SDI ventures into aluminum sheet production

Steel Dynamics Inc. (SDI) says its board of directors has authorized construction and operation of a 650,000-metric-ton recycled aluminum flat-roll mill and two supporting satellite recycled aluminum slab centers. The company will invest an estimated $2.2 billion in the three facilities, with commercial production planned to begin in the first quarter of 2025. In a news release about the investment, SDI says it will fund the project using available cash and cash from operations.
Founded in 1993, Fort Wayne, Indiana-based SDI is among the largest and most diversified U.S. steel producers and metals recyclers. SDI produces steel with fewer carbon emissions using electric arc furnace (EAF) technology with recycled ferrous scrap as the primary input. The company says it plans to bring the steel minimill culture and related operating efficiency to the flat-rolled aluminum industry.
This is not SDI’s first venture into nonferrous metal production. In 2012, SDI partnered with Spanish company La Farga Group to establish SDI La Farga LLC, which produces copper wire rod from recycled copper at its plant in New Haven, Indiana. With its purchase of OmniSource Corp., its scrap recycling division, in 2007, SDI acquired Superior Aluminum Alloys, New Haven, which OmniSource established in 1997.
SDI says its steel customers are significant consumers and processors of aluminum flat-rolled products and seek the company’s high-quality, sustainable, customer-centric approach within the flat-rolled aluminum market.
Mark D. Millett, chairman, president and CEO at SDI, says, “We have intentionally grown with our customers’ needs, providing efficient sustainable supply chain solutions for the highest quality products. Thus far, this has primarily been achieved within the carbon steel industry—however, a significant number of our carbon flat-rolled steel customers are also consumers and processors of aluminum flat-rolled products. … We are also excited to further diversify our end markets with plans to supply the sustainable beverage can industry.”
SDI says its metals recycling platform is expected to supply all the aluminum scrap needed for the rolling mill and aluminum slab operations.
The North American flat-rolled aluminum industry has a supply deficit estimated at more than 2 million metric tons in large part because of growing demand from the automotive and beverage can industries, SDI says. This deficit is being addressed through imports of higher-cost aluminum flat-rolled products, which exceeded 25 percent of North American consumption in 2021, the company adds.
The company says it plans to locate the $1.9 billion mill in the southeastern U.S. and to begin operations in the first quarter 2025.
SDI, which is partnering with Unity Aluminum Inc. in a joint venture, will own more than 94 percent of the rolling mill facility. Ashland, Kentucky-based Unity’s employees provide significant aluminum industry operating expertise, SDI says, complementing its own proven extensive construction and operating talent.
SDI Investor Relations Manager Tricia Meyers says, “Steel Dynamics chose to structure this rolling mill as a joint venture, with Unity Aluminum having a 5.6 percent equity stake as their employees provide significant aluminum industry operating expertise to the project, complementing Steel Dynamics’ own proven extensive construction and operating talent.”
At full capacity, SDI says its aluminum rolling mill will require approximately 900,000 metric tons of annual aluminum slab supply. The rolling mill likely will supply approximately 50 percent of this requirement on-site, with the remaining amount to be provided by constructing two additional satellite recycled aluminum slab centers: one in the southwestern U.S. and the other in north-central Mexico. The two facilities are expected to cost $350 million in aggregate, with the Mexico facility expected to begin operations in 2024 and the U.S. facility by the end of 2025, SDI says. The company will own 100 percent of the satellite facilities.
Korea Zinc invests in Igneo Technologies

Igneo Technologies LLC, which is headquartered in White Plains, New York, says it has finalized a majority investment agreement with Korea Zinc, a smelting company based in Seoul that specializes in precious and nonferrous metals.
In a disclosure, Korea Zinc says it has taken a 73.21 percent share in Igneo for 432.4 billion Korean won ($330 million) through its U.S. subsidiary, Pedal Point Holdings.
Established in 1974, Korea Zinc produces 1 million tons per year of 18 different nonferrous metals, including zinc, lead, copper, gold and silver. Korea Zinc launched Pedal Point, a wholly owned subsidiary, last December to build out its presence as a global integrated circular resource platform.
Igneo says the capital investment and strategic support will allow it to accelerate its global growth strategy, including projects currently underway, such as the construction of a new secondary smelter in Savannah, Georgia, that will process 90,000 metric tons annually once it is online in early 2024.
Igneo Chief Operations Officer Brian Diesselhorst says the companies have been in discussions for six months regarding the deal. While private equity investors were offering higher valuations, Igneo selected Korea Zinc’s offer because the company represents a strategic partner that allows Igneo to achieve full circularity, he adds.
