Hydraulic handlers have skyrocketed as the material handling machine of choice at high-output recycling facilities
Within the recycling industry, the heavy iron has always been most at home where iron-bearing scrap is lifted high and in large amounts.
While lattice-boom cranes can still be seen in many locations doing the heavy lifting, hydraulic material handlers have been put at the top of the shopping list for most ferrous scrap processors updating their material handling fleets.
When shopping for scrap handlers, recyclers have a number of choices not only of different equipment manufacturers, but also of different configurations, platforms and lifting capabilities.
HIGH AND WIDE
Hydraulic material handling machines are not the only type of equipment that can move large amounts of material. But an advantage they offer is to be able to reach high and wide to both pick up and drop off material. Also, the machines can be configured to work with a variety of attachments that can perform specific tasks required by scrap recyclers.
As an example, Caterpillar Inc., Peoria, Ill., offers 17 material handling models that are marketed to the scrap market (nine on treads, five on wheels, two on rails and one pedestal unit).
Those machines vary in horizontal reach from less than 35 feet for the smallest model to 55 feet for the largest mobile model. The maximum heights that can be reached vary from less than 40 feet to 70 feet for the largest crawler-mounted model.
Additionally, high-reach Caterpillar models that are marketed to the demolition industry can reach maximum heights of more than 83 feet.
For stationary applications, pedestal cranes can offer an even wider reach. The E-Crane, a large equilibrium crane that is most often pedestal or gantry-mounted, has been installed in U.S. and Canadian applications to reach 81 feet, and can be configured to offer 150 feet of reach.
Lifting capacity desired is another determining factor in making a scrap handler purchase. Using the Caterpillar line again as an example, machines heavy duty enough to be marketed as scrap handlers are offered with lifting capacities ranging from less than 16,000 pounds to more than 48,500 pounds.
Determining the optimum lifting capacity (and operating weight) of a machine is a key efficiency factor for recyclers. On the one hand, a machine that is too small will not be able to keep up if output at a facility grows. On the other hand, a machine too large for its application means a recycler has overpaid and is probably burning through more fuel than is necessary.
Choosing which attachments to use from among lifting magnets, mobile shears and several types of grapples, involves carefully evaluating material handling operations. Most recyclers keep more than one type of attachment on hand and will change the work tool needed to suit the task.
One additional consideration is whether to choose a material handler on wheels or treads, or, in some cases, to consider a rail-mounted or pedestal-mounted machine. The mobile platforms are more common, with wheeled units getting the nod at paved scrap yards. At unpaved yards with mud that can create tricky conditions, tracked machines are still preferred.
A CASE IN POINT
A scrap recycling company that has done its research can estimate how much power and reach it will need when it goes into the market to buy a new machine.
With those parameters in mind, a shopper can then compare the features of the machines in the appropriate weight class, and take a closer look at the intangibles.
When Tube City Inc., King of Prussia, Pa., was recently in the market for new scrap handling machines, company officials knew that durability was going to be a key requirement.
“You won’t find any tougher application for a scrap handling fleet anywhere in the country,” says David Coslov, vice president of Tube City’s maintenance and equipment operations. Coslov, who is based at Tube City’s U.S. Steel Gary Works operations in northern Indiana, was among those from the company who looked over equipment available from several manufacturers.
At the company’s Gary facility, material handlers are operated around the clock for 365 days a year to keep the U.S. Steel furnaces fed with the scrap portion of their charge. “We measure the performance of our machines very closely,” says Coslov, who notes that Tube City tracks the use of all its machines through a computer program that collects information on maintenance records, downtime, failure costs and other records.
Over time, Tube City has been able to build a detailed performance chart of the nine handlers that function at the Gary complex. The company can gauge lifting capacity, hourly performance, uptime, downtime, cost of service, strong points and weak points, as well as manufacturer and dealer responsiveness.
“When we go to the market, we want to be able to match the right machine for the job,” says Coslov. “We also want to be assured that we are going to be able to get quick response from the dealer who supplied the machine. We want to know that our needs are going to be serviced and that machinery downtime is going to be kept to a minimum.”
Tube City’s most recent purchasing decision led it to Sennebogen, a German equipment maker beginning to establish a presence in the North American scrap handling market. Tube City’s Gary location took delivery of a Sennebogen 870 wheeled scrap handler late this past summer.
The hydraulic scrap handler was sold through the Crane & Machinery Inc. dealership in Bridgeview, Ill., an authorized distributor of Sennebogen equipment through the Sennebogen LLC master dealership, based in Charlotte, N.C.
Coslov says the machine will help handle the 200,000 to 250,000 tons per month of ferrous scrap that moves through the staging area located near U.S. Steel’s blast furnaces.
The machine’s durability and the simplicity of its design were among the features that impressed Coslov and other Tube City officials. Coslov says he favors the simpler electronic controls and other design considerations that resulted from meetings between representatives from Tube City and Sennebogen. The maintenance vice president remarks that the electrical systems of some machines “are too technical and complex for the scrap environment they operate in. It causes more problems than it solves.”
