
SDI works to increase shredded scrap use
During a Steel Dynamics Inc. (SDI) earnings call April 21, the company’s executives spoke about the advantages of SDI’s vertically integrated operations and the rising role that obsolete scrap is playing at its electric arc furnace (EAF) steel mills.
“The team continues to effectively lever the strength of our circular manufacturing operating model, benefiting both our steel and metals recycling operations by providing higher quality scrap, which improves furnace efficiency, and by reducing companywide raw material working capital requirements,” SDI Executive Vice President and Chief Financial Officer Theresa E. Wagler said.
The steel company’s Chairman, President and CEO Mark D. Millett added, “In today’s environment, our advantage of having our metals recycling platform is even greater. In the last 18 months, our recycling and steel teams have worked closely in developing a higher quality shredded scrap that can be used in place of prime scrap. The combined efforts resulted in our Butler flat-roll steel division reducing its need for prime scrap from 65 percent of its mix to only 40 percent while achieving the same steel qualities. We are currently rolling this out to our Columbus [Mississippi] and Sinton [Texas] steel divisions, allowing for a lower cost, readily available lower scrap supply.”
He added that because of the historically high spread between prices for prime and obsolete grades of approximately $170 per ton, the reduced prime scrap requirement has provided SDI with “significant” cost savings.
However, SDI does have plans to close the loop on prime scrap generated by some nearby customers purchasing steel from its Sinton mill.
Millett said, “We have seven customers locating on our site, representing up to 1.8 million tons of annual flat-roll steel processing and consumption capability. Four are already operating, and the other two have broken ground—other three have broken ground, actually. This represents a unique closed loop process as we provide them on-site steel and, simultaneously, we claim their scrap to be rerouted into new steel products.”
Additionally, SDI’s purchase of Zimmer, a Mexican metals recycling company, in 2020 “provides a critical source of prime scrap supply to the Sinton mill, he said.
Regarding SDI’s Sinton mill, Millett said, “This electric arc furnace steel mill represents next-generation, lower carbon-emitting steel production capabilities providing differentiated products and supply chain solutions.”
He added that the site “provides us with a more diverse value-added steel product portfolio and benefits our customers with an even broader climate-conscious supply option. Sinton’s strategic location is centralized in an underserved consumer region that represents over 27 million tons of relevant flat-roll steel consumption in the U.S. and Mexico. We offer shorter delivery lead times, providing a superior customer supply chain solution for the region. We also effectively compete with steel imports arriving in Houston and the West Coast.”
Millett continued, “We currently expect 2022 shipments from Sinton to be over 1.5 million tons, achieving utilization of approximately 80 percent by the end of the third quarter and over 90 percent before year-end.”
The company posted net sales of $5.6 billion and net income of $1.1 billion, or $5.71 per diluted share, in the first quarter of 2022, which ended March 31. Excluding costs of approximately $84 million, or 31 cents per diluted share (net of capitalized interest), associated with the startup of its Sinton flat-roll steel mill SDI’s first quarter 2022 adjusted net income was $1.2 billion, or $6.02 per diluted share.
For additional information on SDI’s Q1 2022 earnings, visit http://bit.ly/sdi-shredded-scrap.

US Steel posts record Q1 profits
United States Steel Corp., headquartered in Pittsburgh, has reported first-quarter 2022 net earnings of $882 million, or $3.02 per diluted share. That compares with first-quarter 2021 net earnings of $91 million, or 35 cents per diluted share, representing a year-on-year increase of nearly 870 percent.
“It was another quarter of records at U.S. Steel with the continued demonstration of the power of our ‘Best for All’ strategy,” U.S. Steel President and CEO David B. Burritt says. “The team’s stellar performance drove our best ever first-quarter results, despite the challenging global dynamics that emerged throughout the quarter.”
Referring to U.S. Steel’s Big River Steel electric arc furnace (EAF) mill in Arkansas and other scrap-melting EAF steel mills, Burritt says, “Our minimill segment delivered 38 percent earnings before interest, taxes, depreciation and amortization (EBITDA) margins, outperforming both minimill and integrated peers.”
