Forklifts make it possible to move and relocate skids and pallets stacked with any kind of heavy material imaginable. They can lift, load, raise, lower and move nearly any item you just can’t get your arms around, let alone get off the ground. Add an attachment and the possibilities are even greater.
Imagine moving a pallet’s worth of materials one-light-enough-to-lift-item at a time and you begin to get an idea of how invaluable forklifts can be for material handlers. Superhero show-offs aside, if you manage a recycling or scrap facility, there’s a good chance you could use a forklift.
WHAT DO YOU THINK YOU ARE MADE OF?
What material is best for moving material? In the case of forklifts, especially those with exterior use, the answer is often steel. Its durability means longer life for the machine and less chance of damage in a scrap yard where weather and mechanism-threatening scrap can be a factor.
Steel is most often the material of which a forklift’s frame and chassis is made. And in the case of exterior-use forklifts, it is a good idea to have a steel plate that protects the underside of the machine from possible damage done by driving over sharp scrap or rocky terrain. It’s also important to closely examine the different forms of power available to run a forklift before making a purchase for your facility. Electrically run forklifts used to be for smaller indoor jobs but new designs have increased weight capacity and can do the same jobs as the gasoline and diesel-run models. Electric forklifts are quieter and easy to maintain but still best utilized inside, where bad weather will not affect their function.
Diesel and gasoline-run forklifts are more common for exterior use, partially because of emissions and noisy engines that would affect an indoor work environment. Dual-fuel options are available on some new models that allow an operator to switch back and forth between gas and diesel. Propane is a potential choice of fuel for both interiors and exteriors.
HEAVY METAL
Lift capacity is often the number one feature that forklift buyers look at before putting up the capital for such an important investment. Different jobs require different weight capacities, so it’s up to the buyer to figure out what strength is required. However, it is impractical and expensive to buy a different forklift for each job in and around a facility. This is why many managers look carefully to find forklifts that can provide “do-all” solutions.
For a multi-tasking forklift, one might want to go with the greatest weight capacity available combined with the smallest, most maneuverable body. This way, the machine that is lifting the heavier loads outside is still the same machine that can cut sharp corners and go down narrow aisles inside.
“For us, lifting capacity and maneuverability are important,” says Chad Donley, quality assurance associate with Annaco, Inc., Akron, Ohio. “You get to where you can lift up to 10,000 pounds but the [forklift] gets so big that it might as well be a loader.”
That is why many companies like Daewoo are streamlining and updating existing larger-capacity models so that they can carry the same weight but with a less bulky body. Trudi Baronchuck of Daewoo Heavy Industries America Corp., Warrensville Heights, Ohio, says Daewoo is currently producing units that can maneuver in tight spots while maintaining the type of lift power usually associated with outdoor units.
“We have added two very large units— our 100 and 150,” Baronchuck says. “They go from 22,500-pound lift capacity to 33,000-pound lift capacity. Before we had stopped at 15,500 pounds. Most of those units are used for outdoor environments, but now there is a focus on indoor use and narrow aisles so they have a very tight turning radius.”
Doug Baringer, sales engineer of Royal Tractor Co., Inc., New Century, Kan., echoes this interest in versatility when talking about that company’s new PT-300 and PTE-300 models. “The idea is kind of a yard-shuttle, indoor-outdoor machine that we tried because we believe there is a market for it,” Baringer says. “We’re building them in the range of 16,500-pound to 40,000 pound capacity. Electric power is what sets the PTE model apart from the standard PT.”
RE-INVENTING THE WHEEL
All forklift wheels are not created equal. There are several factors, including lift-capacity and primary workplace (interior or exterior) that dictate the best type of wheels for the job. Most often, forklifts designed for outdoor use come equipped with pneumatic tires which can be filled with air, water or foam to help prevent punctures on rough terrain. Solid tires are commonly used on interior forklifts. They provide more articulate movement for a forklift and have a wider turning radius. Cushion tire trucks are primarily designed for smooth surface use. 1
Solid pneumatic profile tires, like the ones on Royal Tractors’ PT Series combine the durability of pneumatics with the control of a solid tire. “It’s built on our cushion truck chassis design, but it’s got a pneumatic profile cushion tire. In other words, it’s solid,” Baringer says. “There are so many cushion tire trucks, which are smooth pavement only, and that limits what the machine can do. Many places have material stored outside, and when you have to go outside with a forklift designed for interior use it’s too often a problem.”
CREATURE COMFORTS
Ergonomics have moved to the forefront of important features on most new models of forklifts. Safety and comfort quickly becomes very important for anyone who has his or her posterior planted on a hot piece of machinery for eight-hour workdays. There are several ways to make the ride a little easier.
“You have people who literally do this for a whole shift long, and these operators have to be comfortable,” Baronchuck says. She points out which types of features Daewoo has concentrated on improving. “That the seats are comfortable is a major consideration, as is excellent visibility. The levers are all at arm’s length and the [newer models] are much less noisy than they used to be.”
Barringer also mentions ergonomic improvements to Royal Tractor’s line. “We are offering air seats on our cushion tire units now,” he says. “We are going away from tread-plate floorboards. We now put a smooth floorboard in with the real heavy-duty rubber mats. Sometimes the heat coming up from the steel floorboard can really be a problem. The rubber floor mat really helps with that.” Baringer says that some models even come with tilt steering columns.
