
From smartphones and skyscrapers to airplanes and autos, aluminum is all around us. Globally, demand for lightweight, strong and infinitely recyclable aluminum is growing fast. Aluminum offers manufacturers and designers in all sectors a wide range of options for product modernization.
Moreover, as concerns about climate change are addressed in every industrialized region of the world, aluminum’s inherent sustainability advantages play a vital role in helping to decrease life cycle carbon emissions.
The numbers confirm recognition of aluminum’s overall value to modern society. The domestic aluminum industry ships nearly 26 billion pounds of aluminum annually, up more than 36 percent since 2009. While growth across all industries is on the rise, automotive represents the most important growth market. Demand in the building and construction sector grew nearly 19 percent since 2009, while the transportation market grew an unprecedented 95 percent during that same time. An unmistakable materials evolution is under way in the automotive industry, and it is happening even faster than many predicted.
UNINTERRUPTED GROWTH
Aluminum is already the second-most-used material in new car and truck construction. Engines, wheels, bumpers, hoods and trunk lids led growth in past years. Today, however, automotive aluminum use is accelerating at a record pace as a material of choice for the body structures of some of the most innovative vehicles currently available. With no signs of slowing, aluminum is poised for 50 years of uninterrupted growth.
Several reports, including those from Ducker Worldwide and WardsAuto, signal intentions of automotive engineers and designers to increase their use of aluminum as the preferred material to help meet 2025 fuel economy and greenhouse gas emissions (GHG) standards. Within the next decade, it is expected that every automaker will have more than one aluminum-intensive vehicle within its fleet.
Aluminum can absorb twice the crash energy of steel in an accident. – The Aluminum Association
“Aluminum is well-positioned to help move the nation’s freight more efficiently and effectively by providing lightweight solutions in a variety of applications across the heavy- and medium-duty truck markets,” says Heidi Brock, president and CEO of the Aluminum Association, Arlington, Virginia.
Brock’s comments stem from a February 2016 study by Trucking Efficiency—an initiative established by the North American Council for Freight Efficiency (NACFE) and the Carbon War Room (CWR) that aims to double the efficiency of the North American trucking fleet by eliminating barriers to information, demand and supply—that reports commercial truck fleets looking to increase fuel efficiency, haul more freight and retain more drivers can rely on lightweighting as a key enabler. The study found that substituting the nation’s fleet of Class 8 tractor-trailers with aluminum-intensive models would save 9.3 million tons of carbon dioxide annually. (Read more in the sidebar, “Looking into Lightweighting,” at right.)
INFINITE POSSIBILITIES
No other material offers automakers the versatility and environmental benefits of aluminum, which is a key factor of the material’s rapid adoption. Several statistics from the Aluminum Association convey its usefulness:
- aluminum is infinitely recyclable;
- nearly 75 percent of all aluminum produced since 1886 is still in use today; and
- recycling aluminum requires 95 percent less energy and produces 95 percent fewer GHG than manufacturing primary aluminum.
Once produced, aluminum can be recycled repeatedly without any degradation while maintaining significant economic value. As a result, automakers can tap an endlessly renewable supply of aluminum by embracing closed-loop recycling, as Ford and Jaguar Land Rover successfully demonstrate. (Atlanta-based aluminum rolling and recycling company Novelis has closed-loop recycling agreements with a number of its automotive customers, including Ford and Jaguar Land Rover, ensuring manufacturing scrap is recycled.)
Recycled aluminum not only helps automakers improve the sustainability of their operations and their products over the long term but also provides supply chain security. For these reasons, the recycling rate for automotive aluminum is in excess of 91 percent in North America, according to a 2016 report from the Worchester Polytechnic Institute’s Center for Resource Recovery and Recycling. The study uses a “grave-to-gate” material flow analysis approach to determine the end-of-life vehicle (ELV) recycling rate of automotive aluminum and its alloys. Grave-to-gate spans the moment an automobile becomes obsolete to the moment the aluminum metal units are recycled and enter back into life as input material for a new application, to include automotive.
Three operations contribute to total aluminum metal recovery after an automobile reaches its end of life: dismantling, shredding and downstream separation.
