
Interest in sustainable packaging solutions is growing, driven by consumer demand, government legislation and technology advances. According to the Smithers Pira report “The Future of Sustainable Packaging to 2018,” the sustainable packaging market will grow to reach $244 billion by 2018.
The most common sustainable packaging trends are downsizing and lightweighting of packaging; increased recycling and waste recovery; increased use of recycled content; increased use of renewably sourced materials; and improvements in packaging and logistical efficiency, the report notes.
Molded pulp packaging can claim many of these benefits. And Chris Miget, president of St. Louis-based EnviroPAK is positioning his company to take advantage of molded pulp packaging’s cost-efficient and environmentally friendly reputation.
Miget founded EnviroPAK with George Crump and a team of investors and engineers in 1995. In the years since, the company has grown to consume more than 20 tons of over-issue newspapers (OIN) daily, producing molded pulp packaging for manufacturers serving the electronics, medical, consumer goods, automotive and plumbing industries.
AREA OF EXPERTISE
“We specialize in producing a transfer molded thin-wall product, the most prevalent type used in the industry today,” Miget says.
“The process uses a forming and transfer die with a standard thickness of 1/16 of an inch and has provided delicate protection for eggs and lightbulbs for more than 100 years. It is today’s packaging medium of choice for industries such as electronics, hardware and bottled goods.”
Midget says EnviroPAK can add a premium finish to its standard process, a recent development, making its molded pulp packaging suitable for retail and high-end consumer products.
EnviroPAK sells its custom molded packaging through a network of distributor partners throughout North America and occasionally abroad.
“We believe we produce the best molded pulp product in North America,” Miget says. “By adopting the proven principles of lean manufacturing, we have been able to continually increase our speed to market.
“Additionally, our award-winning design team allows us to meet the unique and challenging demands of packaging professionals,” he says.
The company has an in-house design and tooling department that features multiple CNC (computer numerical control) machines with the latest technology, Miget says. “This is in addition to the processing and molding equipment we have to convert the recycled newspaper to packaging each and every day,” he adds.
FROM PAPER TO PACKAGE
Miget says EnviroPAK’s process starts with a sorting and weighing station, where incoming OIN, which the company purchases from within a limited radius of its St. Louis plant, is visually inspected prior to being incorporated into the pulping process.
“The loading and pulping process is semiautomatic to ensure continuous pulp consistency,” he says.
“Once the pulp slurry has been brought to the ideal fiber content, we introduce it to one of the multiple molding systems,” Miget continues. “The molding systems take the tooling we create in-house and rotate them through the slurry to form the packaging shapes needed.”

The wet molded shapes pass through an automated drying system until they reach their ideal moisture content before semiautomated removal and packaging systems prepare the packages to be transported to EnviroPAK’s clients.
The company produces roughly 50 million to 75 million pieces of molded pulp packaging per year, Miget says. “To better illustrate,” he says, “this kind of volume fills thousands of 53-foot trailers per year.”
Because EnviroPAK focuses on custom molded solutions, Miget says each product the company produces is different in shape and size.
EnviroPAK is able to provide economical solutions to its clients in part because of the stability that has existed in OIN pricing. “The cost of our raw materials has stayed consistent, allowing us to meet the budgetary needs of our end users,” he says.
When asked how declining newspaper production could affect the company, Miget says, “EnviroPAK has been utilizing recycled and recovered ONP for more than 20 years. From the time we produced our very first piece of molded pulp packaging, our clients have asked us what we were going to do when ONP became obsolete. This concern continues to be in the news given the dramatic effect the Internet has had on our lives.”
He adds, “However, we continue to turn away tons and tons of high-grade No. 9 ONP (over-issue news).”
Miget says EnviroPAK is prepared should the company need to begin using ONP No. 8 or No. 6. “Over the past 24 months, we have implemented dramatic process enhancements into our operation that include sorting/detrashing of the ONP consumed in production.”
EnviroPAK also is investigating alternative agrowaste fibers that could be used to supplement its recovered fiber, he says, should that become necessary.
