When operations at a scrap yard reach a certain level of sophistication, acquiring a material handling machine that can handle high volumes and provide significant reach becomes a necessity.
The variety of material handling equipment now serving the scrap industry is staggering. Sorting it out into categories could result in several different scenarios, based on platform (wheels, treads, rails or pedestal), on configuration (lattice boom, or two or three-piece hydraulic), on origin (built for scrap, or converted from an excavator), and even power source (the vast majority are diesel, but there are now electric-powered pedestal material handlers on the market).
HOW MUCH MOBILITY?
Purchasers of scrap handlers buy them for different reasons, and those reasons can lead to different decisions as far as which platform is most suitable.
In some cases, a large material handling machine is being bought for one specific and very stationary purpose, such as feeding an auto shredder, a large ferrous baler, or for loading scrap barges.
For these applications, the processor may consider a stationary or pedestal-mounted handler. Manufacturers of these stationary machines note that they can be designed specifically to address one task with a certain amount of confidence that they won’t be pressed into service to try and accomplish other chores.
Thus, the length and rotation of the boom and even the attachment chosen can be designed to cater to the desired reach, lifting capacity, and ability to handle a certain type of material.
Other advantages that can be gained from a stationary machine include a cab with an elevated height that allows the operator to survey the process carefully and the safety factor of having a machine secured to the ground so that tipping becomes a non-issue.
Northshore Manufacturing Inc., Two Harbors, Minn., recently installed two pedestal-mounted cranes at a California waste transfer station and MRF. Space constraints and safety considerations led to a novel idea: rather than mounting cabs atop the handlers, a separate control room with a video monitor was created. “Our operator has a seat and a control set-up virtually identical to what he would have in a traditional handler cab,” says a spokesperson from the waste handling company. “Rather than looking out a windshield, however, he looks at the pit area on a 19-inch color monitor.”
According to a Northshore spokesperson, the company could potentially install the same closed-circuit camera and monitor technology on other Northshore/Builtrite models, including those used in scrap handling applications.
While there is some demand for pedestal-mounted machines, most material handlers purchased in the scrap and recycling industries are hydraulic ones mounted on rubber tires, treads or railcars.
“A lot of the scrap yards are going to concrete or pavement surfaces,” says Ken Cornett, an applications specialist with LBX Co., makers of Link-Belt equipment. “So, thus, they look for rubber-tired machines so that the mobility is a little better and because they’re less damaging to the surface.”
Most vendors of scrap handlers agree that rubber-tired machines—which must usually be equipped with solid tires or other types of tires designed to withstand sharp metal scrap or other hazards that can puncture normal tires—have gained in popularity throughout the 1990s.
Scrap handlers on treads (or crawlers as they are also called) still remain the favored option for many recyclers. Treads offer enough mobility to move from task to task within a given yard, although at a relatively slow rate of speed. They can also make their way through mud and over rough terrain in most cases, which can be an important consideration at some facilities.
Rail-mounted cranes or scrap handlers—a common site at steel mills—can also be found at some scrap yards. Scrap-handling cranes mounted on rails offer a speed advantage, according to Jim Westlake, a vice president with Eastern Railway Supplies, West Seneca, N.Y. “You can travel from 14 to 20 miles per hour, versus five or six miles per hour on tires and two or three on treads,” says Westlake.
A manager at one steel mill servicing company that recently purchased a rail-mounted Liebherr scrap handler says the rail option was chosen because of its “reliability and cost per hour to operate, its efficiency, its short cycle time and its speed moving in the yard.” The Liebherr 954 material handler is mounted on a rail base provided by Railcrane Corp., Chagrin Falls, Ohio. It is operated by International Mill Service Inc. (IMS) to load electric arc furnace charging buckets at a steel mill in Warren, Ohio.
CONVERSIONS VIE WITH PURPOSE-BUILT MACHINES
Scrap processors can almost be considered late-comers to the large-scale material handling market. Certainly, much of the design of material handling equipment in previous decades was done for the construction industry and the bulk shipping industry.
Because of the one-time lack of scrap-specific machines, converting existing machines has become an industry segment of its own.
The original conversions may have been simple enough: taking off the hooks or wrecking balls used by the construction and demolition industries along with their cable cranes and putting in their place a lifting magnet. In all likelihood, some of the cable cranes still in use were purchased pre-owned from these industries and converted for scrap use in this way.
When hydraulic excavators began making their debuts several decades ago (as upgrades of the venerable “steam shovels”), this created a new and somewhat more complex conversion opportunity.
Simply changing attachments from a bucket to a grapple or magnet would not create a machine with maximum scrap-handling productivity. Excavators are designed to reach into the ground and dig, so are not necessarily engineered to either reach long distances or carry large volumes of material.
But a handful of engineers and equipment mechanics devised ways of converting excavators (by replacing the boom and adding counterweights, for starters) to function as material handling machines. When many of these individuals began finding ready markets for their converted machines, manufacturers began taking notice.
Now, most heavy equipment manufacturers are either offering converted excavators as their own original equipment or—increasingly so—are designing and making machines to appeal specifically to the scrap market.
Caterpillar Inc., Peoria, Ill., increased its offering of material handling machines targeted specifically to the scrap market when it purchased the former Material Handling Crane Systems almost two years ago. That company, now an operating unit of Caterpillar, specializes in converting and designing excavators for use as scrap and material handling machines.
LBX Co., Lexington, Ky., has several models in its Scrapmaster line, including machines with operating weights ranging from 70,000 pounds to 138,000 pounds. “The machines we build for the scrap industry have heavier duty frames and heavier turntable bearings,” says Cornett. “The components are built to withstand more stress.”
