Today, scrap recycling firms face unprecedented challenges, such as volatile markets, soaring operating costs, environmental issues and regulatory oversight, just for starters.
There’s increasing pressure from consumers, too. More and more, scrap consumers—in North America and elsewhere—expect their scrap recycling suppliers to become certified to some flavor of quality, environmental and/or health/safety standard. ISO, QS, TS, OHSAS, RIOS, Z10—the proliferation of initials seems endless.
To date, well more than 100 scrap recyclers have taken the plunge into the alphabet soup of certification. Others are in the process or are actively considering it. The rest hang back, feeling ill-informed, uncertain, confused. What to do? Which to choose?I’ll outline, in brief, the various quality, environmental and health/safety standards pertinent to scrap recycling businesses today, including key principles, purposes, credentials, experience, benefits and other issues.
WHY BUSINESS MANAGEMENT STANDARDS? Every organization exists to achieve an objective. The objective of an orchestra is to make music. The objective of a recycling firm is to convert scrap into commodities that consumers will pay for.
To achieve its objective, every organization follows a plan. An orchestra works off a score, and a scrap recycler follows a plan, too, consisting of many steps, from raw material acquisition through transportation, production, inspection and packaging; from sales contracts through delivery and acceptance.
Unlike the orchestra, the typical scrap recycler’s plan is neither formal, documented nor the result of an objective design process. Instead, it is often a hybrid of:
• A big helping of past practice ("This is how our parents and grandparents did it.");
• A dollop of observation ("Over at I & M, they do it this way."); and
• An occasional dash of bitter experience ("We’d better not ever do that again!").
Shape-shifting virtually moment to moment and taught with varying levels of competence by one generation of workers to the next, among the workforce the plan is often ill-understood, inconsistently followed and prone to abrupt rupture upon the exit of key people. This forces the scrap recycler to reacquire lost skills and relearn vital lessons at costs that are hidden, yet significant.
Such informality was tolerable when many, if not most, scrap recycling firms were relatively small, family owned and operated, with strong (not to say tyrannical) management, employees tenured for life, operating in homogeneous communities amid a slower-paced market. Today’s insightful scrap recyclers have perceived that this brave new century of international markets, speed-of-light change, workforce mobility and industry consolidation requires a better way of doing things. Today’s scrap recyclers regard themselves, rightfully, as professional business enterprises—manufacturers, no less—for which thoughtful process planning, disciplined execution and continual striving for excellence is no less important than rigorous financial management.
That’s where management standards and systems come in. More than simply credentials to hang on the wall, management systems based on ISO (International Organization for Standardization) 9001 (quality management), ISO 14001 (environmental management), OHSAS (Occupational Health and Safety Assessment Series) 18001 (safety management) and the others to be described here, help scrap recyclers operate their key processes according to defined plans, aimed at achieving specified goals, following best practices consistent with universal quality, environmental and safety management principles.
KEY PRINCIPLES. The first key management system principle is the process approach. ISO 9001, the fundamental management standard, requires mapping out a business as a network of inter-related processes that work together to add value and to achieve overall business objectives (the most important of which is to make money). Key among these are the "core processes" (the ones that lead directly to your getting paid). There are also "support processes" (i.e. payroll, training, maintenance) that do not add value, but are necessary to support the processes that do.
With the process approach, the recycler identifies these processes, designates responsibility and authority, sets objectives and determines the best methods for achieving them.
Defining the processes in this way is the first element of what’s called the "Plan-Do-Check-Act" (PDCA) model, around which today’s management standards are built. The first step is to plan the process. Next, do the process steps. The recycler then checks the outcome to see how the objectives were met. Finally, the recycler acts on the result, learning from the experience and adjusting the plan as needed. PDCA, when well implemented, helps the recycler avoid repeating mistakes and improve efficiency and results.
I’ll take a look at the various management standards available to scrap recyclers today, which include ISO 9001:2000, ISO 14001, OHSAS 18001, as well as the industry-specific Recycling Industry Operating Standard (RIOS, an integrated quality/environmental/safety standard) and ANSI/AIHA Z10-2005 (safety management standard from the American National Standards Institute).
ALPHABET SOUP. ISO 9001 and ISO 14001 are just two of the many thousands of voluntary standards sponsored by International Organization for Standardization. ISO, as it’s nicknamed, is made up of national standards groups representing 156 countries. (The U.S. ISO representative is ANSI [American National Standards Institute].) This makes ISO a truly worldwide standards writing authority.
