
While single-screw extruders perform the lion’s share of recycling applications, twin-screw machines have a lot to offer recyclers—especially when the goal is a higher-value end product.
Are twin-screws for everyone? That depends on a number of factors, including the quality and consistency of feedstock and the intended final product, suppliers say. But most agree that twin-screw extruders have a lot to offer when it comes to compounding to add value to recycled materials. Some intriguing possibilities arise when twin-screw extruders and single-screw machines are used in tandem. Suppliers also point to advances that cut energy consumption, lower degradation and allow for processing a wider range of recycled materials.
TWIN-SCREWS: VERSATILE PLATFORM
One proponent of twin-screw extruders for recycling applications is Dustin Kremer, the founder and owner of Uway Extrusion LLC, Marshall, Indiana. In his view, twin-screw extruders are suited particularly to recycling. He points to their flexibility in modifying a formulation to achieve a desired result and to remove volatiles during the extrusion process.

Although the U.S. market has been relatively slow to adopt twin-screw technology for recycling, Kremer says international markets have adapted more quickly. He notes that some large consumer product companies require a certain percentage of postconsumer resin in their packaging and sheet products, making twin-screw extruders a more attractive option.
Kremer says when he gets an inquiry from a potential customer, he asks what the feedstock is and how stable it is. Single-screw extruders may be the most cost-effective option for reprocessing postindustrial scrap; but, twin-screw extruders should be considered if the processor plans to add fillers or plasticizer or to run multiple materials, Kremer says.
Another twin-screw extruder supplier active in the recycling sphere is Feddem GmbH & Co. KG, Sinzig, Germany. Managing Director Dieter Gross points to the advantages of his company’s machines in compounding formulations with improved properties. According to Gross, the majority of Feddem’s customers are producing “upcycled” materials from postindustrial scrap from automotive, consumer products, furniture and other industries.
Gross says the company’s main advantage is gentle processing technology. For engineering plastics, Feddem offers a kneading-block-free screw configuration that results in less shear and minimizes polymer degradation; for glass-reinforced compounds, the kneading-block-free mixing zone provides better glass-fiber distribution.
Twin-screw extruders should be considered if the processor plans to add fillers or plasticizer or to run multiple materials. – Dustin Kremer, Uway Extrusion
For better protection against wear arising from abrasion and corrosion, Feddem offers a steel alloy manufactured by a hot isostatic pressing process. A wear-resistant layer is incorporated into the barrel and also provides protection in the side feeder opening; for corrosion protection, it can be applied to the vent or to the degassing opening. For vacuum-sensitive products, the extruders use side vacuum degassing instead of a conventional vacuum connection on top of the barrel, which Gross says can increase throughput by up to 30 percent compared with conventional degassing.
One U.S.-based supplier of twin-screw extruders that is actively exploring recycling is Entek, Lebanon, Oregon, an established manufacturer of twin-screw machines for compounding and sheet extrusion applications. In addition to supplying new twin-screw extruders, Entek is also a longtime supplier of wear parts—replacement screw and barrel segments—for various twin-screw machines operating in the field in recycling and other applications.
Linda Campbell, Entek director of sales, says the company is exploring leveraging its wear parts business to expand its presence in the recycling industry. “We think wear parts might be a great service to provide for this industry,” she says.
Campbell adds that Entek’s base model twin-screw machine can be configured to meet various needs. “There wouldn’t be a lot of adjustments to fit recycling products because of the flexibility of our equipment,” she says. “Our machine is already a good fit for recycling.”
MORE INNOVATIONS BUILD IN VALUE
Charlie Martin, president and general manager of Leistritz Advanced Technologies Corp., Allendale, New Jersey, says twin-screw extruders have their niche. “Like anything else in recycling, it has to be selectively applied,” he says.
He observes that twin screws are used when there is a compelling reason, such as in processes that incorporate a compounding step sometimes in a tandem arrangement with another extruder.
One example of where twin-screw extruders are well-suited is recycling polyvinyl butyral, which is used for auto windshield safety glass. Regrind contains residual glass, which can be mashed up and put through coarse filtration, then put through a second twin-screw extruder to compound in additional fillers. “It’s the perfect application for a twin to a twin,” Martin says.
Eberhard Dieterich, business unit manager of Coperion Corp., Sewell, New Jersey, shares the view that co-rotating twin-screw extruders are suited to some application-specific recycling processes. “You have to be careful of what is in the mix, the particle-size distribution and what kind of contamination you have,” he says. “If you want to add value, then you usually go with a twin screw because you want to incorporate additives, or reinforce it or make a masterbatch out of it.”
He says the company has supplied co-rotating twin-screw extruders for recycling in-plant scrap, where there is relatively good control over the purity of the material.
Dieterich notes the company’s STS series twin-screw extruder line, which is less expensive than its ZSK extruder, has been attracting attention from operators interested in using it in recycling processes.
He says enhancements to the STS line have potential benefits in recycling processes. Recent improvements include higher torque, allowing the extruder to run at lower speeds, reducing shear and degradation of the melt. The STS line also offers higher wear protection on screw elements.
Coperion has a relationship with recycling equipment supplier Erema Engineering Recycling Maschinen und Anlagen GmbH, Ansfelden, Austria. Erema’s Corema system incorporates a Coperion-supplied co-rotating twin-screw extruder with a single-screw extruder to combine recycling and compounding in a single step. The Erema compactor is coupled with a screen changer; a Coperion twin-screw extruder melts and cleans the polymer, and it also compounds. This integration works with recycled raw material that is not free-flowing, in strips or bulk, or if it is contaminated with solids or liquids.

