On Dec. 19, 2007, former President Bush signed the Energy Independence and Security Act into law, effectively increasing the Corporate Average Fuel Economy (CAFE) standards for passenger cars from the current figure of 27.5 miles per gallon to 35 mpg by the year 2020. Beginning in 2011, the CAFE standards will begin gradually increasing to remain on pace for the 2020 target figure.
The new standards are the latest factor encouraging automobile manufacturers to find ways to increase fuel efficiency. The most popular way of doing so seems to be eliminating unnecessary weight from vehicles, as automakers are turning to lightweight steel, aluminum and plastic to replace the traditionally heavier steel previously used in the manufacturing process. Not surprisingly, automobile recyclers are paying close attention to these trends and evaluating how the shift in material will affect their future downstream operations and ultimately their bottom lines.
MANUFACTURING TRENDS
Ten years ago steel accounted for 65 percent to 66 percent of the weight of the average automobile, while today’s figures have dipped to 60 percent to 61 percent, according to Bill Heenan, president of the Steel Recycling Institute, based in Pittsburgh. He attributes the weight reduction to the replacement of traditional steel with high-strength, low-weight steel.
However, some of that decrease must be attributed to the rise in the use of aluminum and plastics to lighten the weight of vehicles. Mazda USA reports that the amount of plastic used in automobiles has increased by about 15 percent in the last 10 years. Meanwhile, within the last 10 years, aluminum has surpassed iron as the second most abundant material in automobiles and now accounts for 8.7 percent of the weight of the average vehicle and is expected to reach 10 percent by 2020, according to Buddy Stemple, chairman of the Auto & Light Truck Group for the Aluminum Association, Arlington, Va.
The shift in the composition of automobiles has not gone unnoticed by automobile recyclers. Auto recyclers have relied on eddy currents for years to separate nonferrous metals downstream of the shredder. Recently, however, many yards have added more eddy currents, air separation equipment and more sophisticated nonferrous separation equipment in response to the increasing prevalence of aluminum in vehicles.
"We now have seven eddy currents and eight air separators in response to the added throughput we are experiencing from the increasing aluminum content in vehicles," says Adam Weitsman, president of Upstate Shredding in Owego, N.Y.
Plastic separation technology in auto shredder downstream systems is a more recent phenomenon and has made great strides recently, according to sources.
"All of a sudden, more shredders started recovering plastics over the last few years because the value of plastic as a recovered material has matured and gone up dramatically," says Trip Allen, president of Energy Anew Inc. and co-founder of MBA Polymers Inc., Richmond, Calif.
Use of plastic separation technology is beginning to take hold in the auto shredding industry but is still expensive to install. Weitsman says Upstate Shredding is one of a few shredders planning to add plastic separation equipment within the next year and also would like to incorporate glass separation, though technology has not yet advanced enough to do so.
At this time, it appears auto recyclers are successfully responding to the current trends in automobile manufacturing. However to stay ahead of the curve, they may benefit by forecasting how their downstream systems will be affected in the future by the changing composition of automobiles.
MATERIAL APPLICATIONS
During the past 10 years, vehicle components that have transitioned from steel or iron to aluminum include front and rear suspension parts, heat exchangers, doors, hoods, trunk lids and fenders, according to Stemple. He adds that aluminum is better suited than high-strength steel for applications that call for rigidity rather than strength.
"Our research shows that about 10 percent of the parts of the car benefit from strength," says Stemple. "Obviously high-strength steels are ideal for that. "The rest of the car benefits from other things like stiffness, which high-strength steel doesn’t offer much of."
Heenan begs to differ. He argues that while the application of aluminum in vehicle manufacturing can lead to weight savings and increased fuel economy, the costs of widely transitioning from steel to aluminum would be too costly for manufacturers. He acknowledges that there are specific applications where the use of aluminum can make sense, such as engine blocks, but he says he believes it will not replace steel in the majority of applications any time soon.
