
Photo by DeAnne Toto

With multiple machines operating at the same time and piles of materials to manage, scrap yards can be challenging to navigate, operate and maintain. With all the facets of these facilities, maintenance means more than just ensuring equipment is tuned up and the yard is clean. When safety and material containment are ignored, yards can face operational risks.
Overseeing safety
Jim Wiseman, executive vice president of Smart Recycling Management, Nicholasville, Kentucky, has 25 years of experience working in scrap yards. He says fires are one of the biggest risks the industry faces as they have the potential to halt operations completely and, at their worst, can result in fatalities. Focusing on the biggest risk areas can help reduce the hazard fires pose to scrap yard operations.
“A huge issue in our industry now is fires within scrap yards, and predominantly one might initially think that they occur just with shredders,” he says. “And while they do a lot of the time, that’s not the only risk.”
Wiseman says operators need to practice good housekeeping when storing material that is to be shredded as well as shredded material, with well-managed piles.
Additionally, shredders can throw out flammable remnants of unprocessed scrap, which is a safety and housekeeping concern.
“You have airbags and other types of things that are in the shredded product that can create that problem,” he says. “Shredders themselves are a huge, huge safety issue. And, so, the maintenance of a shredder in terms of the equipment is important, but also just everything that has to do with any part of the shredder matters, too.
“You always want to drive by in the yard car at night, and particularly in the summertime,” Wiseman continues. He says this is because auto shredder residue, or ASR, poses a fire risk and needs to be “managed and maintained correctly,” therefore “you don’t want to have more fluff on the ground to end the night.”
Wiseman also notes that the overall look of the yard is important, too. When he worked at scrap facilities, he says he would make a point to take a general look around before operations started for the day.
“Managing a scrap yard is organized confusion,” he says. With so many moving trucks, people and machinery, it can look like a mess once the day gets going and make it hard to ensure everything is in its place and ready to go.
“I liked to look at the yard when the dust was settled, either before the day started or once it was over,” he says.
Wiseman adds that operators can get a better idea of what’s going on at the yard when equipment isn’t running because there’s no noise pollution and no people around.
Additionally, one area of yard maintenance that often is overlooked is facility signage. He says scrap yard operators should consider whether the facility is easy to navigate, and Wiseman adds that it is helpful to designate an employee to monitor the yard during operating hours. He or she should be aware of the people who are in the yard and where they are going.

Machine maintenance
Routine machine maintenance is critical to ensuring a scrap yard is operating with minimal risk, Wiseman says. Shredders, which Wiseman says are a huge fire risk, also can pose a safety risk to an operator or service technician who isn’t trained or careful when adjusting or the shredder or addressing maintenance issues.
“The drum in a shredder is very heavy,” he notes. Just because the machine is powered down doesn’t mean parts aren’t moving. “When you shut that switch off, that drum doesn’t quit running. There’s inertia there that keeps it moving for a while,” he says.
Other important areas of machinery to monitor include forklifts and front-end loaders. Wiseman says he advises checking the brakes on mobile equipment every day and looking thoroughly for leaking fluid. These measures will help prevent accidents and reduce related risks throughout the workday.
To ensure everything is being looked at closely day to day, Wiseman says a formal, written maintenance plan is useful. He adds that a yard where he was previously employed used a checklist system for each piece of machinery.
“If there was a piece of equipment an operator was supposed to use, let’s say a crane, … the operator had a checklist for that machine to fill out before using it,” Wiseman says.
Checklists at that yard included everything from ensuring that all the lights worked to checking brake functions and looking for fluid leaks.
He adds that no machine is any less important than the next when it comes to ensuring proper maintenance.
“One machine can bring down three other pieces or create a bigger problem,” he says.
Other large pieces of equipment, such as horizontal balers, should be checked daily before use to ensure nothing is malfunctioning or broken, Wiseman says. The environment around the machine also should be examined to ensure it is safe to operate in. This helps to prevent safety and financial risks, he says.
“If you’ve got a piece of equipment that processes materials, it helps you make money and prepare material to go to the market. If that piece of equipment is down for a long time because it was not maintained properly, that’s a loss for you,” he says. “It hurts everybody. It doesn’t just hurt the operation where it occurred.”
A supportive culture
Companies should view safety, maintenance and risk mitigation as vital to their operations. Wiseman says it all starts with a good company culture. “You follow your owner or yard supervisor,” he says. “If the guys in charge act like an issue isn’t that important, that’s an issue in my book.”
A company culture that ignores small maintenance and safety issues can evolve into ignoring larger maintenance and safety issues down the line, which affects a scrap yard’s profitability and could put employees at risk. For example, a smaller issue like an overlooked leak can spiral into a bigger issue with equipment down the line if the operator continues to ignore it. “Now, all of sudden, that equipment can’t make any money for [them],” he says.
