Mobile material handling machines— from forklifts to large scrap handlers—can all carry hefty price tags. Hopefully, a machine purchased will be worth every penny. But whether the new owner is filled with pride or buyer’s remorse, the best way to justify the expense is to maintain the machine so it performs well for an extended number of years.
The term “maintenance” can be a broad one when it refers to the care and upkeep of mobile material handling machines working in the often harsh environments of recycling facilities.
Maintenance decisions can start with adding extra armor to scrap handlers and also includes the more commonly considered oil and fluids changing schedules. Machine operator habits and the condition of the ground on which machines must tread also end up being maintenance and vehicle life expectancy considerations.
AN OUNCE OF PREVENTION
An English scholar might contend that the term “preventive maintenance” is redundant, since if one is attempting to maintain a machine in its peak condition, then that automatically involves preventing the machine’s condition from declining.
However, there are ways of preventing misfortune from befalling a machine that go beyond the realm of actual maintenance duties.
Many of those methods begin at the shopping stage. Buyers of equipment that is destined to toil in rugged work environments—scrap yards, demolition sites, glass cullet processing facilities—can prevent future headaches by shopping wisely.
A number of manufacturers of forklifts, loaders and other material handlers offer special “armor” packages on newly-ordered machines. Many forklift makers can add a steel plate beneath the undercarriage to protect engine and drivetrain parts from damage caused by pieces of metal or other objects that the lift truck may run over in scrap yards and other industrial facilities.
Some skid steer makers also offer additional armor, including thicker steel bodies and added plates or guards to prevent damage to the undercarriage and, of course, to the operator.
Buyers of hydraulic scrap handlers, too, should make sure the machines are as prepared as possible to work in the conditions they will encounter. “The machines we build for the scrap industry have a heavier-duty frame and heavier turntable bearings,” notes Tim Wilson, a product specialist with Caterpillar Inc., Peoria, Ill. “The components are built to withstand more stress,” he says of the company’s hydraulic handlers built for the scrap market.
Tom Hickson of Liebherr dealer Republic Crane & Equipment Co., Charlotte, N.C., says that Liebherr builds its scrap handlers differently from its excavators. “They start with the application in mind. The undercarriages are different for a scrap handler than those on an excavator would be,” he notes. He says extra protection is also provided over the outrigger cylinders and that protection rings are placed between the tires.
The tires themselves can be a source of downtime at scrap facilities or demolition sites. Most mobile material handling equipment owners in these segments have become convinced that solid tires, foam-filled tires or other specialty tires are an expense that proves worthwhile by minimizing the downtime cause by failed tires.
Another way to minimize downtime is to provide as clean a work area as possible—no easy task in a scrap yard or scrap-consuming mill or foundry. There are several methods available to clean up paths and heavily-traveled areas at recycling facilities, including sweeper attachments that can be mounted on skid steers or other mobile material handling equipment.
Despite the best maintenance efforts, machines will “age” as they put more operating hours under their belt. “Repair problems tend to become more common over time,” notes Caterpillar’s Wilson, who estimates that a properly-maintained large material handler could last 30,000 operating hours or more.
Wilson relates a commonly-used tactic to prolong a machine’s life in terms of years of service. “At 15,000 hours, an owner or operations manager might move a machine to a less demanding application. A scrap metal company might move the machine to a feeder yard,” says Wilson, adding that “at a large yard, it’s not hard to put on 20,000 hours pretty quickly, especially if they’re running more than one shift.”
FLUID VIGILANCE
Regularly scheduled maintenance is not the stuff television dramas are made—or even corporate video highlights. But despite the mundane nature of checking fluid levels, changing fluids, checking brake pads and other regularly scheduled assignments, these operations can be critical to running a recycling facility profitably.
“The life expectancy of all equipment has to do with maintenance,” says the maintenance supervisor of one southern company. Although he admits that the importance of the work could easily be overlooked by the less vigilant, he declares that “you have to keep up with it. You have to keep decent records. As much of a pain as it is, you have to do the paperwork.”
Some operations managers have found that remaining loyal to one brand of a given type of equipment is one way to streamline the maintenance procedures and stock the necessary parts to lessen downtime.
John Deere & Co., Moline, Ill., is among the manufacturers who have introduced several maintenance and service programs catering to material handling equipment owners. The company has designed what it calls the “Total Repair Cost Management (TRCM)” strategy of machine maintenance, which includes a software package called MaintainIt.
The MaintainIt software will “put complete machine histories at your fingertips,” and combines such features as spare parts inventory lists and a maintenance task check list. The software allows the operator to track inventory and schedule maintenance procedures based on hour-meter readings or by date.
