Sleek styling, remote controls and computerization are likely trends for the heavy equipment of the future.
Caterpillar Inc., Peoria, Ill., with its NPI (new product introduction) process, is looking out for your future. We are looking 15 to 25 years into the future and trying to determine what it will be like out there in the various businesses that our equipment is used in.
Once we have a vision of what that industry will be like, we try to determine just what kind of a machine it will take to accomplish the job in that industry 20 to 25 years in the future. We then take that vision of that machine and fold it back to today in three to six year increments. These increments depend on how often we are going to update these machines. The smaller machines may be updated every three years, while the larger ones may be updated every six years. As we fold this vision of the machine back to today, we determine if there is technology available to accomplish this vision of the machine. If it is, we put it on the next update. If it is not available, then we have to invent it. That is the job of our research people at our technical center in Mossville, Ill.
THE FUTURE: A CERTAIN DESTINATION
Why should you be concerned and interested in the future? Because you’re going to spend the rest of your life there. When you are planning for the future, just remember one thing, the future usually arrives before we are ready for it.
Now, let’s take a little trip into the future. Many of us are being towed into the 21st century, and we’re screaming and clawing, trying to hold our way back. All of us have a natural tendency to resist change. We don’t really want to look too far into the future. It’s scary out there! We won’t know what to do. But really, there isn’t anything that we cannot do.
One of the mottos we go by at Caterpillar is this: Those who say it can’t be done should step aside for those who are doing it. There are plenty of people around who say, “You can’t do that; we tried that years ago and it didn’t work.” Or, “What we have is good enough.” But we have to continually improve these products. If we don’t, someone will come along, reverse engineer them, make some improvements and pass us by. Continuous improvement is the only way to keep your customers satisfied.
Some of the concepts and machines Caterpillar develops you’ll definitely see in production. Some of them you might see for sale. Some of them you definitely won’t see. But nevertheless, we’re trying to get you to think about them “outside the box.” We’re going to examine some general trends that we see going on in your area, in your country, in the world and in our industry. We’ll examine what we are going to be doing about these trends and how these trends will influence the design of the future machines. We’re going to show you where we are, where we are going, and where we are going from there. Remember one thing—change is the only constant.
We have to change. I’ll guarantee you one thing, if you are running your businesses ten years from today exactly the same way you are running it today, you’re going to be out of business. Technology is changing so fast, that if we don’t change, we will be lost in our competitors’ dust.
DRASTIC CHANGE
In taking a look at prototype models, try not to laugh: Remember, we can do anything. Equipment doesn’t have to look like it does today. It’s not going to look like it does today.
This is a high-speed excavator. When excavators travel, you want the distance between the rear sprocket and the front idler to be short so that it is more maneuverable and easier to turn. When you get to where you want to work, you want that distance to be long, so that the machine is more stable. You’ll notice that from the travel position, the high idler goes down into the roller frame and the front idler telescopes out giving you a long undercarriage. Notice the operating station is up inside the boom, right where they have the best view of the bucket. They go up and down with the boom. Not only do they go up and down, so does the counterweight. So basically you are just raising the full bucket and the counterweight is helping. Today it doesn’t. It helps to hold you on the ground, but it doesn’t help to get you out of the hole.
And then there is the future machine 999 wheel loader. It kind of looks like a mad bumble bee. Notice anything different about this loader? The front tires are bigger than the back ones.
We design the front final drives, differentials and axles to take all the high loading forces and low gear torque . All the work and force it takes to load the bucket goes into the bucket, up the lift arms, down through the front frame into the front axle, differential, final drive and out to the ground through the tire. That’s how we design the gears in the axle. They have to take all of this high loading and torque. Then we put the same size final drive and differential on the rear. What does the rear end do? All it does is haul around the engine; it doesn’t do much work at all. So you can put a different size axle on the rear. This will save some money, because axles are one of the most expensive arrangements on the loader.
