Portable crushing in North America long meant wheel-mounted equipment. There was some track-mounted crushing around, but it was usually big machinery working at the face of a quarry. This is unlike Europe and parts of Asia, where small, nimble mobile equipment has been used for some time.

Indeed, most on-site crushing in Europe is done by track-mounted equipment. In North America, C&D recycling industry demand for smaller track-mounted crushing equipment has grown quickly only in the past decade. That kind of action draws attention from equipment companies that supply the recycling industry. "Track-mounted crushers are now a big business in the United States," according to Ian Williamson of BL Pegson, a British crusher manufacturer with U.S. headquarters in Durand, Mich. BL Pegson is part of Terex Crushing and Screening, Louisville, a division of Terex Recycling.
At first the mobile crushers were imported from Europe and Asia. Now several American manufacturers are offering their own models to satisfy the growing demand. But as might be expected, there have been several claims and counterclaims as to the attributes of track-mounted crushing and screening equipment. Indeed, some manufacturers agree with Jay Giltz of Eagle Crusher Co. Inc., Galion, Ohio, who says, "It’s a fad. Look at how many people are just renting or demoing them, not buying them."
In an attempt to help solve some of the confusion swirling about the machinery, and to provide both sides of the debate, we contacted several of the manufacturers involved to ask them their opinions on the role of mobile (track-mounted) equipment, especially versus portable (wheel-mounted) crushers. Here is our report.
Pros and Cons
Almost everyone concedes that mobile crushers are quick to get to work. "Mobile’s advantage is ease of set up," says Ron Greiss of Kolberg-Pioneer, Yankton, S.D. "You can get it off the trailer and up and running in five minutes. Many people are looking at that and saying, ‘If I can get crushing in five minutes, am I better off?’"
Williamson adds, "A large part of the cost for the operator of a portable plant is for moving the machine. These just get off the truck and are ready to run."
This type of set-up makes a mobile easier to erect and assemble than a portable, according to Paul Smith, Johnson Crushers International (JCI), Eugene, Ore. "It used to take three to four guys and a couple of loaders, maybe a crane, to set up these plants. There was lot of cribbing with large timbers, and jockeying of the crusher into place. Then you had to run it a few hours and reset the blocks." Wrestling with the timbers, says Smith, was the number one cause of workmen’s comp claims in the portable crushing industry. "These hydraulically engaged foundations eliminate dealing with cribbing. Even the walkways can be hydraulically raised. It is more elaborate, but simpler to operate. One person pushes a button, reducing labor needs for set up."

That reliance on hydraulics for ease of use could be an Achilles heel, says Bob Myers of Telsmith, Mequon, Wisc. "Operationally, mobiles are a sophisticated piece of equipment that a contractor has to pay a lot of attention to," says Myers. "Many recyclers are small- to medium-sized companies, and don’t have the on-staff mechanics capable of maintaining something this sophisticated." Because the machines are so compact, they are difficult to service. "It’s like everything is in a suitcase."
Even one of mobile crushing’s biggest supporters, Williamson of Pegson, will say that "maintenance is the only disadvantage of track-mounted, because of their compactness. There isn’t a lot of room for electronics and such. However, in other areas of maintenance they do offer an advantage. Instead of having to clean out underneath a crusher and its transfer points, you just move it. It’s a lot easier to do it then."
Williamson doesn’t see as a disadvantage another facet of mobile crushers that other manufacturers pointed out: Discharge room under the crusher. Giltz from Eagle Crusher says, "Many experts will tell you you need at least three feet of space between the bottom of the crusher and the discharge chute in order to handle the rebar. Otherwise, it gets wrapped up in there and is difficult to remove."
He adds that a stationary crushing system has it best, as it can usually be any height it needs to be, and can have a lot of room underneath to handle rebar. "It can be set up properly because there are no height restrictions," he notes. "To make a portable, you have to squish down a stationary. Sacrifices have to be made to get it down to 13 feet 6 inches high so you can move it on our highways. Those disadvantages are magnified with tracks, because they take up even more room."
