
A high-rise targeting exclusive clientele in Florida states, “Waldorf Astoria is known for providing unforgettable experiences in landmark destinations worldwide. Rising 1,049 feet above Biscayne Bay, the striking tower will be the tallest building south of Manhattan, offering breathtaking views and signature experiences.”
The 100-story residence will be breathtaking, but before one can enjoy the luxury, the building must be erected. Construction began in late 2022 and is expected to be completed in 2027, with more than 88 percent of the 360 private residences already sold. Within its glamorous façade is a fundamental recycled metal: rebar.
Florida-based Advanced Rebar and Engineering Services (ARES) is the main rebar fabricator for this residence project. “The sheer size of the construction and architectural requirements makes the project exciting and challenging, and we are preparing accordingly,” says Mario Esquivel, plant manager at ARES.
The company is meeting the project’s rebar needs primarily with Nucor Corp.-produced steel from the Charlotte, North Carolina-based steelmaker’s Frostproof rebar micromill in Florida, which is about two hours from the site. Esquivel lists the proximity, flexible rebar size and good service as the driving factors for their successful working relationship.
For the Waldorf Astoria and many other projects ARES undertakes, the spooled rebar material provides fabricating advantages, including quality, processing efficiencies and special length planning that saves on residual scrap. Spooled rebar also is available from minimills, but he says the proximity to customer needs makes the Nucor micromill a more attractive proposition.
Freight costs also are cheaper from the Frostproof site to the company’s West Palm Beach fabrication site, and in the case of ARES, company-owned vehicles can pick up the material if it is needed urgently, or pickups can be planned in conjunction with projects that could have drivers returning from the mill’s direction, adding to operational savings.
“The backing from Nucor’s bigger electric arc furnace [EAF] minimill in Birmingham, Alabama, also complements the regional micromill as product can be brought via rail for special needs,” Esquivel says.
The Frostproof rebar micromill, which was commissioned in December 2020, was the second in Nucor’s portfolio after the Sedalia, Missouri, site, which also was commissioned in 2020. Nucor’s Frostproof micromill has the capacity to process approximately 500,000 tons of scrap metal annually. According to Italy-based Danieli, which supplied equipment for the mill, it produces rebar ranging from Nos. 3 to 11 (9.5 to 35.8 millimeters) in straight bars up to 60 feet and in spooled coils up to 5 tons. The mill also will provide the No. 18 rebar required for the bottom floors of the project.
An innovative approach
Nucor brought innovation in business structure and technology to the steel industry with the advent of the EAF mini-mill. Its first minimill in Darlington, South Carolina, was commissioned in 1969 and employed a vertical integration business model to supply steel to its many divisions, which produced long steel joists. The revolution that effectively increased the rate of recycling has since spread globally.
Minimills’ consumption of scrap metal eliminated mining expenses, reduced manpower, limited energy consumption, decreased hazards, reduced pollution, facilitated flexibility and accelerated technological innovation. The minimill’s lower design cost also allowed companies to strategically select locations and integrate adaptive processes, keeping regional scrap supplies and finished steel needs in mind.
Nucor innovated further, leading the way for the minimill concept for flat steel with a $250 million budget that led to the introduction of continuous casting technology at its flat-rolled steel mill in Crawford, Indiana, in 1989. Developing continuous casting technology that is customized for the minimill was an important step forward, enabling production of high-quality steel in one seamless process, leaving the billet step behind.
Nucor began its rebar micromill journey in 2017, and the recently announced Pacific Northwest site will be its fourth and largest rebar micromill, with an annual capacity of 650,000 tons. Its other micromills are in Missouri, with an annual capacity of 350,000 tons; Florida, with an annual capacity of 350,000 tons; and North Carolina, with an annual capacity of 430,000 tons. The latter aims to start production by the end of 2024.
Other ongoing investments include the 3 million-tons-per-year West Virginia sheet mill expected to start by 2026, and a second melt shop in the Arizona bar mill with an annual capacity of 600,000 tons.
The company’s flexible raw materials mix for 2023 consisted of 53 percent obsolete scrap, 26 percent prime scrap, 15 percent direct-reduced iron and hot-briquetted iron and 6 percent pig iron. Pig iron volumes have declined since early 2022 as the company replaced it with more scrap amid supply chain issues resulting from the Russian-Ukraine war. In fact, 60 percent of steel recycled in the U.S. comes from obsolete scrap, which primarily is supplied by the automotive and construction industries.
