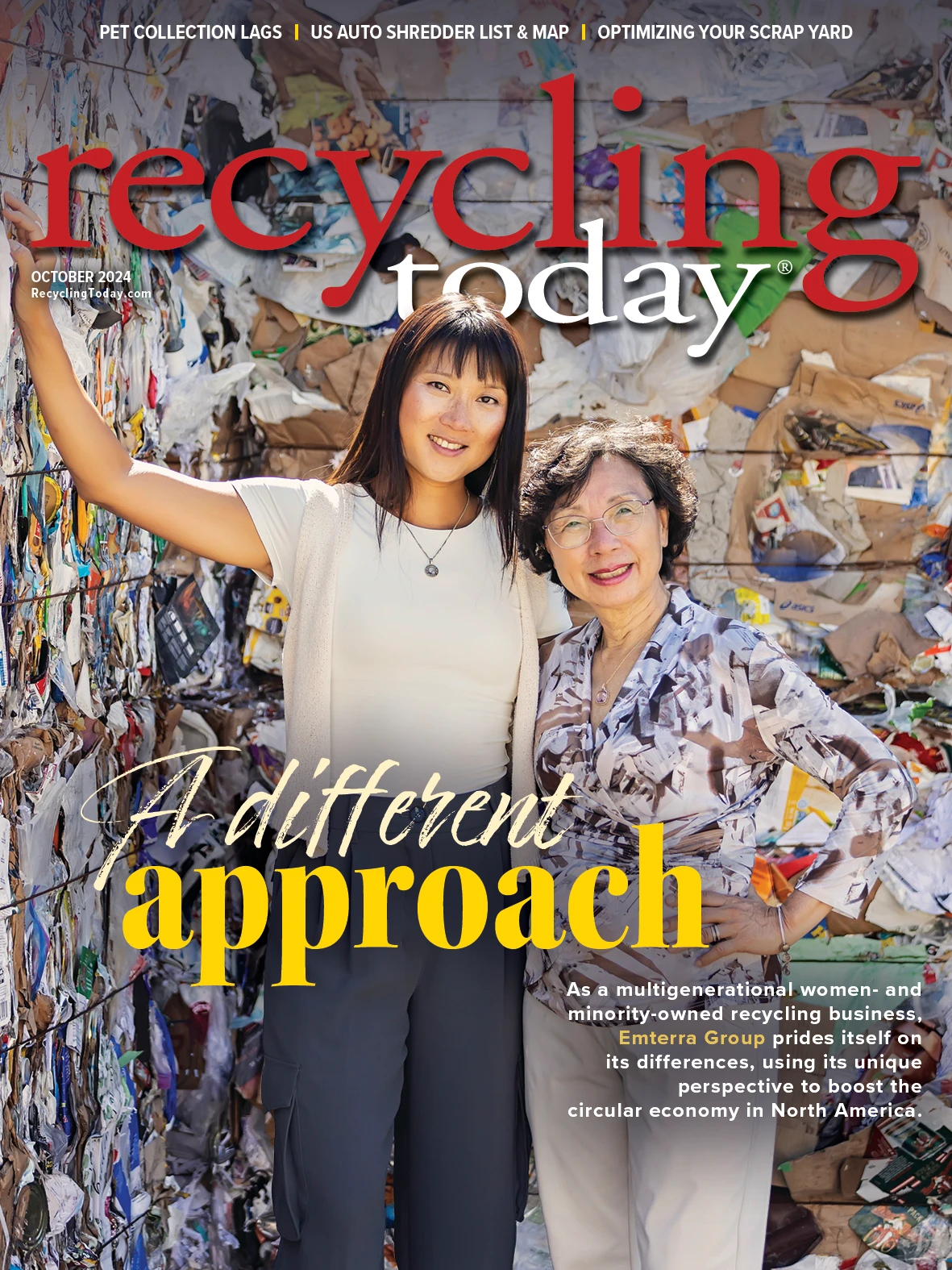
Explore the October 2024 Issue
Check out more from this issue and find your next story to read.
Latest from Recycling Today
- ReMA opposes European efforts seeking export restrictions for recyclables
- Fresh Perspective: Raj Bagaria
- Saica announces plans for second US site
- Update: Novelis produces first aluminum coil made fully from recycled end-of-life automotive scrap
- Aimplas doubles online course offerings
- Radius to be acquired by Toyota subsidiary
- Algoma EAF to start in April
- Erema sees strong demand for high-volume PET systems