
Aqua Metals, BASF partner to enhance AquaRefining performance
Aqua Metals Inc., McCarran, Nevada, says it has partnered with BASF, which will supply electrolyte in addition to exploring technical improvements to enhance Aqua Metals’ AquaRefining performance.
AquaRefining is a room-temperature, water-based process that emits less pollution than traditional methods, according to Aqua Metals. The modular systems are designed to reduce environmental impacts from lead-acid battery recycling. Aqua Metals plans to supply equipment, services and licensing for the AquaRefining technology to partners.
BASF SE is headquartered in Germany. BASF Corp., its Florham Park, New Jersey-based North American affiliate, produces and markets chemicals and related products in North America.
BASF will provide the initial supply of Aqua Metals’ electrolyte for all new licensee facilities and will be the preferred supplier partner to licensees for their ongoing needs, according to a news release from Aqua Metals. The specially formulated AquaRefining electrolyte is the key chemical compound used in the AquaRefining process. BASF will offer AquaRefining to its existing and prospective battery recycling clientele, and Aqua Metals will incorporate the BASF product into every initial deployment and system fill. Aqua Metals and BASF also will explore technical enhancements to further improve the electrolyte formulations for enhanced AquaRefining performance and increased equipment longevity.
“We are very pleased to partner with BASF, one of the leading chemical companies, to be our preferred provider of electrolyte for AquaRefining,” says Aqua Metals President and CEO Steve Cotton. “We chose BASF due to their commitment to industry-leading standards and track record of delivering high-quality products. This partnership will also leverage BASF’s global reach to help offer AquaRefining to applicable companies within their global client base as well as work with us in the future to explore ways to enhance the electrolyte for improved AquaRefining performance,” he adds.
Also, Aqua Metals says it is developing a method to streamline its recycling process, having filed a provisional patent for the methodology. The company says it expects the process to provide economic and environmental benefits for AquaRefining licensees. To learn more, visit http://bit.ly/aqua-metals-patent.

Alter Corp., Toyota Tsusho America form partnership
Scrap processing and trading company Alter Trading Corp., headquartered in St. Louis, says it has partnered with Toyota Tsusho America Inc. (TAI) to form Altech Recycling LLC, which is constructing a metals separation plant in Arkansas to produce aluminum products from shredded scrap. The new company’s output will supplement demand at TAI production facilities as well as supply other business partners in North America.Jack Grundfest, senior vice president and chief administrative officer of Alter, says, “Alter Trading and Toyota Tsusho have a longstanding relationship, and this joint venture was a logical next step for the two companies.”
He declines to disclose each company’s ownership stake in Altech, saying, “We don’t discuss details of transactions, but I can tell you that this partnership benefits both parties on a number of levels. Alter is the operating partner working very closely with TAI.”
TAI is the North American-based affiliate of Toyota Tsusho Corp. of Japan, a member of the Toyota Group, which also includes Toyota Motor, Toyota Industries, Aichi Steel, JTEKT, Toyota Auto Body, Aisin Seiki, Denso, Toyota Boshoku, Towa Real Estate, Toyota Central R&D Labs, Toyota Motor East Japan, Toyoda Gosei, Hino Motors, Daihatsu Motor, Toyota Home and Toyota Motor Kyushu.
The Altech plant will convert zorba, which is a mixed-metal shredded scrap grade primarily comprised of aluminum, supplied by Alter and other shredder operators as needed to meet market demands, according to a news release from Alter. The heavy media plant will produce two main products from the zorba it processes: a clean aluminum product known in the industry as twitch and secondary products that are commonly referred to as heavies.
Altech Recycling will sell its products, which Grundfest describes as “the highest quality products available,” to TAI as well as to consumers around the globe as market demands dictate.
“The vast majority of the twitch will be for domestic consumption at Toyota Tsusho facilities, while the heavies will be sold to export customers for further processing,” he adds.
