They aren't as loud and showy as larger equipment, but nimble forklifts and skid steers carry their fair share for recyclers.
The beep-beep warning of a moving forklift truck is part of the audio setting at most industrial work sites, with recycling facilities being no exception.
Many recyclers of paper, light metals and curbside materials rely almost exclusively on forklifts and compact skid steer loaders to carry the mobile material handling load. High-volume operators may graduate to larger handlers and loaders, but even they still use the smaller machines to handle appropriate loads.
At scrap yards, material recovery facilities (MRFs) and other recycling plants throughout the world, these compact worker bees do what they are asked by plant managers and workers who have come to depend on them.
STICK A FORK IN IT
The high-rising cable cranes may catch a visitor’s eye first. And solid looking hydraulic material handlers and skid steers gain attention with their rugged tires and treads and closed-in operator cabins.
But based purely on head count, smaller and quieter forklift trucks continue to perform a lot of the material handling work needed by recyclers.
In a survey recently conducted by Recycling Today, more than 90 percent of the companies responding that operate material handling equipment use one or more forklifts. The percentage outweighs those for all other types of machines, including skid steer loaders and wheeled loaders.
And in most cases, recyclers own more than one forklift, with the forklift owners among survey respondents owning an average of 3.8 of the industrial trucks.
Compared to results of a similar survey conducted four years ago, forklifts appear to be even more ubiquitous now than they were then. In the 1997 Recycling Today survey, 80 percent of respondents operated one or more forklifts, compared to greater than 90 percent in the 2001 survey. And in 1997, 46 percent of the forklift owners used just one of the machines, while this year 64 percent of forklift owners use more than one of the machines.
Recyclers operating indoor facilities often opt for forklifts powered by electric-charged batteries. The clean-burning battery models are devoid of emissions and generally operate at a lower decibel level, helping recyclers stay within noise limits.
Propane is also popular as a fuel choice, with these models also being used indoors or in applications where the lift trucks may work both indoors and outdoors and require a longer “cruising range” between charges or fill-ups.
Diesel models still maintain market share, with many lift truck buyers believing diesel forklifts can offer the most power for heavier work. The heaviest lift trucks—which look from a distance more like large wheel loaders—are generally equipped with diesel engines. The Daewoo D150, as an example, can lift more than 30,000 pounds with its Daewoo D1146 diesel engine.
The smaller forklifts are more commonly the ones filling a lot of needs for recyclers. Paper recyclers rely on lift trucks to move finished paper bales from the baling area to a waiting container or storage area.
Similarly, nonferrous metal recyclers who sort various alloys into Gaylord boxes or similarly sized containers use forklifts to convey full containers to the shipping area.
The forklift market is a competitive one, with several manufacturers vying for attention.
One Stop Shopping |
Imagine a giant showroom where a recycling plant manager could comparison shop for forklifts, skid steers, loaders, scrap handlers and even cable cranes—all in one place. Every three years in Las Vegas, imagination becomes reality when ConExpo-Con/Agg is held inside and outside of the Las Vegas Convention Center. Although the show was created and is sponsored by associations in the construction and road building industries, the equipment on display is also used by several other industries, and the mammoth expo draws attendees from many of these other economic sectors. In 2002, ConExpo takes place from March 19 to 23. The show’s organizers are preparing for another record-breaking event in terms of space rented and the number of exhibitors who will be present. As of this summer, more than 1.8 million net square feet of outdoor and indoor exhibit space had been reserved by more than 1,300 exhibitors. Those totals already surpass the records established at the 1999 ConExpo event. “More than 420 new companies will join the excitement, exhibiting at ConExpo-Con/Agg for the first time in 2002,” says Peter T. Vlahos, the show’s managing director. “Their enthusiasm and a strong commitment from returning exhibitors have increased the footprint of the event’s exhibit space to over 41 acres.” While some of the equipment is specific to contractors who work with concrete and construction, virtually every manufacturer of mobile material handling equipment brings a fleet of vehicles for attendees to examine and, ideally, put on their shopping lists. Some makers of loaders and material handlers host special events where the equipment’s capabilities are demonstrated live for attendee audiences. |
As with larger types of mobile equipment, companies are touting ease of operation and operator comfort factors inherent in their machines. Caterpillar Inc., Peoria, Ill., says its lift trucks feature a “spacious operator’s compartment, a specially contoured seat and flexible operator restraint system with a resilient belt [to] offer freedom of movement with security.”
