As processing equipment has grown, so has the preference for heavier loaders.
Balers can now bale paper at outputs once hard to even imagine by recyclers. Likewise, metal processing machines—from shears to shredders to balers—are available in gigantic sizes with ravenous appetites.
To feed these recycling raptors, plant operators are sometimes looking to wheel loader models more commonly associated with massive earth-moving efforts.
Construction-sized wheel loaders are no longer a rare site at recycling facilities, especially at larger ferrous yards, but even at paperstock plants with ramped up capacity.
BY THE BUCKET LOAD
Without question, there are piles of scrap material at larger yards and facilities that can best be moved and loaded by loaders with capacities of five cubic yards or more.
In some cases, such as where tall reach height is required or the careful feeding of processing machinery means that tighter control of what is picked up is needed, than hydraulic handlers might get the nod over wheel loaders.
But in locations where enough material is being loaded and moved in bulk, one or more wheel loaders will almost certainly be part of the scrap handling fleet.
Wheel loaders are sold into a number of markets, many of which absorb a far greater number of machines than the recycling market. The construction industry is almost certainly the largest purchaser of wheel loaders, with the machines being a workhorse in site preparation duties.
But the machines are used to move more than dirt and gravel, and are also used to move snow, coal, ore, animal feed and scrap metal and paper.
The Case Construction Equipment division of Case New Holland offers not only a number of different sized wheel loaders, but also a variety of buckets to accommodate the demands of industrial customers.
For its 621B model wheel loader, Case suggests buckets in the range from two cubic yards to 2.75 cubic yards. The buckets can include teeth or a bolted-on edge to suit the application.
Caterpillar Inc., Peoria, Ill., offers 17 wheel loader sizes in its line, plus an additional eight models marketed as having “waste handling arrangements.”
Cat’s smallest loader is typically equipped with buckets holding around one cubic yard, while its largest loader (used in massive mining operations) can be equipped with a bucket that carries 40 cubic yards of material.
ARMOR-PLATED
As with other material handling machines, when wheel loaders are sold into the scrap market, buyers often request features that will help the machines endure the jagged metal and airborne dust that can cause harm to a piece of equipment.
In a recent presentation at an Industrial Customer Seminar, engineer Earl Dowell of Caterpillar Inc., Peoria, Ill., notes that Caterpillar offers its scrap customers loaders equipped with additional armor to protect hoses and other non-metallic parts from potential damage from jagged metal pieces.
For paper recyclers and those in the solid waste industry, Cat wheel loaders can be equipped with a heat jacket that covers hot engine parts, preventing small pieces of paper from coming in contact with the hot engine and igniting.
In that same vein of thinking, machines can be equipped with a reversible fan that blows off accumulated pieces of paper and other small items that might stick to the grill and ignite when the front of the machine is at a higher temperature.
John Deere Construction Equipment Co., Moline, Ill., has teamed with Waste Management Inc., Houston, to design wheel loader machines built specifically to work in solid waste and recycling applications.
A two-year collaborative project led to the creation of the 644H and 304H wheel loaders, which were designed and tested by engineers from both companies.
“Since they were designed specifically for this application, they include numerous features that make the operator’s job much easier,” says Roger Mohr, director of the John Deere Corporate Business Division.
According to the companies, both the compact 304H waste handler and its “larger cousin,” the 644H, offer unique cooling and guarding systems for extra protection in harsh environments. The cooling system includes an optional reversible radiator fan so the operator can periodically blast debris off the screens without leaving the cab.
Benefits of both loaders include integrated guarding to protect the fuel tank, engine, underside and key grease points; faster reach, longer reach and high dump height.
Unique to the 304H is stereo steering, which offers “the tightest turn radius in its class,” according to the companies. The 644H offers a high-lift option that adds more than a foot to the reach height to reach up over high-sided trucks and trailers.
SINGLE SHIFT MENTALITY
From super-sized shredders to high-volume extrusion balers, processing equipment used by the recycling industry has burst into a new era of high output over the last two decades.
Not all businesses can necessarily collect enough material to turn out three times as much product (although some have). What others are doing is processing their tonnage in few hours each day.
With processing equipment that can do this, the next step is to own material handling equipment that can keep up with the shredder, baler or shear.
In Recycling Today’s 2001 survey of recyclers, more than 60 percent of those responding operated a wheeled loader, with many of those owning more than one of the machines.
The machines are used in several applications, with high-volume loading and unloading of loose scrap materials being the most common. While in some cases smaller skid steer loaders can do the same work, many recyclers are finding that using the larger loaders makes sense.
Operators of auto shredders use the machines to load ferrous shred from beneath the shredder plant to waiting bunker areas or rail cars. At large MRFs and paperstock plants, wheeled loaders move loose paper grades tipped from collection trucks onto waiting trucks or boxcars.
When Komatsu American International Co., Vernon Hills, Ill., conducted a tour of North America three years ago displaying some of its larger volume equipment, the company had little trouble convincing forward-thinking recyclers that large loaders had a future.
Regarding the sale of one machine, a Komatsu distributor said at the time of the tour, “once it started picking up twice the weight—which means twice the revenue—the customer started doing the math. There are some variables involved, but they could buy this machine and, in 125 days, it just paid for itself. And for the next 10 years, it just makes you money.”
More and more recyclers seem to be doing that math, and concluding that high volume machines that can help them prepare more material for shipment in less time will ultimately prove to be a wise purchase. RT
Get curated news on YOUR industry.
Enter your email to receive our newsletters.
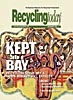
Explore the November 2001 Issue
Check out more from this issue and find your next story to read.
Latest from Recycling Today
- Returpack reports increased DRS activity in Sweden
- Trade groups align against European export restrictions
- Construction, auto sectors show mixed signals
- Politics in Turkey threaten recycled steel outlet
- Toppoint Holdings expands chassis fleet
- Lego creates miniature tire recycling market
- Lux Research webinar examines chemical recycling timetables
- Plastics producer tracks pulse of wire recycling market