Williamson disagrees. "Under our jaw is 28 inches of room. Although others will say you need more, that is enough room to handle rebar and not puncture the conveyor belt."
Mike Vigil of Komatsu America Corp., Vernon Hills, Ill., does say that discharge room can be an issue. Most of the models, including Komatsu’s, raise the conveyor for travel and lower it for production to at least two feet of clearance. "It’s an issue everybody has to face. But the customer needs to size the material properly first before feeding the machine. It is not a problem then, and you get higher production."
There are still trade offs, says Ed Conner of Irock, Wooster, Ohio. "You can’t make the head or tail pulleys too long in order to keep the height down. Hoppers aren’t too big, but a lot of people are now feeding their crushers with excavators, anyway."
Myers of Telsmith says that on a mobile plant the feed area is usually smaller than on a portable. "Unless you feed them with an excavator, they can’t handle all the material that is coming in. Most contractors have mid-sized loaders, and this is too big for the feeders of most of these mobiles."
Chase the face
One thing track-mounted crushers do well is move. "Mobile’s biggest advantage is moving around the jobsite. Tracks can go where a truck gets stuck," says Eric Houle of Erin Systems, Portland, Maine.
Conner from Irock points out that the mobile "can be walked back into the pile to cut down on travel times for the loading equipment." The principle is similar to how a tracked crusher is used in quarrying applications, where it moves to stay close to the quarry face, or "chases the face."
Greiss from Kolberg-Pioneer believes that consideration matters. "Traveling the few feet with a material handler can add up in time and money," he says.
Even so, the operator is not using that expensive undercarriage all the time, says Dave Urbanek of Sandvik Rock Processing, Appleton, Wisc. "It spends a lot of time sitting there. That is a lot of money to be just sitting there." He suggests that another way to get the advantages of following the face is to put a dolly underneath the portable crusher, and have a dozer move the crusher around the site.
At some job sites, compactness is a distinct advantage, because a mobile doesn’t take up much room in crowded working areas. "On the East Coast we have several tight spots that a full portable crusher will not fit into," says Conner from Irock. "These will."
Another debate is over the production rates of track-mounted versus wheel-mounted crushing systems. Eagle’s Giltz insists mobiles provide less production per hour. Conner makes the point that there are some basic principles of crushing that are not going to change whether the unit is on wheels or tracks. "By putting our usual crusher on tracks, and not a scaled-down model, we have found little difference in production whether it is on wheel or tracks," he says. "On tracks, it might not be the same capacity as a portable, but it is 90 percent."
Adds Greiss from Kolberg-Pioneer, "Any production rate disadvantage is more than made up by more hours crushing [versus setting up]."
To those with less capital, the cost of mobile against portable crushers may be a disadvantage. Track-mounted costs more, because tracks cost more—for some manufacturers as much as 50 percent more—although most quoted smaller percentages.
Pegson’s Williamson did add that he thinks it matters where the machine is made. If manufactured in a part of the world where wages are lower, then that does help to keep the costs down.
Market and Marketing
Are mobile crushers just a status symbol? A couple of the manufacturers interviewed think so. "Somebody who wants to be a big player, or look like one, might buy one," one manufacturer says. "Keeping up with the Jones," another manufacturer says of buyers' motives.
Dave McLaughlin, Cedarapids Inc., Cedar Rapids, Iowa, adds that "everyone wants the new technology, they may deny it, but it is true." He continued, though, that the technology is new to the U.S., not Europe.
"Initially the mobile crushers coming into our country from overseas were designed for over there, and were too small. They did not work as well here, as I am sure our design would not work over there," says Irock’s Conner. "But now you are seeing the ‘Americanization’ of the designs. They are being tailored to the U.S. market."