Pete Haikio, Sky Trak/Omniquip, Port Washington, Wisc., also understands the importance of ergonomics. “From an operator’s standpoint we have a full compliment of operator compartments,” Haikio says. “We spend a lot of time concentrating on the operator and making it easy to run our product. We recognize that there are a lot of different people that run our machines during a day and we want to make the controls very intuitive and easy to use.”
Revised safety standards issued by the Occupational Safety and Health Administration (OSHA) require that there are training programs for forklift operators. But good safety means more than compliance with training. Manufacturers are encouraged to have their equipment meet OSHA safety specifications in an attempt to curb unnecessary accidents, which can cause bodily harm to both operators and innocent bystanders.
Most manufacturers know the importance of safety and take steps necessary to help ensure it. “All of our machines are built in accordance to the current ANSE specs, and OSHA works off of the ANSE specs on mobile equipment,” Baringer says. “We’ve put in operator restraint systems above and beyond what is normally called for.”
Other training programs are also available. “There is an OSHA operating training program available that we helped develop through EMI,” Haikio says. “In our industry, OSHA has a requirement that all operators be trained in operations by December 1. That applies to industrial forklifts, rough-terrain telescopics and rough-terrain straight masts and trailer-mounted machines. It seems to be a hot topic today.”
There are certain features buyers can look for to help them choose a model with safety in mind. Things like a wide-view mast, overhead guards and rearview mirrors help with visibility. Cowl covers reduce the risk of wires or hoses from drifting into an operator’s face. Wide entrance steps and rubber padding help reduce slipping or falling on or around machinery.
MAINTENANCE IS THE KEY TO PERFORMANCE
But not all features are for the benefit of operator safety and comfort. Sometimes practical design is the objective.
“We concentrate a lot of our design efforts on maintenance,” says Haikio. “We try to do things that stretch out service intervals so that it gives operators and owners more flexibility.”
Baronchuck says that some of the new Daewoo models utilize a clamshell design that aids service maintenance by opening up easily. “Other models have a tool-less floor plate that you can easily lift out for maintenance,” he says. “If a truck is down you have to get it up fast, because time is money. That is taken care of with the easy accessability for maintenance.”
“Our maintenance programs are pretty much stipulated by our dealers,” Baronchuck says. “And they are preventative maintenance programs. Most likely in recycling, you would have more frequent maintenance programs. In that kind of environment you would want to have preventative maintenance.”
Haikio says that there are actions being taken to lengthen intervals between maintenance. “We believe that daily requirements for maintenance are a thing of the past, and we’re designing our machines to have much longer service intervals. If an operator is doing daily maintenance—and not daily checks, because I think daily checks need to be done—he is not working, which affects productivity. We tend to have 250-hour service intervals. We think that’s pretty important.”
Some recyclers approach maintenance with their own program. Donley says that his facility employs a software program to help keep maintenance up to date.
“We have our own preventive maintenance program that’s run through the manufacturer,” Donley says. “A computer program pulls up automatic work orders at the intervals the manufacturer suggests. It could be an oil change at every 100 hours or a diagnostic check at every 1,000 hours.”
“Maintenance is so dependent on the conditions,” Baringer says. “I imagine for recyclers, maintenance is tough. They run over steel all of the time—gouging tires. Also, there is contamination of the environment. Air cleaners aid help with that. All our machines come with a pre-cleaner on them which extends the life of the air filter itself.”
ATTACHMENTS: MAKING THINGS MORE EFFICIENT
Sometimes a material handler’s job isn’t as simple as lifting and dropping, and sometimes a basic fork design isn’t enough to get the job done. Instead of putting up more capital for separate lift trucks, some managers choose to invest in attachments of their forklifts. This extends their capabilities, giving a forklift multiple facility uses.
Some attachments you can buy pre-designed from the manufacturer. But some companies, like Royal Tractor, will custom design attachments to fit a client’s needs.
“We have some rotator attachments so that if you are doing large quantities of small pieces you can dump hoppers,” Barringer says. “We custom design a variety of tools for foundries and smelters,” he adds.
As forklifts continue to develop, so do new types of attachments to mount on them, allowing the industry to become increasingly more efficient. As demand increases, manufacturers are beginning to make attachments a priority.
“We spend a lot of time on attachments,” Haikio says. “Clearly that is a big driver in our industry in general. Recycling we see as a growing segment as well, so we are developing attachments that would be conducive to that—rotating grapples, those types of things.”
Sometimes the attachments are added at the dealer level rather than by the manufacturer, and clearly they can be for applications beyond recycling. “Some of our dealers have done that,” Baronchuck says. “I know that in Canada they used buckets for apple and potato harvests. Also, clamps for paper and drums have been configured, but again that would be done at the dealer level.” The author is a staff member of Recycling Today.
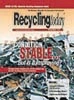
Explore the November 1999 Issue
Check out more from this issue and find your next story to read.
Latest from Recycling Today
- Eagle Dumpster Rental identifies its MRF-unfriendly items
- American Securities acquires Integrated Global Services Inc.
- Fleetio integrates Maintenance Shop Network add-in
- 3rd Eye expands suite of fleet safety solutions
- Newsom orders SB 54 revision
- Biffa sees recycling, composting opportunities at events
- Copper market navigation stress lingers
- IWS ramps up NJ MRF