Safety factors are also a consideration, with companies such as Komatsu International America Corp., Vernon Hills, Ill., touting the “excellent overhead protection” armor it installs over the driver’s seat, and “highly reliable power brakes.” The company is also tapping into the desire for operator comfort by offering adjustable tilt-wheel steering on some models and orthopedically designed seats.
THE SKID STEER STORY
When something more multi-faceted than a forklift is required, the skid steer loader is often the next step up in material handling.
Skid steers, also called compact loaders, have replaced forklifts in some instances, but more often seem to work in tandem with lift trucks at recycling facilities. In many cases, skid steers work with incoming loose materials while forklifts continue to be used to transport bales or full Gaylord boxes and containers at the end of a processing operation.
Skid steers are so named because of the turning ratio of the machines, which allow them to operate in confined areas while minimizing driving in reverse. The machines are generally considered more versatile than forklifts, since they are designed to change out attachments, and thus can act as loaders, mobile shears and even as forklifts.
Skids Save Workers Time, Effort |
As the recycling program in Abbotsford, B.C., Canada, has grown over the past decade, so has the number of Bobcat skid-steer loaders used by the municipality. The machines are used to save time and labor in handling the materials, which range from milk jugs and tin cans to newspaper and cardboard. The program began in 1990. At that time, a Bobcat 743 loader was used to help process a total of 1,350 metric tons of recyclable materials. In 2000, volume exceeded 10,000 metric tons and kept three Bobcat loaders busy. The machines, purchased from a nearby Bobcat dealership, include a 753, 763 and a new 863 G-Series loader. “The Bobcat loaders handle about 60 percent of all product,” remarks John Richards, who manages the Abbotsford recycling program. The facility, operated by Abbotsford Community Services, is essentially designed around the Bobcat equipment. To get the job done quickly and efficiently, the 863 pushes incoming material onto conveyor belts where it can be sorted by hand. Once that is done, the two smaller machines, equipped with Bobcat grapple buckets, load the cardboard onto a conveyor that feeds the material to a baler. The loaders are also used to load newspaper onto trailers and to pack loose, sorted paper into other trailers, where it is hauled to the mill. —Paul DeMarinis (This item originally appeared in the Bobcat Worksaver publication.) |
The machines continue to grow in popularity with recyclers, according to the most recent Recycling Today mobile material handling survey. While 49 percent of respondents owned one or more skid steers in 1997, this year’s survey revealed a 64 percent ownership rate among respondents.
The versatility of the machines is one reason for their popularity, while the fact that many are built to endure the bumps and bruises that can occur in a recycling environment is also helpful.
Marketing materials for companies such as Bobcat Inc., West Fargo, N.D., John Deere, Moline, Ill., and Caterpillar demonstrate the variety available not just in skid steer sizes and lifting capacities, but also in types of attachments that can be used.
Help for Hydraulics |
The hydraulic system is one of the fluid systems circulating the lifeblood for mobile material handling machines. Hydraulics control the moving parts that do the lifting and loading for forklifts, skid steers, wheel loaders and large scrap handling machines. Mechanics working at recycling facilities soon learn to spot and fix hydraulic problems, and repair specialists sent by dealerships and equipment companies must be taught the hydraulic schematics of the machines they work on backwards and forward. For mechanics who wish to retain a textbook on hydraulics nearby, the Society of Automotive Engineers Inc. (SAE), Warrendale, Pa., is distributing Hydraulics in Mobile Equipment, a reference book on the subject. The book is published by the German manufacturer Bosch and is being distributed in North America by the SAE as “an ideal reference book for those working in development, production and service of hydraulic systems,” according to a news release put out by the organization. According to the SAE, nearly half of all hydraulics applications involve mobile equipment. The book presents up-to-date technology on hydraulic system components with an emphasis on applications with tractors and forklifts. Hydraulics in Mobile Equipment is available for $45 from SAE International through its Web site at www.sae.org or by calling toll-free in the U.S. or Canada at 1-877-606-7323. |
In one promotional piece, John Deere notes that its skid steers can be equipped with the following:
•a wide variety of buckets from three feet to seven feet wide
•a four-in-one bucket that also digs
•tooth bars that allow buckets to scarify pavement
•hydraulic breakers that pulverize pavement
•a combination grapple bucket ideal for handling loose scrap
•a backhoe dipper arm
•pallet forks (in several sizes and space configurations)
•an angle broom for cleaning jobs
•a cement mixer and a cold planer for paving applications
•tillers, nursery jaws, bale spears and landscape rakes for the agriculture and landscape markets
•trenchers and augers for less intrusive digging applications.
