
Canadian polyethylene terephthalate (PET) recycling facility is seeing an increase in production and a reduction in costs by using
Water bottler Ice River Springs installed a PET bottle-to-bottle recycling line last year at its Feversham, Ontario, plant. The Starlinger recoStar PET 165 HC iV+ line features a Nordson BKG HiCon screen changer that uses Flex Disc filter cartridges for melt filtration.
“The major aim
In PET recycling, there’s usually a high amount of contamination, says Christian Schroeder, global product manager for Münster, Germany-based Nordson BKG melt delivery products. As a result, screens require frequent changes, increasing costs.
Nordson’s BKG backflush technology addressed the problem, he says, as backflushing of the screen substantially prolongs screen life. But every backflush leads to
“Therefore, our key goals were to enlarge the filtration area as much as possible and decrease the melt loss during the backflush process as much as possible,” Niedl says.
The Nordson BKG HiCon K-SWE-250-4K-75/RS-FC backflush screen changer, using Flex Disc cartridges, has a filtration area that’s 2.4 times bigger than standard screens. It has a total area of about 4,000 square centimeters, filtering the melt with a fineness of 56 microns. It also provides for high process stability, as 75 percent of the filtration area is available during screen changing and backflushing.
In addition, Nordson has reduced backflush volume by 40 percent.
Increasing the filtration area reduces the number of screen changes, Schroeder says. “An expanded filtration area leads to a lower flow rate of the melt, which means that the dirt particles hit the filtration medium with little force and are separated from the melt easily.”
The Flex Disc consists of multiple cassettes, and the two screen packs within each cassette allow for the large filtration area. Previous case studies showed screen life can be extended by up to nine times, depending on machine size, contamination level, polymer
The Flex Disc prevents material stagnation zones because the melt has a low residence time. It also reduces pressure variations that can hurt end-product quality, Schroeder says. The device’s steel screen prevents pressure loss and resists deformation, allowing it to hold up to mechanical stresses.
Ice River Springs bought the high-capacity version of the
Schroeder says if the differential pressure increases because of filter screen contamination, the screen changer’s bearing piston automatically moves into the
An Ice River Springs spokesperson says, “The new filtration system has improved our purification process, reduced waste and improved performance to a level at or beyond the commitment made by Starlinger. As recycling streams evolve and become more challenging, this reliable system will continue to provide the quality resin required by Ice River Springs in the coming years.”
Starlinger’s Niedl says the Nordson technology boosts the line’s overall efficiency. “With the Nordson Flex Disc filter integrated into our PET recycling system, the melt loss that accumulates during the backflushing process in the course of the filter cleaning is down to 1.4 to 1.7 percent—a figure that is a lot lower than normal in PET
The line recycles washed PET flakes made from bottles collected curbside.
Ice River Springs operates Blue Mountain Plastics, a PET recycling plant, at its Shelburne, Ontario, headquarters. It is equipped with washing and recycling lines and produces bottles with up to 100 percent recycled content.
For more
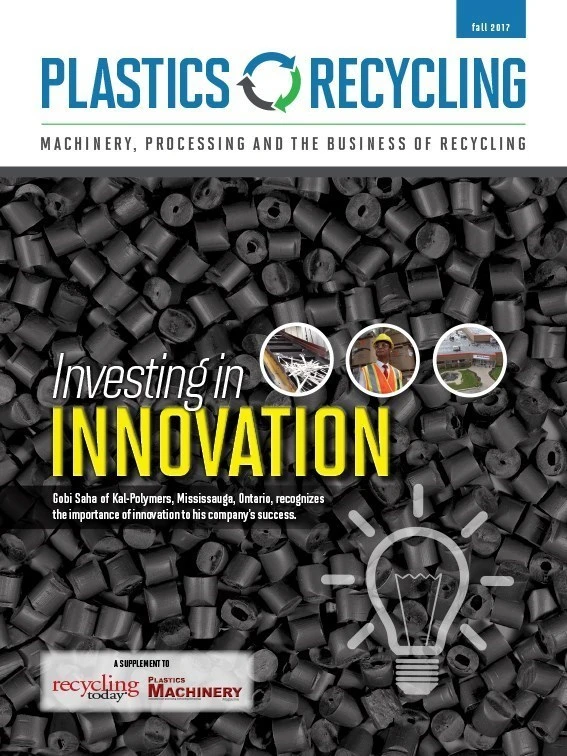
Explore the October 2017 Plastics Recycling Issue
Check out more from this issue and find your next story to read.
Latest from Recycling Today
- AF&PA report shows decrease in packaging paper shipments
- GreenMantra names new CEO
- Agilyx says Styrenyx technology reduces carbon footprint in styrene production
- SABIC’s Trucircle PE used for greenhouse roofing
- Hydro to add wire rod casthouse in Norway
- Hindalco to invest in copper, aluminum business in India
- Recycled steel price crosses $500 per ton threshold
- Smithers report looks at PCR plastic’s near-term prospects