
Most companies look for a business opportunity first and then find the right materials to take advantage of it. However, KW Plastics Recycling has become the world’s biggest plastics recycler by doing it a different way—buying scrap material, then figuring out what to do with it.
“It has always been our commitment—and it comes straight from our owners—that we always take a stream of material, then we develop a home for it,” says Scott Saunders, general manager of KW Plastics Recycling in Troy, Alabama.
Notable achievements

A sign in the lobby at KW Plastics Recycling lays the recycler’s claim to being the world’s biggest by virtue of handling 500 million pounds per year. KW Plastics started in 1981 as a recycler of polypropylene (PP) automotive battery cases. The recycling division was launched in late 1993 to take advantage of a new resin source—high-density polyethylene (HDPE) milk containers. Saunders moved from another KW Plastics division to the recycling division just a few months after it was launched.
The recycling division has seen regular growth. It was even profitable during the 2008-2009 recession years. Despite depressed prices for recycled resins, Saunders says KW Plastics Recycling sold more resin in 2016 than in the previous year.
KW Plastics Recycling’s contrarian business model has produced some remarkable successes for the company. A few years ago, KW Plastics Recycling started buying woven bags. “There are some real challenges to that material,” Saunders says. “It took us almost two years to get the processing end right, but we did.
“You have to understand what it takes to buy scrap, how hard it is to get a supplier and how you have to hold onto them. We have a long-term view. We want to deal with someone for a decade and not just a truckload.” – Scott Saunders, KW Plastics Recycling
“We recycled about 60 million pounds of bag fiber material in 2016, and we are the only ones in the U.S. doing that,” he says. “We had a commitment to the product and the technology, and we were able to find markets for it.”
The resin from recycled woven fiber has several uses. It is sold, used internally in compounds for customers and goes into the parent company’s proprietary products.
A potentially bigger success story is developing. “Before 2012, we recycled zero pounds of polypropylene tubs and lids. Today, we are at 70 million pounds per year,” Saunders says. But the potential is far greater.

He estimates that about 600 million pounds a year of HDPE laundry detergent containers are recycled in the U.S. “We think there is that much market potential for PP tubs and lids, and we are very excited about the growth possibilities. We are already processing about 150 million to 170 million pounds of laundry detergent bottles. We fully expect to do that much in PP tubs and lids.”
Postconsumer PP has become more readily available in the United States since 2013, when the Chinese government implemented its so-called Operation Green Fence policy. Until that time, operators of U.S. material recovery facilities (MRFs) had little incentive to separate PP out of the bales because there was a market for mixed bales in Asia, even when those bales were loaded with contamination.
Operation Green Fence eliminated that market option. “That focused the MRFs’ attention on the fact that they were making a product. Over the past couple of years, their product has gotten better,” Saunders says.
KW Plastics Recycling was ready to accept this new material stream.
Fundamentally, it considers itself a resin company. “We just have a different raw material stream than Exxon or Mobil or any of those other guys,” Saunders says. The company produces about 30 different grades of resin, including resin approved for food packaging.
Successful partnerships
The secret to KW Plastics Recycling’s 23-year record has been the long-term relationships it has with its suppliers—the companies that collect and sell bales of postconsumer plastics.

“You have to understand what it takes to buy scrap, how hard it is to get a supplier and how you have to hold onto them,” he says. “We have a long-term view. We want to deal with someone for a decade and not just a truckload.”
Saunders says prices go up and down for postconsumer material, and buyers drop in and out of the market, but KW Plastics Recycling will take a supplier’s material any time. “We have always wanted to be a home for our suppliers’ material. That works because our customers’ base is just-in-time and the supplier base is just-in-time. Somebody in that chain has to be the buffer because everybody can’t be just-in-time. Someone has to hold some inventory.”
That is a role KW Plastics plays. It built storage capacity so it could aggressively go after raw material. “When others back away, we use it as an opportunity,” he says. “We tell our suppliers that we are going to take their material now but please keep selling to us when everyone else wants to buy. We are always looking for more material.”
KW Plastics Recycling buys bales of postconsumer material from all over the world, generally in 40,000-pound lots. The recycler arranges to ship it to Troy, generally in trucks from Wiley Sanders Truck Lines Inc., a Troy-based company owned by Wiley Sanders, one of the two owners of KW Plastics. About 50 trucks per day arrive at the KW Plastics Recycling loading docks. When it reaches Troy, the material is weighed and visually graded for quality. The material is then washed in a process developed by Kenny Campbell, the other owner of the company.
The next step is reducing the plastic to flakes sized approximately 0.63 inch. The flake then is dried and blown into one of 16 storage silos at the facility.
When a resin order comes in, flake is sent from the silo to the extrusion line for processing, then packaged in an octagonal box that holds 1,700 pounds or loaded directly into a bulk tanker or railcar.
PP is washed and blended in the same facility as HDPE, but it is then moved by tanker truck across the street to a separate processing facility the company has expanded to handle the growing business.
Wash lines are critical
KW Plastics Recycling’s six washing lines each have eight tanks and are 300 feet long. They were designed and built in-house. Each line can wash about 25,000 pounds per hour compared with commercial lines that generally max out at about 6,000 pounds per hour.