Despite these possible changes, Miget says, “Molded pulp continues to be one of the most cost-efficient solutions for packaging professionals when compared to resin- and plastic-based materials that often fluctuate with market conditions.”
According to EnviroPAK’s website, www.enviropak.com, packaging costs go beyond raw materials to include transportation, warehousing, labor and design. “We save our customers money and resources every day in each of these categories,” the company says. “EnviroPAK’s molded pulp can reduce costs by as much as 70 percent when compared to other packaging materials.”
INVESTING IN GROWTH
Miget sees opportunity for EnviroPAK in the “uptick in reshoring manufacturing to the continental United States.” He says, “Companies that had previously brought their products in from overseas packaged and ready for retail are now reconsidering these decisions and are looking at U.S. manufacturing and packaging operations.”
Miget adds, “EnviroPAK is uniquely located in the central United States, offering significant benefits in shipping costs.”
“Over the past 24 months, we have implemented dramatic process enhancements into our operation that include sorting/detrashing of the ONP consumed in production.” – Chris Miget
He says packaging is a global topic of discussion as the concept of the circular economy takes hold outside of Europe and as that continent’s recycling principles are adopted more widely. “Our domestic customers that sell their products overseas have to meet these green and sustainable packaging guidelines to be competitive,” Miget says.
For those companies that want to transition to more environmentally friendly packaging, Miget says EnviroPAK recently announced a multimillion-dollar investment in infrastructure and equipment to increase the manufacturing capacity at its St. Louis plant by 35 percent to 40 percent. He says the company’s investment “reflects the rapid growth of the company and the increased demand for sustainable packaging and domestically manufactured molded pulp.”
Miget adds that EnviroPAK also is looking at a possible expansion of its product lines and the potential acquisition of additional production capacity.
The company owes its growth in part to increasing consumer demand for “green” packaging and to a growth in manufacturing in the U.S. Therefore, Miget says it’s important for EnviroPAK to be able to “showcase the benefits to its customers of utilizing recycled materials in lieu of virgin materials.”
Get curated news on YOUR industry.
Enter your email to receive our newsletters.
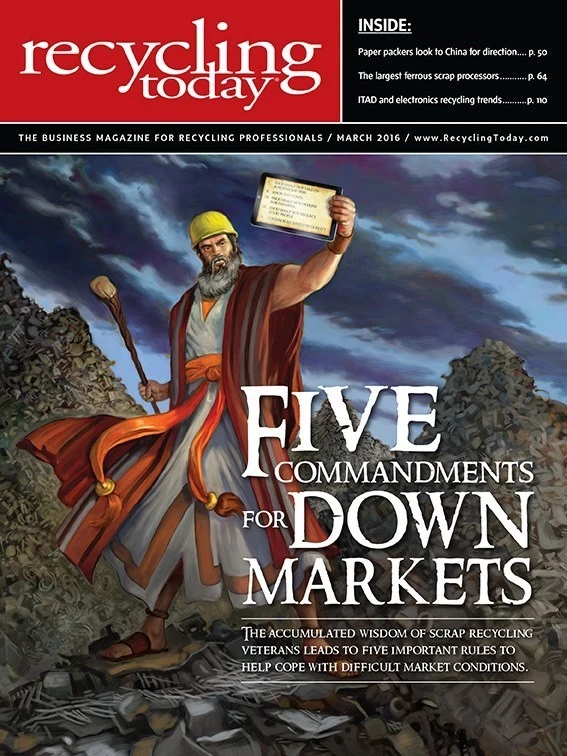
Explore the March 2016 Issue
Check out more from this issue and find your next story to read.
Latest from Recycling Today
- Steel Dynamics cites favorable conditions in Q1
- Hydro starts up construction in Spain
- Green Cubes unveils forklift battery line
- Rebar association points to trade turmoil
- LumiCup offers single-use plastic alternative
- European project yields recycled-content ABS
- ICM to host colocated events in Shanghai
- Astera runs into NIMBY concerns in Colorado