Southern Recycling opens new facility
Southern Recycling LLC—along with representatives from Warren County, Kentucky; the city of Bowling Green, Kentucky; the Bowling Green Area Chamber of Commerce; and Southern Recycling’s parent company, Houchens Industries—gathered to officially open the company’s new processing facility in Bowling Green. The new facility features equipment that will increase the company’s scrap processing capacity.
“We are thrilled to have this new state-of-the-art recycling facility here in Bowling Green,” says Spencer Coates, president of Houchens Industries. “We at Houchens Industries and Southern Recycling would like to thank everyone involved in the design and completion of this facility, including the Chamber of Commerce, city and county governments and their representatives and Stewart Richey Construction. Of course, we are most thankful to the management and employees of Southern Recycling for their hard work and dedication.”
With the new location in Bowling Green, Southern Recycling now operates five processing facilities: three in Kentucky and two in Tennessee.
Southern Recycling was founded in 1985 and serves industrial, commercial and residential recycling customers. The company says it specializes in processing and shipping more than 25,000 tons per month of ferrous and nonferrous scrap and other recyclables at its facilities.

W. Silver Recycling opens new plant in Southern California
W. Silver Recycling opened its new Calexico, California, metals recycling facility in April. The plant is W. Silver’s 11th location, with eight facilities in the United States and three in Mexico.
Lane Gaddy, the president and CEO of W. Silver, tells Recycling Today, “We are especially excited about this site as it completes a long-term vision for W. Silver of coast-to-coast coverage on the Mexican border. It opens up the largest maquila region in which we are not operating in currently in Mexico.”
Gaddy says the site is well-suited for servicing maquilas in the states of Baja California and Sonora in Mexico, as well as customers in California’s Imperial Valley and those in southwest Arizona.
The site is a greenfield 5-acre parcel with rail service provided by Union Pacific.
“Our entire team has been working for months to prepare for the opening of our first office and facility in California, and we’re ready to start partnering with new customers along the Baja and Sonoran border of Mexico,” Gaddy says. “With sites across the entire southwest, this new location now allows us to better serve the maquilas along California’s southern border. Direct access to rail and the port of entry will help us reach more customers and continue to grow our business.”
W. Silver was founded by William Silver in 1920 in El Paso, Texas, the city that still serves as its headquarters. The company specializes in servicing industrial accounts in Mexico and the southwest United States and has more than 500 employees in the U.S. and Mexico at its 11 locations and at customer sites.

University develops lithium-ion battery recycling solution
Researchers at Rice University in Houston say they have a solution, literally, to deal with sometimes difficult-to-recycle lithium-ion batteries used in electric vehicles, cellphones and other electronic devices.
Materials scientist Pulickel Ajayan and colleagues at a Rice laboratory say they have used an environmentally friendly deep eutectic solvent to extract recyclable elements from the metal oxides commonly used as cathodes in lithium-ion batteries. The goal, researchers say, is to curtail the use of harsh processes to recycle batteries and also to keep batteries out of landfills.
The solvent, made from choline chloride and ethylene glycol, extracted more than 90 percent of cobalt from powdered compounds and a smaller but still significant amount from used batteries, the researchers say.
“Rechargeable battery waste, particularly from lithium-ion batteries, will become an increasingly menacing environmental challenge in the future as the demand for these through their usage in electric vehicles and other gadgets increases dramatically,” Ajayan says.
“It’s important to recover strategic metals like cobalt that are limited in supply and are critical for the performance of these energy-storage devices,” he continues.
“This has been attempted before with acids,” says Rice graduate student and lead author Kimmai Tran. “They’re effective, but they’re corrosive and not eco-friendly. As a whole, recycling lithium-ion batteries is typically expensive and a risk to workers.”
The researchers built small prototype batteries and found that cobalt could be recovered from the eutectic solution through precipitation or even electroplating to a steel mesh, with the latter method potentially allowing for the deep eutectic solvent to be reused.
“We focused on cobalt,” says Rice alumnus Marco Rodrigues, now a postdoctoral researcher at Argonne National Laboratory. “From a resource standpoint, it’s the most critical part. The battery in your phone will surely have lots of it. Lithium is very valuable too, but cobalt in particular is not only environmentally scarce, but also, from a social standpoint, hard to get.”
An abstract on the process is available at http://bit.ly/ricelabs.
DOE opens lithium-ion battery recycling center
The United States Department of Energy (DOE) has opened a battery recycling research and development center at Argonne National Laboratory in Lemont, Illinois. The goal of the R&D facility is to reclaim and recycle materials such as cobalt and lithium from spent lithium-ion batteries.
The launch of the DOE’s lithium-ion battery recycling center, called the ReCell Center, “will help the United States grow a globally competitive recycling industry and reduce our reliance on foreign sources of battery materials,” the agency says.
“The ReCell Center will help expedite the pursuit to profitable lithium-ion battery recycling,” says Jeff Spangenberger, director of the ReCell Center.
“ReCell brings our national laboratories, the private sector and universities together to develop advanced technologies that safely and cost-effectively recycle lithium-ion batteries,” says Daniel R. Simmons, assistant secretary of the DOE Office of Energy Efficiency and Renewable Energy (EERE). “This center will create jobs and create a national supply of lithium-based battery materials, as well as spur the adoption of an affordable electric vehicle economy.”
The DOE says the ReCell Center is a collaboration between Argonne, the National Renewable Energy Laboratory (NREL), Oak Ridge National Laboratory (ORNL) and several universities, including Worcester Polytechnic Institute (WPI) in Massachusetts, the University of California at San Diego and Michigan Technological University.
WPI has received a one-year, $150,000 contract to conduct research on the effects of impurities on the cathode materials used to manufacture lithium-ion batteries.
Yan Wang, a WPI professor of mechanical engineering who developed a process for recycling lithium-ion batteries that can recover and reuse cathode materials regardless of their chemistry, will lead the project. Battery Resourcers, a company co-founded by Wang, licensed the patented process and has established a pilot plant in Worcester to demonstrate that it can be scaled up to near-commercial capacity.
The ReCell Center is supported by the DOE with $15 million in funding over three years, and its work will include development of test beds and a process scale-up facility at Argonne.
The DOE also announced the start of its Lithium-Ion Battery Recycling Prize. The prize encourages entrepreneurs to find innovative solutions to collecting, storing and transporting discarded lithium-ion batteries for eventual recycling. It will award cash prizes totaling $5.5 million to contestants in three phases designed to accelerate the development of solutions from concept to prototype.

