The newspapers, bottles and cans placed in the curbside recycling bin or dropped off at the collection center ultimately make their way to a material recovery facility (MRF) for sorting, processing and shipment to a consuming manufacturing plant.
MRFs have evolved and grown over the past two decades, as recycling programs have expanded and—in some cases—consuming plants became hungrier for more material that could be culled from the residential recycling stream.
The old newspapers (ONP) grade of scrap paper is now a major part of the feedstock going into secondary pulp that is used to make a variety of paper products. Aluminum used beverage containers (UBCs) are valued as feedstock to make can stock and other grades of aluminum, while steel cans and most forms of plastic enjoy steady if unspectacular markets.
The MRF has thus become a hub of processing and shipping activity that helps supply a number of industries with secondary raw materials.
WAVE OF THE FUTURE |
The trend toward more single-stream recycling programs has generated a tremendous amount of interest. Advocates of the sorting and processing procedure note the ability to collect larger amounts of material most cost effectively. However, opponents feel that as recyclables are commingled together the quality of the collected material significantly declines, resulting in increased residue and lower value of the material. During the Paper Recycling Conference & Exposition, held in June in New Orleans, three speakers weighed in on the positives and negatives to this method. Speakers at the panel included a representative from a waste management firm, a representative from a Canadian-based paper company, and a consultant to the solid waste and recycling industry. Brian Taylor, editor of Recycling Today magazine, noted that over the past decade, "most communities remained committed to curbside recycling, but public officials also scrutinized the cost of operations much more carefully. On the collections end, cost savings were sought by putting fewer trucks with fewer people on the road, with these trucks ideally running faster routes while collecting more material." To deal with the material in a cost-effective manner, Taylor continued, "Advocates (of single stream methods) see single-stream processing and mechanical sorting advances as the hope toward the maximum recovery of recyclables. The short-term pain may be blurred paper grades and some rejected shipments, but ultimately MRFs are being equipped to reliably handle a greater percentage of the solid waste stream while shipping out a number of marketable secondary commodities." Harvey Gershman, president of the consulting firm GBB Inc., Fairfax, Va., ticked off some of the biggest disadvantages to single stream. One is the residue in the paper, especially glass. "Glass in the single stream is a problem. Additionally, said Gershman, "There are higher processing costs. It costs more to unscramble a more scrambled egg. There are more sorting costs. In a dual stream system glass is more easily sorted. That doesn't happen in a single stream flow." While glass can be a problem, Gershman noted that the amount of glass in the recyclables stream is declining. According to Gershman, glass right now constitutes only around 5 percent of the average collected stream. With this in mind, he adds that it may be a better move to remove glass from the materials collected. Concerning the growth of single stream MRFs, Gershman noted that there was one of these types of MRFs less than 15 years ago. Now, there are around 85 single-stream MRFs, with more expected to be added over the next several years. Rina McGuire, with Cascades, a large Canadian-based forest products company, said that the company "didn't care" whether the material came from a single or multi-stream source. While the company didn't come out strongly on either side, she did stress that the quality of the material was essential. Additionally, anyone looking to ship to the company's mills also needs an ample quantity of material. One of the biggest downsides to single-stream programs can be the low quality of the processed material. "If you need more manual sorting it is very costly. There is a higher level of contamination." To achieve higher quality, McGuire stressed that the ideal situation is to take in material from a same group of suppliers. At the same time, the need for price stability is a major issue for the material. Steve Ragiel, vice president of recycling for Waste Management Inc., Houston, said some of the issues with current recycling programs include high collection costs, high processing costs, extremely volatile commodity pricing, and the capital intensive nature of programs while extremely tight municipal budgets. The primary advantages for single stream collection is the lower collection cost and an adequate supply of material for mills, Ragiel noted. He added that while many opponents of single stream processing cite glass contamination as a big problem, he feels that with the proper sorting, there are some viable end markets for the material. A key type of equipment to use is an optical sorting system to extract glass, he added. Backing this opinion, Ragiel said that Waste Management already has more than a dozen single stream recycling facilities, with a number of other facilities scheduled to be re-opened by the end of the year. |
DEFINING A MRF
For purposes of our list, Recycling Today chose to include only facilities that process 50 percent or more residentially generated material. Certainly many facilities with a higher mix of commercially generated material also take in bottles, cans and other curbside commodities. These facilities can rightly be considered as material recovery facilities. It should also be noted that mixed waste procesing faclilities were not considered for this particular chart.
