
George Allen Mebane IV founded Unifi in 1971 with the intention of disrupting how textiles are made. The synthetic fibers manufacturer has innovated over the years, but its 2007 introduction of Repreve recycled fiber allowed Unifi to level up its commitment to sustainability by recycling its manufacturing scrap and then polyethylene terephthalate (PET) bottles through its Repreve Bottle Processing Center and Repreve Recycling Center.
Meredith Boyd, senior vice president of sustainability, technology and innovation at Unifi, joined the Greensboro, North Carolina-based company as it was preparing to launch Repreve. Since its launch, Repreve has risen in popularity and is on track to account for 50 percent of Unifi’s sales by 2025 in addition to having recycled more than 35 billion bottles through 2023. She says the company intends to recycle 50 billion bottles by 2025.
In her role, Boyd works alongside Unifi’s intersectional teams to drive international growth, playing a critical role in product conception and execution while emphasizing sustainable practices and development.
“It was really exciting to be part of both the technical and operational and development and also the commercial aspects of bringing Repreve to a really significant scale, first in the Americas and then later globally,” she says.
In the area of sustainability, Boyd says the company works to ensure it’s making specific claims about why Repreve is better than virgin polyester products and backing it up with data, such as its recently released life cycle analysis.
“We are looking at what can we do operationally,” she says. “What can we do with the equipment in which we invest that can further reduce the overall environmental footprint of Unifi?
“On the technology side, that piece of my role is tied into ensuring that we are leveraging the best possible ways to make all of our products. Our team works to research different manufacturing technologies and prove existing ones, and looking at the environmental aspects of a lot of those decisions has become a core part of our process.”
The innovation aspect of her role involves creating new products and delivering new solutions that help bring the company’s sustainability and performance benefits to a broader audience, whether it be upstream with suppliers or downstream to customers.
Boyd shares more about Repreve’s place within Unifi in the following interview, edited for clarity and conciseness.

Recycling Today (RT): What does sustainability mean at Unifi?
MB: It’s our mission. For us, that mission is empowered through Repreve to reduce carbon emissions associated with products because we are giving those discarded resources new purpose, and that’s as high-performance materials that are going to perform head-to-head with a virgin equivalent.
For us, it really has become an empowerment mission because we’re able to then provide that material to our direct customers and, ultimately, to the brand customers, the consumer, and it’s a way that can say small changes can make big differences.
Sustainability can feel intimidating, but by making small choices about where I spend my own resources, I’m able to make a difference here, and Unifi through Repreve is helping me understand just how big that can be.
RT: Can you speak specifically to the role recycling plays in achieving the company’s sustainability goals?
MB: Recycling is becoming a more and more significant part of everything we do. By having such high-quality recycling processes, it opens up the Repreve materials to go anywhere. For example, at our Bottle Processing Center, that’s where we take materials like plastic bottles and transform them into a clean, washed polyester flake. That flake then can travel to our Repreve Recycling Center, where it’s made into our resin products, but it also can go to companies that can use that material directly.
The next step in the process is, essentially, you’re taking the flake material, and you can also have textile waste material, and you’re melting it down. It’s in this lava-like, molten state. You’re removing contaminants, that’s the proprietary piece for us, and then we’re creating what’s called a resin. That resin becomes the raw material to make Repreve yarn, but it also can go into applications that use resin as the starting point.
It’s been exciting for us to grow that piece of the business where we are able to then provide raw materials into industries that we don’t have the manufacturing for today. That has been a growth area for us.
RT: My understanding is that when it comes to recycling PET bottles into fibers for textile applications that pelletizing isn’t necessarily required, it can be used in the flake form. So, you are actually bringing it to a pellet even for your textile applications?
MB: By creating a resin, we are able to ensure this product is going to be as virgin-analogous in properties as possible. That means a couple things. One is polyester is an amazing material because it doesn’t mind if you heat it up and cool it down and heat it up and cool it down. We’re able to do a lot to actually ensure the cleanliness of that stream is optimized. We want to end up with properties that are virgin-analogous. By having this process, we’re able to get rid of a lot of contaminants.
When you think about that Repreve recycled polyester yarn, imagine a tiny, tiny rope, and every individual little piece of that is a filament. Some of these filaments are actually finer than the diameter of a piece of hair, and if you have contaminants that are even smaller than what our eyes can see, they can create process failure; they can generate waste.