Nucor selects Kentucky for new mill site
Charlotte, North Carolina-based Nucor Corp. has announced it will build its new scrap-fed electric arc furnace (EAF) steel plate mill in Brandenburg, Kentucky. That city is situated on the Ohio River southwest of Louisville, Kentucky.
Nucor says it will invest approximately $1.35 billion to build the mill, which will be capable of producing 1.2 million tons per year of steel plate products. The company says it expects the plate mill to be fully operational in 2022, pending regulatory approvals and obtaining appropriate permits.
“This strategic investment will enable us to build a clear market leadership position in the United States plate market,” says John Ferriola, chair, CEO and president of Nucor. “Kentucky is an excellent location for this mill, right in the center of America’s largest plate-consuming region. Our acquisition of the Gallatin sheet mill in Ghent, Kentucky, five years ago has been a tremendous success, and we are pleased to add a second mill in the state.”
With the new plate mill, Nucor will be able to produce 97 percent of the products the domestic plate market demands, including what it calls specialty higher margin products.
The mill will produce cut-to-length, coiled, heat-treated and discrete plate ranging from 60 to 160 inches wide and in gauges from 3/16th of an inch to 14 inches. The company says the Brandenburg mill will employ more than 400 people full time at an average annual salary of $72,000.
The mill’s location on the Ohio River will give Nucor logistical advantages in sourcing raw materials and serving customers throughout the Midwest, the company says.
Nucor currently operates plate mills in North Carolina, Alabama and Texas.
The company has two additional major investment projects underway at its Gallatin sheet mill in Kentucky. That mill’s new galvanizing line will be operational during the second quarter of 2019. Additionally, a project to increase Gallatin’s hot-rolled coil capacity at expanded widths of up to 73 inches is expected to come online during 2021, Nucor says.
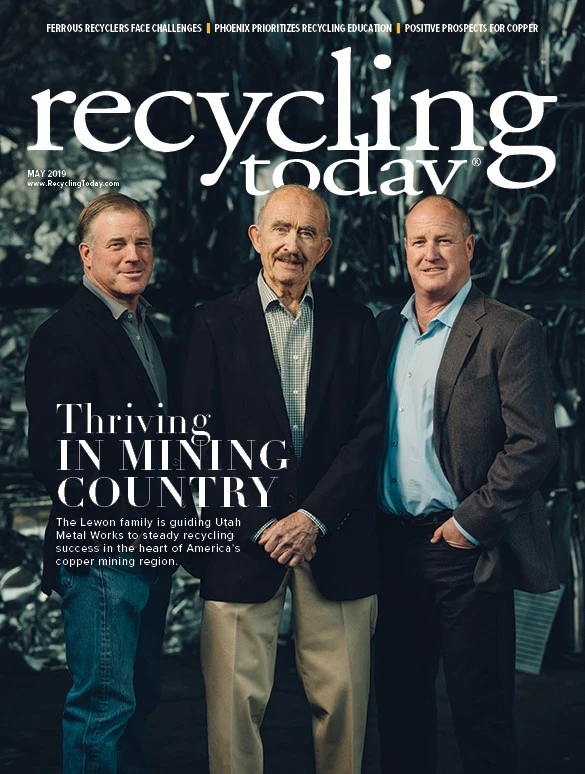
Explore the May 2019 Issue
Check out more from this issue and find your next story to read.
Latest from Recycling Today
- Haber raises $44M to expand to North America
- Canada Plastics Pact releases 2023-24 Impact Report
- Reconomy brands receive platinum ratings from EcoVadis
- Sortera Technologies ‘owning and operating’ aluminum sorting solutions
- IDTechEx sees electric-powered construction equipment growth
- Global steel output recedes in November
- Fitch Ratings sees reasons for steel optimism in 2025
- P+PB adds new board members