“It all goes back to that organized confusion,” he continues. “You can’t do anything about the trucks that are running all over the place. You can’t do anything about the cranes and the equipment and the people, but it has to be at least organized.”
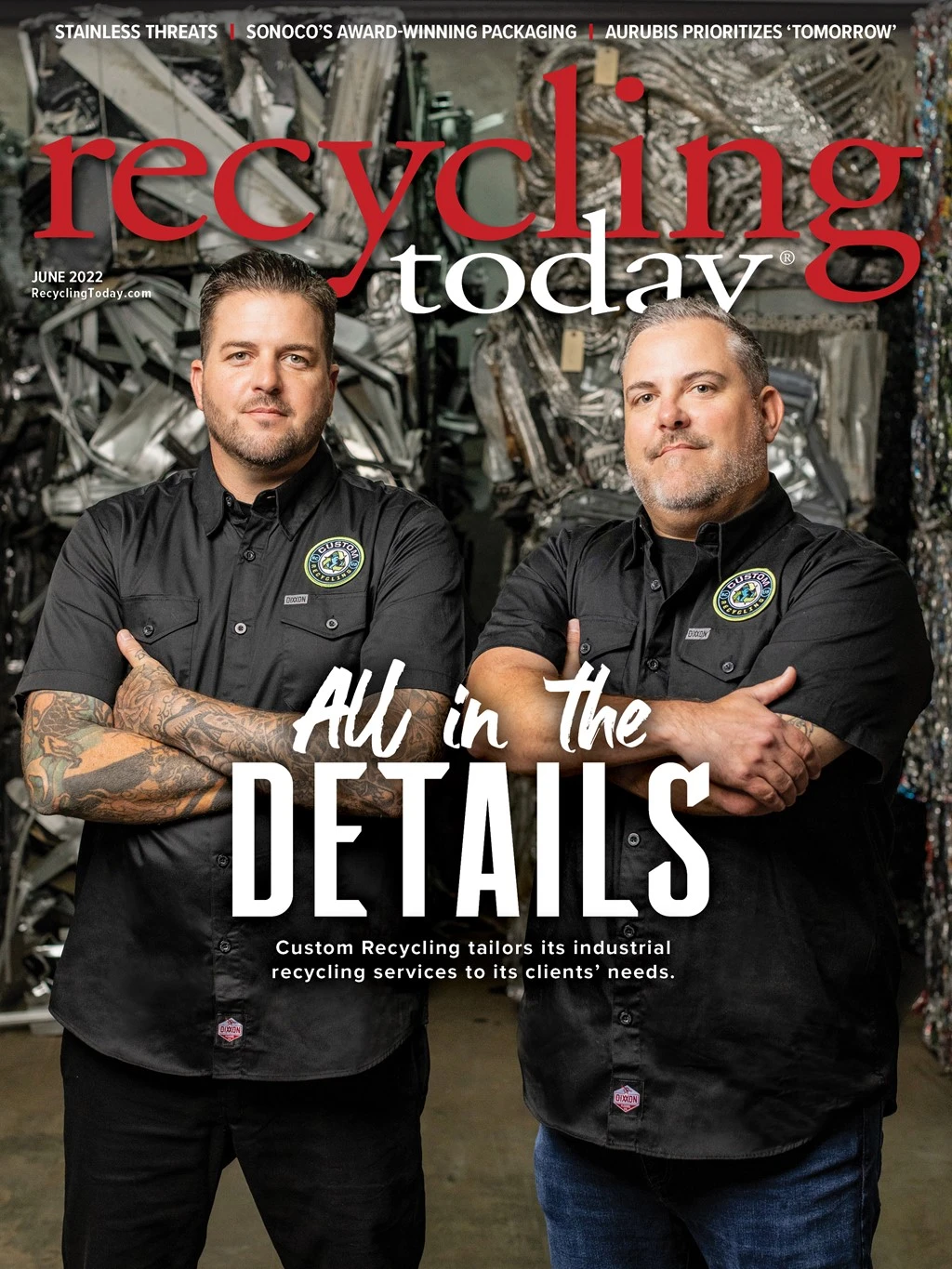
Explore the June 2022 Issue
Check out more from this issue and find your next story to read.
Latest from Recycling Today
- ReMA, Germany’s VDM issue joint tariff statement
- Singapore EAF melt shop idled
- LME reports healthy trading volumes in Q1
- Hyundai adds dealer in Wisconsin
- Study finds recycling symbols largely recognizable
- Reworld announces executive leadership transitions
- Longtime paper industry veteran announces retirement
- Aurubis CEO says its metals play vital role