
Ron Shumaker had worked his entire career in sheet metal manufacturing, but after abruptly being laid off in his early 40s, he figured it was time for a change—a change that allowed him and his family to control their destiny.
In April 1990, he took a chance and answered an ad in the back of a newspaper promoting a business for sale in Decatur, Illinois—Decatur Recycle Paper Co.—leaning into what his son Todd Shumaker says is a lifelong entrepreneurial spirit.
“His mom was an entrepreneur who owned a business, and on my mom’s side, her dad and mom owned a jewelry business, and I think that spirit kind of always just ran in the family,” Todd says.
“He visited [the business] and was intrigued by it. He’d always been around manufacturing, and this had a manufacturing component to it along with the environmental components. So, quite literally, he risked the family’s security and bought this small little business that provided recycling services.”
The Shumakers rebranded Decatur Recycle Paper Co. to Midwest Fiber Recycling and expanded the company from a single facility in Decatur in 1990 to six facilities across the Midwest.
The company’s latest venture involves a partnership with Circular Services, a developer and operator of circular economy infrastructure in the U.S. that is managed by New York-based Closed Loop Partners, which acquired Midwest Fiber Recycling in December 2023 under its recycling arm, Balcones Recycling—a move the Shumakers expect will be good for business and good for recycling.
“It’s bittersweet transitioning a family-owned business,” says Todd, director of new business development at Midwest Fiber Recycling. “But I think all the employees at Midwest Fiber are excited to continue this journey with Circular Services and playing out their game plan for recycling and what we can do for them in the Midwest.”
Building from the ground up
When Ron purchased Decatur Recycle Paper Co., his sons, Todd and Mike, were in high school, and their entry into the business was at the ground floor. “We had, I think, two full-time employees, and we had more cats than employees,” Todd jokes. “It’s a sign of a well-run recycling center—enough cats to take care of the mice.”
The site had an old baler and some additional older equipment that was not suitable for processing much material, and Todd describes that period in the early ’90s as not necessarily recycling friendly. “Businesses were on board, but the ones that were on board were really just doing it for the financial gains, in most cases,” he says.
“Fortunately, over the years, we continued to grow; the markets were good, [and] my dad was a good operator.”
In 1995, the company relocated from a 5,000-square-foot facility to a 25,000-square-foot facility, and it was then that the Shumakers realized the potential of recycling in the Midwest.
“We said, ‘Man, we’ve got to reach out and go further,’” Todd says. “So, we continued to acquire and, through partnerships with municipalities and haulers in the area, we grew additional facilities throughout Illinois and Indiana over the next 30-odd years.”
By then, the name Decatur Recycle Paper Co. didn’t fit the business anymore and, the Shumakers rebranded to Midwest Fiber Recycling in 2001.
As the company rebranded, it also was looking to continue to grow its footprint and acquired Weyerhaeuser Recycling in Normal, Illinois, setting Midwest Fiber up for what has been continued growth in the Greater Chicago market.
“They were always a really tough competitor for us,” Todd says of Weyerhaeuser. “We were able to grow and acquire that facility and, from there, we established some relationships with some of the larger national waste haulers and the regional waste haulers who weren’t happy with the situation they had in Peoria, Illinois, and the process they used, so they reached out and said, ‘[If] we committed volume to you, would you open and expand into the Peoria market?’”
After establishing its Confidential On-Site Paper Shredding (C.O.P.S.) business in 2003, which processes more than 3,330 tons of recovered paper annually, Midwest Fiber opened a second site in Peoria in 2005—a full-service collection and baling facility—and that inspired more growth.
“The Peoria expansion was really what got us [thinking], ‘Maybe we need a downstate processor for single stream,’” Todd says. “That’s when we [decided] to open our single-stream MRF [material recovery facility] in Normal, Illinois.”
Midwest Fiber opened its MRF in Normal in 2011, co-located with its commercial/industrial processing facility and loading dock.
