_fmt.png)
When Nucor Corp., Charlotte, North Carolina, announced the site of its first electric arc furnace (EAF)
In North America, Dallas-based Commercial Metals Co. (CMC) has had a
Globally, Italy-based steel mill equipment maker Danieli has been setting up
American acceptance
Danieli, although based in Italy, has been a supplier of melt shop equipment to North America for several decades.
When Danieli began approaching current and prospective customers about its

In early December 2009, CMC held a grand opening ceremony at the Mesa mill, which was designed to produce some 280,000 tons of steel rebar annually, using ferrous scrap as 98.5 percent of its feedstock.
“The eyes of the world are looking at this plant, which is the first of its kind in the United States,” CMC then-CEO Murray McClean said at the time. He said the new technology would allow the company to melt, cast and roll steel in one uninterrupted process, promoting higher yields and lower energy costs.
Less than six years later, in July 2015, CMC announced it had selected Durant, Oklahoma, as the location for its second
“The location of the mill in Durant, Oklahoma, 80 miles north of Dallas, will allow us to better serve a growing North Texas market as well as expand into markets in Oklahoma, Kansas, Nebraska, Arkansas
In 2017 it was Nucor’s turn to invest in the
In November 2017, Nucor announced plans to build a $250 million rebar
“This rebar
“We are encouraged by the tremendous support received by the state and local community in Missouri, and Nucor has decided to pursue an additional micromill project.” – Dave Sumoski, Nucor
Rebar supply to the Kansas City, Upper Midwest and Plains states markets currently travels long distances, giving the
A Nucor executive also disclosed that the steelmaker is seeking a site for a second rebar
According to
Global reach
Mills operating at a suitable scale to serve a region is one part of the
At the SteelMint 2017 Steel Scrap & Raw Materials Conference Asia in Bangkok in the fall of 2017, Sridhar Rao, who works from Mumbai for Danieli, described the evolution of the company’s
“Micromills make minimills smaller and more profitable,” Rao said. They use Danieli’s FastArc and FastCast technologies, he said, to continually charge scrap and engage in “endless casting and rolling” to create a process that goes from scrap to finished billets to a rolling mill to (depending on the type of steel produced) spooling lines, all in a relatively small facility.
Rao said customers in Greece, the United States
That represents a considerable productivity advance compared with an early-stage installation in Italy in the late
Sponsored Content
Labor that Works
With 25 years of experience, Leadpoint delivers cost-effective workforce solutions tailored to your needs. We handle the recruiting, hiring, training, and onboarding to deliver stable, productive, and safety-focused teams. Our commitment to safety and quality ensures peace of mind with a reliable workforce that helps you achieve your goals.
Sponsored Content
Labor that Works
With 25 years of experience, Leadpoint delivers cost-effective workforce solutions tailored to your needs. We handle the recruiting, hiring, training, and onboarding to deliver stable, productive, and safety-focused teams. Our commitment to safety and quality ensures peace of mind with a reliable workforce that helps you achieve your goals.
Sponsored Content
Labor that Works
With 25 years of experience, Leadpoint delivers cost-effective workforce solutions tailored to your needs. We handle the recruiting, hiring, training, and onboarding to deliver stable, productive, and safety-focused teams. Our commitment to safety and quality ensures peace of mind with a reliable workforce that helps you achieve your goals.
Subsequent advances in output have been more rapid, he said, with the
Rao listed several factors in
- The equipment was originally designed for further improvements.
- A culture of teamwork was cultivated
between customers and suppliers. - Danieli tries to offer the “full support” of its personnel during the stages of plant ramp-up.
- The continuous involvement of the company’s R&D personnel before, during and after plant startup has led to ongoing improvements.
- The overall optimization of maintenance plans allows mills to operate in peak conditions.
Rao said Danieli is targeting a 100-tons-per-hour output rate in a future installation, adding that he was convinced the concept can make scrap-fed EAF mills “smaller and more profitable for straight bars, wire rod
In addition to its established minimill and
In parts of the world where induction furnaces have been shut down because of environmental or various other regulatory concerns, Danieli says

On its website, Danieli says the concept “calls for a mill that exploits the particular local availability of scrap or iron ore, as well as the market for the finished product, and converts raw materials to finished products in the most efficient way, with extremely short transport requirements. The
The company says the rated capacity of its
Whether such new types of EAF mills are set up in North America or farther afield, the notion of scrap-fed steel production techniques retaining and expanding overall steelmaking market share is likely to strike ferrous scrap processors and shippers as welcome news.
Get curated news on YOUR industry.
Enter your email to receive our newsletters.
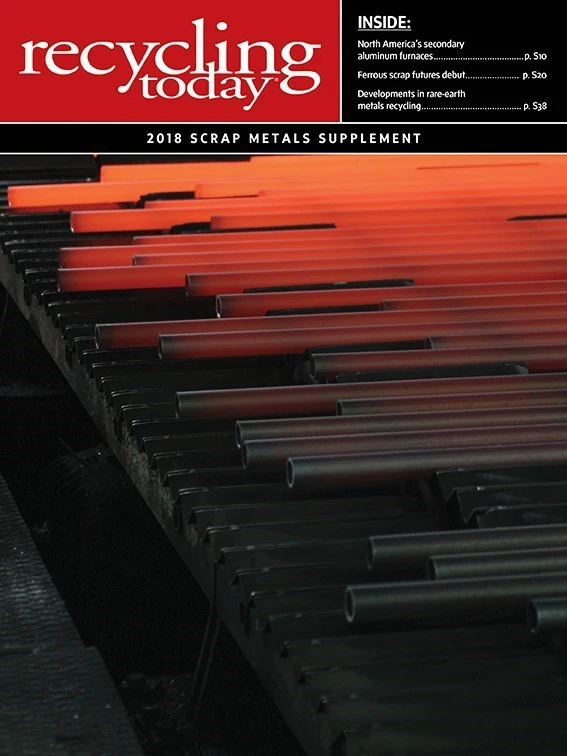
Explore the January 2018 Scrap Metals Supplement Issue
Check out more from this issue and find your next story to read.
Latest from Recycling Today
- Athens Services terminates contract with San Marino, California
- Partners develop specialty response vehicles for LIB fires
- Sonoco cites OCC shortage for price hike in Europe
- British Steel mill’s future up in the air
- Tomra applies GAINnext AI technology to upgrade wrought aluminum scrap
- Redwood Materials partners with Isuzu Commercial Truck
- The push for more supply
- ReMA PSI Chapter adds 7 members