
Mega Recycling and Compounding Services LLC, Romeoville, Illinois, is expanding its processing capabilities this year by adding three single-screw extruders to its 75,000-square-foot operation. Bret Garrison, the company’s president and founder, says this additional vertical integration is necessary to help Mega Recycling, which currently uses six toll processors for compounding and pelletizing its recycled resins, cut its costs.
“We plan to have them installed and fully operational by March 2019,” he says of the extruders.
The company’s plans also include the installation of twin-screw extruders before the end of 2019, which Mega Recycling intends to have operational by 2020, Garrison says.
By customer request
Mega Recycling is a relative newcomer to the plastics recycling sector, having been established in 2014. But the recycling firm’s sister company, Mega Polymers Inc., dates back to 2008, and Garrison has nearly 30 years of experience in the company’s specialties of distributing, brokering and compounding engineering-grade virgin thermoplastic resins. He worked for Bruck Plastics, also of Romeoville, a regional distributor and compounder of thermoplastic resins, and for RTP Co., Winona, Minnesota, a global compounder of custom engineered thermoplastics, before establishing Mega Polymers.
Garrison says Mega Recycling grew out of Mega Polymers’ desire to “be of service to a special customer of ours” that requested recycling services.
He continues, “That said, of course our goal was to make a profit by doing so.”
That customer was Accumold LLC, a microinjection molder based in Ankeny, Iowa.
Mega Polymers recycled roughly 16,000 pounds of plastic scrap for Accumold in 2013, its first year working with the company in this capacity. “We stuck with just Accumold for a good year before we tried it again with another company that kept material clean and free of contamination,” Garrison says. By the end of 2017, Mega Recycling recycled more than 230,000 pounds of plastics for Accumold, and its number of recycling contracts grew to more than 50.
“Mega’s philosophy has always been to listen carefully to our suppliers and our customers and, by doing so, find a way to faithfully serve the plastics industry,” he adds. “We have found that there is a need for reliable recycling partners wherever you go.”
Mega Polymers and Mega Recycling specialize in compounded engineering-grade thermoplastic molding resins. “We specialize in these because they serve a select niche within our industry and they also help support the much needed profit margins,” Garrison says. “They also bring unique value and service to our customer base.”
The companies’ compounding expertise includes custom colors, flame retardants, impact modifiers, electromagnetic interference / radio frequency interference shielding, wear-resistant compounds, electrostatic protection and conductivity elastomers.
Mega Recycling’s commonly handled resins include nylon, polybutylene terephthalate (PBT), acetal, polyphenylene sulfide (PPS), polycarbonate (PC), acrylonitrile butadiene styrene (ABS), polyetherimide (PEI), polyphenylene oxide (PPO), polyethylene (PE), polypropylene (PP) and high-impact polystyrene (HIPS).
PP accounts for the bulk of material it processes on a per-pound basis, with mixed-color regrind being its most popular product and black pellets coming in a distant second.
While PP is the leader in terms of volume, its tight margin and low price mean the resin accounts for only 20 percent of the recycler’s gross revenue, he explains.
“Engineering grades are the rainmakers for profitability,” Garrison adds, mentioning a number of name brand resins the company recycles.
Mega Polymers and Mega Recycling share a single facility in Romeoville and have 1.7 million pounds of resins in inventory as of early December 2018. “I would say that 70 percent of our inventory is recycled resin and 30 percent is prime virgin materials,” he says.

Further vertical integration
Mega Recycling’s operations include seven grinders: two from Zerma Machinery & Recycling Technology of Shanghai (a 100-horsepower and a 25-horsepower), two from Cumberland of New Berlin, Wisconsin, (a 100-horsepower and a 60-horsepower), two 60-horsepower grinders from a Chinese manufacturer and one 15-horsepower model from Rapid Granulator Inc., Leetsdale, Pennsylvania.
The company runs one 12-hour shift five days per week. Once the single-screw extruders are installed and operational, Garrison says Mega Recycling likely will expand its operating hours to three eight-hour shifts five days per week.
The single-screw extruders Mega Recycling is in the process of installing are ideal for compounding PP, he says, while the twin-screw extruders the company plans to add later this year are well-suited to processing nylon, which Garrison says is Mega’s No. 2 seller.
He says that while a distant second to PP in volume terms, nylon is responsible for a “very large percentage” of the company’s gross revenue because of its better margins. “It is one of my favorite engineering-grade polymers because of nylon’s cost-to-performance ratio. You get a lot of bang for your buck using nylon.”
While Garrison says Mega Recycling “has a lot to learn still from our recycling brothers and sisters,” he adds that he feels the company’s knowledge of compounding lends it advantages that some recyclers might not have.
“It’s one thing knowing the wide assortment of off-the-shelf products available today, it’s another to fully understand polymer technology,” he says. “Polymer technology combined with compounding expertise is a unique and valued language.”