Looking ahead, Burritt says, “We currently expect the second quarter to be the company’s all-time best second quarter as our balanced customer portfolio, raw materials integration and operating leverage is expected to expand adjusted EBITDA and support another quarter of strong EBITDA margin and cash generation. We believe U.S. Steel is well-positioned to earn a significantly higher multiple as we demonstrate improved earnings performance, higher free cash flow, increasing direct returns to stockholders and outstanding leadership in innovation and research and development.”
He says U.S. Steel’s Best for All strategy remains viable, particularly in light of the geopolitical uncertainty and elevated raw material costs seen today. “Our iron ore mines are a unique competitive advantage that cannot be easily replicated by other competitors,” Millett continues.
“Additionally, we continue to progress on our sustainability goals and deliver the ‘green’ products our customers are increasingly demanding. We are also demonstrating our environmental, social and corporate governance (ESG) leadership. Earlier this year, Big River Steel became the first North American steel facility certified by [Australia-based] ResponsibleSteel. This is independent affirmation of our commitment to ESG excellence and sustainable processes and products.”
Hydro breaks ground on Michigan plant
Aluminum producer Norsk Hydro ASA, based in Norway, has broken ground on an aluminum recycling plant in Cassopolis, Michigan. The plant has been designed to produce some 120,000 metric tons of aluminum extrusion ingot per year using what Hydro calls 75 percent postconsumer scrap.
Hydro’s President and CEO Hilde Merete Aasheim was among those present at a ceremony April 20 in Cassopolis. Hydro says it will invest an estimated $150 million to complete the project. The ingots made there will be used in automotive applications, other transportation uses, consumer and building system applications, the firm says.
“Aluminum is a key enabler in the green transition,” Aasheim says. “Recycling aluminum scrap reduces energy consumption and greenhouse gas emissions whilst promoting a more circular economy. Our plant in Cassopolis will be an example of sustainability and profitability going hand in hand.”
The Cassopolis plant will be the first large-scale producer of Hydro Circal in North America. That branded aluminum extrusion ingot contains at least 75 percent postconsumer scrap, certified by third-party auditors, and has what Hydro calls a market-leading CO2 footprint. “With a growing focus on sustainably produced aluminum, several North American customers have expressed interest in Hydro Circal,” the company says.
Hydro calls itself a leader in low-carbon recycled aluminum and says it can expand that status by bringing Hydro Circal to the U.S. market.
“Our state-of-the-art technology allows us to dig deep in the scrap pile and re-create value by bringing low-value scrap types back to life as value-added products to demanding customers whilst supporting them in delivering on their sustainability ambitions,” says Eivind Kallevik, an executive vice president with Hydro.
Trond Gjellesvik, North American president of Hydro Aluminum Metals, tells Recycling Today that while the company is piloting technology in Germany that will allow it to use a wider array of obsolete scrap, the Michigan site does not include plans to deploy similar separation and sorting technology currently.
Gjellesvik says Hydro mainly will purchase 6000-series alloy obsolete scrap for use at the site, including aluminum wheels and power cables, as well as postindustrial scrap from extrusion-producing facilities.
“We typically like to work directly with the scrap providers” rather than brokers, he says.
Get curated news on YOUR industry.
Enter your email to receive our newsletters.