Nucor estimates its current steel bar production capacity at about 9.5 million tons per year at 15 bar mills, though not all is rebar, excluding the last two micromill investments. The company’s total steel mill shipments were 23.3 million net tons in 2023, including 8.2 million net tons of rebar and 2.1 million of structural steel.
CMC’s story

CMC innovated the micromill design for long steel. Micromills use energy more efficiently than minimills, eliminating the need to reheat semifinished billets via continuous casting. Billets not only faced a reheating challenge, but rebar produced this way had length limitations that needed additional welding technology.
The steelmaker operates nine EAF mini- and micromills in the U.S. and is the largest producer of rebar in the country. Its locations include two mills in Arizona and one each in Arkansas, Florida, New Jersey, Oklahoma, South Carolina, Tennessee and Texas. Interestingly, CMC’s humble beginnings are rooted in 1916 in a recycled materials yard. In the 1950s, it began to think about how to make its long steel differently and set up the first CMC mill in Dallas in 1962.

CMC Steel Arizona was the first rebar micromill to operate successfully upon its commissioning in 2009. The micromill brought the advantages of continuous casting closer to customers in a more modular design. The second micromill opened in Durant, Oklahoma, in April 2018, with an annual capacity of 300,000 tons.
“The continuous heat and rolling to create spools of No. 3, No. 4, No. 5, No. 6 and, in some cases, even No. 7 rebar sizes without the limitations of billet manufactured perfectly wound, nontwisted rebar, which allowed for better product straightening and bending,” says Timothy L. Berg, vice president of business development at Murrysville, Pennsylvania-based Applied Systems Associates (ASA), a provider of software for the rebar industry.
Efficiencies are further improved with larger rebar spools. New machines can handle larger spooler weights, which can provide a big advantage to downstream fabricators and end customers since the machines run longer between spool changes. The lack of twists in the bar and compact coils also magnifies efficiency.
CMC’s Arizona 2 was commissioned this year with an annual capacity of 500,000 tons, including 150,000 tons of merchant product. Arizona 2 was CMC’s third micromill and the first capable of producing merchant bar products, including angles, channels, flats, rounds and squares, in an energy-efficient, continuous casting process. In the case of rebar mini-mills, their retooling design also allows flexibility to adjust to market conditions.
Sponsored Content
Labor that Works
With 25 years of experience, Leadpoint delivers cost-effective workforce solutions tailored to your needs. We handle the recruiting, hiring, training, and onboarding to deliver stable, productive, and safety-focused teams. Our commitment to safety and quality ensures peace of mind with a reliable workforce that helps you achieve your goals.
Sponsored Content
Labor that Works
With 25 years of experience, Leadpoint delivers cost-effective workforce solutions tailored to your needs. We handle the recruiting, hiring, training, and onboarding to deliver stable, productive, and safety-focused teams. Our commitment to safety and quality ensures peace of mind with a reliable workforce that helps you achieve your goals.
The Texas-based steelmaker continues to grow. Its fourth rebar micromill with 500,000 tons of capacity broke ground in July 2023 in West Virginia and is slated to be commissioned by mid-2025.
CMC also is vertically integrated with its local recycling facilities. The company externally shipped 2.9 million tons of steel products and 1.9 million tons of downstream products in North America in its 2023 fiscal year, and its Europe operations shipped 1.7 million tons in 2023.
Rebar consumers have seen the benefits provided by CMC’s and Nucor’s micromills. “Quality, proximity and operational ease depending on machinery on-site can play a role in sourcing rebar for fabrication jobs,” says Bill Soffer, general manager of Florida-based Ferrosource’s rebar division. “Micromills getting closer to the customer can also help reduce freight costs.”
Esquivel previously managed a rebar fabrication shop in Georgia and says he was satisfied working with CMC.
CMC and Nucor are committed to net-zero carbon emissions by 2050, and the micromill design also benefits their sustainability goals.
Get curated news on YOUR industry.
Enter your email to receive our newsletters.