Regarding the sister companies, Garrison says, “We are unique in that we can offer our diverse plastics industry such a wide assortment of products and services.”
"We go in and sit down with management and ask them how important the recycling program is. We always encourage them to do the right thing for the right reason." – Bret Garrison, president, Mega Recycling and Compounding Services LLC
Garrison says the companies take a consultative role with clients and help with product design and engineering. “Design engineers count on polymer engineers, like ourselves, to explain what their polymer choices are and to design a polymer solution that is still within their budget requirements.”
Mega Recycling’s customers are compounders, extruders and molders in the contiguous U.S., Mexico and Canada, he says.
Recycled resins might not always be a good fit for medical applications or some automotive applications because manufacturers require traceability, which can be difficult to provide. However, he says, Mega Recycling still serves these customers by buying and processing their plastic scrap.
Points of pain
During his recycling education, Garrison says he has learned that “quality and consistency are the most important elements of our reprocessed compounded products.” However, he adds, “It is not an easy business to produce consistent-quality products; but, with great care it can be done.”
Garrison continues, “Quality in produces quality out,” which is why ensuring suppliers are properly sorting material and monitoring for contamination are keys to Mega Recycling being able to produce quality recycled plastic compounds.
Mega Recycling’s staff inspects incoming scrap and offers training to its generating customers to ensure material cleanliness. “We go in and sit down with management and ask them how important the recycling program is,” he says. “We always encourage them to do the right thing for the right reason.”
Garrison says transportation costs have had a “tremendous impact on the recycling industry.” He adds, “The good old days of bringing in contracts from either coast are long gone, or so it seems today.”
He says logistics costs have increased 50 percent in the last year, noting that the company spent $1 million on transportation in 2018. This increase has reduced Mega Recycling’s operating radius. “We can’t go much longer than a 300-mile radius, or the logistics expense takes up all the profits,” Garrison says.
However, he sees one benefit to the more localized nature of the business: “We don’t have to compete with someone 1,000 miles away, either.”
Garrison says Mega Recycling is investigating adding in-house transportation services because the cost of freight is one of the top three things he thinks of daily along with quality and contamination. It’s a decision Mega likely will make in the first half of the year, he adds.
With the growth the company is experiencing, Garrison says “there is a good chance we will outgrow this building and have to get another building and perhaps dedicate it to our compounding services.”
He adds that the company’s Romeoville home should make finding a new building easy. “It’s the distribution headquarters for the universe,” Garrison says. “We have plenty of buildings to choose from here.”
Roughly three years remain on the current building lease. Garrison says he is looking for a 150,000-square-foot building for the next location. “We want to make sure we’re growing at the right rate. Staying under one roof would be more ideal.”
Get curated news on YOUR industry.
Enter your email to receive our newsletters.
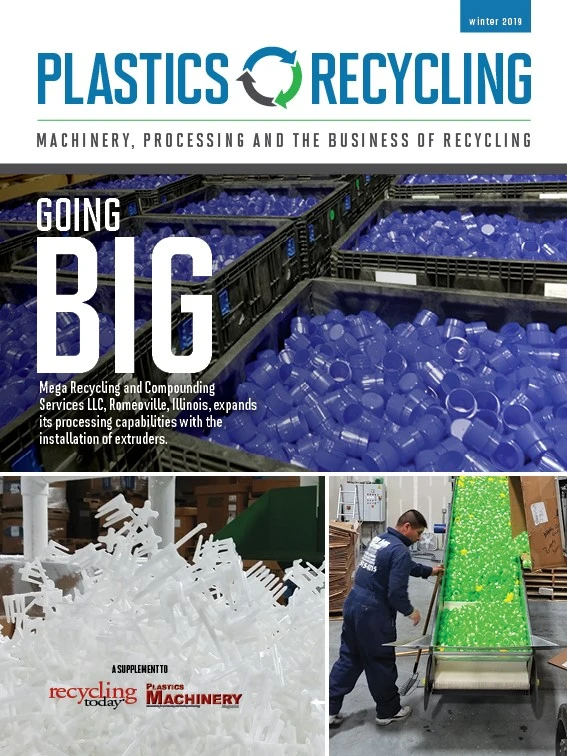
Explore the February 2019 Plastics Recycling Issue
Check out more from this issue and find your next story to read.
Latest from Recycling Today
- Toppoint Holdings expands chassis fleet
- Lego creates miniature tire recycling market
- Lux Research webinar examines chemical recycling timetables
- Plastics producer tracks pulse of wire recycling market
- Republic Services, Blue Polymers open Indianapolis recycling complex
- Altilium produces EV battery cells using recycled materials
- Brightmark enters subsidiaries of Indiana recycling facility into Chapter 11
- Freepoint Eco-Systems receives $50M loan for plastics recycling facility