Eugene, Oregon-based Bulk Handling Systems (BHS) supplied the system for the Normal MRF, and because Midwest Fiber wanted it co-located with its commercial/industrial recycling facility, specific needs had to be addressed.
“We were a little landlocked, and BHS designed a very efficient system in a relatively small footprint,” Todd says. “We’ve done several upgrades to the MRF, as well, typically working with BHS on those upgrades.”
The MRF processes approximately 160,000 tons annually and features an optical sorter from the BHS National Recovery Technologies (NRT) business unit; six robotic sorters from Louisville, Colorado-based technology provider Amp, with four installed in 2021 and two more installed last year after experiencing rapid growth; and a baler supplied by Bakersfield, California-based Sierra International Machinery.
“We built the facility, and fortunately the volume has followed, which has led to those improvements, like adding an optical sorter,” Todd says.
“We’ve added additional screens as well to help with cleaning the end products, specifically the containers and the missed paper, to make sure we have a good, clean, salable product.”

Two years after construction was completed on the Normal MRF, Midwest Fiber acquired Data Management Services in Terre Haute, Indiana, to try its hand in an unfamiliar market.
“It gave us a whole different market to capture,” Todd says. “It’s a little bit further away—about two hours from our next closest facility—[and] there are different paper mills we work with [and] different suppliers in a growing area.”
Midwest Fiber’s final acquisition was Community Resource Inc. (CRI) of Urbana, Illinois in 2017—a business that services the Urbana-Champaign region. The market features the University of Illinois, which Todd says has a “very robust” recycling program and a multi-family recycling program Midwest Fiber took over when it bought CRI.
The purchase of CRI rounded out Midwest Fiber’s six-location footprint, which Todd describes as five traditional commercial/industrial baling facilities that complement its MRF in Normal.
“We operate like a hub-and-spoke approach,” he says. “Strategically, [the] Normal [site] is our main processing facility, and our other facilities can become spokes where they may be an hour away, and the hauler or municipality there will dump material, and we’ll transload it to the main processing facility.
“We’ll do that with other recyclers who have that same challenge we had—they’re in a relatively small community, [and] there’s not enough material being collected to build a MRF. So, we’ll work with them to gather material, and it gets transferred back to [us] for processing.”
“At the end of the day, if we can get all of us working on the same page together, we can make a lot of great things happen.” – Todd Shumaker, director of new business development, Midwest Fiber Recycling
Evolving its operations
Midwest Fiber’s supply base covers approximately a 100-mile radius from each of its facilities, spanning from the South Side of Chicago to northern St. Louis and into Indianapolis.
The company employs a four-step approach when consulting with potential suppliers: analysis, alignment, adoption and account management. It involves meeting with suppliers to determine goals and challenges, collecting data and implementing processes to make procuring material as seamless as possible.
“[Suppliers] may end up with five or six different types of commodities that will end up back at our recycling facilities, and we’ll grade them, pay them accordingly and take their small volumes and combine it with other people’s volumes—that’s where the bulk of those clients come from,” Todd says.
As part of its evolution, Midwest Fiber started a brokerage business just before the onset of the COVID-19 pandemic, and Todd says that segment has grown “significantly” over the last three years.
The company specializes in multiple materials, including paper, plastics and metals, in full and partial loads, and markets more than 1,100 truckloads per month. Shumaker says the lack of travel during the pandemic actually helped build the brokerage unit and, in 2023, Midwest Fiber’s brokerage division handled more volume than its recycling facilities for the first time in company history.
“We had really great salespeople that couldn’t go out and make sales calls, so we’ve grown a relatively robust brokerage division that’s helping other recyclers, manufacturers and distribution facilities market their products mill-direct with the partners from our plants,” he says.
