ISRI requests reinstatement of mutilated coin redemption program
The Washington-based Institute of Scrap Recycling Industries (ISRI) is urging the U.S. government to reinstate its mutilated coin redemption program, which was suspended in 2019. The move is in response to the U.S. Mint’s request for comments regarding proposed revisions related to the exchange of damaged coins, updates to redemption rates and procedures and acceptance and processing of bent and partial coins.
In its comments, which were sent to the U.S. Mint July 6, ISRI details the burden placed on recyclers when the program was suspended for a second time in 2019. The program previously was suspended in 2015.
“Shredding is the predominant method for recycling heavy steel-bearing end-of-life products into commodity-grade products, including automobiles, appliances, coin-operated laundry machines and vending machines,” the statement says. “Shredding greatly improved recycling productivity with great benefits for environmental protection, natural resource conservation, manufacturing sustainability and reliability as well as worker safety.”
ISRI says the U.S. Mint’s proposal could drive some recyclers to return to less effective manual sorting and separation processes that unnecessarily increase risks to workers.
“Without any indication that recyclers would not be eligible to redeem coins through this program, recyclers continue to collect coins from their shredding and downstream sorting and separation operations and now have over six years’ worth of mutilated coins stored at their facilities,” ISRI notes. “Accordingly, recyclers have lost significant revenues as a result of the program’s suspension.”
ISRI suggests two solutions to enable the U.S. Mint to continue accepting mutilated coins from recyclers and foreign sources. One is a qualified redemption program allowing recyclers that demonstrate compliance with the regulations to continue redeeming the mutilated coins collected. The other is site inspections for recyclers to weed out criminal activity, such as fraud or intentionally damaging coins.

Chiho sells two Liberty shredding plants to AIM
Subsidiaries of Montreal-based American Iron & Metal (AIM) have purchased auto shredding plants previously operated by the Liberty Iron & Metal subsidiary of Hong Kong-based Chiho Environmental Group.
A Hong Kong Exchange disclosure filing in late June by Chiho Environmental Group indicates its shredder yards in Erie, Pennsylvania, and in Phoenix have been purchased by AIM Erie and AIM Phoenix, respectively.
“The disposal assets include certain equipment, machinery, vehicles, trailers, containers, computer software and inventory of the shredder facilities that the group owns and operates in Erie, Buffalo, [New York], and Phoenix,” the Chiho filing states in part.
The filing indicates AIM will pay $17 million for the equipment and metals assets, and the company will pay $12.7 million for the four parcels of land it will acquire from Chiho.
Chiho Environmental Group expanded beyond its base in China and Hong Kong in the previous 12 years or so by purchasing the assets of the Scholz Group in Germany and Liberty Iron & Metal in the United States.
While the company has retained many of the Scholz assets in Europe, this most recent transaction seems to indicate a nearly complete exit from the United States market by Chiho, which is affiliated with the government of Chongqing, China.
In late 2020, Chiho filed another disclosure spelling out the sale of an auto shredder yard in Girard, Ohio, to New Jersey-based Metalico Inc.
The Liberty Iron & Metal website lists the Phoenix and Erie yards as its only locations operating in the United States. (The Buffalo site, which the Chiho filing indicates is at 207 and 267 Marilla Street, is not listed.) The website also lists a location in Chihuahua, Mexico, as still operating.
Metals information service company Argus reports that AIM CEO Herbert Black said the move represents an expansion of the Canadian firm’s presence in the U.S. market.
The Arizona, New York and Pennsylvania assets will be added to AIM’s current U.S. portfolio, which includes one location in Cleveland and three facilities in Maine. AIM operates multiple locations in Canada.
Metal Exchange Corp. reorganizes secondary aluminum casting capacity
Metal Exchange Corp. (MEC), with headquarters in St. Louis, says it is reorganizing its secondary aluminum casting capacity and rebranding its secondary cast product lines at its Pennex Aluminum Co. LLC sites in Wellsville and Greenville, Pennsylvania, and its Continental Aluminum site in New Hudson, Michigan, as MEC Cast Products.
