New York's Taylor Recycling Facility LLC creates a showcase mixed C&D recycling plant.
It all started with semantics. Taylor Tree Service, located near Montgomery, N.Y., about 100 miles north of New York City, was quite contentedly processing land-clearing debris and turning it into mulch and related products, and had been doing so since 1956.

But in 1989 the New York state law changed, and the definition of C&D waste now included land-clearing debris. All of a sudden Taylor unexpectedly found itself in the C&D business.
The family-owned company, not afraid of a little expansion, decided to dabble in more of the C&D waste stream and began doing some simple "dump and pick" recovery from construction waste. Taylor’s goal was to remove material that might hurt the tub grinder making the mulch. But that little bit of sorting led to more scrutiny of the operation by the New York Department of Environmental Conservation (DEC). Debates sometimes turned to disputes between the DEC and Taylor, which had since changed its name to Taylor Recycling Facility LLC.
The two entities were not getting along. Sometimes these types of disputes have ended with lawsuits, administrative actions, recriminations, arrests and even plant closings. But this story, though far from a fairy tale, continues with Taylor developing a new, more technologically advanced mixed C&D sorting and processing facility with a state-of-the-art environmental protection system that has absolutely no impact on the local environment. This gets the DEC off the company’s back (of course, never all the way).
The new Taylor recycling facility sits on 30 acres of industrial property in Montgomery, which is near Newburgh. The entire site has been graded so that the contours of the area decrease toward the center of the site. In other words, the perimeter is the highest point, and the middle is the lowest. There is only one inlet for water onto the site, and only one outlet, in the center. A carefully designed leachate filtration system makes sure that all leachate water leaving the site is cleaner than what enters the site.
In addition, all processing of mixed C&D at the operation is done inside a building. The 35,000-square feet building is outfitted with a misting system that controls the dust inside almost to a level equal to that of outside air. Material is tipped on a concrete pad inside the building. Almost all the finished products are either stored under-roof or live loaded into trucks for delivery to customers.
There is no stationary diesel engine in the plant, in order to comply with the Clean Air Act.
James W. Taylor Jr., president of Taylor Recycling Facility, says the company did all the environmental work voluntarily, "to ensure to ourselves that this is a safe, clean operation."
Tom Kacandes, who worked at financing many recyclers in New York State before developing a wallboard recycling company that now operates on the Taylor site, says that before the new facility, "Taylor had a typical operation, and was looking to expand it. We avoided a series of issues by setting up the operation indoors. Now, in terms of what is in the regulations and what is in the law, the DEC can’t touch us."
The Upgrade
It is indeed difficult to touch the new processing operation Taylor Recycling has installed. The system is very simple, according to Jamie Taylor, managing partner. Trucks with mixed C&D pull onto the site and are weighed and inspected for non-acceptable contaminants. They proceed down to the concrete tipping floor inside the building where about 20 workers use the new processing system to sort the waste.

There a Taylor employee helps them get the roll-off dumped or the tailgate opened, all the while giving the load another once-over. Separated, clean concrete, wood or gypsum are sent to specific processing areas separate from the mixed C&D.
The material on the tipping floor is fed with a grapple-attached excavator onto a 6-feet by 20-feet fingerscreen made by Erin Systems, Portland, Maine, to separate out the unders. These fines travel to the end of the line on a conveyor where they are blended in with otherwise unrecyclable materials already ground up to make an alternative daily landfill cover (ADC).
After the fingerscreen, the overs travel up an inclined belt and go through a 10-station, enclosed picking station with a 60-inches-wide belt, again from Erin. The first thing pulled is garbage, the sheets of plastic and carpeting that did not get picked out by the excavator on the tipping floor.
"Anything that would hurt our ADC product is removed," says Jamie Taylor. The rest of the stations are looking for metals, concrete, clean sheet rock, cardboard and clean wood. The wood is placed on a separate, 48-inches-wide conveyor and sent to a wood bin inside the plant until it is trucked to the outdoor mulching operation.