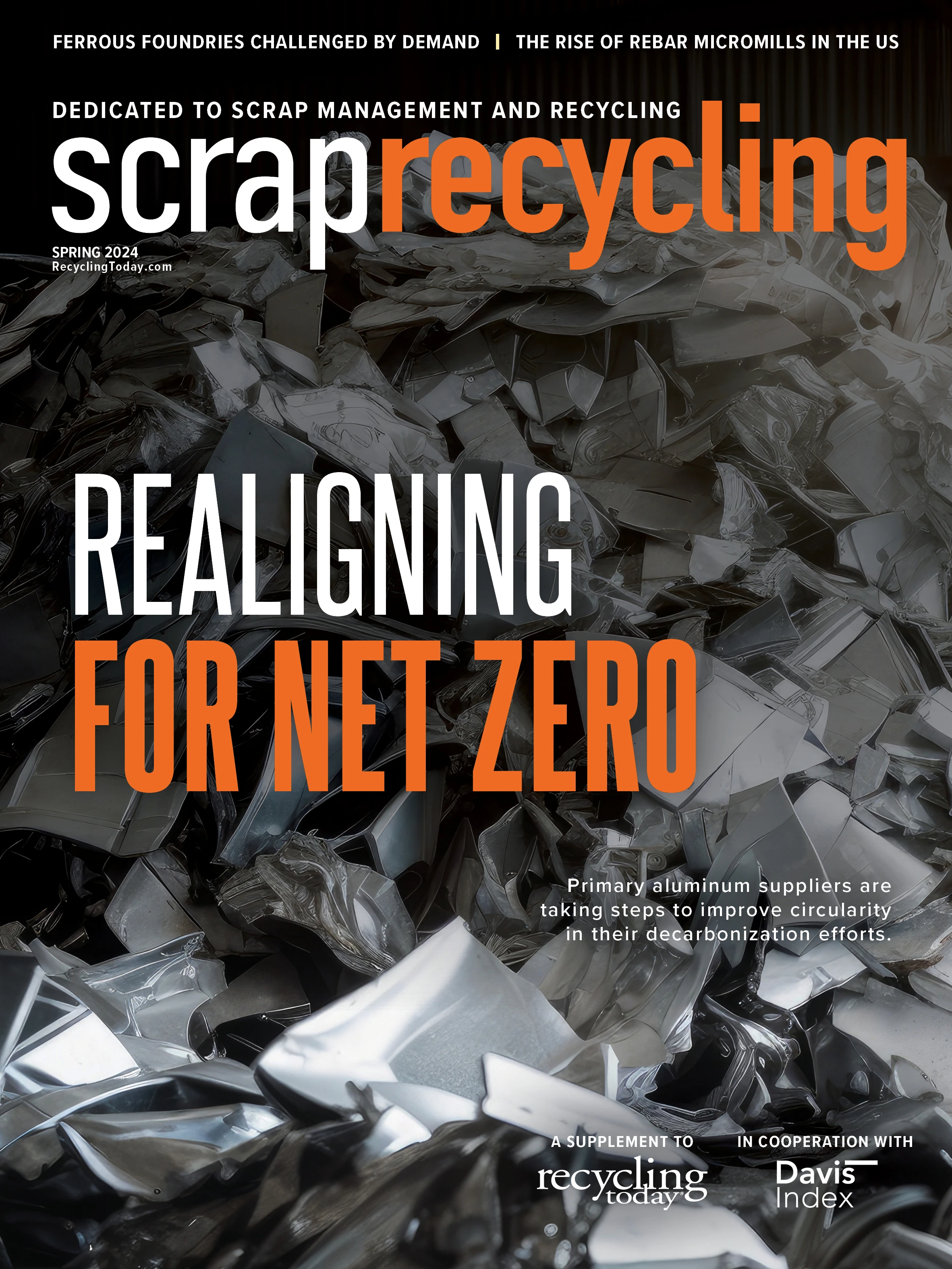
Explore the Spring 2024 Scrap Recycling Issue
Check out more from this issue and find your next story to read.
Latest from Recycling Today
- Athens Services terminates contract with San Marino, California
- Partners develop specialty response vehicles for LIB fires
- Sonoco cites OCC shortage for price hike in Europe
- British Steel mill’s future up in the air
- Tomra applies GAINnext AI technology to upgrade wrought aluminum scrap
- Redwood Materials partners with Isuzu Commercial Truck
- The push for more supply
- ReMA PSI Chapter adds 7 members