Original equipment manufacturers (OEMs) that need a steady supply of recycled resin do not always have good choices. The prevailing method is to establish good relationships with one or more suppliers of recycled resin. But, it seems like the entire world is clamoring for more recycled resin, and traditional recyclers are caught between a generally inadequate collection system and increased demand for their products, plus a delivery system that can be problematic.
The results can be fluctuating prices, uncertain delivery schedules, uneven material quality and little ability to ramp up supply when demand increases. The unfortunate recyclers cannot solve all those problems.
Some OEMs have a different solution. By recycling in-house, they take on the responsibility to source and reprocess recyclables in return for greater control over their resin supply chains. This circularity model can be a good business practice and a strong sustainability process that benefits the OEM as well as its customers.
I had an opportunity recently to visit plastics processing companies that also are recycling plastic for their own products and have been struck by how easily the reprocessing operation can fit under the same roof as injection molding, thermoforming and extrusion machines.
Monoflo International Inc., a manufacturer of reusable, injection molded transport products, such as bulk containers, pallets and totes, recycles up to 3 million pounds per month of polyethylene terephthalate (PET) and polypropylene (PP) at plants in Winchester, Virginia, and Ottawa, Kansas. Monoflo’s reprocessing operation provides about 20 percent of the total content for its products.
Axjo America injection molds spools and reels for wire, cable and other products entirely from recycled resin. It recycles that resin in Axjo’s injection molding plant in Conover, North Carolina, processing about 730,000 pounds of polyethylene and PP resin per month.
Placon, a manufacturer of thermoformed clamshells, trays and blister packaging, processes 120,000 pounds of PET bottles per day into recycled PET flake in a building next to company headquarters in Madison, Wisconsin. All the flake goes into Placon’s packaging.
Why did these plastics processors become plastics recyclers?
“We were sourcing flake from all over the world, and it just really wasn’t meeting our quality requirements,” Dan Mohs, Placon chairman and CEO, says in the Winter 2020 issue of Plastics Recycling. “That caused us to look at technology to build the recycling facility.”
At Axjo America, in-house recycling gives the company better control of its manufacturing process, including availability, quality and price of the recycled resin. It can control the resin’s melt flow, viscosity and material variations.
All three of these companies must work hard to source the material they need, but that has just become part of the business.
Will more companies take this approach? As processors need more and better recycled material to meet their customers’ or their own needs, it is a viable option.
Get curated news on YOUR industry.
Enter your email to receive our newsletters.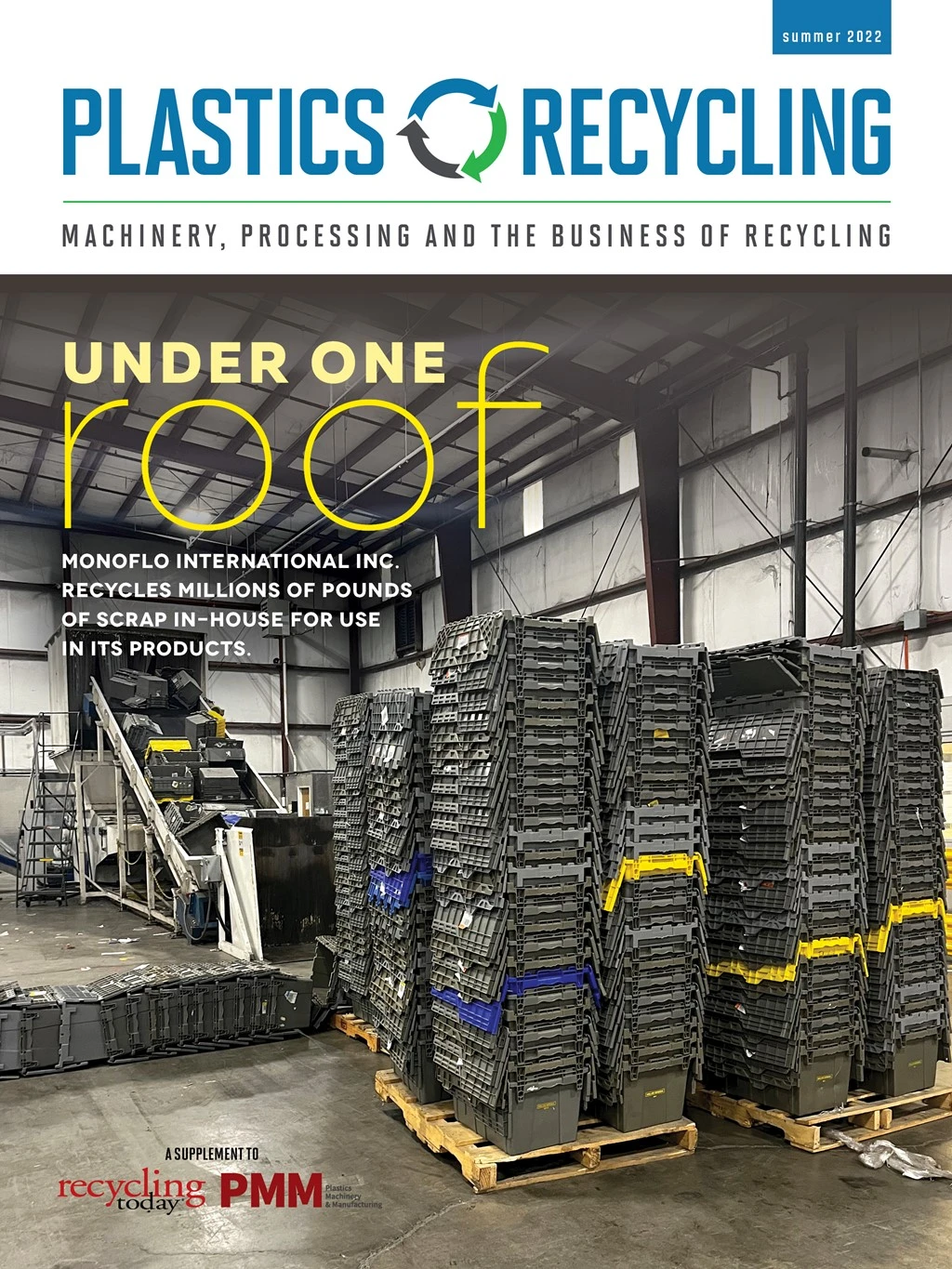
Explore the Summer 2022 Plastics Recycling Issue
Check out more from this issue and find your next story to read.
Latest from Recycling Today
- ReMA opposes European efforts seeking export restrictions for recyclables
- Fresh Perspective: Raj Bagaria
- Saica announces plans for second US site
- Update: Novelis produces first aluminum coil made fully from recycled end-of-life automotive scrap
- Aimplas doubles online course offerings
- Radius to be acquired by Toyota subsidiary
- Algoma EAF to start in April
- Erema sees strong demand for high-volume PET systems