We’re working on a backhoe loader that’s actually a backhoe/forehoe loader. Note that the backhoe can dig either way—going backward or forward.
COMPUTERIZATION
One of the clear trends we see going on in the industry that definitely will continue to happen is this: Tomorrow’s machines are definitely going to be “electro-X.” What do I mean by “electro-X”? “Electro-X” means electro-hydraulic, electro-mechanical, electro-pneumatic, electro- just fill in the blank.
Electronics will be used to control the hydraulics, used to control the mechanical items, and used to control the pneumatic items. The electronics can give you a more precise control over these other systems.
Electronics are the system integrators. These electronics are small microchips, small computers.
Let me give you an example of electro-X. If you have bought a new car recently with a lot of goodies on it, then there is more computing power on that car than on the Apollo space mission that went to the moon about 20 years ago.
Think about that: More computing power on your car than on that space vehicle. That includes the rockets and the lunar lander put together. Today’s cars have electronically computer controlled ignitions. They have computer controlled anti-lock brakes, traction control, memory seats, etc. All of this stuff takes computing power.
Cars are becoming computers with wheels. Cameras are computers with optics. Airplanes are computers with wings. It has been said that there is more computing power in the $2.98 birthday card that plays “Happy Birthday” than was available in the world in 1950. There is more computing power in the 1996 $250 Nintendo 64-bit game system than in a 20-year-old, $2.5 million Cray super computer.
Prognostics! |
Prognostics is the ability to predict an event. According to Tom Muller, a former engineer with Caterpillar Inc., this is where the computer controlled machine of today and tomorrow is taking equipment operators. It will have the ability to warn of possible problems that are coming in time so they can be fixed before failure. “Think of the machines as becoming more human-like. We know when we are not feeling just quite right. Now, thanks to sensors, they are developing that same capability.” Says Muller, “Life insurance companies make money betting on how long you are going to live. They have tables that tell them, under most conditions, just how long you are going to function and at what level, before you start to wear out. We know the same thing about our machine components. They all have life curves. Some things wear out faster than others. If we monitor these rates, we can predict when the component will need an overhaul.” Iron talks, says Muller, and the best mechanics know this. “They listen, look at the iron, and they can usually tell what the problem is. Prognostic abilities will also do the same thing. One thing a computer really does well is count. It can count how many times the piston went up and down on a machine in a day, or count for a month, or count from the machine’s birth. This information, along with remembering how much fuel went through the engine, gives a really good indication as to how the engine has been used, and how much life has been taken out of it. This is what will be happening in the machines of the future.” |
SUPER-SIZE IT
Here’s another trend. If the scrap industry follows the mining industry, then bigger is better. How big can these machines become? Can they become big enough that these machines fit in the box of a bigger truck? What is the weakest technology link for these machines becoming larger? Right now, tires are the weakest technological link to machines getting any bigger and still functioning well.
Why is “bigger is better” a trend in the mining (or the scrap) industry? Because one man on this Cat 994 can do the work of two men on the next size smaller machine. One man versus two men. More productivity per person is something that all of us need to pursue.
SIMPLY COMPLEX
Much like jumbo shrimp, the construction machines of tomorrow are going to be an oxymoron. They are going to be what I call “simply complex.”
What do I mean by simply complex? Think about what photography was like 20 years ago. If you wanted to get into being a photographer, you’d spend about $500 to $750 to buy yourself a good single lens reflex camera.
The camera would have all kinds of gadgets and dials on it, and inside the box you would find an instruction book about three-quarters of an inch thick. You’d go through that book and learn how to set all the dials, etc. And as you read the book you would discover that you need an exposure meter, a flash attachment, a tripod, filters, additional lenses, this and that, not to mention a camera bag to carry it all around in.
So you go out and buy all that stuff. After all of these purchases, you have a couple thousand dollars invested in your hobby and several instruction manuals. And maybe, after 25 to 50 rolls of film, if you are a quick study, you can take a pretty good picture.