Scrap processors and demolition contractors also attach mobile shears to the larger skid steer models.
Move It (And Lose It) |
From simple infeed units to elaborate sorting systems, conveyors are moving tons of recyclables through recycling plants. The humble conveyor belt is not taken for granted by recyclers. In the recycling industry, different forms of conveyors do much more than just move material from point A to point B. Although the sole purpose of many conveyors is the movement of material, an array of specialty conveyors act as screening and separation devices for recyclers as well, shaking out contaminants or splitting equally valuable streams. These machines—with a variety of descriptive names—add value to an end product at the same time they are conveying material efficiently through the production process. Among the types of conveyors recyclers can consider when designing a plant are vibratory screens equipped with discs, fingers, grates or stars that allow some materials to fall through (usually onto another conveyor) while other materials move forward. A visitor to a material recovery facility (MRF), an auto shredder yard or a paper stock plant is likely to see a number of conveyors. In auto shredder operations, whole cars may be lifted by a scrap handler onto the infeed conveyor, and from there go the shredder and a series of conveyor belts that send iron-bearing scrap one direction and nonferrous metals another, until the output is placed in bunkers awaiting its turn to be loaded and shipped to a mill. MRFs may be most reliant on conveyors, with moving screens pushing material forward at the same time it is sending it to different paths, often on more conveyor belts heading to different balers for final processing. |
In an industry that has seen commodity prices stay low and the need to operate efficiently stay at an all-time high, skid steers have stayed in favor among recyclers. “If I had to work with just one piece of equipment, it would be our Bobcat 753 [skid steer loader] because it’s so versatile and works so efficiently,” says Sam Morris of Mid-Coast Solid Waste Corp., a Rockport, Maine, company that also operates a baler and works with loose recyclables.
Morris says the versatile and productive skid steer “enable us to run the facility with just two people and still turn out about three tons per day of baled newsprint, mixed paper, corrugated cardboard, tin and plastic jugs.”
Morris’ words are music to the ears of skid steer manufacturers, who market their models along with a variety of attachments promising the very same result: to allow recyclers to accomplish several tasks with one machine that will be sturdy and reliable.
The author is the editor of Recycling Today and can be reached via e-mail at btaylor@RecyclingToday.com .
Weighing In and Checking for Trouble |
For recyclers looking for the absolute fastest cycle times and throughputs in their yards, instruments that measure and detect material while it is in transit have a definite appeal. Two common stopping points at a scrap yard are the scale and the radiation detection station. While manufacturers of this equipment have done a commendable job of speeding up both processes at the point where a truck enters a facility, they are also working on alternatives. Both onboard scales and radiation detectors mounted on attachments have been introduced and are in use by recyclers. Accu Load, Oxnard, Calif., offers a Forklift Weighing Program that provides a “lift and display” measurement reading that it says is accurate to within one percent. The device gives the user “speed and flexibility in weighing during peak traffic or production periods,” a company news release states. The measurements taken can be used when loading trucks, verifying shipments or taking inventory. An innovation in radiation detection has been the Cricket, a radiation detector mounted onto a scrap-handling grapple. The Cricket is made by Rad/Comm Systems Corp., Mississauga, Ontario, Canada. Rad/Comm’s Steve Steranka says practicality was one of the main reasons to incorporate a radiation detection device into the grapple. “We looked at the entire scrap handling industry and decided the best way [to detect radioactivity] was to get in contact with the metal itself. It was totally impractical to use a hand-held radiation detection device to get every piece,” he notes. Users of the Cricket can safeguard against the costly liability of shipping (or worse yet melting) radioactive scrap while causing no or minimal hiccups in the productivity-centered task of moving scrap metal into and out of processing machinery and to the steel mill’s furnace. According to Steranka, Rad/Comm is also developing a magnet attachment with the same radiation detection capabilities. |
Get curated news on YOUR industry.
Enter your email to receive our newsletters.
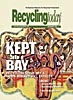
Explore the November 2001 Issue
Check out more from this issue and find your next story to read.
Latest from Recycling Today
- Returpack reports increased DRS activity in Sweden
- Trade groups align against European export restrictions
- Construction, auto sectors show mixed signals
- Politics in Turkey threaten recycled steel outlet
- Toppoint Holdings expands chassis fleet
- Lego creates miniature tire recycling market
- Lux Research webinar examines chemical recycling timetables
- Plastics producer tracks pulse of wire recycling market