To some extent facilities that concentrate on the residential stream are designed to do more sorting and to process a greater variety of materials. Without question, though, when Recycling Today presents a list next year of the nation’s largest paperstock plants, the vast majority of these will also accept both residentially-generated paper grades, as well as cans and bottles, in addition to commercially-generated material.
Unfortunately, designating a facility as either a MRF or a paperstock plant is somewhat arbitrary. Many facilities with a commercial to residential split ranging from 51/49 to 70/30 may look and sound like a MRF, but because a line had to be drawn, they will be considered as paperstock plants for purposes of creating our lists. The line is blurry, however, and we are open to suggestions for other definitions or criteria for designating a plant as one or the other. Please feel free to contact the editors with your thoughts.
When ranking the MRFs, we chose the tonnage of secondary fiber shipped from the facility as the lead criterion for ranking. Although the processing of containers is of equal importance at most MRFs, the container mix can vary greatly depending on a MRFs location (deposit system state or non-deposit system state; collecting from single-stream, dual stream or commingled routes; whether glass—a heavy but not especially valuable commodity—is part of the mix). Thus, secondary fiber was seen as a benchmark that would vary the least as an incoming recyclable from plant to plant.
Some of the sources we spoke to were unsure whether this was the best way to rank MRFs, and it is almost certainly an imperfect way. As with the 50/50 split criterion, we are willing to consider an alternative method of ranking the MRFs. Call us, send us a letter, a fax or an e-mail (btaylor@RecyclingToday.com) with suggestions and comments.
Following is a chart and brief description of 20 facilities that met the designation of a MRF by our definition. Recycling Today wishes to thank Eileen Berenyi and Governmental Advisory Associates Inc., Westport, Conn., publishers of Materials Recycling and Processing in the United States. The 2001-2002 edition of this directory was the basis for much of the information presented in the chart and article that follows.
Those interested in purchasing this comprehensive directory of recycling facilities can do so through the Online Bookstore found at www.RecyclingToday.com. The directory is also available in CD-ROM format.
1) CHARLESTOWN RECYCLING CENTER
This large recycling center, formerly operated by Prins Recycling and now owned by Casella Waste Systems Inc., Rutland, Vt., processes material collected by Casella and other haulers throughout the Boston metropolitan area. Bollegraaf sorting equipment and two horizontal balers made by Bollegraaf help the plant process sizable amounts of fiber and containers. KTI Inc. purchased the former Prins facility when it was a growing publicly-traded company on its own. Casella’s purchase of KTI meant the facility changed hands once again, although through all the ownership changes it has continued to process a sizable amount of secondary fiber, plastic, glass and metal containers.
This massive Seattle MRF processes material collected by the Rabanco regional solid waste company, now owned by Allied Waste Inc., Scottsdale, Ariz. Several different Harris balers are used to compress the newspapers and other paper grades, as well aluminum and steel cans collected from throughout the Seattle area. The MRF is located in an old steel mill that was retrofitted by Rabanco in the late 1980s. In addition to curbside commodities, some municipal solid waste, yard trimmings and C&D debris are handled at the site.
3) RESOURCE MANAGEMENT
This Chicago area plant processed some 273,500 tons of material in 2001, according to Resource Management president Cal Tigchelaar. The 150,000-sq. ft. plant was expanded in 2000. The MRF takes in material collected by haulers in Illinois, Wisconsin, Indiana, Michigan and Missouri.
4) WASTE MANAGEMENT – MINNEAPOLIS
Waste Management Inc., Houston, recently consolidated several Twin Cities operations into one large MRF, located in Minneapolis. This mega-facility takes in both residential and commercial material, with the residential segment supplying the greater balance. So far in 2002, the plant is churning out fiber at the rate of 8,000 tons per month.