"Anything not picked off the conveyor goes directly into the grinder," says Jamie Taylor. The 500-hp grinder is from West Salem Machinery. "Everything is ground to two-inch minus and sent on to an 18-feet-long starscreen deck for further sizing." From there the unders material joins the other unders conveyor from the front of the system, while the overs are re-circulated to the grinder.
Two magnetic separators, one inline by the grinder and one cross-belt on the conveyor to the stardeck, also remove ferrous metal.
As mentioned, the ADC can go on the concrete floor or be live loaded by the truck drivers. A camera is placed high in the loading area, and each of the Taylor trucks has a wireless video screen in it. The drivers just push the button to reverse the conveyor for ADC and use the video screen to know when to move the truck forward to fill the bed level.
The plant is capable of processing 50 tons per hour, although Taylor has been running it at about 40 tph.
Jim Taylor says the plant has only about a three percent residual rate, although about 50 percent of the plant’s production has been for ADC for a municipal landfill north of the plant. Taylor says the company is new to this level of C&D processing and considers ADC just a bridging material to additional higher- profit, added-value products as the company becomes more familiar with the equipment and develops new markets.
Gypsum Recycled Here
One material Taylor is doing something with today is gypsum. Separated by a wall and permitted separately is a drywall recycling facility operated by TKM Materials, which Kacandes founded with partner Ken Mogul. TKM has an exclusive contract with U.S. Gypsum to supply gypsum reprocessed from scrap wallboard.
"It’s a proprietary process we created for that market," Kacandes says. The process is relatively simple, with the basic machinery being a modified mill, paper separation equipment, and air suction system to help control dust in the totally enclosed building. Obviously, unlike the C&D area, there is no misting to keep down dust. But maybe the most important component of the system is the beneficial use determination (BUD) TKM got from New York State in order to sell the material to USG.
"In New York, unlike nearly everywhere else, BUDs are for specific customers, not by market," says Kacandes. He reports that USG is very satisfied with the product being supplied back to their wallboard plant. "We started with the spec they gave us to meet, and we exceeded that spec by more than 100 percent. If we had several hundred thousand tons of this material, it would be all sold."
Kacandes says that it is profitable to recycle gypsum, but "it is not a wildly profitable niche because we are competing with landfilling, and in New York there is no functional regulatory preference for recycling of C&D."
Keeping the gypsum out of the ADC product has other advantages, both in marketing and environmentally. Waste wallboard in landfills may be the cause of the growth of gypsum recycling sector of the industry. Gypsum in a landfill can eventually cause hydrogen sulfide gas, one of the worst smells in the world. In fact, at high enough levels it is considered a hazard to human health.
Jim Taylor says, "Any manufacturer who makes a product has to be concerned with the end disposal of the product. In New York, if a site has become hazardous for any reason, and it can be identified whose product went into the site, then that party is now partly responsible for its clean up."
Wood Work
Taylor Recycling Facility cut its teeth on recycling wood, and that is still a leading activity today. The state allows recyclers to process "unadulterated" wood into mulch and higher-end products.
Jim Taylor estimates that in 2002 the facility will use its Diamond Z tub grinder, which works outdoors in a separate area from the C&D center, to produce nearly 30,000 tons of mulch, in a variety of styles. A Becker-Underwood colorizer is utilized to make red mulch, a hot seller in the region.
The dirty wood, as well as asphalt shingles, is left on picking belt line in the C&D processing area and sent through the grinder to make ADC. The product has a Toxicity Characteristic Leaching Procedure (TCLP) performed on it once every 3,000 cubic yards, checking for high levels of any of 60 compounds. "This kind of checking does a couple of things," says Jim Taylor. "It gives us a position of strength when dealing with regulators because you know the true composition of your material, and it guarantees our success for tomorrow."
One future project being looked at is the addition of a clean fuel burn plant to power the entire recycling facility. "A $12,000-a-month electric bill will get you thinking that way," jokes Jim Taylor. But there is a serious side to the idea, as there has been a push nationally to promote green energy, and an electric transmission line runs along the site, allowing for hooking onto the grid.
