
For hospitals across the United States, reducing waste management costs as well as how much material they send to landfills is becoming increasingly important. This is especially true for the plastics that are used just once in hospitals every day.
Yet, in hospital settings, doctors and nurses are there to save lives, and this singular focus can hinder any chance of recycling in operating rooms.
A program launched in 2012, Blue Renew, seeks to help make recycling in operating rooms accessible. Blue Renew was started by the former Kimberly-Clark Health Care, which is now run by Halyard Health, a medical technology manufacturer based in Alpharetta, Georgia. Formed in 2014, Halyard Health operates 14 global manufacturing facilities. The company’s step-by-step program assists medical facilities by training operating room teams to correctly collect clean “blue wrap,” connecting hospitals to recyclers and collectors that move the material downstream, baling, densifying and shredding the plastic, ultimately compounding it into a new resin.
Dan Constant, the president of Sustainable Solutions LLC, Gainesville, Georgia, and a consultant to Halyard Health’s Blue Renew program, says blue wrap is a common name for sterilization wrap that protects and contains surgical instruments. It is typically blue in color and made of No. 5 polypropylene (PP) plastic. Blue wrap makes up 5 percent of operating room waste daily, he adds.
Since its inception, Blue Renew has collected 5 million pounds of blue wrap from hospitals’ operating rooms, with about 400 U.S. hospitals participating in the recycling program today.
Health care plastics often are made of high-quality materials, a requirement for use in medical applications, and are designed for specific uses, writes Alison Bryant in the article “Health care plastics: untapped feedstock, untapped business opportunity” in the September 2017 issue of Recycling Today. Bryant is a consultant with and the corporate marketing manager for Antea Group, with U.S. headquarters in St. Paul, Minnesota.
“This results in very little variance in key characteristics, such as melt flow, viscosity and tensile strength, therefore enhancing the properties and value of resins and products manufactured in them,” Bryant writes. “These plastics are generated continuously with very little change in composition over time, meaning they are a reliable, high-quality stream coming from willing and eager providers. The result? A golden opportunity for recyclers with the insight to see the possibilities,” she continues.
Constant describes Blue Renew as an approach to the circular economy. “Our program takes blue wrap collection full circle, from collection to baling, shredding, densification and finally resin compounding into BlueCON resin,” he says.
Sustainable Solutions created the BlueCON resin, which is made from 80 percent operating room recycled plastic, and includes products such as bed pans, wash basins, distribution totes and recycling and garbage bins.
When operating room teams are finished with their blue wraps, they toss them into a bag. The bagged wraps are picked up by a service provider that already is visiting the hospital, from waste haulers to the company that delivers uniforms. This backhaul system keeps costs down and the materials moving, Constant says. “They’re going to the hospital anyway, so why not assist with the program?” he asks matter-of-factly.
Once off-site, the collection company then bales the wraps, typically using a 60-inch vertical baler, Constant says. The baled PP wrap is sold to recyclers, who use shredding equipment to take a 4-foot-by-5-foot wrap and shred it into pieces. Recyclers shred the material to make it small enough to fit into a densifier or extruder. The densifier melts it down to the size of popcorn, Constant says, which is a half-inch in diameter.
He adds that the “ultimate goal of recycled blue wrap plastic is to compound it back into a recycled resin.”
Once the material is shredded and densified, recyclers sell it to compounders that create resin pellets. “The company who is buying this material is using it solely for resin compounding, so the format, cleanliness and price is very important,” Constant says.
Money also is a factor when it comes to transporting the materials. Constant describes the light nature of loosely shipped materials, which is how nearly all loads of blue wrap leave hospitals. (He notes that space is almost always a concern at hospitals, limiting the opportunity for an on-site baler.) Ultimately, the goal is to get from point A to point B in the least number of steps, Constant says. By baling, shredding and densifying the wraps, recyclers can cut costs related to transportation and therefore increase their margins.
“As a recycler, you have to come up with ways to beat freight cost, and these costs can be thwarted by heavier loads and ready-to-use materials for your customer,” Constant says.
He adds, “There’s some companies I’ve worked with that have shredded blue wrap small enough that they go straight to the extruder. Saving money is the name of the game, and with all the great equipment out there, the possibilities are endless.”
As the Blue Renew program grows, Sustainable Solutions and Halyard Health are considering hospitals’ requests for more products made with the recycled resin, including lunch trays and urinals. Constant describes this as a “win-win” for all involved.
For more information: Halyard Health, 844-425-9273, www.halyardhealth.com Sustainable Solutions LLC, 855-478-7824, http://constantlygreen.net
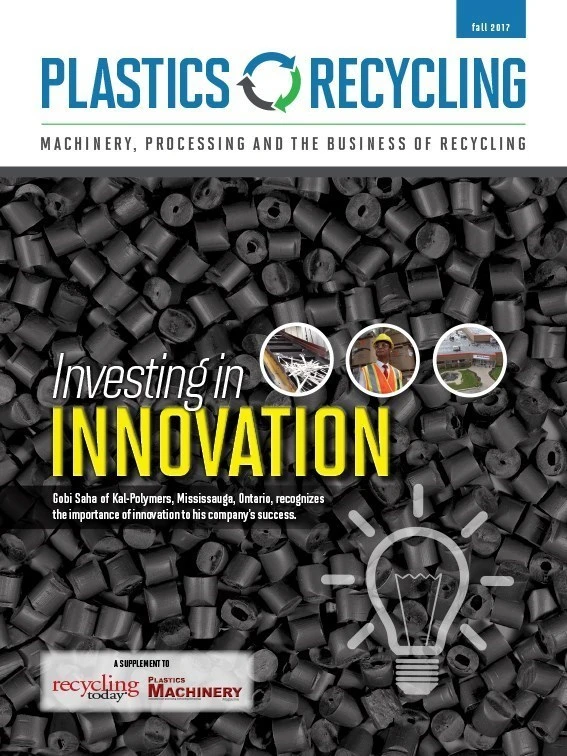
Explore the October 2017 Plastics Recycling Issue
Check out more from this issue and find your next story to read.
Latest from Recycling Today
- Two factors raise ferrous export questions in April
- Analyst: Scrap imbalance lost amid copper’s critical status
- AF&PA report shows decrease in packaging paper shipments
- GreenMantra names new CEO
- Agilyx says Styrenyx technology reduces carbon footprint in styrene production
- SABIC’s Trucircle PE used for greenhouse roofing
- Hydro to add wire rod casthouse in Norway
- Hindalco to invest in copper, aluminum business in India