Maintaining healthy top-line revenue at scrap recycling companies has been more difficult in the past two years as flows of incoming scrap have been harder to obtain.
With industrial production down, construction and demolition work in a trough and the purchase of new autos and appliances down considerably, the leading sources of scrap generation have been firing their engines at slower speeds.
Auto shredder operators are pursuing scrap volumes as are all other dealers and processors. One option they have, however, involves investing to extract more metal, by percentage, from their obsolete scrap stream, no matter what volume may arrive each week or month.
THE UNTAPPED WELL
Throughout the last two decades, makers of metals sorting and separating equipment have successfully convinced auto shredder operators that investing in the equipment they make will soon yield a healthy return on investment.
DON’T FORGET FERROUS |
In an essay written for Recycling Today in 2009, Bill Tigner, president of U.S. Shredder & Castings Group, Trussville, Ala., writes that recyclers and equipment providers are not only experimenting with downstream nonferrous scrap capture, but they also continue to tinker with their ferrous yields. Shredding plant configurations and dust control methods have all come into play, notes Tigner, who writes, “With the introduction and fine tuning of water injection systems, dust control, cleaning and explosion reduction (not elimination, of course) have all been greatly improved. The current debate has drawn down to whether two [drum] magnets are best or only one.” Tigner has his preferred answer: “Two drum magnets in line are extremely successful in various systems throughout the world. They can generally match or exceed the performance of a single magnet plus z-box system, although their success relies on one major variable: the volume and speed of material as it is exposed to the magnets.” Tigner adds, “While one magnet with a supporting z-box air system is viable as proven by a couple of manufacturers, the advantages of two magnets (with or without air) make this system a more effective and often a less costly approach to clean shred.” |
Shredder owners and operators have largely learned from that experience, and most have become eager researchers and often purchasers of new sorting and separation technology as it is introduced.
What began as the placement of one or two eddy-current separators at the end of a shredding system has turned into an entirely new sub-sector of the industry, with specialists who produce downstream systems designed for maximum recovery and flexibility to adapt when markets change.
When scrap companies, or their equipment suppliers, announce a new shredding plant installation, the announcement almost always includes a description of the accompanying downstream system that will help to extract as much clean nonferrous scrap as possible.
Before the installation or sale, auto shredding plant makers typically compete to assure the prospective buyer that they will either work with select allied vendors to design a thorough downstream system or that they will help the recycler choose among vendors to tailor the system that is best for the application.
When Tube City IMS and Riverside Engineering announced the Tube City shredder installation in West Mifflin, Pa., the size and throughput of the 88 x 112 plant was certainly mentioned, as were the system’s downstream capabilities.
“We were seriously considering closing our shredding operation because the margins were minimal and costs high; however, upon consulting with Riverside, we realized that investing in new technologies would lead to significant increases and reduced costs,” said David Coslov of Tube City IMS in August of 2009, when the new plant began operating.
Scot and Craig Uhrig of All Recycling, Englewood, Colo., have spent the past decade growing their business around increasingly larger and more sophisticated shredding plants. (See “All Systems Go” in the December 2009 edition of Recycling Today.)
A MUNICIPAL MARKET |
The city of Ames, Iowa, announced in November of 2009 that it had installed a nonferrous metal recovery system at its Arnold Chantland Resource Recovery Plant to pull more metals out of its municipal solid waste stream. “We believe this new equipment will allow us to collect more than 150 tons of nonferrous metal annually, keep it out of the landfill, and recycle it while generating revenue,” says Gary Freel, Resource Recovery Plant assistant superintendent. Previous to the addition of the new equipment, the facility only used magnets to extract ferrous metals. The equipment included a 40-inch Steinert eddy-current working in tandem with an Induction Sorting System (ISS) from Steinert. The system was expected to cost $1.1 million to purchase and install. The county says it expects to see the payback for the purchase within four years. |
Even after the market downturn of 2008, the Uhrig brothers continued to invest in areas of the business they calculated would pay off, including the installation of new downstream shredding equipment in 2009.
Eddy-current separators remain a vital part of most of these downstream systems and, in some cases, are deployed four or even six at a time against the various fractions of scrap product being churned out by shredders. Units may be arranged to address different sizes of scrap as well as being deployed at different stages of metallic versus nonmetallic content.
A variety of new automated identification and separation technologies have joined eddy currents on the roster of sorting equipment being deployed at shredder yards, targeting red metals, aluminum, stainless steel, insulated wire and any number of other valued materials that previously may have been unrecoverable at the shredding plant site.
The widespread acceptance of this equipment has provided an ongoing task for the Institute of Scrap Recycling Industries Inc. (ISRI) committee that updates scrap metal product specifications. In the past several years, a variety of new post-shredder nonferrous scrap grades have been created as shredding plant operators continue to expand their ability to produce new blends or clean new streams of scrap from their shredder infeed.
STAYING CURRENT
The severe downturn in pricing and credit markets that occurred in the fall of 2008 has been followed by a sustained reduction in scrap volumes. That combination would seem to be enough to dampen the enthusiasm of scrap recyclers to invest in more equipment.
But shredder operators contacted for a story on their sector (See “Moving Target,” starting on page 64 of this issue.) almost unanimously agreed that investments in downstream shredder sorting not only pay for themselves in a slower market, but they may be even more important to stay competitive.
“If you can make a better quality nonferrous product, you’re going to be more successful in this market,” says Dan Wycoff, general manager of Shine Bros. Corp., Spencer, Iowa. Like many other shredder operators, Wycoff says Shine Bros. Corp. is “producing some of the new grades in addition to zorba.”
Research also continues into ways of adding plastic sorting and recovery into downstream systems. Progress in harvesting recyclable, clean plastic scrap effectively and affordably from the post-auto shredder stream has been slower, but research and development continue.
The innovations from manufacturers are likely to continue as well. For the 2010 ISRI Convention & Exposition, at least one vendor is already promising something new for scrap recyclers to continue in terms of sorting technology.
In a news release, Eriez, Erie, Pa., says its new machine will be able to capture a portion of the residue stream that had previously been allowed to pass through downstream equipment, or had to be hand sorted.
In all likelihood, shredder operators who have benefitted from new technology in the recent past will be willing to consider a new product offering that could improve metals yields and bottom-line results.
Get curated news on YOUR industry.
Enter your email to receive our newsletters.
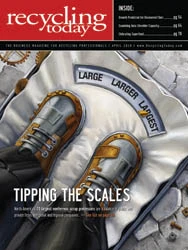
Explore the April 2010 Issue
Check out more from this issue and find your next story to read.
Latest from Recycling Today
- Freepoint Eco-Systems receives $50M loan for plastics recycling facility
- PET thermoform recycling the focus of new NAPCOR white paper
- Steel Dynamics cites favorable conditions in Q1
- Hydro starts up construction in Spain
- Green Cubes unveils forklift battery line
- Rebar association points to trade turmoil
- LumiCup offers single-use plastic alternative
- European project yields recycled-content ABS