Very little concrete ordinarily is found in the construction waste stream; it mostly comes from demolition. Before the installation of the new processing system, Taylor Recycling Facility mostly did dump and pick to recover materials.
That process lends itself more to construction than demolition waste. But roadbase that meets NYDOT spec for Item 4 is another product Taylor Recycling now sells, and probably will handle more in the future as more demolition material comes in.
Currently the operation contracts out its crushing because that is the most economically feasible manner to get the product made.
Roadblock
Jim Taylor is bullish on C&D recycling’s future. "I am a firm believer that we as a society can accomplish 100 percent recycling of C&D material," he says. And his company has put its money where his mouth is by installing the new plant. But he does see some roadblocks.
First is government. Taylor Recycling Facility did receive what amounts to a $500,000 grant from the state to help with its equipment purchase. Also, the Montgomery site easily has one of the most advanced systems of environmental protection. Yet he says the environmental enforcers continue to ratchet up the standards the Taylor plant has to meet, all the while not requiring other recycling facilities in the state to get to his plant’s level.

But he also points that regulatory agencies seem overly concerned with C&D’s impact on public health. "If our industry was having any kind of an effect on the environment, we would see it in our employees first," he says. "We have had people here 10, 11 years, and they are all healthy. Granted, there may be rare exceptions in the overall general public, but we feel C&D is safe to those working around it."
Tom Kacandes adds another angle to the government’s role. "One of the regulatory inefficiencies you have right now is that the more you handle waste, the more regulatory attention you draw. So you have more regulatory cost than if you just slam the stuff into a truck and send it off to another state’s landfill. This is a disincentive to recyclers. This facility is not a risk to the environment, why should it bear the same cost as a landfill, which is almost guaranteed on a scientific basis to release pollution into its environment, both during its operation and forever after its closure?" asks Kacandes.
"Landfills should be monitored more. This facility does not have mercury air emissions the way landfills that usually have lower costs do. So why is that not being regulated as an air source?" he wonders.
The waste industry, especially the landfill lobby, is another roadblock, according to Jim Taylor, whose company does have its own roll-off service. "We are the biggest competition to the people who own the holes. That’s our competition. We do need landfills, they are tools to recycling in the future." But, he continues, their lobbying influence allows them to get a respite from the constant regulation recycling is under.
The waste industry’s day will come, however, says Kacandes. "The transfer station business model is about all tapped out. They have just about exhausted all the ways to increase efficiencies, through compaction and walking floor trucks. All the while recycling’s efficiencies are only going up, and its profit growth potential is much greater."
Freight costs are "the most misunderstood and missed aspect of our business," says Jim Taylor. "It is the cost of freight that drives this business. Sometimes the cost of freight is more than the cost of the product and the processing. What everyone has to figure out is, how do you make the cost of freight work so that it makes the combined operation attractive to your customer?"
He is confident the industry will figure out that problem, and others. C&D recycling just makes too much sense, he feels. "We also are attracting some good players to our industry. There are a lot of people out there who want to make money and want to help the environment. We are pleased to be a part of that."
The author is associate publisher of C&D Recycler and executive director of the CMRA. He can be contacted via e-mail at turley@cdrecycling.org.
Get curated news on YOUR industry.
Enter your email to receive our newsletters.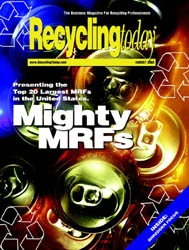
Explore the August 2002 Issue
Check out more from this issue and find your next story to read.
Latest from Recycling Today
- Athens Services terminates contract with San Marino, California
- Partners develop specialty response vehicles for LIB fires
- Sonoco cites OCC shortage for price hike in Europe
- British Steel mill’s future up in the air
- Tomra applies GAINnext AI technology to upgrade wrought aluminum scrap
- Redwood Materials partners with Isuzu Commercial Truck
- The push for more supply
- ReMA PSI Chapter adds 7 members