In a January 2016 study, “Automotive Aluminum Recycling Rate for the USA,” conducted by the Center for Resource Recovery and Recycling and the Metal Processing Institute at Worcester Polytechnic Institute, process-specific surveys were distributed to facilities to investigate the percentage of aluminum metal recovered and material flow proportions into and out of each respective operation. The study assumes that dismantling is preceded with the most valuable and reusable parts, such as catalytic converters, wheels, bumpers, engines, transmissions, extracted and distributed to the appropriate consumers (i.e., battery recyclers, scrap dealers, retail part sales, etc.).
Once dismantled, the ELV is flattened into hulk form and delivered to an auto shredder where, dependent upon market value, it may be mixed with scrap metal from other industrial sectors, including consumer durables and construction.
Aluminum in automobiles saves 44 million tons of carbon dioxide emissions as compared with today’s steel cars. – The Aluminum Association
Finally, downstream separation systems operations use a dry and/or wet automated sorting technology to upgrade scrap in value and by product specification. Shredded automotive scrap can be sorted based on color, weight, magnetic property, electrical conductivity, density and chemical composition. Downstream separation systems incorporate appropriate technologies that target metallic constituents that fit their process-specific business models. Following downstream separation, the recovery is completed.
Secondary aluminum recycling facilities convert recovered aluminum-containing scrap, old or new, into a fully recycled, reusable product. These products are either in the semifabricated mill product form (i.e., extrusion billet, ingot, sow, etc.) or in the final consumer-ready form as castings, extrusions or sheets for further shaping and inspection. The feedstock to these plants is pretreated through a cleaning process involving heat or chemical treatment to reduce contamination resulting from impurities, such as carbon from polymers, paints and lacquers.
DRIVING SUSTAINABILITY
Beyond recycling, the aluminum industry is constantly innovating to reduce its environmental footprint further. Aluminum is more sustainable today than at any time in history. The expanded use of hydroelectric power sources for aluminum production, which has risen from 63 percent in 1995 to more than 80 percent today, contributes to a nearly 40 percent reduction in carbon emissions for North American primary production, according to a peer-reviewed life cycle assessment (LCA) released in 2013 by the Aluminum Association.
Moreover, a 2014 LCA conducted by Oak Ridge National Laboratory, based in Tennessee, found “in the areas of cumulative energy demand, potential ozone depletion and other likely factors in climate change, aluminum rises to the top as the best choice for the environment.”
Looking ahead, aluminum producers will continue to increase the material’s sustainability value proposition during every stage of an automobile’s life. As the United States and the rest of the world strive for a more fuel-efficient and lower carbon dioxide future, aluminum is a big part of the solution.
Get curated news on YOUR industry.
Enter your email to receive our newsletters.
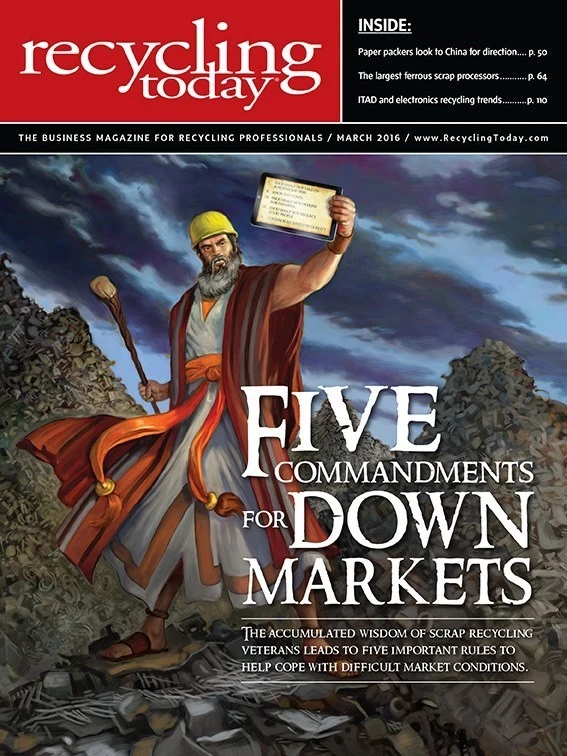
Explore the March 2016 Issue
Check out more from this issue and find your next story to read.
Latest from Recycling Today
- Nucor expects slimmer profits in early 2025
- CP Group announces new senior vice president
- APR publishes Design Guide in French
- AmSty recorded first sales of PolyRenew Styrene in 2024
- PRE says EU’s plastic recycling industry at a breaking point
- Call2Recycle Canada, Staples Professional expand partnership
- Circular Services breaks ground on north Texas MRF
- Tariff uncertainty results in choppy nonferrous scrap flows