The Wellsville plant is a shared facility that will produce extrusions under the Pennex brand and billet under MEC Cast Products, Mark Buchner, president of MEC Cast Products, tells Recycling Today. The company’s aluminum extrusion plants in York, Pennsylvania, and Leetonia, Ohio, will continue to carry the Pennex Aluminum name.
“Our cast products businesses have grown substantially over the years and have a very strong customer focus,” Rick Merluzzi, chief executive officer of MEC, says. “By establishing MEC Cast Products, it further strengthens the strategic focus of our business.”
Buchner adds, “We’ve had the chance to evaluate all markets and are excited about the opportunities that are before us. Between the three plants, we have strong operating capacities and capabilities. Our plan is to shift our focus primarily on the billet market segment as it strongly aligns with our company’s expertise, capacity and capabilities.”
As part of this shift, MEC Cast Products will phase out production of aluminum alloys used for die casting and deoxidizers in the steel industry at its New Hudson site. Production at that site will be adjusted to meet the company’s internal needs as it realigns resources to the aluminum billet segment.
Buchner says, “We are successfully finalizing and fulfilling all contracts with existing customers to ensure their needs were met in a timely fashion.”
Casting equipment at the company’s Wellsville plant includes a 130,000-pound regenerative melt furnace, while its Greenville plant has two melt furnaces with one holding furnace, according to the Pennex website.
The renamed casting division is ISO 9001:2015 certified and uses common alloy type material to produce 7-, 8-, 9-, 10-, 12- and 14-inch diameter billet in 1xxx, 2xxx and 6xxx series aluminum alloys.
According to Continental Aluminum’s website, its reverb and rotary furnaces allow it to use a range of scrap that includes aluminum turnings, old sheet, shredded aluminum, aluminum radiators, cast aluminum, automobile wheels, extrusions, mixed low copper clips and mixed, painted siding, aluminum dross and twitch.
Buchner says the New Hudson site will consume more wrought scrap than cast scrap because of the change in production, but the total volume of scrap consumed will not change.

Peruvian steelmaker buys Florida shredder yard
Peru-based electric arc furnace (EAF) steelmaker Corporación Aceros Arequipa S.A. (CAASA) says it has agreed to purchase an automobile shredder yard in Florida that was formerly operated by Topsham, Maine-based Grimmel Industries. Additionally, CAASA will acquire a second Grimmel yard in St. Petersburg, Florida, as part of the transaction.
In an announcement posted to its website, CAASA says it has “signed a contract to purchase the assets of two business units that collect metal cargo located in Florida” and that the acquisition was made through two subsidiaries created to undertake the purchase: Aceros America Port Manatee LLC and Aceros America St. Pete LLC.
According to the 2020 Recycling Today Auto Shredder List and Map, Grimmel Industries operates a shredder in Palmetto, Florida, known as Port Manatee Scrap Recycling. Palmetto is located on the Gulf Coast of Florida, about 40 miles south of Tampa.
The CAASA announcement states in part, “Among the main assets acquired are two 116,000-square-meter (1.25- million-square-foot) yards, a 6,000- horsepower and 450-rpm shredder, as well as a magnetic metal separator that will allow the segregation of nonferrous material for export mainly to Asia.”
The EAF steelmaker says it expects to supply itself with 100,000 tons of ferrous scrap per year from the Florida operations, “reinforcing the supply of recycled steel” for its upgraded EAF melt shop in Pisco, Peru.
“The new furnace requires almost 400,000 tons per year or more, so we must assure the volume,” CAASA Strategic Sourcing Manager Diego Arróspide Benavides shares with Recycling Today.
He adds that “100 percent of the ferrous scrap will be shipped to Pisco” from Florida.
Tulio Silgado, CAASA general manager, says that with the acquisition, “the company continues to consolidate its expansion and integration of the value chain, ensuring the raw material for the production of international quality steel.”