Igneo CEO Danish Mir says Korea Zinc shares Igneo’s vision and commitment to creating a circular economy. He says Korea Zinc is “forging the relationships and assembling the pieces” that will enable the company to meet its commitments and the goals it has established. “That’s what drew us to them.”
He adds that the partnership with Korea Zinc enables vertical integration, with the copper concentrate that Igneo produces being used to produce copper foil that will be used in manufacturing electric vehicles, for example.
Igneo presently operates a metal recovery furnace in Isbergues, France, with an infeed capacity of 30,000 metric tons annually. That plant was known as Terra Nova SAS, and it was constructed by scientists who developed the pyrolysis technology the company uses.
The company that would come to be known as Igneo purchased Terra Nova out of bankruptcy in 2014, finetuned the technology and renamed the plant WEEE Metallica. It has since been renamed Igneo France SAS.
Igneo is set to break ground on its Savannah facility in late summer, Mir says. That facility will have two furnaces with 90,000 tons of combined “sustainable copper concentrate” output. The first furnace is expected to go online in 2024. “Based on its ramp-up, we will determine time frame [to install] the second furnace,” he says, adding that permits for the facility are in place.
Igneo produces copper concentrate from low-end electronics using pyrolysis.
“We can handle low-grade material,” Mir says. “That’s what makes us special.” Rather than rely on printed circuit boards as infeed material, he says Igneo can take small electronic devices, such as calculators, alarm clocks and toys, and process them. He describes these devices as the “fastest growing fraction” of end-of-life electronics, adding, “and people don’t have an answer for it.”
The Savannah location will be fed in part using scrap from evTerra Recycling, a subsidiary of Igneo’s that processes end-of-life electronics. Unlike other companies in the space that primarily focus on remarketing devices and components from high-end devices, evTerra is targeting low-grade and midgrade devices.
EvTerra has processing operations in Las Vegas and Atlanta and a sales office in Tampa, Florida.
The company will be opening additional processing locations in Chicago and San Antonio in August and September, respectively, with their shredders coming online three months later, Diesselhorst says. When all the sites are running, evTerra will have 140,000 tons of annual end-of-life electronics shredding and sorting capacity in the U.S., he adds.
In a news release about the announcement, Yun B. Choi, vice chairman of Korea Zinc, says, “Tapping into Igneo’s robust capabilities to collect and process end-of-life electronics will allow Korea Zinc to upgrade its standing in secondary copper refining.
“With Pedal Point now fully running, Korea Zinc will be delving into the wealth of such opportunities in North America and beyond to find partners across verticals with the goal of making metal refining more efficient, circular and sustainable,” Choi adds.
For more information on Igneo and its plans in the U.S., see the full article at http://bit.ly/igneo-kz.
Hydro invests in Kentucky plant

Hydro ASA, based in Norway, has announced its North American Hydro Aluminum Metals business unit is investing $15 million into its Henderson, Kentucky, facility to expand recycled aluminum production.
The company says the investment will support two key projects. First, it will install a new homogenization furnace to improve the plant’s capabilities to meet the specifications of the growing U.S. automotive market, allowing the Henderson site to produce a greater volume of alloys from recycled metals at a lower carbon footprint.
Second, Hydro will install a new baghouse that will allow the plant to use greater volumes of postconsumer scrap and explore using new, more difficult types of scrap, such as material with paint or other contamination, which the company says requires advanced equipment to recycle. The baghouse also will improve air quality inside the plant and reduce the overall environmental footprint.
Currently the Henderson remelting facility produces more than 90,000 metric tons of metal annually.
“At Hydro, we want to accelerate the green transformation of the aluminum and automotive industries by increasing our use of postconsumer scrap to pull more used material into the value chain and promote a circular economy while also delivering our automotive customers advanced, high-strength alloys,” says Trond Gjellesvik, president of Hydro Aluminum Metals in the U.S.
The investment into Hydro’s Henderson plant also will enable it to produce higher volumes of its Hydro Circal after independent risk management and quality assurance company DNV certified the facility July 1. The certification follows the recent approval of Hydro’s Commerce, Texas, plant to produce Hydro Circal.
Hydro says initial volumes from the Commerce and Henderson plants will be 4,000 metric tons, with large-scale production first coming from Hydro’s new recycling facility in Cassopolis, Michigan, which is expected to begin operations in 2023. That plant will have 130,000 metric tons of extrusion billet capacity.