“Consistency of movement is critical in this industry,” Todd continues. “Most of us don’t have large warehouses where we can just stockpile bales of paper when market conditions aren’t favorable. Matt McDermott, who takes care of commodity sales, helps to make sure we have contracts in place. So, we’ll try to do contracts with mills to make sure we have some consistent movement. That helped us in our brokerage, as well.”
The growth of the business has led to an increasing number of employees, so Midwest Fiber implemented its Entrepreneurial Operating System to help manage the business and communicate with employees after recognizing not everyone was on the same page when it came to the goings on at Midwest Fiber.
“It became clear to us a few years ago that, while my brother and I and our leadership team maybe had a really clear vision, we weren’t great at giving that vision to the employees, so they didn’t know where we were going,” Todd says.
The key to maintaining strong relationships among company leadership and its broader employee base, however, has been staying present in the day-to-day operations—getting to know the employees who work the floors every day and walking through the facilities to create more meaningful connections.
“It has been a differentiator for us over all the years that we’re very connected to the employees we have,” Todd says.
“At the end of the day, if we can get all of us working on the same page together, we can make a lot of great things happen rather than just one or two people working on them. What we found is that, in the past, we had one or two people trying to do these things, but to steer a ship right when everybody else is going left didn’t work very well. Now, everybody is rowing in the right direction, and we found a lot of momentum in that.”

A new chapter
Late last December, Circular Services announced it had acquired Midwest Fiber, bolstering the portfolio of MRFs operated by Circular Services’ recycling arm, Balcones Recycling.
Circular Services operates several circular materials management companies, including Austin, Texas-based Balcones Recycling, promoting recycling to municipalities across the U.S.
Prior to the acquisition, Balcones was among the largest independent recycling companies in the U.S., handling more than 1 million tons of recyclables annually through its operations in New York, New Jersey, Florida, Texas, Arizona and Arkansas. With the addition of Midwest Fiber’s operations, it will have 18 MRFs within its footprint.
“For us, part of it was ... trying to figure out what the next transition was going to look like for my brother and me when we wanted to leave the business. Trying to transition it to the next generation, we knew it was going to be pretty challenging—one, is [if there are] family members who are interested in this business and, two, we had growth goals we probably were going to have a real challenge meeting on our own,” Todd says.
That’s when the Shumakers approached Circular Services to see if it would be a good fit to help Midwest Fiber realize its regional growth goals.
“It just seemed like such a natural fit by what they’ve done in other markets,” Todd says. “Quite truthfully, the fact that they really don’t have a footprint in the Midwest and with their goal to continue to grow the circular economy in an area where they didn’t have a footprint already [as well as us] having a strong leadership team that could continue to expand the Midwest market for them, it just seemed like a really natural fit.
“I think a lot of their core values aligned with our company’s core values. For that, we were really excited when [Circular Services] came along.”
In the last few years, Balcones Recycling has embarked on several major projects, including a $61 million MRF in San Antonio set to open in 2026. It also has won recycling contracts in San Antonio and Phoenix.
Todd cites those initiatives as examples of the growth he and his family see for Midwest Fiber with Circular Services.
“We’ve got a great reputation in the Midwest, [and] Circular Services has a great reputation in the other areas they market in, and just providing those two together is going to bring opportunities in the Midwest as well—ones that we search out, and ones that get brought to the table,” he says.
“We hope to be able to replicate those same things here in the Midwest.”
Get curated news on YOUR industry.
Enter your email to receive our newsletters.