Mike Horrocks, CEO of Erema North America Inc., Ipswich, Massachusetts, says Erema has offered single-screw extruders for many years. They are robust and relatively inexpensive, he adds.
The Corema system is the company’s response to demand for higher-quality product. “One trend we see is to try to get higher quality and more consistent technical specification of the recycled material,” Horrocks says.
In the Corema system, a single-screw extruder and a twin-screw extruder are used to the best advantage, he says. The single-screw extruder is able to handle a wide variety of materials, including film, foam and fibers. It filters the melt and delivers it to the twin-screw extruder, which homogenizes, devolitizes and compounds the additives. Either Coperion’s STS or ZSK twin-screw extruder can be incorporated into the system, depending on customer requirements.
The process incorporates several steps from start to finish. The recyclate is fed by auger, conveyor belt or roll feeder into a cutting compactor drum, which also drives off moisture. At the bottom of the drum is a counter-rotating cutting tool designed for high throughput. The single-screw extruder melts the material, which goes through a melt-filtration system, either a backflush filter or Erema Laser filtration system that is designed for high contamination content. After going through the filter, the melt is introduced into the twin-screw extruder via a melt pipe or melt pump. At the end of the twin-screw extruder is a pelletizing system.

MAS (Maschinen und Angenbau Schulz) GmbH, Hobelweg, Austria, differentiates itself in the twin-screw extruder market with its co-rotating conical NCT twin-screw design. Hartmut Bendfeldt is president of eFactor3 LLC, Pineville, North Carolina, which represents MAS in the U.S. He says the conical screw efficiently processes low-bulk-density material, such as flake and bottle scrap. “Our screw design allows it to pull in shredded material that weighs 3 pounds per cubic foot,” he says.
He notes that the MAS machine is suited to processing recycled polyethylene terephthalate (PET) and polylactic acid (PLA). The NCT extruder has a short barrel, reducing dwell time and providing good homogenization. It also requires less energy to turn the screws; MAS says that energy consumption of its conical twin-screw extruder is 20 percent to 40 percent lower than conventional twin-screw extruders.
The MAS extruder can handle materials composed of up to 50 percent to 60 percent talc or calcium carbonate. It does not use a side feeder, so it is limited in terms of accepting certain types of glass fiber. On the other hand, Bendfeldt notes that the NCT is very efficient in taking in postconsumer flake and filler through the feed throat, essentially recycling and compounding in a single step.
MAS complements its NCT extruder with cleaning and filtration equipment before and after the extrusion stage. At Fakuma, it announced that it increased the capacity of its DRD waterless resin cleaning system. The latest DRD model doubles the throughput by increasing the number of rotor blades in the drum, with only a minimal increase in energy consumption. MAS also has increased the capacity of its continuous disk melt filter after the extruder. The CDF 500D-P melt filter has two parallel disc melt filters, with a usable filter area of about 970 square inches and a throughput of 13,228 pounds per hour.
Get curated news on YOUR industry.
Enter your email to receive our newsletters.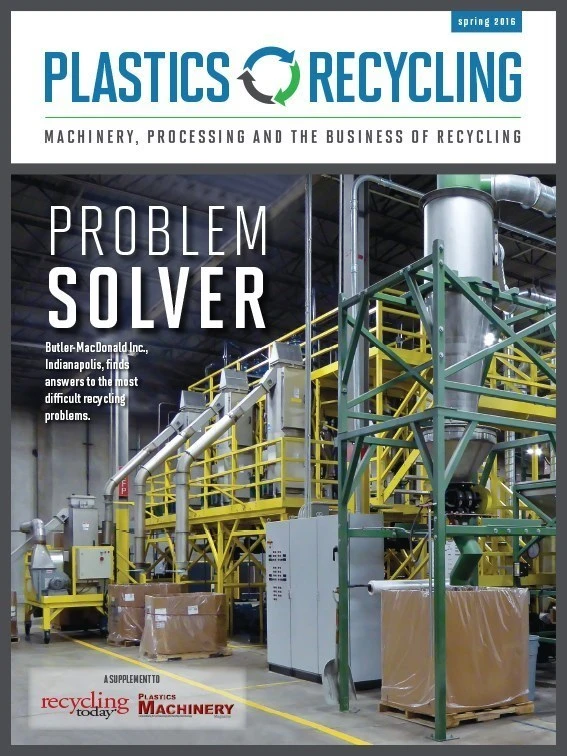
Explore the April 2016 Plastics Recycling Magazine Issue
Check out more from this issue and find your next story to read.
Latest from Recycling Today
- Astera runs into NIMBY concerns in Colorado
- ReMA opposes European efforts seeking export restrictions for recyclables
- Fresh Perspective: Raj Bagaria
- Saica announces plans for second US site
- Update: Novelis produces first aluminum coil made fully from recycled end-of-life automotive scrap
- Aimplas doubles online course offerings
- Radius to be acquired by Toyota subsidiary
- Algoma EAF to start in April