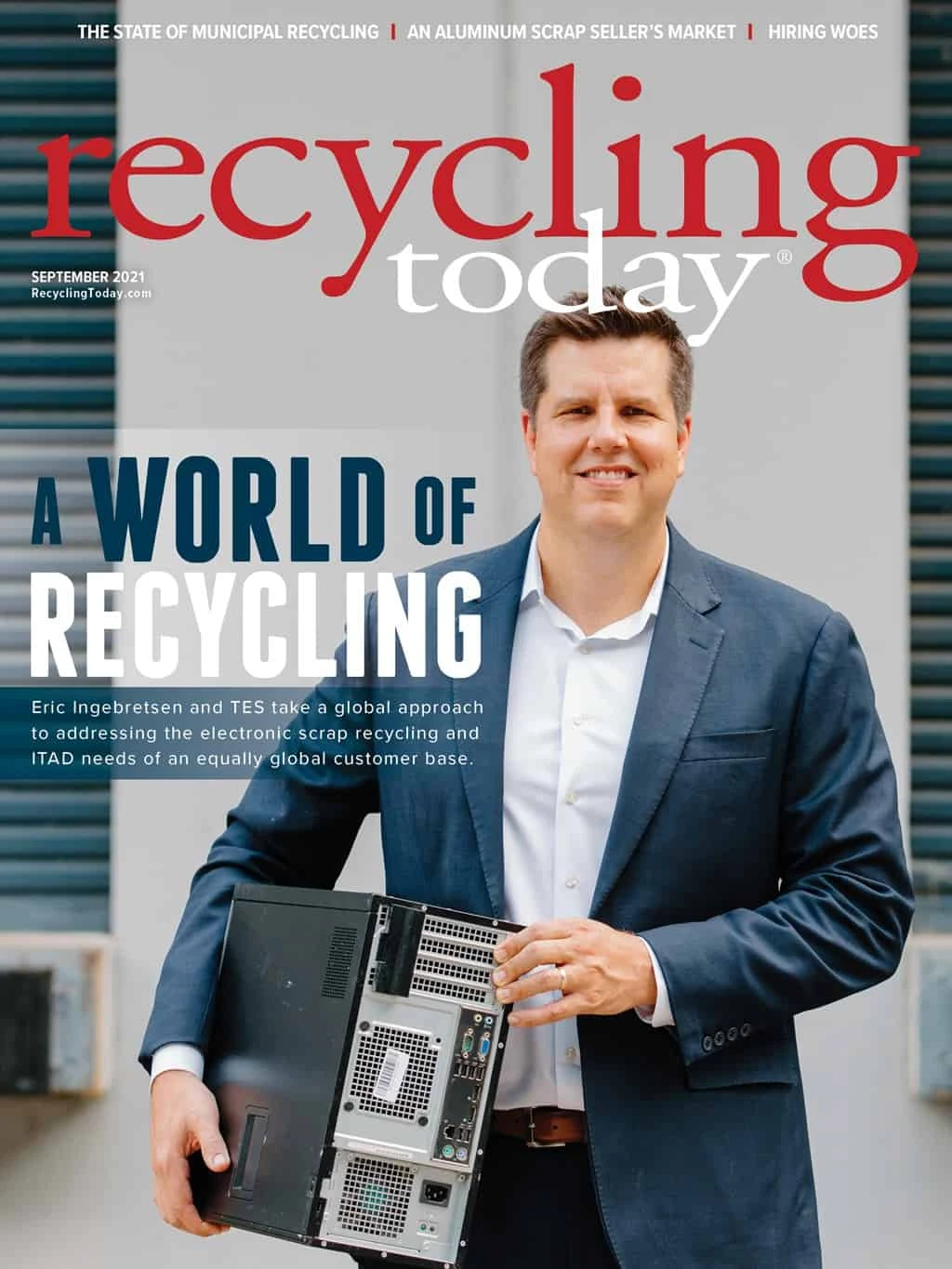
Explore the September 2021 Issue
Check out more from this issue and find your next story to read.
Latest from Recycling Today
- ReMA opposes European efforts seeking export restrictions for recyclables
- Fresh Perspective: Raj Bagaria
- Saica announces plans for second US site
- Update: Novelis produces first aluminum coil made fully from recycled end-of-life automotive scrap
- Aimplas doubles online course offerings
- Radius to be acquired by Toyota subsidiary
- Algoma EAF to start in April
- Erema sees strong demand for high-volume PET systems