“Washing is what separates one company from another,” Saunders says. “Anybody can buy a state-of-the-art extruder if they can get it financed. The real question is whether you can clean material at rates that will allow you to make money.
“Raw material varies, so you have to design a line that can handle good-quality, medium-quality and bad-quality material. What sets us apart is we build wash lines that can handle PP tubs and lids on the same line that we wash bulky 5-gallon buckets,” he says.
“Since we are always looking for new streams, we have to have a wash line that can handle the one-offs,” he says. “We are not just looking for PET bottles to supply a PET bottle plant. That is really the key to our ability to buy new materials. You can’t buy a commercial wash line for woven materials because nobody has done it.”
Because of the contaminants present in the material, including sand, grease and even metal, a wash line is run for a couple of days, then drained and repaired before going back into service.
For size reduction, KW Plastics Recycling uses shredders from SSI Shredding Systems Inc., Wilsonville, Oregon, and Cumberland granulators from the ACS Group, New Berlin, Wisconsin. Saunders says he has six operational shredders and two spares. KW Plastics has exclusively used SSI shredders and Cumberland granulators for at least 25 years.
“We try to align ourselves with good-quality equipment suppliers,” Saunders says. “Then we develop expertise in maintaining and improving that equipment.”
He says the company has worked with SSI and Cumberland over the years to modify equipment. For example, it has worked with SSI to improve knife design.
After size reduction, material is dried in house-built gas dryers before it is blown about 200 feet into one of five flake-storage silos. The silos hold 8 million to 12 million pounds each. “We are not afraid of inventory,” Saunders says. This storage capacity is the key to continually buying whatever material suppliers have to offer.

When the material comes back for further processing, the first stop is one of KW Plastics Recycling’s nine extruders. Most were purchased used, then rebuilt in-house to KW Plastics’ specifications. “We have our own specifications on how we want them to run, screw design and all that,” Saunders says. “Extruders haven’t changed much since 1960. It is the perfect piece of equipment to keep for a long time.”
The nine extruders are a mix of single- and twin-screw models with screw diameters ranging from 6 inches to 12 inches. The separate PP processing facility has six extruders.
The company recently purchased two new single-screw extruders from Davis-Standard LLC, Pawcatuck, Connecticut, because it needed them quickly and did not have time to rebuild older models. At the end of the extruder, underwater pelletizing equipment from Gala Industries Inc., Eagle Rock, Virginia, creates pellets. Gala Industries is another 30-year veteran in the KW Plastics Recycling plant. “They make excellent equipment,” Saunders says.
There is at least one new brand in the plant. “A couple of years ago, we were having a hard time finding someone to build slide-plate screen changers for us, so we tested Ettlingers. We found it was a huge step forward,” he says. “We used to need one operator per machine. Now we will have seven or eight machines running with only two guys in the entire plant.” Once the resin has been pelletized, it likely will go into one of KW Plastics’ dedicated 120 bulk tankers or 68 railcars.
Responsive service
Saunders says his staff knows customers well enough to anticipate their resin needs, particularly seasonal requirements. “We try to have cars loaded and waiting on our long-term customers so when they need it we can roll.
“We try to respond in a week or less. Some customers are two days away by truck, but most of the time we can deliver in 48 hours. It doesn’t do our customer any good to get an order if he cannot respond to it.” He says 99 percent of material is shipped to customers in the American heartland.
The processing plant runs 24 hours per day, seven days per week. It employs about 225 people.
KW Container is a separate business set up next door to injection mold a line of paint buckets from 100-percent-recycled material. It uses about 100 million pounds per year of KW Plastics Recycling resin, including some of the woven fiber material.
Future opportunities
Where will the next opportunity come from? While the company currently processes 500 million pounds of material per year, KW Plastics Recycling estimates it has capacity to process 1 billion pounds. “We are always looking for new opportunities,” Saunders says. “If we can identify a source of material with enough volume and we think we can design a process, we will do it.”
For more information: KW Plastics Recycling, 334-566-1563, www.kwplastics.com
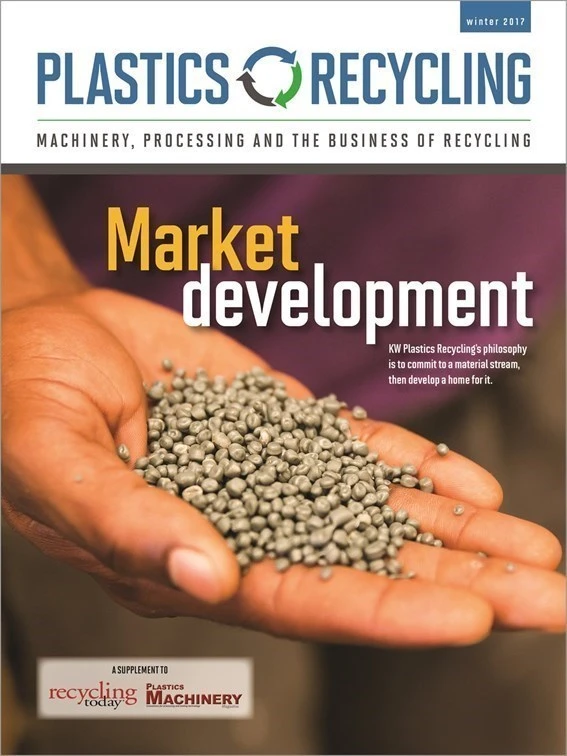
Explore the February 2017 Plastics Recycling Issue
Check out more from this issue and find your next story to read.
Latest from Recycling Today
- CP Group announces new senior vice president
- APR publishes Design Guide in French
- AmSty recorded first sales of PolyRenew Styrene in 2024
- PRE says EU’s plastic recycling industry at a breaking point
- Call2Recycle Canada, Staples Professional expand partnership
- Circular Services breaks ground on north Texas MRF
- Tariff uncertainty results in choppy nonferrous scrap flows
- CATL, Ellen MacArthur Foundation establish battery partnership