
In the residential Chicagoland suburb of Palatine, Illinois, a business has grown substantially in recent years but has managed to keep its high-volume recycling operation largely out of sight. The street out front is clean and quiet, yet inside the walls of MBL Recycling’s facility lies a state-of-the-art construction and demolition (C&D) recycling center.
In 2005, MBL owner Rob Lenzini and his family saw a need for a recycling facility that would serve the northern suburbs of Chicago. As in almost all areas of the country, especially urban areas, landfills were being closed or facing dumping restrictions.
The main problem with recycling C&D debris is coming up with an economical and safe means to separate the materials so they can be sent to other facilities for processing as secondary products or for use as raw materials to make plastics and metals. However, over the last 20 years, significant progress has been made to develop sophisticated systems to sort like materials into their respective categories. Most facilities still use some manual labor for sorting, though robotic solutions are on the horizon to take over at least some of these tasks. MBL is no exception and has invested heavily to create a state-of-the-art operation.
Traditionally, diesel-powered hydraulic excavators equipped with either a bucket or thumb combination or a grapple attachment have been used to help sort, compact and load this material into feed hoppers. But operators in these challenging and dusty enclosed environments find that diesel machines tend to overheat because of frequent clogging of their air filters. These machines also require an added level of maintenance to ensure their performance. Typically, these excavators have their engine lives shortened significantly in this environment. Beyond maintenance considerations, running diesel engines in an enclosed facility poses its own set of health risks because of the exhaust fumes.
Builtrite Manufacturing saw an opportunity to provide a real solution to the industry. Builtrite has been designing and building stationary electric material handlers since the company’s founder saw a need for these machines while working in transfer stations in the 1980s.
As the world started seeking “greener” solutions that help reduce fossil fuel emissions, other industries have sought out Builtrite equipment for handling C&D debris, scrap metal and logs. The handlers have come to be used in these and other high-volume production processes.

The key advantage of a stationary electric machine versus a diesel unit is that the electric power unit can be separated from the machine and removed from the dusty environment. Because electric motors do not require air for combustion as diesel motors do, there are no air filters to replace. Also, because no harmful emissions are produced, they can be used safely indoors. Finally, because electric material handlers are bolted to the floor, no tires or tracks need to be replaced, and those expensive reinforced concrete floors last much longer. Overall, running an electric material handler—as opposed to a diesel machine—typically cuts operational costs in half and reduces maintenance costs even more.
Lenzini, recognizing the advantages of the stationary electric handler, decided to contact Builtrite about procuring one for MBL’s facility. After touring MBL’s MRF and evaluating what Lenzini needed to accomplish, the Builtrite team went to work.
The Builtrite team and Lenzini concluded that Builtrite’s model 2300-SE had the proper amount of reach and lift capacity and was the right tool for the job. However, Lenzini wanted some specialized components, including a custom boom and the ability to use a fixed-style demolition grapple. To fulfill Lenzini’s needs, the Builtrite team collected information from MBL and then made a drawing proposal, customized for the specific facility needs. After feedback from the MBL team, Builtrite made several changes, and the green light was given to produce the machine.
“What I liked best about dealing with Builtrite was their willingness to listen to my specific application needs and suggestions on what it would take to produce a machine that would work well at my facility,” Lenzini says. “We decided to have the power unit moved off the machine and placed on the other side of our sorting hopper, keeping it away from most of the dust. We also incorporated an autolube system to reduce wear, maintenance and downtime and installed stairway access to the cab. I also wanted a machine made in the U.S. Builtrite was the solution that checked all the boxes.”
While MBL Recycling was recently purchased by Economy Disposal, the site’s Builtrite material handler promises to be a fixture of Economy’s recycling operations for years to come.
When asked about the acquisition and Builtrite’s contribution to the MBL facility, Economy Disposal President Ron Tazelaar said, “Rob is still with us, and we’re really pleased he chose to purchase the Builtrite 2300 SE! It’s right here with us as we grow this business.”

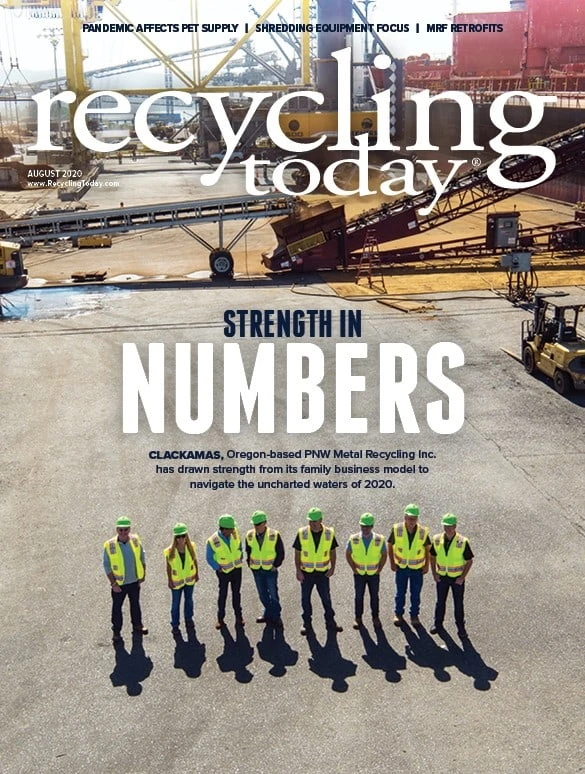
Explore the August 2020 Issue
Check out more from this issue and find your next story to read.
Latest from Recycling Today
- Cyclic Materials to build rare earth recycling facility in Mesa, Arizona
- Ecobat’s Seculene product earns recognition for flame-retardant properties
- IWS' newest MRF is part of its broader strategy to modernize waste management infrastructure
- PCA reports profitable Q1
- British Steel mill subject of UK government intervention
- NRC seeks speakers for October event
- LME identifies Hong Kong warehouses
- Greenville, Mississippi, launches aluminum can recycling program