What happens today? Today, for about $125 to $200 you can buy what I call a “point and poke” camera. It comes with an instruction book that is about three pages. It tells you how to open the back of the camera, where to put the film, and how to shut the back of the camera. Then what happens?
It winds itself, it reads the bar code on the film as it goes by so it knows what film speed is, and it stops at picture number one. When you want to take a picture, you point the camera and poke the button, and that’s about all that is involved. It sets the exposure, focuses itself, flashes if necessary, and winds on to picture number two. Again you point and poke, picture three, four, etc.
When it gets to the end of the film, what happens? It rewinds the film all the way back to zero. Now all you have to do is figure out how to get the back of the camera open to get the film out. It does the rest by itself, and the pictures that come out are as good as the pictures you took out of that high-priced camera and gear 15 years ago.
Now that is a very, very, very complex camera but very simple to operate. That’s what we mean by simply complex. The machines of tomorrow are going to become very complex, but very simple to operate. Point and poke machines. Every bit as productive as today’s, but very simple to operate.
Why is this important to owners of companies who operate heavy equipment? Because there is a trend out there that just scares me to death, and should scare you, and that is this: Today’s kids do not play in the dirt.
When we grew up, most of us played in the dirt. Today’s kids may play in the dirt when they’re two, three, or even 3-1/2 years old, but once they hit four or five years old, what are they doing? They’re playing Sega and Nintendo games and typing on computers. They’re not out playing in the dirt.
When they grow up and become adults, and enter the work force, they’re still not going to want to go out and play or work in the dirt. When I was growing up, and that big piece of yellow equipment went by, my reaction was: “Wow! I want to get on that. I want to drive that. I want to design that.”
Not today’s kids. When they grow up they’re going to want to sit at computers, not work and play in the dirt. Guess what our business is? Working and playing in the dirt. The trend that is happening in the world is that it is becoming harder and harder to find and to keep good heavy equipment operators! You may already see this trend in your area.
Tomorrow’s operators are going to be less skilled, so we’re going to have to make tomorrow’s machines simpler to operate but every bit as productive—point and poke machines—simply complex.
If you think that that trend is kind of scary, remember this: Today’s kids would rather play in the dirt than they would in the grease and oil! Tomorrow’s mechanics are going to be even harder to find than tomorrow’s operators.
The Intimidation Factor |
Programming a computer seems like a task that is not for the technologically faint of heart. But almost all of us have programmed a computer, though we may not be aware of it. Says retired Caterpillar Inc. engineer Tom Muller, “Everybody likes technology, as long as it is easy to use—or it may be that you don’t even know that you are using it.” As an example, Muller often asks attendees of seminars he is speaking at to raise their hands if they have never programmed a computer. While most hands stay raised, his next question brings the vast majority of them down. “If you have cruise control on your car, put your hand down,” he asks. “You will almost always get every hand to go down,” notes Muller. “And if you don’t, ask them if they have an AM/FM radio in their car for which they program in the stations that they want to listen to.” Noting that the VCR is another example, Muller can then state to his audiences, “There you go. You’re all computer programmers and you didn’t even know it.” |
A REMOTE SCENARIO
In a mining application, a computer can be programmed to store the topography of the mine, and a video relay can show dump trucks running on the road. Now these are autonomous trucks: There is nobody driving these trucks. Therefore, they can look different, i.e., with no cabs and more room for payload.
They must still be able to detect obstacles in the road, pass each other at high speeds and schedule their own service and maintenance. This is future technology, but the future is now!
Several years ago this truck was running at our proving grounds in Tucson, Ariz. It is a 150-ton truck. Nobody was driving that truck. It used global positioning satellite (GPS) for navigation, and a radar system to detect obstacles in the road. It was a totally computer controlled truck.
We had two 50-ton trucks running at a customer’s job site in Texas. Nobody was driving those trucks.