Get curated news on YOUR industry.
Enter your email to receive our newsletters.
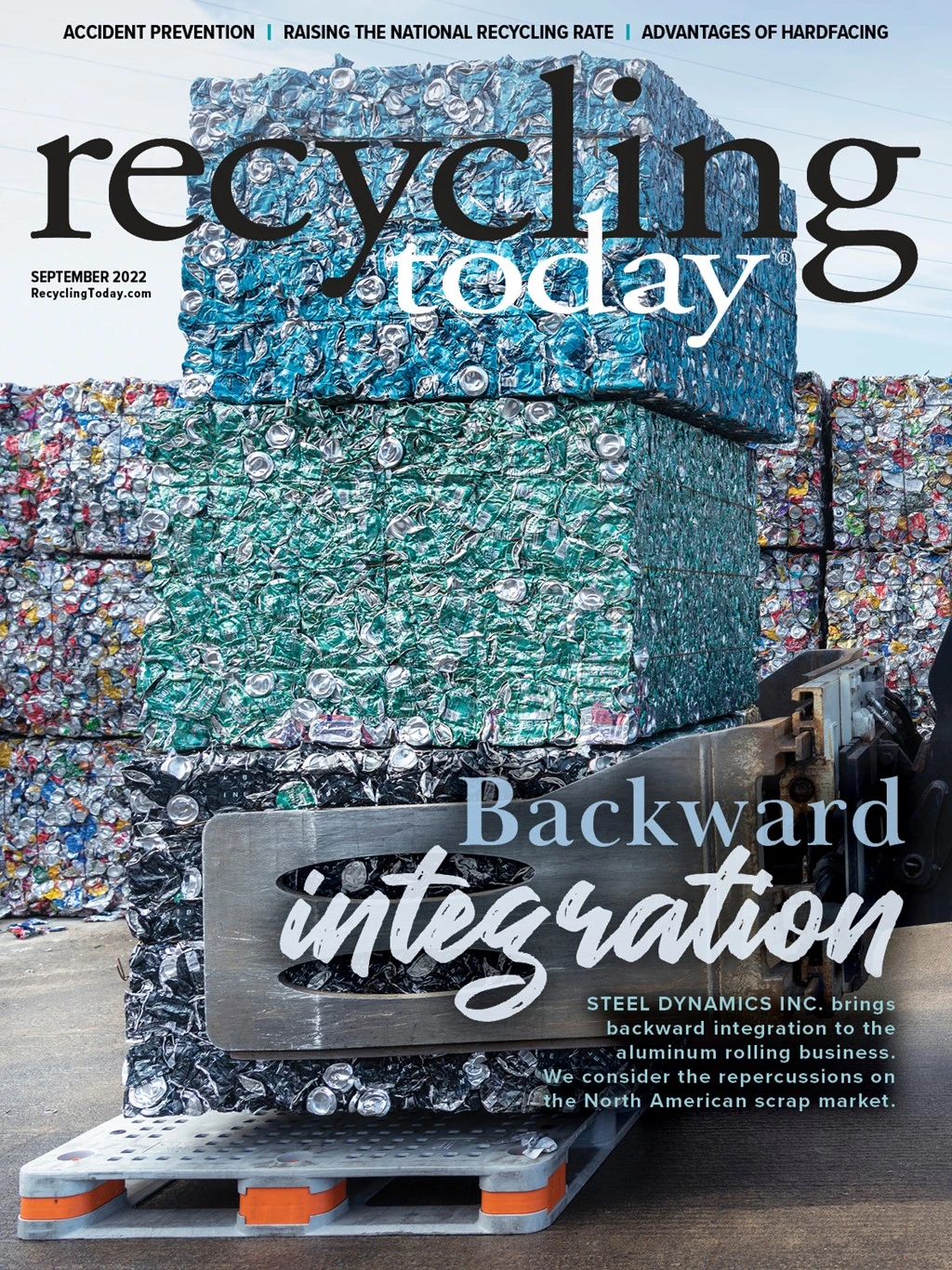
Explore the September 2022 Issue
Check out more from this issue and find your next story to read.
Latest from Recycling Today
- Astera runs into NIMBY concerns in Colorado
- ReMA opposes European efforts seeking export restrictions for recyclables
- Fresh Perspective: Raj Bagaria
- Saica announces plans for second US site
- Update: Novelis produces first aluminum coil made fully from recycled end-of-life automotive scrap
- Aimplas doubles online course offerings
- Radius to be acquired by Toyota subsidiary
- Algoma EAF to start in April