Most of the manufacturers agreed the majority of the track-mounted crushers sold today are designed to handle the smaller jobs. Says McLaughlin from Cedarapids, "You can get a track crusher, screener and even conveyor up and running full steam in 45 minutes. These things are great for jobs of 5,000 to 20,000 tons. The standard used to be that no crushing system was moved onsite for jobs less than 100,000 tons. It cost too much otherwise. That has all changed."
So who is, or could be, buying and using track-mounted machinery? There are several possibilities, according to the suppliers, but the one segment mentioned most often was the contractor segment.
"We figured we would be selling them to the same contractor we are already selling excavators and loaders to," says Vigil of Komatsu. "Our mobiles are competing in different markets than most portables. The market for mobiles is a contractor who doesn’t even know he needs a crusher. He is used to sending small amounts of concrete off-site, or having someone else come on-site to do it. But as trucking costs go up—and they will continue to go up—crushing the small amounts of concrete at the site makes more sense."
McLaughlin from Cedarapids has similar thoughts. "The developing market for these things could be the building contractor who wants to use it at his development site to crush material to use on-site," he says. "Between jobs he could keep it busy doing other small jobs, to the possible detriment of the local recycler."
Trucking costs are cited by Erin’s Houle as one reason mobiles took off overseas. "In Europe trucking is much more regulated, more so than crushing and screening plants. If it has wheels on it, such as a portable crusher, then the regulations are very strict about ABS brakes and other more expensive safety features. It is a lot easier to have 10 track-mounted crushers and only one trailer."
Also in Europe, according to Williamson from Pegson, weight limits on highways are not as stringent as in the U.S., and 16-foot-high trailers are possible. "You can move a 100-ton crusher with fewer restrictions."
He adds that "track-mounted crushers will not take the place of big recycling yards, but sometimes those operators get opportunities for small jobs, where there isn’t much material on-site and the contractor there wants to use the material on-site. Then the mobile makes sense. It would be a complement to the recycling yard’s operations."
Telsmith’s Myers thinks that for a recycler, having only a mobile will limit opportunities. "Most of these machines will be rented through a distributor. The contractor may have it for two weeks or a couple of months as a rental as a way to help take care of a problem, such as size reduction or making backfill. Somebody really into the recycling business is not going to go with that style, they are going to go with something with higher production."
Higher production models may be on the way, McLaughlin says. Crushers for recycling have been mostly small, but he sees size increasing. It’s like it used to be for portables in recycling, he says. In the early days of recycling, impactor sizes used to go only to 40 inches, and jaws were 22 inches by 36 inches or 32 inches by 44 inches. Now impactors go to 60 inches and jaws as big as 63 inches are available for recycling. "And bigger is better in recycling," McLaughlin says.
He adds that the technology for mobiles has come a long way in the past five years. It had to, in order to compete with portables. Greiss adds that now makers of both types of machines will try to match the advantages of the other. "Mobiles will drive portables to be better. The philosophy behind mobiles—less downtime because of quicker set up and take down—will affect portable crusher design." And the winners will be the recyclers buying the machinery.
The author is associate publisher of C&D Recycler and executive director of the Construction Materials Recycling Association and can be contacted via e-mail at turley@cdrecycling.org.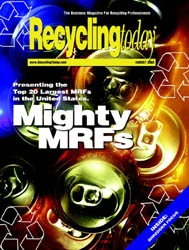
Explore the August 2002 Issue
Check out more from this issue and find your next story to read.
Latest from Recycling Today
- Athens Services terminates contract with San Marino, California
- Partners develop specialty response vehicles for LIB fires
- Sonoco cites OCC shortage for price hike in Europe
- British Steel mill’s future up in the air
- Tomra applies GAINnext AI technology to upgrade wrought aluminum scrap
- Redwood Materials partners with Isuzu Commercial Truck
- The push for more supply
- ReMA PSI Chapter adds 7 members