We are also working on auto dig excavators. Basically you take them to where you want them to dig, tell them how deep you want them to dig, hit dig, and leave the cab and let them dig! It even knows how to dig around big rocks that may be in the way.
This is an excavator that has the ability to see, or to perceive. It has to know where the pile is, where the last bucket full came from, where the truck is, and where to dump the load into the truck.. The technology for machines to see and perceive is here today.
In a less remote control-based scenario, what the operator does is point the loader at the pile with the bucket on the ground, and poke the accelerator to the floor. The machine will automatically load the bucket when the machine contacts the pile, and the operator does not have to touch the implement controls until he wants to control the linkage for dumping the bucket.
Some operators are good operators, and may be able to beat the computer at filling the bucket. If they think they can, they just hit the teach button, load the bucket the way they normally do, and then when the bucket is at the height that they want to take control, the hit it again. The next time the operator goes into the pile, the machine will dig just the way he taught it to. This is also a good feature if you have a good operator and several not-so-good ones. The good operator can teach their machines to dig as good as he can. If cruise control works on cars, and reduces the fatigue of driving, it should also work on heavy equipment.
What will cabs of tomorrow look like? Knowing your kids and grand kids, what is the number one thing that you will have to have in these cabs? Probably a big booming stereo, followed by air conditioning.
Remember, they don’t want to be there anyway, so you’re going to have to entertain them and keep them comfortable.
What is number three? Tomorrow’s cabs will have to have video games in them! When kids play video games, they are trying to beat the game or beat their last score. They will play and play to try to become better. Or, in our vernacular, they are trying to improve their productivity!
THE FUTURE MEDICINE MAN
The smartest doctor in the world has got to be the veterinarian.
The veterinarian works on all kinds of animals: those with two legs and two arms; two legs and no arms; four legs, a horn, a tail, or maybe the patient has no legs at all! And the worst part of it is, when his patients come into see him, they can’t tell him where they hurt!
Yet today we expect our mechanics and service people to be as smart and know as much as the veterinarian.
The operator calls and says that the machine isn’t running right. The service man asks “what’s the matter with it?” The operator says, “I don’t know, just come out and fix it!” He gets to the field and the machine has tracks, or it could have wheels; it has this hydraulic system or that hydraulic system; this electric system or that electric system.
And unless their are pieces laying on the ground, the machines can’t tell them where they hurt. Yet we expect them to know everything about it. So mechanics are very, very important to us, and we have to help them all we can.
This is where electronics come in. The electronics on the machines of tomorrow are going to have to tell the mechanics where they hurt. Not only are they going to have to tell them where they hurt now, they’re going to have to tell them where they hurt in the past.
The mechanic’s going to come in, download the computer, and listen to it to find out what’s going on. If you look at the machines, they are becoming more like us.
They have a pump, we have a pump. They have a hydraulic system, we have a hydraulic system. They have an electrical system, we have an electrical system.
What we are doing to the machines now is adding brains to them. These brains require inputs just like ours. They get these inputs from sensors. More and more sensors are being added to the machines.
These sensors will supply more information to the computers, which will make things easier to diagnose by telling us more and more about the machine.
As you can see, Cat is thinking far out into the future. With your help and the help of the dealers, we can all set new standards that would have been unheard of just a few years ago.
The author is a former engineer with Caterpillar Inc., at its Aurora, Ill., facility. The article is an edited version of a presentation made earlier this year at a Caterpillar Industrial Customer Seminar.
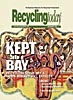
Explore the November 2001 Issue
Check out more from this issue and find your next story to read.
Latest from Recycling Today
- Returpack reports increased DRS activity in Sweden
- Trade groups align against European export restrictions
- Construction, auto sectors show mixed signals
- Politics in Turkey threaten recycled steel outlet
- Toppoint Holdings expands chassis fleet
- Lego creates miniature tire recycling market
- Lux Research webinar examines chemical recycling timetables
- Plastics producer tracks pulse of wire recycling market