Because of the care, deliberation and collaboration that go into these standards, ISO 9001 and ISO 14001 represent the best and most advanced thinking of an international consensus of experts and are generic. (ISO 9001 and ISO 14001 are easily applicable to scrap recycling firms as well as to any other organization producing products or services for customers anywhere.
Termed a quality management standard, ISO 9001 is actually a business management standard. It addresses the processes the scrap recycler operates in order to meet customer requirements and to achieve customer satisfaction. ISO 9001, being a generic standard, is easily adaptable to any organization.
ISO 14001 is the environmental management standard. It requires the recycler to identify the ways its operations impact air, water and land; control those impacts; demonstrate compliance with laws and regulations; and improve its ability to minimize and/or prevent pollution. ISO 14001, being generic as well, is easily adaptable.
OHSAS 1800 is aimed at the management of health and safety. It is not a standard the way ISO 9001 and ISO 14001 are. OHSAS 18001 is an assessment series published by the U.K.-based BSI Group. Though internationally accepted, OHSAS 18001, is not, properly speaking, a standard, but rather a "specification."
OHSAS 18001 requires the scrap recycler to control health/safety risks and hazards associated with its operations and demonstrate improvement by minimizing and/or eliminating illness and injury.
All three of these standards—ISO 9001, ISO 14001 and OHSAS 18001—follow PDCA, have many common elements and are parallel in structure. The recycler that wishes to manage the quality, environmental and safety aspects of its operation can therefore implement an integrated management system, streamlined and without redundancy, and become simultaneously certified to ISO 9001, ISO 14001 and OHSAS 18001.
To date, at least two U. S. scrap recycling companies, Miller Compressing Co. of Milwaukee and Wilmington Iron & Metal Co. of Wilmington, Ohio, have implemented and certified integrated 9001, 14001 and 18001 systems. They implemented one single system, underwent one certification audit and earned all three internationally recognized certificates.
Marketed by the Institute of Scrap Recycling Industries Inc. (ISRI), "Recycling Industry Operating Standard" (RIOS)—formerly Scrap3—is a quality, environmental and health/safety (QEH&S) specification designed for scrap recyclers. According to ISRI, RIOS "is intended to help yards to achieve measurable continual improvement in QEH&S performance."
RIOS is a fee-based membership program. To obtain the RIOS specification itself and access to guidance materials for implementing the system, members pay an initiation fee. ISRI members pay $2,000 per yard, capped at $20,000. Members also pay an annual maintenance fee of $975 per year per yard, capped at $20,000. These fees do not include any necessary consulting or certification costs. Nonmembers pay substantially more.
According to ISRI, the American National Accreditation Board (ANAB) plans to accredit RIOS as an industry-specific standard. At that time, recyclers would be able to obtain certification to RIOS. This is not, however, the same as ISO certification. A detailed comparison of the RIOS specification to the ISO/OHSAS standards shows some 115 pertinent ISO/OHSAS requirements that RIOS does not address in areas such as purchasing, nonconforming product handling, product identification and calibration. Thus, a system fully compliant with the RIOS specification would not necessarily pass an ISO or OHSAS audit.
Z10 (ANSI/AIHA Z10B2005) is a fairly recent health/safety management standard sponsored by American Industrial Hygiene Association and approved as an American National Standard by ANSI. It was developed under AIHA’s sponsorship by a committee of interests including the American Foundry Society, the American Society of Safety Engineers, OSHA (Occupational Safety and Health Administration), NIOSH (National Institute for Occupational Safety and Health) and the National Safety Council.
Like the other standards and specifications discussed here, Z10 is built around the Plan-Do-Check-Act model. It closely mirrors OHSAS 18001 in many respects and addresses most of the same safety management issues as RIOS. Z10 is, however, more prescriptive than OHSAS (and RIOS) in several key ways. Z10 is generally stronger and more specific in the area of employee responsibility and participation. It is more prescriptive with respect to management of change. And it is much stricter than OHSAS or RIOS in its ranking of responses to health/safety hazards and risks.
ANAB and several U.S. certification bodies offers Z10 accreditation. However, Z10’s reach apparently extends only to U.S. borders at this time; none of the overseas accreditation or certification bodies queried for this article recognize Z10 today.
