Those who are tempted to think that change is a distant force that cannot be shaped by them personally should probably have a chance to meet Sam Proler.
Proler, 90, is part of a Texas-based family that played an instrumental role in the hyper growth of the ferrous scrap industry in the 1940s, ‘50s and ‘60s.
Although he stepped away from the industry more than three decades ago, some of the projects that Sam spearheaded made critical changes in the scrap and electric arc furnace (EAF) steel industries that are still evident today.
MAN AND MACHINE. Obsolete automobiles have been considered worthy feedstock for steel mills and metals smelters for decades, but their journey from their final parking space to the furnace has changed dramatically.
When Sam was active in his family’s Houston-based scrap business in the late 1940s, harvesting the scrap from autos was a labor intensive process. Torch-cutters and smaller alligator shears were commonly deployed at that time.
Life After Scrap |
Since stepping away from the scrap industry in 1969, Sam Proler, now 90, has lived a long and productive life. After decades of criss-crossing the country to help the family business grow and spread the Prolerizer process, Sam opted for a rural setting for his retirement years, spending much of them at his ranch in the Lake Conroe area in East Texas hill country. Occasionally, he used to be tempted to get back into the scrap industry, including a shipbreaking venture that he considered. Additionally, he has purchased properties to maximize the liquidation value, including a gun barrel plant purchased for $3 million whose equipment and scrap he was able to sell for $10 million. And for a time, Sam tried his hand at cattle ranching, but quips, "They were eating me up instead of me eating them up." He now uses some of his land to grow citrus fruits and tomatoes, but says he devotes as much of his time as possible to his family. "I like to invite relatives and friends from all over to come here," states Sam, who also notes that he celebrated a second bar mitzvah in coordination with his 90th birthday. |
At the Ford steelmaking plant, obsolete autos were baled one at a time and then fed to an open-hearth furnace. "The idea didn’t work," says Sam, noting that Ford wasn’t taking advantage of the full capacity a baler could offer, nor was it necessarily removing impurities sufficiently.
By the end of the 1940s, Ford Motor Co. sent out letters to scrap companies throughout the United States offering to sell the baler, and according to Sam, he was the only one of 1,300 dealers who showed enough interest to fly to Detroit and see the baler. He purchased it with the intention of making some upgrades.
"I modified it to address their practice of putting only one car in at a time," recalls Sam. "I put a hopper on it and placed a ramp on either side of the hopper. Then trucks could back up and tip a load of whole cars at one time."
While touring the Ford Rouge steel complex, another machine caught Sam’s eye. "They were using an old slag-breaker and also selling that. I bought it for $10,000—which was a lot of money back then, especially when scrap was only $13 per ton and labor was pretty cheap too," Sam remarks.
But Sam believed that the guillotine-style slag breaker could prove ideal for preparing structural scrap and, after making some modifications to the design, he was able to sell it to a scrap processor in the Eastern United States for $60,000.
In modifying both machines, Sam points out that he had to do the design and fabrication in-house with spare parts and sheet metal culled from the Proler Steel Corp. scrap yard. "It wasn’t a case of picking up a phone and calling a vendor," he comments.
As a direct result of his one trip to the Rouge steelmaking complex, Sam says he was able to help introduce two significant new scrap processing upgrades that helped lead the scrap industry into a new, automated era.
Although torch-cutters and alligator shears can still be found in scrap yards, when a company sets up a ferrous scrap operation with the intention of handling a healthy amount of scrap, either a baler, a shear or a combination unit is soon on the job.
Sam was not finished putting his energy into new processing methods, however. The Proler family’s greatest contribution to scrap processing automation was yet to come.
A BUNDLE OF PROBLEMS. The cliché that a problem is only an opportunity in disguise can be an inspiration to some, but it can be difficult to embrace for others who are in the middle of a vexing problem.
In the mid-1950s, Sam Proler and his family’s scrap company, Proler Steel Corp., had a problem: They possessed some 40,000 tons of No. 2 auto bundles but were seeing an absence of interest from steel mills in their product. "Most steel mills didn’t want them—they had too many contaminants like copper and rubber," says Sam.
A Verb is Born |
When last names become attached to an object or an action that causes them to become everyday words, that can be good (the Heimlich maneuver saves lives, for instance), or perhaps not so good (military officer Benedict Arnold would probably be less pleased to find out how his name is commonly used). In scrap circles, the Proler family was able to turn its name into a trademarked word that has lived on thanks to a 45-year-old patent. Two years after the Proler Steel Corp. applied for a patent for the automobile shredder it designed, the company filed for another patent that allowed him to claim a trademarked name for the process. In 1962, the word "Prolerized" was trademarked to the Proler Steel Corp., three years after the company wrote to the Patent Office to use the term to describe the scrap created from its new processing method. The inspiration for the name? "I got the idea from a bottle of milk that said ‘Pasteurized,’" Sam recalls. |
On a flight from a Kennecott Copper facility in Utah to Omaha, Neb., Sam recalls drinking screwdrivers and trying to think through this problem when the idea of deploying a hammermill on entire automobiles came to him. "I asked the stewardess for paper and a pencil and started sketching what this thing would look like," Sam recalls.
Such mills were used widely in mining applications, and scrap companies, including Proler Steel Corp., were using similar machines to crush grades such as turnings and steel can scrap before it headed into the de-tinning process.
After Sam landed in Omaha he couldn’t wait to tell his brothers Israel (Izzy), Hymie and Jackie, and was equally eager to contact equipment suppliers who might want in on his idea of running whole automobiles through a hammermill.