He offers this example: The average weight of a car hood made from traditional steel is 39.5 pounds. Transitioning to high-strength steels can reduce the average weight to 32.3 pounds, while using aluminum can reduce the weight to 24.2 pounds. However, substituting high-strength steel for traditional steel will reduce the manufacturers’ cost by $2 per hood. In contrast, substituting aluminum for the traditional steel will increase the manufacturers’ cost by $48 per hood, according to Heenan.
"Knowing these figures, is the auto industry going to choose to use aluminum to reduce mass, increasing gas mileage?" Heenan asks. "Probably not, because it doesn’t make economic sense to do so," he says.
He points to the Audi R8, the first series vehicle with an all-aluminum body, as an example of why aluminum is not likely to displace steel in most vehicle applications any time soon in light of its sharply higher cost. The Audi R8 sells new for more than $100,000, according to Audi’s Web site.
While high-strength steels and aluminum are often competing in similar applications, one function neither is best-suited for is interior absorption systems. That distinction belongs to plastic.
"Safety was one of the really powerful draws to plastics," says Allen. "Plastics had the capability to make interiors of cars safer and created the possibility to have vehicles that saved a lot of lives."
Aside from safety, plastic became widespread in automotive applications because of its functionality and ability to be molded into a variety of shapes and sizes, says Allen. The most common applications increasing the use of plastics within the last decade include air intakes, gas tanks, airbags, side airbags and knee and head impact counter measures. Plastics also have been displacing steel in some applications where concerns for strength are semi-structural, including front-end modules, underbody shields and load floors, most commonly in the trunk compartment, says Jim Kolb, senior director of the Automotive Group for the Plastics Division of American Chemistry, Arlington, Va.
One point the experts agree on is that auto manufacturers are reducing the use of traditional steel in favor of high-strength steel, aluminum and plastic to lighten the weight of vehicles in an effort to meet the new CAFE standards. However, the potential use of these materials in future vehicles is somewhat cloudy because of the emergence of new power trains and the impact they will have on the manufacturing process.
ALTERNATIVE POWER TRAINS
While the days of the internal-combustion engine are far from behind us, most auto manufacturers have started designing vehicles with hybrid or electric power trains. These automobiles decrease the carbon emissions during their useful lives by relying on electric energy stored in batteries and on other sources of energy to decrease fossil fuel consumption.
As vehicles with hybrid or electric power trains become more mainstream, it is difficult to predict which materials will benefit in the manufacturing process. Two schools of thought seem to exist. Proponents of aluminum and plastic insist that lightweighting the vehicle will become more important to maintain the amount of power consumers are used to. On the contrary, steel supporters say lightweighting the vehicle will decrease in importance because reduced energy consumption during its useful life will shift the focus to energy consumption during production and recycling.
Allen, Kolb and Stemple agree that as hybrid and electric power trains replace the internal combustion engine, lightweighting of vehicles will increase in importance. Stemple indicates that it is much easier to generate power from a combustion engine than it is with an electric motor. Considering the less-powerful engine, without lightweighting the vehicle, drivers will suffer a decline in performance, adds Allen.
"Acceleration has always been a function of mass vs. power. When people want fuel-efficient vehicles, they don’t want to have to sacrifice power," Allen says. "They want both, and you can’t get both without lightweighting the vehicle," he adds.
In response to maintaining power while achieving better fuel efficiency, lightweighting the vehicle would seem to most benefit aluminum and plastic. Stemple says he believes aluminum will realize further benefits in the body and structural applications because the new power trains are heavier than those in vehicles powered by internal-combustion engines.
"All of the new power trains, be they electric or hybrid, all add weight to the car, and weight is the enemy," Stemple says. "Manufacturers will need to continue to lightweight the structure."
Plastic may also experience additional utility with the transition to hybrid and electrically powered automobiles.