One of the basic pieces of our mission is we want to reduce, reuse, recycle—we want to make sure we’re not generating unnecessary waste. We want to make sure we have a process that is going to run very well. By creating this Repreve resin, it is ensuring we are going to have a raw material that can go into the broadest range of all of these yarn products, whether it’s apparel, automotive, furnishings or industrial. It really gives us that versatility and gives the customer that confidence when they are choosing to specify Repreve; they know it’s going to perform in their process like they expect it to.
RT: I imagine, also, the higher quality the resin, the more consistent the coloration, etc.?
MB: I’m glad you brought that up. While we have our core Repreve recycled offerings, we also have product technologies. Those technologies could be color—we call our product Waterwise, where we’re putting pigment in the polymer melt—or other performance technologies that are highlighting anti-odor or flame retardancy. By having this high-quality resin, it gives us the flexibility to be able to create these different materials and then further enhance the value, whether that’s in other aspects of sustainability, performance or even being able to offset topical chemistries that might have traditionally been applied downstream.

RT: What is the scale of your recycling operations?
MB: The scale of recycling materials that come through and are processed at Unifi’s North Carolina base is in the multimillions. Our Reidsville, North Carolina, Bottle Processing Facility has a 75-million-pound annual capacity, and our flagship Yadkinville, North Carolina, Repreve Recycling Center has 100 million pounds of annual capacity. We receive 40 to 60 approximately 40,000-pound truckloads of material per week and aim to process 1.5 million pounds of those postconsumer bottles we intake in the same time frame.
Beyond that, Unifi collects and transforms waste into Repreve on a domestic and global scale.
RT: Can you talk more about the recycling technologies Unifi employs?
MB: We’ve got pieces that create Repreve, and then we’ve got pieces that complement it.
To create Repreve, we employ a tremendous amount of technology all the way back to even the bottle processing step. We employ technology to sort by polymer type and by color and extensive cleaning and flotation of different byproducts in the bottle process, and that’s in Reidsville. Then we are taking the primary output of that plant, which is clean, clear flake, to Yadkinville to our Repreve Recycling Center.
At the recycling center, we’re employing what is called thermomechanical recycling. We have several lines. We have lines we’ve designed to be able to handle really challenging waste that may not be in pristine form, such as textile waste materials that are coming back from our customers or downstream brands. We’re employing different technology to be able to make sure that whether it’s coming from bottles or textile waste, we can elevate those properties to ensure it performs virgin-equivalent in our processes as well as our customers’.
The actual thermal mechanical recycling process—that heat it up, cool it down process—that’s where it’s in that lava-like state. It’s a liquid now, but it’s still polyester; we haven’t torn apart the material. Then it goes through that proprietary filtration technology to make sure we get it as clean as can be. We’re analyzing the product through inline monitoring and offline monitoring, and then we’re creating that resin.
The resin to make our Repreve yarn is then going next door to our spinning plant. Now, this is a melt-spinning plant, so we’re going to heat it up and cool it down. Again, there are proprietary steps in there to make sure it’s ready to go into what are incredibly fine textile yarns to make the greatest diversity of product to be able to go into all these industries. Out of melt spinning comes an intermediate yarn product, and it looks a lot like dental floss. When we take it into the final step of the process, texturing, we’re going to be drawing it, pulling it, roughing it up, adding bulk. Through these processes, we’re able to engineer the product with the needed properties.
Additionally, from a technology standpoint, I’ll mention FiberPrint tracer. We developed this technology to provide that physical tagging so Repreve would be identifiable whether it’s in resin, whether it’s in the dental floss-looking product, whether it’s in the textured finished product, in fabric, in a garment, in the seat upholstery of your car or pulled out of your closet 25 years from now. That’s allowing us to have transparent communication through the whole value chain. We developed our own certification program as well, U Trust, at the fabric [level] and then more recently at the product level to ensure fabrics are certified to contain Repreve. We do that by ensuring FiberPrint tracer technology is present and at the intended level.
RT: What aspects of your job do you find most invigorating? Challenging?