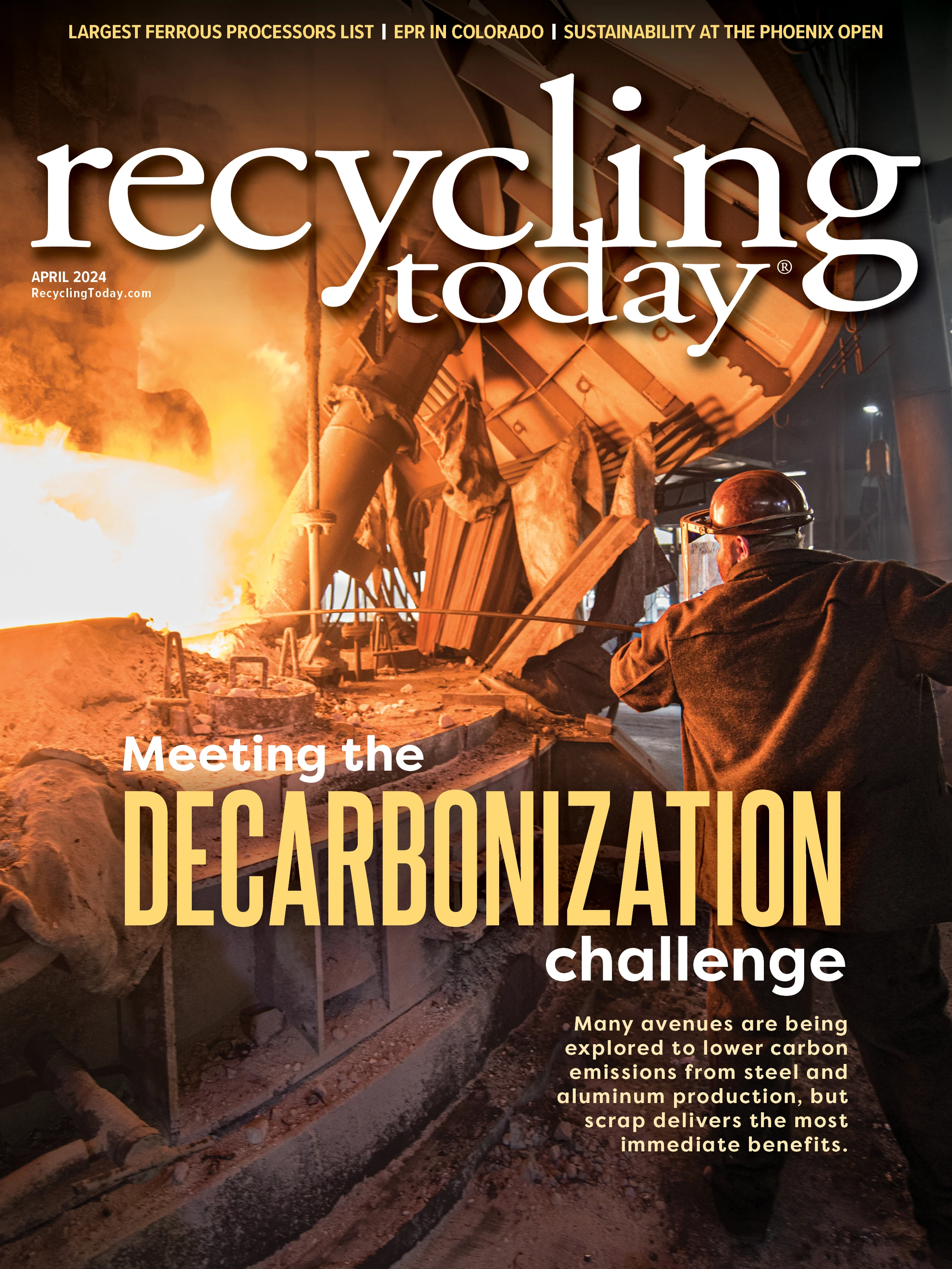
Explore the April 2024 Issue
Check out more from this issue and find your next story to read.
Latest from Recycling Today
- Nucor expects slimmer profits in early 2025
- CP Group announces new senior vice president
- APR publishes Design Guide in French
- AmSty recorded first sales of PolyRenew Styrene in 2024
- PRE says EU’s plastic recycling industry at a breaking point
- Call2Recycle Canada, Staples Professional expand partnership
- Circular Services breaks ground on north Texas MRF
- Tariff uncertainty results in choppy nonferrous scrap flows