5) GROOT INDUSTRIES/CROWN DISPOSAL
A nearly even split of residential and commercial materials are brought to this series of processing lines. A sorting system made by Count Recycling Systems, now a division of CP Manufacturing, National City, Calif., helps separate paper from containers and paper grades from each other. A solid waste transfer station and C&D facility are co-located on the site.
6) WESTBURY-OMNI RECYCLING
This Long Island MRF handles an even split of residential and commercial material. Harris balers help churn out ONP and OCC grades, as well as PET and HDPE plastic bottle bales and bales of tin-plated steel cans. (There are few UBCs running through the plant due to New York’s deposit and return system, under which residents seldom place their aluminum cans in curbside bins.) Material comes in from communities on Long Island as well as from Manhattan and other New York City boroughs.
7) BFI RECYCLING - MINNEAPOLIS
A multi-county area in and around the Twin Cities area is served by this MRF, which features CP Manufacturing equipment feeding Harris balers. A sizable number of containers of all types are processed at the plant, in addition to the considerable fiber tonnage. The facility came online 10 years ago, in 1992.
This MRF takes in recyclables collected from residents in the City of Miami, Miami Beach and other communities in Dade County, as well as from unincorporated areas of the county. Harris balers prepare the fiber tonnage, metal cans and plastic bottles for shipment. The MRF was upgraded in 1998 to handle its growing stream of commingled materials. OCC from cruise ships, which must be processed separately, also makes its way into the plant.
9) POTENTIAL INDUSTRIES
This Long Beach area facility takes in residential material collected from haulers throughout southern California. Bollegraaf sorting and baling equipment and Logemann Bros. baling equipment processes the recyclable stream heading into this plant, which draws material from Los Angeles, Orange and San Diego counties. Potential Industries also handles material from commercial sources.
10) BFI OF NEW YORK – BROOKLYN
This plant’s prior status as a shipper of scrap paper puts it on our list, although it recently stopped accepting paper and instead concentrates on containers. Much of the curbside material collected in New York City is brought to this plant, as well as additional material from parts of Long Island. The-150,000 sq. ft. plant’s Harris balers are used to process ONP, OCC and mixed paper, and still compress plastic bottles and tin cans, as well as some other grades of metal. Pending changes to New York City’s recycling program could reduce the amount of material flowing in, or further change this MRF’s mix of materials.
The MRF serving this Florida county was built to handle high volumes of material, and has been doing so. (See "High Volume MRF Seeks Efficient Systems," April 1999 Recycling Today, or on the Web at www.RecyclingToday.com.) The plant was built and designed in 1990 by RRT Design, Melville, N.Y. and expanded in 1998. Material collected from Palm Beach County and adjacent counties adds up to more than 85,000 tons of residentially generated secondary commodities shipped. An adjacent commercial MRF processes an additional 20,000 tons per year of OCC and other paper grades.
12) ISLAND RECYCLING INC.
With landfill space hard to find in Hawaii, the residential processing facility started by a scrap recycling company has found steady business serving drop-off boxes in Honolulu, surrounding communities and military bases. An Enterprise baler handles ONP, OCC, mixed paper, telephone directories, aluminum cans and plastic bottles.
13) PRINCE GEORGE’S COUNTY MRF
A sorting system with Bollegraaf and Bezner equipment helps sort out the ONP, plastic containers, UBCs, steel cans and glass bottles heading into this 65,000 sq. ft. MRF. Waste Management is the current operator of this MRF, which has two processing lines and was formerly run by CRInc. Material comes from Prince George’s County as well as adjacent Arlington County, Va.
Recyclables collected from some 300,000 households in upstate New York head to this Kenmore, N.Y., MRF run by BFI-Allied Waste Inc. About 70 percent of the material processed at the plant comes from residential programs in several counties. ONP, OCC and mixed paper are all baled at the plant, as are bottles and cans. The plant has served the Buffalo area for more than ten years, opening in 1991.
15) NORCAL TURF/WEST COAST RECYCLING CO.