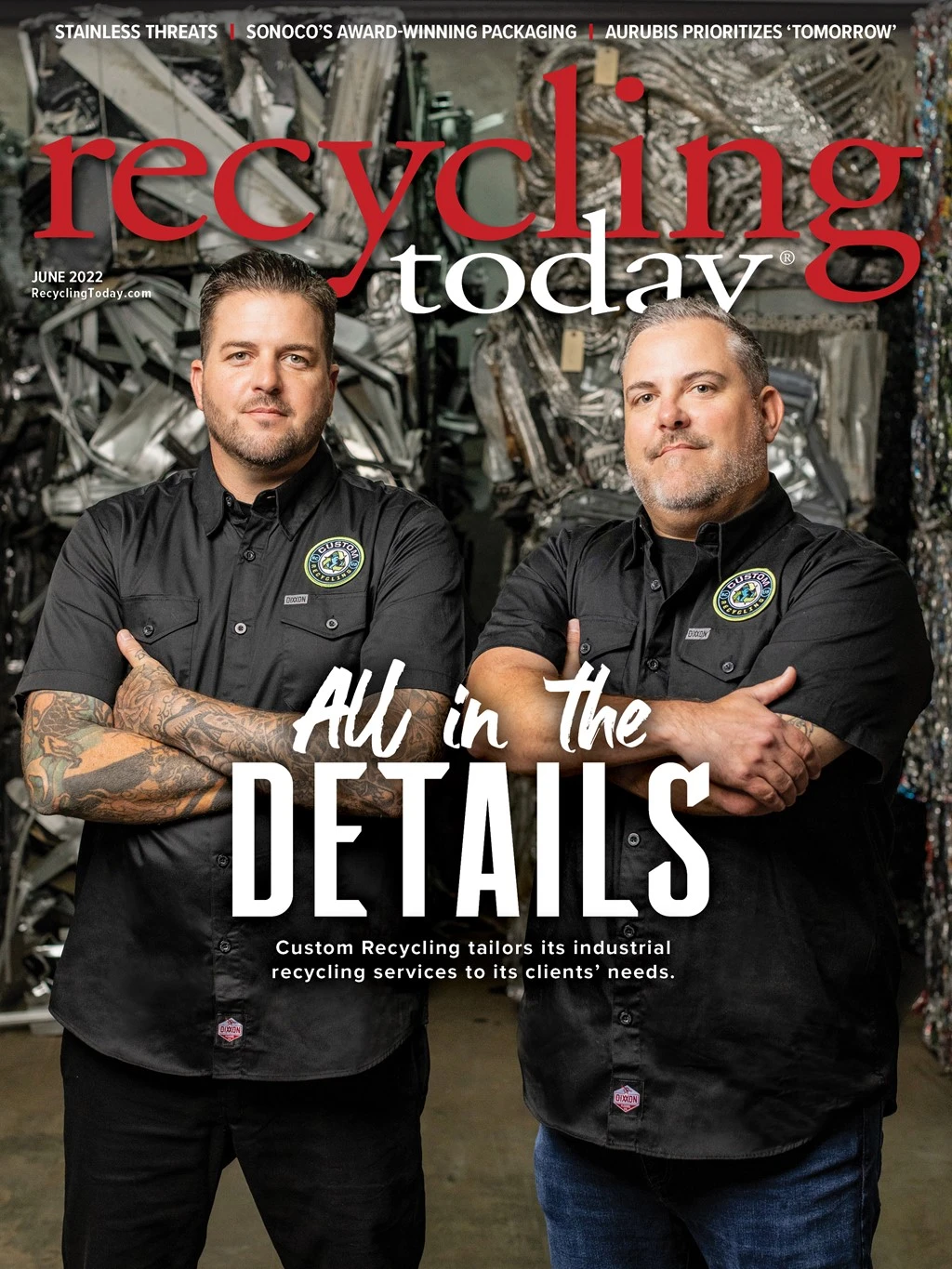
Explore the June 2022 Issue
Check out more from this issue and find your next story to read.
Latest from Recycling Today
- EuRIC, FEAD say End-Of-Life Vehicle Regulation presents opportunity for recyclers
- Recyclers likely to feel effects of US-China trade war
- BCMRC 2025 session preview: Navigating battery recycling legislation and regulations
- Yanmar Compact Equipment North America appoints new president
- LYB publishes 2024 sustainability report
- Plum Creek Environmental acquires Custom Installation LLC
- Avis introduces Harris American Co.
- International Paper in talks to divest 5 European box plants