It takes a lot of “ingredients” to make a commercial or industrial building, and each of those ingredients—or materials to be more accurate—will still be present when the building comes down.
The continuing puzzle for contractors and other recyclers of construction and demolition (C&D) debris is that some of these materials are in demand in their scrap forms, while others can best be characterized as waste.
The good news for C&D recyclers is that two of the most prominent (by weight) materials—concrete and metal—are the two materials most in demand by end market consumers.
CONCRETE DEMAND
The public at large may not be aware of concrete recycling. After all, concrete is not left out at the curb to be collected, and there has been little in the way of public service announcements to make television viewers aware that concrete is a recyclable material.
But road builders, construction firms and demolition contractors have become keenly aware of the recyclability of concrete, with the 1990s marking a breakthrough decade by most accounts.
Nearly 100 million tons of crushed cement concrete is now consumed per year by aggregates users, making up nearly 5% of the overall construction aggregates market. Those numbers are estimates based on a survey conducted by the Portland Cement Association, Skokie, Ill., and the Construction Materials Recycling Association, Naperville, Ill.
Respondents to that survey also indicated that their usage of crushed concrete was likely to increase. An analysis of crushed concrete prepared last year by the United States Geological Survey (USGS), Reston, Va., cited another study that showed that natural aggregates producers increased their production of recycled concrete by 37% in on year alone, between 1995 and 1996.
Demolition contractors and specialized concrete crushing operators have reported similar demand for the recycled aggregates. Eagle Amalgamated Services, Gibsonton, Fla., is a demolition firm that last year took down a 74,000-seat football stadium in Tampa. “We had more inquiries for the [crushed concrete] coming out of the stadium than we had materials available,” says R.V. Shulnburg, chairman of Eagle Amalgamated.
“We feel that concrete recycling is absolutely the way of the future,” adds Shulnburg. “We know it’s going to become more and more prevalent.” Eagle owns and operates pulverizers and portable shears that prep demolished concrete materials for a subcontractor, Angelo Iafrate Inc., of Warren, Mich.
Shulnburg points to the Tampa market as one where there is a strong demand for the crushed concrete. “It is absolutely a good market,” he remarks. “The material is in demand. The nearest quarry to Tampa is 50 miles away,” he notes. “As with most natural resources, you just can’t replenish a quarry—it’s impossible. Recycling’s going to get bigger and bigger.”
Product crushed by Iafrate for Eagle “often goes back for base material on the same project,” says Shulnburg, “or it goes into a road building base. It works better than conventional lime rock, because it has better compaction and moisture actually hardens it up, and allows it to be worked right away, unlike lime,” he comments.
There are still contractors letting opportunities to recycle concrete pass by, perhaps due to years of habitually hauling rubble to a C&D landfill out of habit more than any other reason. But in most cases, a little bit of investigating into recycling processes for concrete and end markets for the aggregate produced have proven to be worth the effort for contractors.
Key factors that figure into the “to be or not to be” question for concrete recycling on a given project are tipping fees and transportation costs. Low landfill tipping fees can make hauling and dumping concrete rubble the most cost-effective method in some cases, and the simplicity of the process can be tempting compared to setting up recycling equipment. This is especially true in markets where there are no aggregates makers accepting demolition concrete for secondary crushing.
In addition to tipping fees, the cost of fuel and the distance to the nearest landfill can be a key deciding factor. “Recycling offers savings in the cost of transporting new aggregates and in the cost of hauling and disposing of the old concrete,” notes the American Concrete Pavement Association, Arlington Heights, Ill., on its website.
As Shulnburg noted in the Tampa area, in markets where quarries are further and further from the active metropolitan building areas, the demand for aggregates made from recycled materials is strong, and the economics of recycling should be favorable compared to hauling and dumping.
METALS IN A SLUMP—BUT STILL WANTED
The demolition bidding process for a building with a large amount of structural steel and/or other metals is usually much different than for a structure with less metallic content.
A large enough building, or an industrial complex with tons and tons of metal, can be considered by scrap dealers part of the “mine above ground” that makes up the scrap metal industry.
Even though metal prices have been in a slump for the last 12 months, the end market for demolition scrap steel, aluminum, copper and other metals has by no means disappeared. In fact, scrap dealers anxious to acquire scrap during a down market have been thankful in some regions for an active demolition and building market, which can provide a potential source of scrap.
Steel scrap is by far the volume leader when it comes to metallic demolition scrap, and the price for ferrous scrap fell dramatically in late 1998. Despite that price plunge and the disappointingly slow recovery that has taken place in 1999, structural steel remains a material that is pulled from the demolition stream even during times of low pricing.
However, figures from the Steel Recycling Institute (SRI), Pittsburgh, show that there is room for improvement. In 1998, 88% of obsolete plate and structural was recycled, down from 90% the year before.