THE CONSIDERATIONS. In deciding which direction to go, the scrap recycler has the following options:
• One or more of ISO 9001, ISO 14001 or OHSAS 18001;
• Integrated ISO 9001/14001 and OHSAS 18001;
• Z10 (if all you want to do is safety); and/or
• RIOS.
ISO and OHSAS have been around for many years; RIOS is in its early years. This creates a dilemma. Until the program has more extensive field experience and objective evidence, it is difficult to verify some claims made for RIOS, i.e., that it costs less than ISO.
RIOS’s integrated approach for integrated quality/environmental/safety management systems is available via other options that exist that are fully ISO compliant, whereas with RIOS that is not necessarily the case.
And that in itself raises a larger issue. A key reason many scrap recyclers obtain some sort of management system certification is in response to a requirement of one or more major consumers. These consumers, driven in turn by the demands of their major customers in the automotive, defense, aerospace and other industries, require ISO and nothing but ISO, which has unmatched recognition around the world. Whether these consumers will accept RIOS certification in lieu of ISO and any incompatibility between RIOS and ISO/OHSAS must be determined at the outset.
Bottom line: The scrap recycler trying to decide between ISO/OHSAS or RIOS may wish to consider consumer acceptance, name recognition and international credibility when deciding whether ISO/OHSAS or RIOS offers the best return on what can unquestionably be a significant investment of resources.
Similarly, Z10, while an approved American national standard and, arguably, stricter in key ways than OHSAS or RIOS, has yet to become widely recognized overseas.
Scrap recyclers may wish to apply Z10 principles to their safety management processes, certifying to OHSAS 18001 until Z10 achieves equivalent stature worldwide.
ISO BENEFITS. When the 125 or so scrap recyclers that have gone the ISO or OHSAS route are asked about the benefits, their answers likely will fall into two major categories: external and internal.
External benefits include:
• Achievement and improvement of customer satisfaction;
• Positive image among customers and consumers;
• Increasingly, ISO certification is a factor in penetrating overseas markets (ISO 14001 certification is an advantage when seeking licenses to do business in places like India and China.); and
• Keeps the organization prepared for external audits and inspections.
Internal benefits include:
• Cost savings resulting in part from the transformation from detection mode to prevention mode—fewer material rejections or downgrades; less release of pollutants to air, water and land; and lower injury rates in light of disciplined mitigation and/or elimination of hazards;
• Disciplined and consistent training for all employees on key tasks, reducing errors, rework and remediation, and reductions in repeat errors through effective corrective action and problem solving;
• Lessens dependency on key individuals through greater distribution of responsibility for quality/environmental/safety management; increase in accountability through monitoring tools such as internal audits; improved communication.
• Provides a blueprint for controlled, disciplined growth, especially when many scrap yards are transitioning from family/entrepreneur mode to corporate mode, an ISO management system helps organize the business, systematize practices and ensure management accountability as the organization expands; and
• Strengthens regulatory compliance through improved awareness of applicable laws/regulations and airtight control of important schedules, filings, records, etc.
BOTTOM LINE. Embarking on management system implementation, be it ISO, RIOS or another, should not be undertaken lightly. To be done correctly and to achieve all the benefits, it requires time, patience, resources, persistence and, above all, ongoing top management commitment. Without these, the result is a paperwork collection and a certificate on the wall. With these, the outcome can, in time, be more robust systems, an improved competitive position and increased profits.
Rob Kantner, president of Kantner & Co. Inc. of Blanchard, Mich., has authored several books on ISO and related management systems. He can be contacted through www.ScrapLeaders.com.
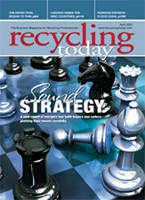
Explore the April 2007 Issue
Check out more from this issue and find your next story to read.
Latest from Recycling Today
- ReMA board to consider changes to residential dual-, single-stream MRF specifications
- Trump’s ‘liberation day’ results in retaliatory tariffs
- Commentary: Waste, CPG industries must lean into data to make sustainable packaging a reality
- DPI acquires Concept Plastics Co.
- Stadler develops second Republic Services Polymer Center
- Japanese scrap can feed its EAF sector, study finds
- IRG cancels plans for Pennsylvania PRF
- WIH Resource Group celebrates 20th anniversary