San Francisco-based waste hauler Norcal Waste Systems Inc. owns this San Francisco "TURF" (Total Urban Recycling Facility), which is operated by West Coast Recycling Co. Norcal, which has the San Francisco residential recycling contract, sends the material it collects here, where it is sorted and much of it is baled by Harris balers. Due to California’s deposit and return system, few UBCs and a relatively small amount of plastic containers are baled here. ONP is by far the leading commodity, followed by glass, steel cans, and HDPE plastic.
16) CR&R INC.
A portion of the residential recycling stream from the City of Los Angeles comes to this facility, as do materials collected from other parts of Los Angeles County and parts of Orange, Riverside and San Bernardino Counties. ONP, mixed paper, glass, OCC, steel cans and HDPE milk jugs make up the majority of material processed at the plant. Some materials accepted come from single-stream collection programs, while others come from dual-stream programs.
17) LAKE COUNTY MRF
Waste Management Inc. operates this Chicago area plant, which takes in recyclables from more than 35 municipalities in northeastern Illinois. A sorting system helps separate several shippable grades, including ONP, glass, mixed paper, OCC, HDPE plastic, steel cans, PET plastic and aluminum cans (from highest tonnage to lowest).
18) BFI RECYCLERY – NEWBY ISLAND
A steady stream of residentially and commercially-generated material (roughly a 50/50 split) comes into this central California facility. Material from San Jose, Santa Clara and other parts of Silicon Valley—as well as from Alameda County—is brought in by waste and recyclables haulers. Commingled materials are accepted at the MRF, which has a CP Manufacturing sorting line.
This Santa Rosa, Calif., facility, operated by Waste Management, traces its MRF origins all the way back to 1978 and some of the earliest curbside collection programs in the U.S. It has been upgraded periodically, and now features a sorting system feeding Enterprise balers. Residential recyclables are collected from Sonoma and Mendocino Counties.
20) METALIFE RESOURCES
Residential recyclables from the Pittsburgh area and other parts of western Pennsylvania are processed at this MRF, formerly operated by Weyerhaeuser Recycling. For more than 10 years, recyclable paper grades and containers have been hauled to the MRF by residential collection contractors. A pair of Harris balers helps prepare the recyclables.
A CHANGING MRF SCENE
One of the difficulties in identifying the right facilities for a Top 20 MRF list is the constant overhauling and consolidating of facilities taking place in the U.S.
As solid waste companies such as Waste Management Inc., Allied Waste-BFI and Casella Waste Systems acquired assets throughout the late 1990s and into this decade, they have examined their transfer station and MRF facilities and made decisions concerning the upgrading of some facilities and the closing of others.
Some of these companies have also made the decision to outsource much of their recyclables processing. This is resulting in the current and future expansion of many MRFs owned by smaller, regional companies. While these plants may not have handled enough tonnage in 2000 or 2001 to make this list, they may have subsequently upgraded and expanded to the point where they belong in the top 20.
The ability to obtain tonnage information at all (whether from 2000, 2001 or projected for 2002) has not been universal. Some companies respond to the inquiries for tonnage figures while others choose to keep such information confidential.
Our preference, of course, is to recognize those MRFs that truly are putting themselves in the elite class of recyclables processing.
If you know of a MRF that should be in our Top 20 or is growing and may well qualify the next time we publish this list, please let us know. Contact Brian Taylor at btaylor@RecyclingToday.com.
The author is editor of Recycling Today and can be contacted via e-mail at btaylor@RecyclingToday.com. Recycling Today assistant editor DeAnne Toto helped with the research for this feature.
Get curated news on YOUR industry.
Enter your email to receive our newsletters.
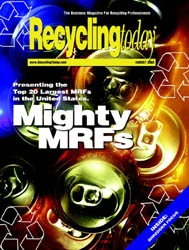
Explore the August 2002 Issue
Check out more from this issue and find your next story to read.
Latest from Recycling Today
- Athens Services terminates contract with San Marino, California
- Partners develop specialty response vehicles for LIB fires
- Sonoco cites OCC shortage for price hike in Europe
- British Steel mill’s future up in the air
- Tomra applies GAINnext AI technology to upgrade wrought aluminum scrap
- Redwood Materials partners with Isuzu Commercial Truck
- The push for more supply
- ReMA PSI Chapter adds 7 members