Novelis creates high-recycled-content aluminum alloy for automotive industry
Novelis, Atlanta, says its RC5754 alloy, a new automotive product designed to contain up to 75 percent recycled content, has been integrated successfully into the structural components of high volume production passenger vehicles.
RC5754 was developed with Jaguar Land Rover and serves as a key component of Jaguar’s REALCAR (REcycled ALuminum CAR) project. First introduced in the new Jaguar XE, the RC5754 alloy also will be featured in all new and legacy Jaguar Land Rover models.
Novelis and Jaguar Land Rover compiled what they learned from developing this new product in “Collaboration for a Closed-Loop Value Chain,” a case study issued in January following the companies’ participation in the University of Cambridge Institute for Sustainability Leadership’s Postgraduate Certificate in Sustainable Value Chains.
“As a leader in alloy innovation and aluminum recycling, Novelis is honored to work with Jaguar Land Rover to help lead the automotive industry in sustainable vehicle manufacturing,” says Pierre Labat, vice president, automotive, Novelis Europe. “Novelis’ new RC5754 alloy not only meets the high recycled-content threshold required by Jaguar Land Rover’s REALCAR project but also it delivers the strength, durability and formability specified by world-leading Jaguar Land Rover engineers.”

Labat recently was promoted to vice president, sales and marketing, global automotive, effective April 1, 2016.
Launched in 2008 by Jaguar Land Rover, REALCAR is a multistakeholder initiative established to create a closed-loop vehicle production model that recycles automobiles at the end of their lives. The RC5754 aluminum alloy, developed by Novelis for REALCAR, is designed to use higher levels of scrap.
Novelis says it expects double-digit growth in automotive aluminum use globally by 2020 and is expanding its manufacturing in Europe, North America and Asia.
Mallin Cos. expands production line
Kansas City, Missouri-based Mallin Cos. has announced the expansion of its wire processing production line, allowing the family recycling business to process a broader variety of materials.
“The benefits of a long-term relationship, fourth-generation leadership and advanced engineering have resulted in a decisively superior wire processing production line,” the company says.
To retain its standards of clean, high-grade choppings and recycled nonferrous scrap metal, Mallin says it made the decision to grow the production line, working with multiple partners, including long-time engineer and original outfitting partner Dallas-based Triple/S Dynamics, part of the KMC Global group of companies, to lead the project.

After two years of planning and installation, Mallin says its new system allows it to proccess a wider range of products for its industrial customers, including extrusions, copper-aluminum radiators and auto shredder residue (ASR).
Mallin Cos. says the upgrades save energy, while all incoming materials are refined and prepared to rigid specifications.
Mallin Cos. Vice President Zachary Mallin says, “Outcomes are already exceeding expectations.”
As an entrepreneur-led, family-owned business, Mallin says it emphasizes continuous research, technological upgrades, marketing and customer service to position its material against that of larger multilocation companies in the scrap and recycling industries.
“We are able to recycle a broader variety of materials through a versatile line that saves energy and maximizes value for our customers,” he says. “Beyond that, all components are refined and prepared to rigid specifications, resulting in products of the highest purity. What’s more, the byproduct is reusable.”
Mallin Cos. says it is one of the largest wire processing facilities in the country, with expertise in wire chopping technology and nonferrous scrap recycling. The company operated one of the first wire chopping facilities in the nation.
ScrapSource to manage scrap for Mueller
ScrapSource, Dallas, has entered into a multiyear contract with Mueller Inc. to provide scrap management services at all Mueller facilities.
Mueller manufactures and engineers metal roofing and steel building products. The company is headquartered in Ballinger, Texas, and serves the Central and Southwest United States with 32 branch locations in Texas, New Mexico, Louisiana and Oklahoma. The company employs more than 600 people.
“We are pleased to be awarded this contract and look forward to working with the Mueller team on setting up a corporatewide scrap metal program,” says Larry Olschwanger, president of ScrapSource.
Rayomé Soupiset, manager of operations of Mueller, says, “ScrapSource’s scrap management program has delivered superior improvements from the way we used to handle our scrap metal recycling, and we now feel that we are fully optimizing the disposition of all of our scrap.”
Founded in 2010, ScrapSource is a boutique scrap management and consulting firm that provides solutions for companies that generate scrap metal during manufacturing. ScrapSource says it helps companies make smarter scrap recycling decisions.
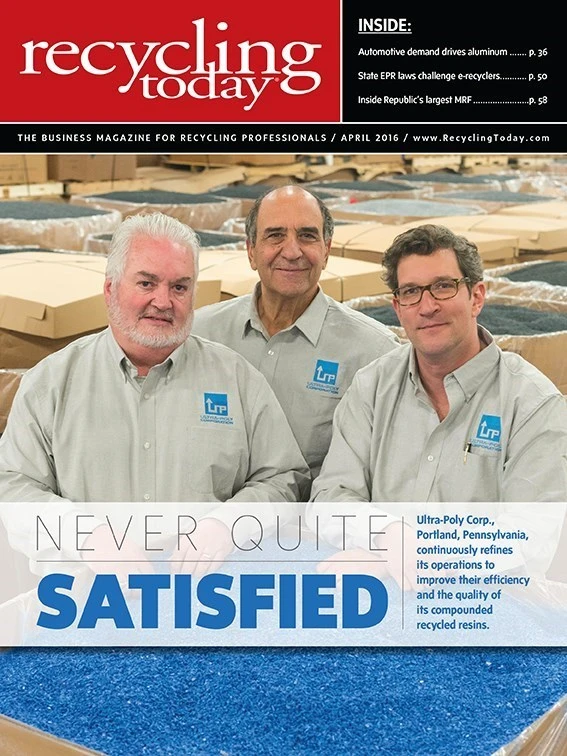
Explore the April 2016 Issue
Check out more from this issue and find your next story to read.
Latest from Recycling Today
- Nucor receives West Virginia funding assist
- Ferrous market ends 2024 in familiar rut
- Aqua Metals secures $1.5M loan, reports operational strides
- AF&PA urges veto of NY bill
- Aluminum Association includes recycling among 2025 policy priorities
- AISI applauds waterways spending bill
- Lux Research questions hydrogen’s transportation role
- Sonoco selling thermoformed, flexible packaging business to Toppan for $1.8B