"The issue with hybrid drive trains and some of the newer drive train technologies is they’re altering where the weight is on a vehicle, which is creating new challenges in protecting passengers," says Allen. "A great way to meet those challenges is to have a very functional and simple tool like plastics to increase your design options."
While Allen, Stemple and Kolb are adamant that lightweighting vehicles will be a primary concern of automakers as they transition to alternative power trains, Heenan disagrees. He says he believes that the decreased carbon emissions during a vehicle’s useful life will shift the environmental emphasis to the production and disposition phases of the automobile’s life cycle, which will benefit steel.
"There will be more emphasis on original manufacturing and end-of-life recyclability and not so much on how lower overall mass will benefit the environment through the reduction of carbon emissions," says Heenan.
While aluminum, plastic and high-strength steel can each make a case for increased utility in response to the transition to alternative power trains, each has downfalls. Plastic suffers from low heat resistance and strength, in addition to its inability to be as easily mass produced as metals, according to Mazda. The cost premium of aluminum compared to steel may stall additional aluminum growth, according to Kia Motors Corp. Finally, high-strength steel is at a disadvantage because there are lighter alternatives that may help automakers save energy and/or power, according to these automakers.
It seems there are advantages and disadvantages for each material in regard to increasing use in hybrids and electrically powered vehicles. Time will tell which materials manufacturers turn to in the production of vehicles with alternative power trains, but it is apparent that change is on the horizon.
READYING THE DOWNSTREAM
It appears the future use of high-strength steel, plastic and aluminum in hybrids and electric automobiles is still a gray area. Most likely these components will continue to work together in vehicles to ensure efficiency, safety and power. Perhaps of equal importance to recyclers as the proportion of materials going into each vehicle is that equipment is now available to aid shredder operators in recovering that material downstream of the shredder.
Auto recyclers seem confident that with the increase in plastic separation technology, their downstreams can accommodate the material in automobiles, no matter what trends emerge.
"I think with the advancements in separation technology, even with the transition from heavier steels to high-strength steel, aluminum and plastic, our operation has the capabilities to adjust to the market, whatever it may be," says Weitsman.
Adjusting their downstream systems to enable the separation of materials beyond ferrous and nonferrous metals may also increase profits for auto recyclers.
"I believe shredders are going to recognize that they’ve been letting a lot of valuable materials go to landfills in the form of shredder residue," says Kolb.
Lacy also points out that as electric cars become more mainstream, there may be a huge demand for the end-of-life batteries that power them.
"The profit from sending those batteries to battery recyclers after disassembly is going to be large, because there is no aftermarket for it yet," Lacy says. "It will be the only place to get them."
As separation technology becomes more mainstream for plastics, Allen says it will become easier to recover other materials in the downstream, in addition to aluminum and plastic.
"What we’re going to see is a progression in the industry. Now that plastics are becoming common in the recycling infrastructure, we’re going to get more and more recovery of the last fractions of shredder residue," says Allen, adding that he envisions a future where everything that goes into an automobile can be recycled.
Kolb is quick to point out, however, that a future where all materials in automobiles can be recycled reaches beyond technology.
"The real trick is not only that we have the technology to do it, but for it to be economically sustainable," Kolb says. "It is not going to become a reality unless people can make a business case for it. And that means making some money from it."
The author is an intern with Recycling Today.
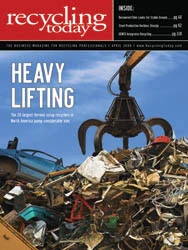
Explore the April 2009 Issue
Check out more from this issue and find your next story to read.
Latest from Recycling Today
- Aqua Metals secures $1.5M loan, reports operational strides
- AF&PA urges veto of NY bill
- Aluminum Association includes recycling among 2025 policy priorities
- AISI applauds waterways spending bill
- Lux Research questions hydrogen’s transportation role
- Sonoco selling thermoformed, flexible packaging business to Toppan for $1.8B
- ReMA offers Superfund informational reports
- Hyster-Yale commits to US production