Erich Sennebogen, managing director of the Straubing, Germany-based company, visited Gary to ceremonially deliver the new machine to Tube City. “Tube City is a very important customer for our company. Tube City took a risk, but had the vision to order the first Sennebogen 870 wheeled machines in the U.S,” he remarked at the late August ceremony.
Erich says his company’s equipment will appeal to owners and operators of scrap yards in North America. “Our philosophy is to make very tough machines. Material handling machines in applications like this work at full stress. There is no easy part of the job.”
THE EXTRAS
It is unclear whether the labor climate this decade will be as tight as it was in much of the 1990s. But one thing the tight labor market of the ‘90s taught business owners and equipment designers is that attention to operator comfort and ease of control mechanisms can make the search for employees a little less intense.
As retired Caterpillar Inc. engineer Tom Muller noted in a recent presentation (a partial transcript of which can be found starting on page S26), “playing in the dirt” is becoming a less attractive job option to an increasing number of young people.
That is one factor prompting equipment companies to pay more attention to operator cab configurations, including comfortable seating, ergonomically friendly controls, climate control and ease of operation.
Recycling company owners may buy the equipment, but they’ll need to have satisfied employees operating the machines on a daily basis. These employees may be similarly concerned about productivity, cycle times and reliability, but they are also likely to be more productive if they are working in a cab that is not excessively loud, hot, cold or uncomfortable.
The promotional materials of most equipment makers now usually include a description of features and options available for the machine’s cab.
John Deere Construction Equipment Co., Moline, Ill., touts comfort as one of five leading factors (along with control, productivity, mobility and energy savings) in favor of one of its excavating and material handling machines.
The company said of its 110 model, when it was introduced three years ago, that the machine features the “widest cab in its industry class, with a large storage area behind the seat.”
Other comfort features noted include low noise levels, a rotating venting system that delivers greater fresh air flow, silicone liquid-filled rubber isolation mounts that reduce cab vibration, adjustable controllers mounted on armrests, an easy-to-read control panel layout, and a sun roof.
Scrap handlers made by German equipment maker Fuchs, whose American offices are in Dallas, are available with air conditioning systems. “These machines work non-stop in scrap yard operations to feed the mills or in garbage transfer stations,” remarks Bill Stenberg, vice president of product support for the Fuchs line. “Either way, these are hard working machines in tough conditions, and the operators need a system that will deliver.”
Fuchs is working with Hammond Air Conditioning Ltd., Ingersoll, Ontario, Canada, to offer Arctic Wolf air conditioning systems in MHL350, 360 and 380 material handling machines.
Jeff Lemon, president and chief system designer with Hammond, says representatives from Fuchs communicated clearly that the systems would have to be durable, yet also priced competitively. “It had to be less expensive than factory air, using a quiet engine-driven compressor as opposed to a hydraulically driven one from the factory and [it would have] to handle constant vibration without failing.”
Stenberg says the system can be installed by Fuchs dealers using a kit. “Not only did [Hammond] design and install an air conditioning unit that is integrated right into the machine and keeps the operator cool from head to toe, it is designed so as not to interfere with the movement of the seat or any of the controls.”
Caterpillar is also touting the ergonomic friendliness of its material handler models. The company describes its 320C MHY operator workstation as quiet, with ergonomic control placement and convenient adjustment devices.
Like many equipment companies, Caterpillar has switched to joystick controls for its material handling machines, a design feature that makes sense when the equipment operators of tomorrow have been raised on video games where mastering joystick and toggle controls separates peak performers from also-rans.
Caterpillar’s Muller noted in his presentation on equipment designs of the future that introducing joysticks is a first step, but that future controls can be configured to look even more like the game system controllers that are second nature to young people.
Commenting on current designs, Muller asks, “Name me one video game that has two levers? There aren’t any. The kids won’t know how to run this machine. Today’s kids play these video games with their thumbs. Can you run a machine with your thumbs? Most certainly. [We have to design] the control schemes that are possible in the future.”
With the video game generation now beginning to reach the workforce, equipment makers are preparing to offer future operators machines they can productively operate.
The author is editor of Recycling Today and can be contacted via e-mail at btaylor@RecyclingToday.com .
Get curated news on YOUR industry.
Enter your email to receive our newsletters.
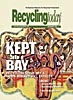
Explore the November 2001 Issue
Check out more from this issue and find your next story to read.
Latest from Recycling Today
- Green Cubes unveils forklift battery line
- Rebar association points to trade turmoil
- LumiCup offers single-use plastic alternative
- European project yields recycled-content ABS
- ICM to host colocated events in Shanghai
- Astera runs into NIMBY concerns in Colorado
- ReMA opposes European efforts seeking export restrictions for recyclables
- Fresh Perspective: Raj Bagaria