Shipping parts promptly has also been a point of competition between manufacturers, several of whom have introduced programs designed to make sure replacement parts are delivered promptly and accurately.
In addition to providing parts and service information, manufacturers are also attempting to make engine compartments and other frequently-maintained areas of the machine accessible.
Forklifts made by Daewoo’s forklift division, with American headquarters in Warrensville Heights, Ohio, are being designed with a clamshell configuration that makes engine maintenance easier. Several other manufacturers are also paying attention to the ease with which both the engine compartment and the undercarriage can be serviced.
The ability to easily sample and drain fluids is a foremost consideration. Owners of larger scrap handling machines (major capital expenses) will often conduct analyses of oil samples drawn from the machines. The spectrographic analysis can reveal the presence of trace elements by type—lead, iron, copper, etc.—allowing a mechanic to pinpoint any problem areas. A mechanic might conclude that the presence of sodium in the oil means that coolant or engine water is leaking into the oil system, while the presence of certain types of metal probably points to excessive wear within the engine, transmission or drive system.
Periodic, scheduled analysis can help mechanics spot trends and ideally take steps to prevent problems that could lead to some sort of system failure.
Other areas of a scrap handler that merit extra attention include the undercarriage and the battery. The undercarriage should be kept as clean as possible (not always an easy task at a scrap yard), or at least kept free of large cakes of mud and pieces of debris. Scrap handlers on treads should have the treads regularly checked and adjusted so that they are at the correct tension level.
Routine battery testing can help prevent the downtime caused by a dead battery, while terminals should also be checked for corrosion and greased if necessary. Replacement batteries should be models that have passed vibration tests with a high grade, since most scrap handlers will put the battery and its connections through rugged conditions caused by rough terrain and occasional bumps and knocks.
ATTACHMENT MAINTENANCE
The maintenance of scrap handling equipment can go beyond the machines to include the attachments as well.
Buckets and grapples most often have hydraulic systems that require some maintenance.
The hydraulic cylinders of grapples and shears should be checked for cracks and leaks. Shear blades must regularly be checked and replaced as needed, while the tines of grapples must also be checked for cracks. The tolerance, or space between the blade and the anvil, of hydraulic shear attachments must also be checked and adjusted if necessary.
Magnets, though seemingly simple in their application, can require several maintenance tasks. The case of the magnet can become cracked, dented or suffer a broken weld, while discolored metal can indicate severe wear. The lifting lugs, the chain and the terminal box should also be checked for broken welds. The terminal box especially should be checked for any broken lead clamps, wire stress or leakage that could cause future problems.
The magnet’s bottom plate should be checked with a straight edge to make sure there is no unusual bending occurring. Any metal discoloration found could also be a source of concern, as it could indicate electrical arcing.
Finally, the magnet coil can be tested with an Ohmmeter for insulation resistance, while a voltmeter can indicate the level of coil resistance. Resistance readings can be checked against the magnet’s rated levels.
Between chores associated directly with the machines, as well as the attachments, there should be little room for boredom for operations and maintenance personnel striving to keep mobile material handling equipment running in peak condition.
THE DAWN OF E-MAINTENANCE
As with everything else, computer technology is changing the way maintenance is performed on material handling equipment. Computer-based software programs are being used by some business owners to better manage their maintenance programs.
Another way computers are being used is to help maintenance personnel in self-diagnosis routines. Some material handlers have recently been designed with an onboard microchip that tracks the complete history of the machine. By reading the data from the chip, a serviceman can find out when the machine was running hot, and for how long; when the oil level dropped below the recommended amount, or any number of other parameters.
“The chip can track these parameters from day one, and continue for the life of the handler, or the chip can be wiped clean, such as after a major overhaul,” says one dealer of this latest innovation to reach the heavy equipment industry.
Other pieces of equipment are being designed with the ability to allow maintenance personnel to plug in diagnostic tools to determine specific system parameters, so repair decisions can be made.
Heavy equipment companies may soon also be using satellites to relay repair information to dealers. In one situation, an onboard transmitter will automatically relay a problem to a satellite, from which problem-solving information can be downloaded by the dealer. The dealer can then call the machine’s owner to discuss repair options, or the dealer can take action even before the owner knows there is a problem.
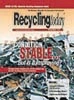
Explore the November 1999 Issue
Check out more from this issue and find your next story to read.
Latest from Recycling Today
- P+PB adds new board members
- BlueScope, BHP & Rio Tinto select site for electric smelting furnace pilot plant
- Magnomer joins Canada Plastics Pact
- Out of touch with reality
- Electra names new CFO
- WM of Pennsylvania awarded RNG vehicle funding
- Nucor receives West Virginia funding assist
- Ferrous market ends 2024 in familiar rut