Initially, Altech Recycling will employ approximately 25 people and will be located on Central Airport Road in North Little Rock, Arkansas. Altech is scheduled to begin operations in the second quarter of 2021.
Alter has a network of nearly 20 auto shredders in the U.S., two of which are operated by Tenenbaum Recycling Group (TRG), which Alter purchased in 2018, in North Little Rock and Rogers, Arkansas. The Altech location in North Little Rock is about 2 miles east of the TRG shredder, Grundfest says, and was included in the purchase of TRG.
“That property offered the perfect start for this project,” he says. “As the project progressed, it became clear that this was a value-added location in North Little Rock because of its central location and location in a city that has a very pro-business mentality.”
“We are proud to be joining forces with one of the world’s global business leaders on this project,” says Alter President and CEO Jay Robinovitz. “The combined talents and strengths of the two entities will provide a quality long-term solution to suppliers, consumers and business partners.”
“At TAI, we are committed to generating value in our communities and the marketplace by creating solutions beneficial to all,” says Shawn O’Connor, TAI vice president and head of the Metals division. “TAI’s innovative collaboration with Alter, a company well-known and respected for its recycling expertise and track record, is a testament to what is possible when we team up for the good of not only business but society.”
Toyota Tsusho Corp. operates in more than 120 countries. TAI and its affiliates have been operating in North America for more than 60 years to support the automotive business of Toyota Group companies and other automotive industry manufacturers. Some of TAI’s existing green supply chain initiatives include operations in postconsumer and postproduction scrap metal collection and conversion to secondary aluminum alloys, along with closed-loop recycling with its customer base.
Founded in 1898, Alter is a privately owned, fifth-generation company that is ISO 9001 and 14001 certified. The company employs 1,325 people and operates 70 metal recycling facilities and seven trading offices in eight states, along with its representative sales office in Hong Kong.
Rio Tinto to add aluminum remelt furnace
London-based mining and metals firm Rio Tinto says it will invest $8.4 million to add a remelt furnace at its aluminum production facility in Saguenay-Lac-Saint-Jean, Quebec.
The company says the investment will help it expand recycling capacity at that site so it can “offer rolled product customers in North America a new, sustainable solution combining low-carbon and recycled aluminum.”
The new remelt furnace will be added at the plant’s casting center. It will recycle aluminum cuttings from Rio Tinto’s own operations and scrap acquired from rolling mill customers in manufacturing sectors. Those rolling mills typically serve the automotive and packaging industries, according to Rio Tinto.
The company says the remelt furnace will have an initial capacity of 22,000 metric tons of end product per year, with the system expected to be operational at the end of 2021.
“The investment continues Rio Tinto’s focus on enhancing the recycling solutions it offers to customers, supporting the transition to a circular economy,” says Tolga Egrilmezer, Rio Tinto vice president of sales and marketing. “This new furnace will allow us to provide a recycling service to our customers for scrap from their manufacturing processes, helping them meet the growing consumer demand for sustainable products. This innovative step will add to our responsible production in Quebec, where we produce aluminum with one of the lowest carbon footprints in the world using hydropower.”
Rio Tinto says the rolled product recycling service “will complement the closed-looped solution Rio Tinto is offering to billet customers from 2021, providing high-quality alloys made of low-carbon primary aluminum and recycled content.”
