Melt filter. A melt filter for removing contaminants from recycled plastic has earned a patent for Fimic srl, based in Carmignano di Brenta, Italy.
An existing method for removing foreign debris from molten plastic involves two separate filtering machines, each on its own extruder. The resin is allowed to cool after passing through the first machine, then is cut into granules and run through the second machine to remove smaller particles. This method is expensive in terms of equipment, and the multiple cooling and heating steps can degrade the plastic’s properties.

A second method involves continuously processing the molten resin through two separate filtering machines inline. However, “the pressures and the length of the entire path … are so high that they greatly deteriorate the plastic material,” the patent states.
Fimic’s invention consists of a hollow body that contains multiple filters arranged in sequence and that has an inlet and an outlet for the molten resin to pass through. The filters have rotating scrapers driven by an externally operated drive shaft. Debris captured by the filters is removed by the scrapers and is directed out of the device through a hollow section of the driveshaft.
Each filter is composed of a perforated disc or plate firmly attached to the hollow body and a metal perforated sheet that rests on the disc. The sheet is not able to withstand the working pressures of the system, which is why it rests against the sturdy disc. The filters have holes of different sizes, so larger contaminants are captured by the first filter and smaller particles are captured by subsequent filters.
A beneficial feature of the invention is that if the pressure of the molten plastic exceeds a certain value, the driveshaft rotates the scrapers to remove any material that could be obstructing the filters. This prevents the melt from reaching unacceptably high pressures. Additionally, “the driveshaft can be set in rotation on command independently of the pressure reached by the molten material, continuously or according to a sequence or time intervals or as a result of anticipated events,” the patent states.
The invention overcomes drawbacks of existing technologies because it is compact, relatively inexpensive, protects the physical properties of the plastic and is designed to be easy to maintain.
Patent 11,103,812; issued Aug. 31

Depolymerization. The U.S. Patent and Trademark Office has awarded a patent to the Saudi Arabian Oil Co., Dhahran, Saudi Arabia, for a process that recycles used plastics by breaking them down into chemicals, such as light olefins, benzene, toluene and xylene.
The new method involves dissolving the polymers using an aromatic-rich solvent and then catalytically cracking them in a reactor. The method can be used to process polyethylene, polyethylene terephthalate, polystyrene, polypropylene, polyvinyl chloride, polyamide, polycarbonate, polyurethane, polyester, natural rubber, synthetic rubber as well as combinations of these polymers.
In one embodiment of the invention, the reactor is operated at temperatures between 1,022 F and 1,202 F, and the dissolved polymer solution has a residence time of no more than one second.
In at least one embodiment, the step of catalytically cracking the dissolved polymer solution also includes catalytically cracking that solution in a riser fluid catalytic cracker reactor.
The invention has advantages over other depolymerization methods, such as delayed coking, pyrolysis, gasification and liquefaction, because it produces less waste, is more economical and doesn’t introduce contaminants such as sulfur and nitrogen, the patent notes.
The company touts the development as an alternative to incinerating or landfilling when conventional recycling is not economical.
Patent 11,104,851; issued Aug. 31
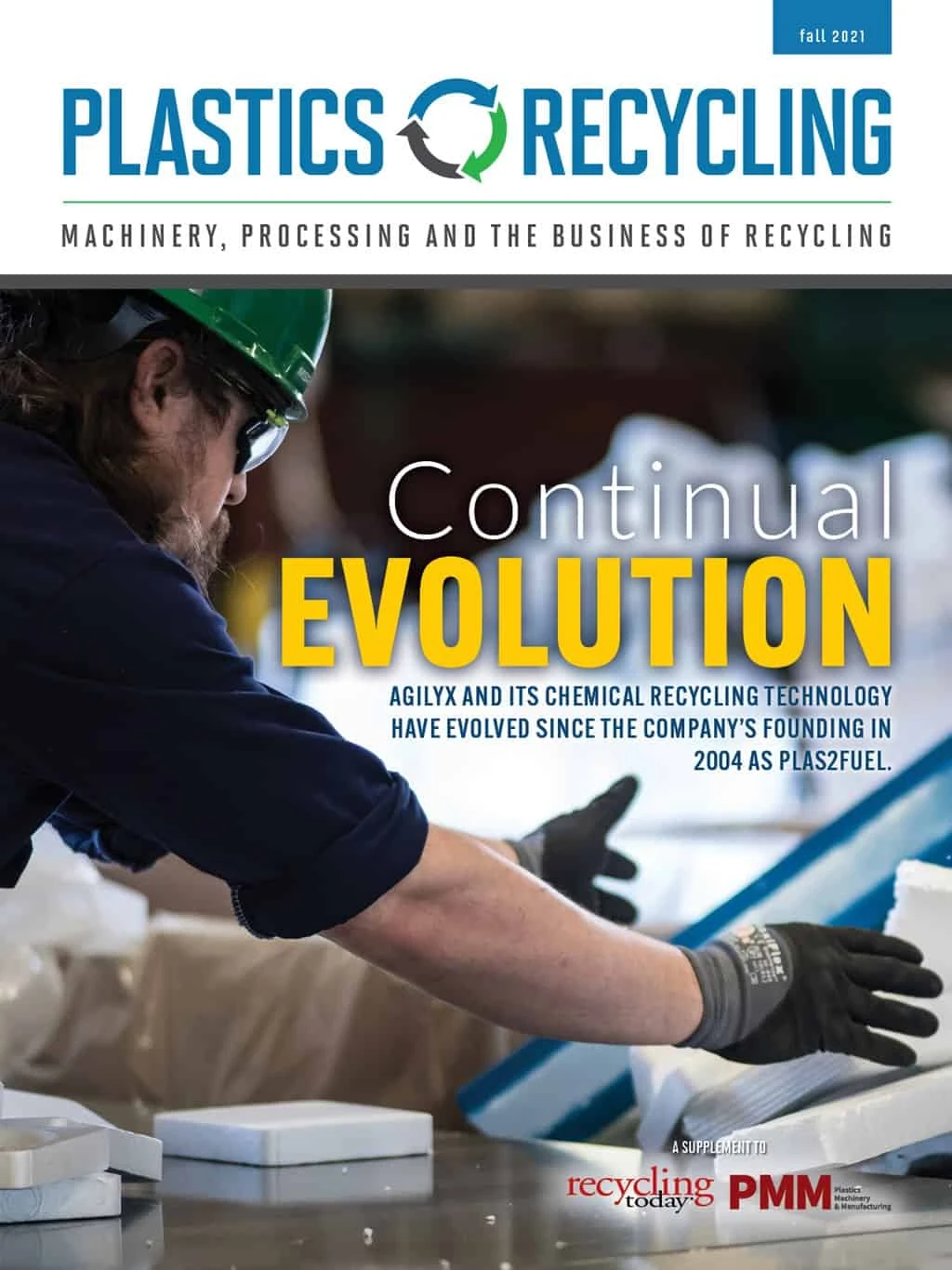
Explore the Fall 2021 Plastics Recycling Issue
Check out more from this issue and find your next story to read.
Latest from Recycling Today
- AF&PA report shows decrease in packaging paper shipments
- GreenMantra names new CEO
- Agilyx says Styrenyx technology reduces carbon footprint in styrene production
- SABIC’s Trucircle PE used for greenhouse roofing
- Hydro to add wire rod casthouse in Norway
- Hindalco to invest in copper, aluminum business in India
- Recycled steel price crosses $500 per ton threshold
- Smithers report looks at PCR plastic’s near-term prospects