Steel used as reinforcing bar for concrete (rebar) is much more often overlooked as a recycling opportunity. According to SRI, just 43.0% of obsolete rebar was recycled in 1998, and only 40% the year before. Often, when concrete is hauled to a landfill rather than being recycled, the steel rebar goes right along with it.
Even though nonferrous prices have been disappointing to scrap traders for the past year (or more in the case of some metals), aluminum and copper piping, tubing and wiring remain commodities with a very real end market.
This decade, there has been no shortage of instances where abandoned industrial and commercial buildings have been stripped of their nonferrous pipes, tubes, wires and sheet metal parts by thieves who knew enough to pick out the metals that bring the highest dollars-per-pound returns.
It may not be the most glamorous endorsement of the demand for nonferrous metals in the scrap market, but it serves as testimony nonetheless of their absolute value.
MORE THAN A WOODEN NICKEL
While its supporters hope that the wood recycling industry will grow to attain the status of a mighty redwood tree, its current status might more accurately be described as that of a younger sapling. There has been some growth, but there is room for more.
Wood recyclers do face some challenges that can make the process difficult. In some instances, they are competing with a renewable resource in trees grown in managed timberlands. And when it comes to products such as wood chips and garden mulch, a difference has emerged in the desirability of different types of waste wood.
Construction contractors and others engaged in land clearing activity have a much less difficult time making a marketable product from green waste (felled trees and limbs). Waste wood recyclers, on the other hand, have a more difficult task producing similar products from wooden boards harvested from demolition sites. The removal of paint and nails provides a processing challenge, and the marketing of a product made from aged, graying boards can be difficult.
Mulch colorizing systems have become one way for waste wood recyclers to increase the marketability of their product. “Mulch coloring is gaining momentum,” says Michael Slattery, regional sales manager of Fecon, Cincinnati, a maker of wood processing equipment, including a colorizing system. “In the East Coast it has been becoming very popular in the past two to three years.”
Slattery predicts that the popularity of colored wood waste mulch will grow and spread further west. But even with colorizing, producers must be cautious of the materials they are using to produce the mulch, he notes. A much higher quality finished product results when a higher grade of feed, for example, wood from new construction projects, is used because it is not contaminated with paint or nails. Mulch made from new construction projects, and then colored either red, black or gold, produces a higher quality finished product.
“We anticipate it becoming a trend to increase profit margins,” Slattery says of colorizing. For a cost of about $3 per cubic yard, wood chip mulch can be colored and marketed in a mulch category that runs about $28 per cubic yard, he notes.
Even more so than with concrete, the availability of affordable landfill space will probably mean that most waste wood heads for a landfill. Compounding the difficulty is the proposal put forth by the U.S. Environmental Protection Agency (EPA) that, in its quest to seek out lead-based paint, casts suspicion on the recyclability of any painted wood.
The proposal, still being reviewed by the agency, would subject any painted wood (and other painted materials as well) that came from a structure built before 1978 to testing for lead-based paint, and would consign it to a landfill if lead paint is found. With most waste wood coming from older structures, the burden imposed on waste wood recyclers to test material or clean material would prove impossible.
It is unclear whether the proposal will ever be enacted, but the threat of the new regulation has caused many wood recyclers to expend energy lobbying against it and to keep their businesses in a holding pattern rather than seeking financing with an eye toward future growth.
STILL SEARCHING FOR NICHE MARKETS
Recycling advocates and those who pioneer the recycling of materials not traditionally recycled still have frontiers to cross in the C&D market.
Metals and concrete have developed into mature recycling commodities markets, and at least in some regions a wood recycling infrastructure is being developed. But at a typical demolition site, there are still materials such as gypsum, plate glass, asphalt shingles and engineered plastics that are most often headed for the landfill.
In some cases—such as gypsum—end markets for the material are only now being developed, with at least the potential existing for a recycling infrastructure to be established.
With other materials, however, the volume produced at any given site does not justify the legwork and effort it might take for a contractor to find a recycling option.
Despite these shortfalls, the C&D recycling markets developed nicely in the 1990s, with an increasing number of construction and demolition contractors who had never considered themselves recyclers entering the recycling industry as a second career.
The author is the editor of Recycling Today.
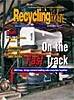
Explore the September 1999 Issue
Check out more from this issue and find your next story to read.
Latest from Recycling Today
- Reconomy brands receive platinum ratings from EcoVadis
- Sortera Technologies ‘owning and operating’ aluminum sorting solutions
- IDTechEx sees electric-powered construction equipment growth
- Global steel output recedes in November
- Fitch Ratings sees reasons for steel optimism in 2025
- P+PB adds new board members
- BlueScope, BHP & Rio Tinto select site for electric smelting furnace pilot plant
- Magnomer joins Canada Plastics Pact