MORE VARIATIONS ON THE THEME
As the twentieth century draws to a close, an inventory of scrap handling machines in use in North America makes for a varied and complicated roster.
Lattice boom or cable cranes—long purchased on the second-hand market by ferrous scrap yard operators—remain on the job at numerous facilities. In a 1997 material handling equipment survey conducted by Recycling Today, one-quarter of scrap processors responding still used a cable crane. (And half of those cable crane owners used more than one of the machines, including 10% who owned six or more.)
Link-Belt’s Cornett is aware that plenty of his company’s cable cranes are still on the job at scrap facilities. “We’re well known for our 98 model cranes and other cranes we built that are still at work today,” says Cornett. “We’re still producing parts for them and we still build an occasional 98 today. It’s a very good machine because of its durability and simplicity.”
Westlake, of Eastern Railway Supplies, says the cable cranes are in demand less from scrap yards than they are from bridge builders and at some steel mills, where they are used to lift heavy slabs.
Hydraulic machines are in demand in a variety of sizes and for an increasing number of different applications.
“The smaller machines, starting at about the 40,000 pound weight class, are used by small facilities that might choose a rubber-tired machine for mobility,” says Tim Wilson, a product specialist with Caterpillar Inc. “The smaller models are also used by large companies to perform off-site work at, say, a generator’s facility to help load scrap,” he continues. “Demolition contractors might choose a small or medium-sized machine on treads to sort and load material at a demolition site,” adds Wilson.
Not surprisingly, according to Wilson, “as the sophistication level gets higher—from a feeder yard to someone with a shear to a large central facility selling directly to the mills—typically the size of the machine tends to get larger, because the volume of material is greater.”
Different applications may also affect the decision by some buyers whether they want a two-piece or three-piece hydraulic handling arm. Westlake notes that the ERS Powerstick made by his company is available in both configurations, and each has its favored applications. “If the buyer is doing a lot of below-grade work, such as cleaning out pits at steel mills, then the three-piece is superior. A two-piece configuration might be sufficient for many other applications,” he notes.
The Powerstick is favored by some buyers for another reason that comes into play: its reach. “It has a 70-foot boom,” says Westlake of the rail-mounted device, “and it enables the user to unload a gondola car—the far end and the near end—without uncoupling.”
Both Link-Belt and Eastern Railway Supplies have roots going back to the days before hydraulic handlers, and both still market cranes with the lattice boom configuration. But even representatives from companies such as these acknowledge that the hydraulic machines can offer clear-cut advantages.
“It’s a proven fact that the hydraulic machines are faster and you have less maintenance than with lattice boom cranes,” says Westlake. He notes that lattice boom machines have clutches and brakes to adjust “all the time, because they’re friction operated.”
Ease of operation—especially at a time with a tight labor market—is another factor in favor of hydraulics. “You can take somebody who’s a novice and within two or three days, that person could be moving a lot of scrap with a hydraulic machine,” says Westlake.
Hydraulic handlers are also starting to find recycling applications beyond the scrap yard. Large volume paper stock plants and MRFs are beginning to enter the hydraulic handler market. Link-Belt’s Cornett notes that the machines are being used to handle baled paper, loose paper and at mixed waste processing facilities to tear open bags and move the mixed waste to its first stage in the separating process.
MRF and paper packing plant operators have found that they can use a hydraulic handler in place of a skid steer that may have been overworked in its attempt to move material at large-volume facilities. The larger handlers can fulfill the role without being overtaxed the way a skid steer would. Additionally, the higher cab of a material handler allows the operator to see potential contaminants and, if a grapple is being used, even remove larger undesirable items.
Without question, as the recycling and scrap industries mature and evolve—and in many cases centralize into larger facilities—large cranes and hydraulic handlers will continue to expand their role in the recycling industry. The author is editor of Recycling Today.
No Shortage of Attachment Choices
There are not only a variety of large material handling machines working within the recycling industry, but also a number of different attachments that work in coordination with those machines.
Lifting magnets are commonly associated with cranes and large scrap handlers, since the ferrous scrap market is the segment of the recycling industry where such machines are most common
Magnets are indeed a common attachment found on scrap handlers, but grapples, shears and hammers can all be found as well. Which attachment is used depends primarily on what type of material is being lifted or processed.
According to Tim Wilson of Caterpillar Inc., ferrous scrap that is going to be baled would most likely be loaded with an orange peel grapple “because the material is often loose or stringy” or perhaps the load consists of white goods. A magnet, on the other hand “is best when material is heavy and dense, such as structural steel, plate steel or I-beams,” he adds.
Wilson notes that “some users will switch out both. They’ll use the grapple for much of the material, but the magnet to sweep off the ground.” The ability to switch attachments quickly, he remarks, is becoming more requested.
Scrap shears have a place in the market as well, and are used to downsize large objects for further processing. Demolition contractors or scrap processors working at a demolition site will often use machines with shear attachments as well as hydraulic hammer attachments.
In the recycling industry, the hydraulic hammer is used to pulverize concrete as a means of blasting it into smaller pieces and recovering the structural or reinforcing steel beneath the concrete.
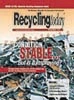
Explore the November 1999 Issue
Check out more from this issue and find your next story to read.
Latest from Recycling Today
- BlueScope, BHP & Rio Tinto select site for electric smelting furnace pilot plant
- Magnomer joins Canada Plastics Pact
- Electra names new CFO
- WM of Pennsylvania awarded RNG vehicle funding
- Nucor receives West Virginia funding assist
- Ferrous market ends 2024 in familiar rut
- Aqua Metals secures $1.5M loan, reports operational strides
- AF&PA urges veto of NY bill