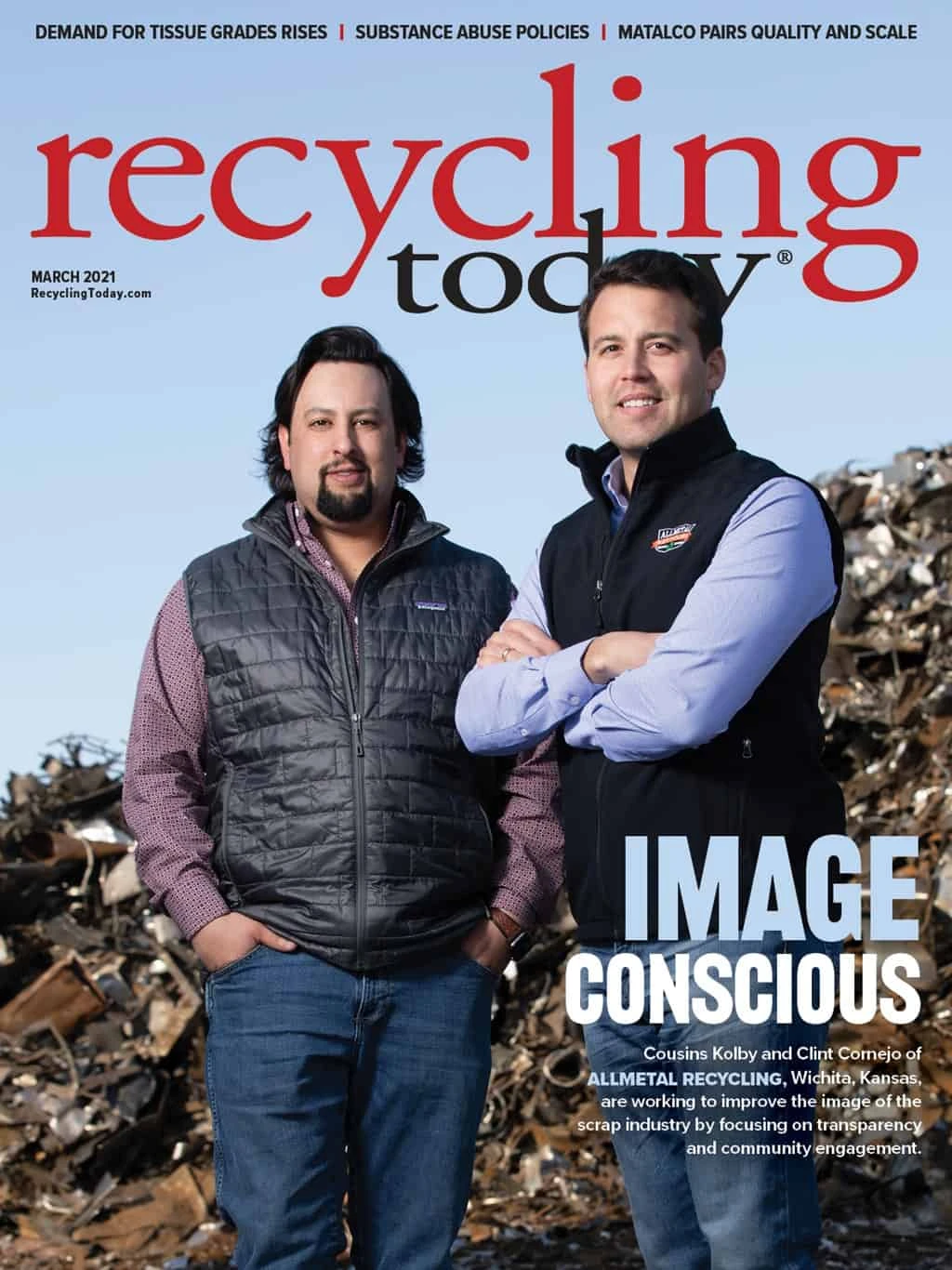
Explore the March 2021 Issue
Check out more from this issue and find your next story to read.
Latest from Recycling Today
- Aqua Metals secures $1.5M loan, reports operational strides
- AF&PA urges veto of NY bill
- Aluminum Association includes recycling among 2025 policy priorities
- AISI applauds waterways spending bill
- Lux Research questions hydrogen’s transportation role
- Sonoco selling thermoformed, flexible packaging business to Toppan for $1.8B
- ReMA offers Superfund informational reports
- Hyster-Yale commits to US production