MB: It’s a dynamic existence. So, for example, when you think about the products that need to be created just to deliver on all the different kinds of textiles, nonwovens or packaging materials, this isn’t a steady-state existence. It’s not something where, “Oh, we created one product in 2007 and now I just hit a button and it runs.” No. There are literally an endless number of products that can be created to serve different performance properties [and] attributes. The Repreve recycled polyester we create, for example, for going into yarn, textile products, is different than the resin that we create for going into packaging materials. So, that constant state of being able to ideate change, never being satisfied—in a good way—with steady state, I think that that really keeps my brain and a lot of my colleagues challenged because we’re constantly questioning, “How can we do this better? How could we eliminate this step from a process? How can we reduce the energy required?” And I love that aspect, but it’s just a continuous innovation mindset.
Yes, there are challenges, and some are really healthy challenges; other ones are pragmatic. You have a new product technology that launches. We have vetted it to the nth degree through all we can internally, and you have that first engagement with a key customer partner. And you go into a commercial fabric formation and finishing process, and they say, “Hey, let me give you some feedback on this.” And then we have to honor that because they are the experts, and that feedback that we value allows us to go back and say, “OK, we need some refinement here. But it can be challenging, too, because you get something kind of to that finish line, but it is not perfectly linear.
You have to be OK, with failure. We need to learn from it. We need to look at: What was avoidable versus what wasn’t? And it’s going to have a real impact on something that we then do in the future.
RT: As beverage brands are committing to using more recycled content, where does that leave Unifi and other recyclers who have targeted the fiber sector more specifically?
MB: A couple things here. One is that in the U.S., for example, our recycling rate is abysmal, and there is so much opportunity to still generate more of these materials ending up in recycling streams instead of in the landfill. There is still such an upside there in terms of generating more of this material, whether it’s going to go into fiber, if it’s going to go into their bottles or if it’s going in [other] packaging. Additionally, the process we’ve developed is very versatile in regard to polyester input material, whether it be bottles or your old workout top. There are other industrial byproduct materials as well that we’re able to use in our processes that could be out of nonwovens, film and certain other types of industrial filaments. We’re able to use very broad waste input materials. We expect will continue to grow in that space. You know about the expansion of our Textile Takeback program in the fall of last year, it’s certainly a part of that.
RT: You’re able to process that all on a single line, blending the bottle material with the textile materials?
MB: We have developed everything from material handling, sort and prep into how we process it, all of that is part of our intellectual property around how to manage different materials, how to ensure you’re achieving the properties of the finished resin or yarn that are needed. But it is a very technically intensive piece. Working with our sourcing team, it becomes somewhat of a very special puzzle to ensure that we are combining the materials in the appropriate way so that we are having that consistency in the recycled product.
RT: Where do you think Unifi could be five or 10 years from now in terms of the bottle-versus-textile mix?
MB: Textile waste inputs have actually been part of Repreve for a long time but continuing to build the ability to handle more challenging textile waste materials, that’s part of our active journey. But this infrastructure also has to be set up. One thing we’re doing today is working very closely with our brand partners to speak about designing for recyclability. How can we look at ways that deconstruction can be facilitated more easily so it’s not an intensive process? And that’s been a really exciting area to have those highly technical material conversations because it also challenges us to have to create materials that maybe have to perform like other materials. So, it’s a very comprehensive area, but designing for recyclability is part of that. And we’re active in industry organizations that are looking at how to really get that infrastructure created, so that we can start to see the ability to bring in the textile materials, pre- and postconsumer, back into the stream.
RT: What does an ideal collection program for textile waste look like look like in your mind at this stage?
MB: It’s going to require some synergy between waste collection, municipalities, manufacturers, even mills and brands in order to really create this whole structure. We have to ensure education is there, the infrastructure is there, that’s sort of what I see as being an essential part.
From a technology standpoint, I think it will take a suite of technologies to handle different materials. Some materials will be very appropriate for thermomechanical recycling. Some materials may have to go down a path that employs chemical recycling by looking at what is the way to elevate the value of that material while ensuring that the lowest environmental impact of that process is maintained. It’s going to take cooperation and collaboration at every step, and that’s an energizing part of it, too.
RT: Do you think retailers have a role to play in textile recycling similar to the role they play in film recycling?
MB: I think it’s such an opportunity. There have been some prominent brands and retailers that have done pilots or ongoing programs, particularly in the apparel space, and then you think about some non-apparel areas, carpet and mattresses, where there have been industry efforts made. I think it’s absolutely part of it. Every step of the chain is going to have to be involved in it.