Sam says he soon approached existing manufacturers of hammermill-style crushers to see if they would be interested in fabricating his automobile shredder.
One manufacturer "said they could build one if the car is quartered and the motor is removed," Sam recalls. But that didn’t match Sam’s vision. "That’s going back to the blacksmith era, chopping with a hammer and cutting with a torch," he states.
"They kept telling me why it wouldn’t work," says Sam of his discussions with potential suppliers at that time.
Eventually Sam found a machine shop willing to work with drawings he supplied to them to fabricate custom parts, while he says he used scrap from inventory to fabricate other parts of his first auto shredder.
"We started in 1956 and it took about a year to build it," Sam recalls. "We built it near the Southern Pacific railway tracks in our Houston yard and used mule power to help us dig the ditches for the foundation," says Sam.
The mule played a part in a new machine that was about to bring rapid changes to both scrap processing and steelmaking.
CHARGED UP. The Proler automobile shredding process, which received a U.S. patent in 1960, worked exactly as Sam had hoped.
Some upgrading and experimentation naturally took place during the process. "Our first motor was a 2,500-hp motor, and it really wasn’t powerful enough," says Sam. "The rotor really slowed down every time we dropped a car in there."
The next step up was more like a leap. "I bought a 6,000-hp motor that had been in a Navy destroyer escort that was being scrapped. It was 10 feet in diameter and weighed about 25 tons," Sam recounts.
The production of ferrous scrap created from shredded automobiles had begun, and steel mills liked what they were seeing. "Just a year or two later, the people running the Armco mill in Kansas City wanted one there. They gave us the money to build that plant and they wanted the scrap as feedstock," he recalls.
Electric arc furnace (EAF) steelmakers were especially hungry for the new shredded grade. In addition to potentially hiding contaminants, bundled autos (or baled scrap in general) caused other problems for EAF steelmakers. "Those bundles were bulky and left a lot of unfilled space in each charge. They would have to put in four to five charges to get a melt in those days," says Sam.
And two more problems: Expensive EAF electrodes were also prone to snapping and breaking if they were pressed against a charge made up of bundled scrap; and those same bundles, if dropped into furnace at the wrong angle, could break the expensive refractory lining.
Shredded scrap helped provide an answer to all of these dilemmas. "As a dense charge, it could increase melting capacity by 35 or 40 percent," says Sam. "You’re talking about big money, not even considering the savings from less electrode and refractory breakage."
Additional customers and joint investors began arriving in Houston to visit the Prolers and get into the field of Prolerizing, as a 1962 patent and trademark filing dubbed the process of shredding whole automobiles. (See sidebar on p. 176.)
The Hugo Neu Co. and representatives from one of its Japanese steelmaking customers visited the Prolers and eventually signed a deal to bring Prolerizing to Los Angeles, where a Prolerizer was deployed and ships were loaded with product and sent to the Japanese mills. Prolerizers were also built in Jersey City, N.J., and Everett, Mass., in part so Hugo Neu Co. could serve additional overseas steelmaking customers.
Other scrap firms throughout North America, some of whom may have scoffed at Sam’s idea initially, soon began designing and building their own plants. "They found out we weren’t as crazy as they thought we were," says Sam. (More information on the growth of auto shredding can be found in the article "A Better Idea," in the January 2002 issue of Recycling Today.)
Throughout the rest of the 1960s, Sam helped install Prolerizer plants in different parts of the United States, as well as helping install one for a 400-year-old scrap company in London, at a location near a Rolls Royce factory.
In 1969, after spending four decades in the scrap industry (starting in his teens), Sam exited the scrap business. He has not completely forgotten the industry, and visited the former Proler Steel Corp. plant in Houston (now owned by French scrap company CFF) three years ago. "I feel fortunate that I’m still going strong at age 90," Sam remarks.
His retirement has been full of other activities (see sidebar on page 173), but he still takes pride in his critical role in not only changing how scrap is processed, but he believes also in helping the United States EAF steelmaking industry become stronger and more profitable.
Some 50 years after Sam’s first experiments with shredding, there are now more than 220 auto shredders in the United States alone, and shredders are dispersed throughout the rest of the world as well.
In addition to providing shredded ferrous scrap to steel mills, the same plants now deploy increasingly sophisticated downstream equipment to make sure that the copper, aluminum and other metals contained in obsolete automobiles, refrigerators, washers and other appliances is directed to the nonferrous metals industry.
As a scrap processor, Sam took a 12-week course in EAF steelmaking to try to more fully understand how the mills used the scrap that the Proler family shipped to them. "They clearly needed high-quality dense scrap, and the Prolerizer process addressed that," says Sam. "I’m proud that I was able to do a lot of innovative things, and I’m really proud to have helped American industry the way I did."
The author is editor-in-chief of Recycling Today and can be contacted at btaylor@gie.net.
Get curated news on YOUR industry.
Enter your email to receive our newsletters.
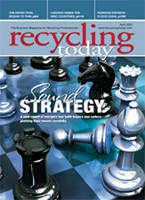
Explore the April 2007 Issue
Check out more from this issue and find your next story to read.
Latest from Recycling Today
- ReMA board to consider changes to residential dual-, single-stream MRF specifications
- Trump’s ‘liberation day’ results in retaliatory tariffs
- Commentary: Waste, CPG industries must lean into data to make sustainable packaging a reality
- DPI acquires Concept Plastics Co.
- Stadler develops second Republic Services Polymer Center
- Japanese scrap can feed its EAF sector, study finds
- IRG cancels plans for Pennsylvania PRF
- WIH Resource Group celebrates 20th anniversary