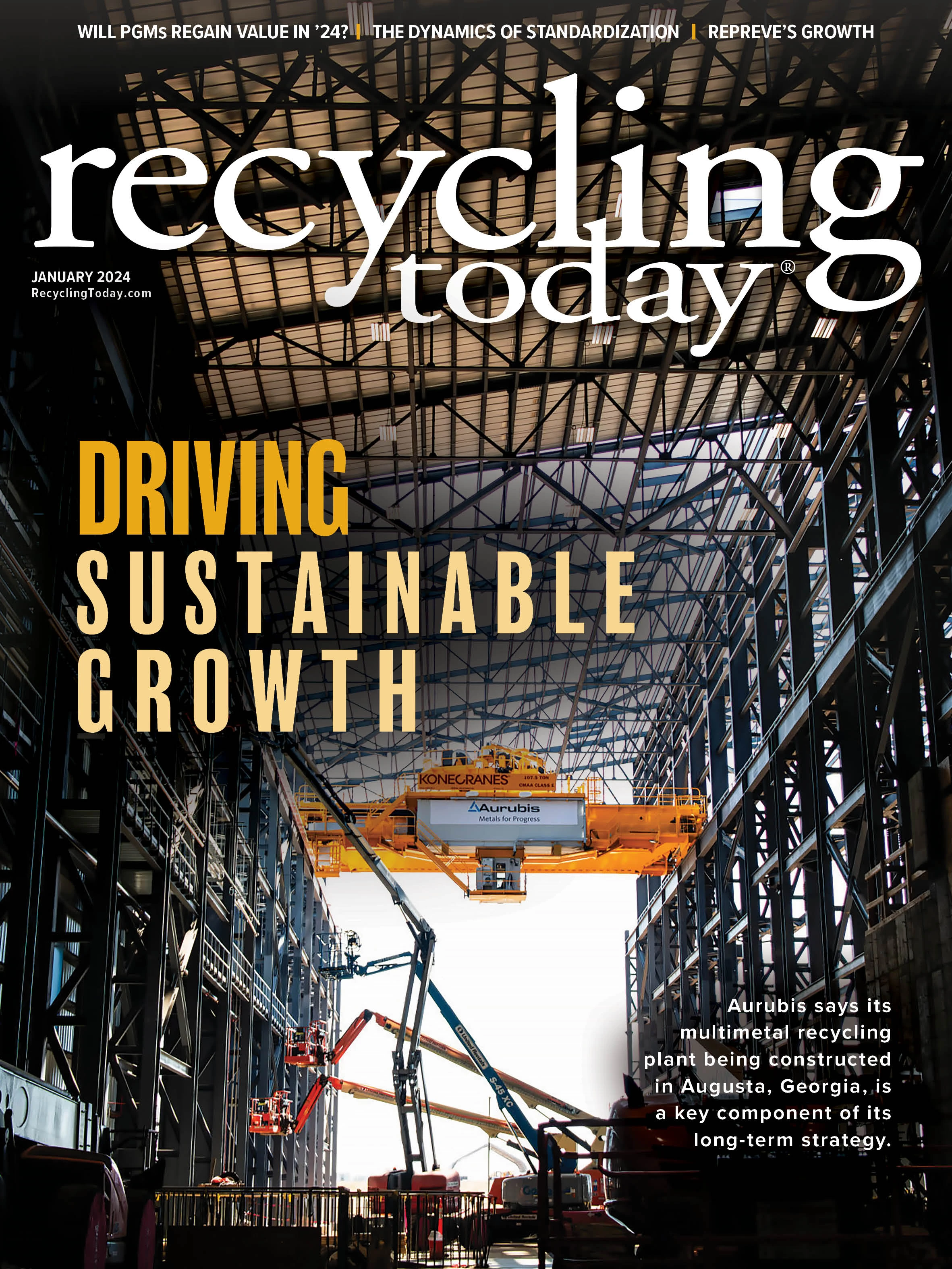
Explore the January 2024 Issue
Check out more from this issue and find your next story to read.
Latest from Recycling Today
- AF&PA report shows decrease in packaging paper shipments
- GreenMantra names new CEO
- Agilyx says Styrenyx technology reduces carbon footprint in styrene production
- SABIC’s Trucircle PE used for greenhouse roofing
- Hydro to add wire rod casthouse in Norway
- Hindalco to invest in copper, aluminum business in India
- Recycled steel price crosses $500 per ton threshold
- Smithers report looks at PCR plastic’s near-term prospects