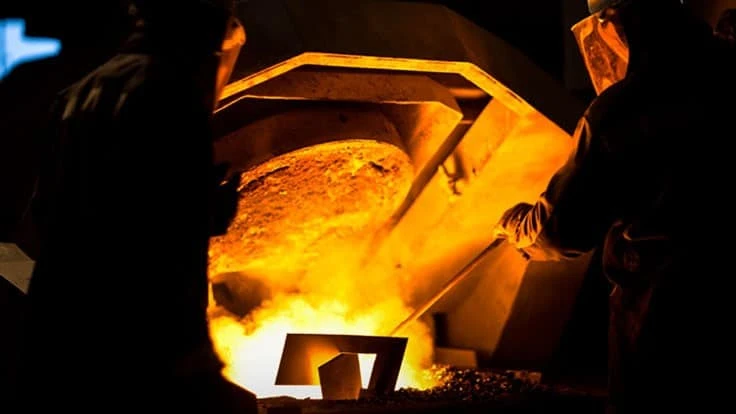
© Maksim / stock.adobe.com

China was set to announce new scrap classifications in July 2020 designed to prevent countries from dumping excess lower quality scrap metals in China’s ports. These classifications are intended to compel suppliers to eschew volumes in favor of producing higher quality scrap. However, that date came and went, and China instead decided to continue its scrap quota program that had been in place since 2019.
China eventually released its new standards for the reclassification of scrap metals Nov. 1, 2020. Despite the final announcement increasing the quality of scrap required, suppliers remained uneasy about shipping into the Asian nation as of late 2020. They say they fear material could be held up in Chinese customs and have chosen to send their volumes elsewhere in Southeast Asia or India instead.
Why the new Chinese quotas matter
China’s impact on the global metals supply chain has been significant since the turn of the century. The Asian nation’s demand in the early 2000s saw pricing reach record highs in what many in the U.S. called the golden age of scrap.
Over the past two decades, China has continued to affect the global metals supply chain, sending ripples worldwide with its latest round of new classifications for scrap metals that are acceptable for import into the country.
The new standard has a more permanent feel to it than the first iteration for this type of restriction under the National Sword policy. For many suppliers looking to meet that requirement, it took nothing more than an extra pass through their shredders’ downstream systems or an additional hand-picker on a conveyor line to correct for the change in quality.
The latest change does not seem to be an easy problem to solve, begging the question, how do suppliers adjust to the new standard?
Over the last decade, China has, on average, imported more than 2 million metric tons of aluminum scrap per year, making it the largest consumer of the material in the world. However, investing only to meet China’s requirement does not seem to make logical or financial sense for many exporters. It increases the payback period by years, depending on the size of the initial investment.
Therefore, to maximize the investment return, scrap suppliers are contemplating producing furnace-ready shredded aluminum packages that can meet China’s new classification for imports and also increase their margins when selling to U.S. smelters. As a justification for the premium, a prepared-to-charge scrap package would lower smelters’ operating costs.
The case for furnace-ready aluminum scrap
As those scrap dealers contemplate investing to produce furnace-ready aluminum scrap and create templates for their financial justifications, the question of what material constitutes an acceptable package could have many different answers. The range of responses will be determined and defined by consuming companies that melt the metal and the degree of comfort they have with outsourcing their ability to produce this type of material.
In the U.S. alone, the aluminum scrap industry accounts for around $8.4 billion in value annually. With a rough price difference of 10 cents per pound between a 95 percent zorba package and a furnace-ready twitch package, the shift to a widely accepted product makes sense for scrap yards with the capital to invest, especially with China importing approximately 2.3 million metric tons of aluminum scrap every year.
The new restrictions mean China will have less qualifying scrap available to import. Thus, demand for higher quality material will grow and justify the investment necessary to meet these new standards.
The need for investment
Some scrap dealers reject the need for large investments to produce a furnace-worthy package that meets Chinese and U.S. consumers’ requirements. Some have cited the garbage in, garbage out, mantra. They say the best way to control a shredded aluminum product’s quality is to sort the material before it enters the shredder, allowing for the most control in regulating the chemistry of the finished good.
In theory, this method can result in selling a more consistent grade and can garner the highest possible price. Using the shredder to process traditionally baled or boxed grades also increases the equipment efficiency of what is most likely the scrap yard’s most significant capex to date.
As scrap yards work through the challenge of funding their capex, many have yet to step back and look at the big picture. The U.S. economy’s capitalistic nature and the individual nature of the country’s aluminum supply chain help to increase competition, which, in turn, can raise the overall cost of bringing a product to market.
In contrast, China is working to control the supply chain from start to finish. China’s need for scrap imports will dwindle as it grows and becomes more self-reliant on its own scrap supply. Therefore, potential investments in U.S. production of furnace-ready material could become obsolete against China’s demand, adding yet another variable to the decision.
Some estimate that China will become a net exporter of scrap within five years, while most believe it is at least 10 years, if not more, away. Either timeline shrinks the ability to recapture the upfront investment. This constraint is leading many to consider more options for producing furnace-ready aluminum by taking advantage of the heavy-media plants already online or coming online in the near-term to maximize supply chain efficiency.
U.S.-based heavy-media plants estimate a capacity shortage of 1.5 billion pounds for the varying degrees of zorba quality produced at the country’s shredder operations. This gap increases the need to invest in the equipment necessary to deliver a worthwhile furnace package. The spread between a 95/2 type zorba package and twitch is encouraging and likely to help flip the switch on investing in the equipment needed to meet the new Chinese standards and the yet-to-be-defined furnace-ready U.S. standard. Since the first round of shutdowns because of the pandemic in late April of last year, the spread between 95/2 zorba and twitch has grown from roughly 3 cents per pound to more than 12 cents per pound, helping to justify those investments. Prior to the pandemic, the spread averaged roughly 10 cents per pound.
The road to furnace-ready aluminum is uncertain. If the industry could start from scratch, it would no doubt look different from what it does today. Manufacturing lines, scrap yard layouts and melting operations would be maximized to shorten the supply chain and to produce a product for the lowest possible cost with a minimal impact on the environment. Without a widely accepted definition, the market could struggle to adapt and invest in the appropriate areas for long-term sustainable growth.
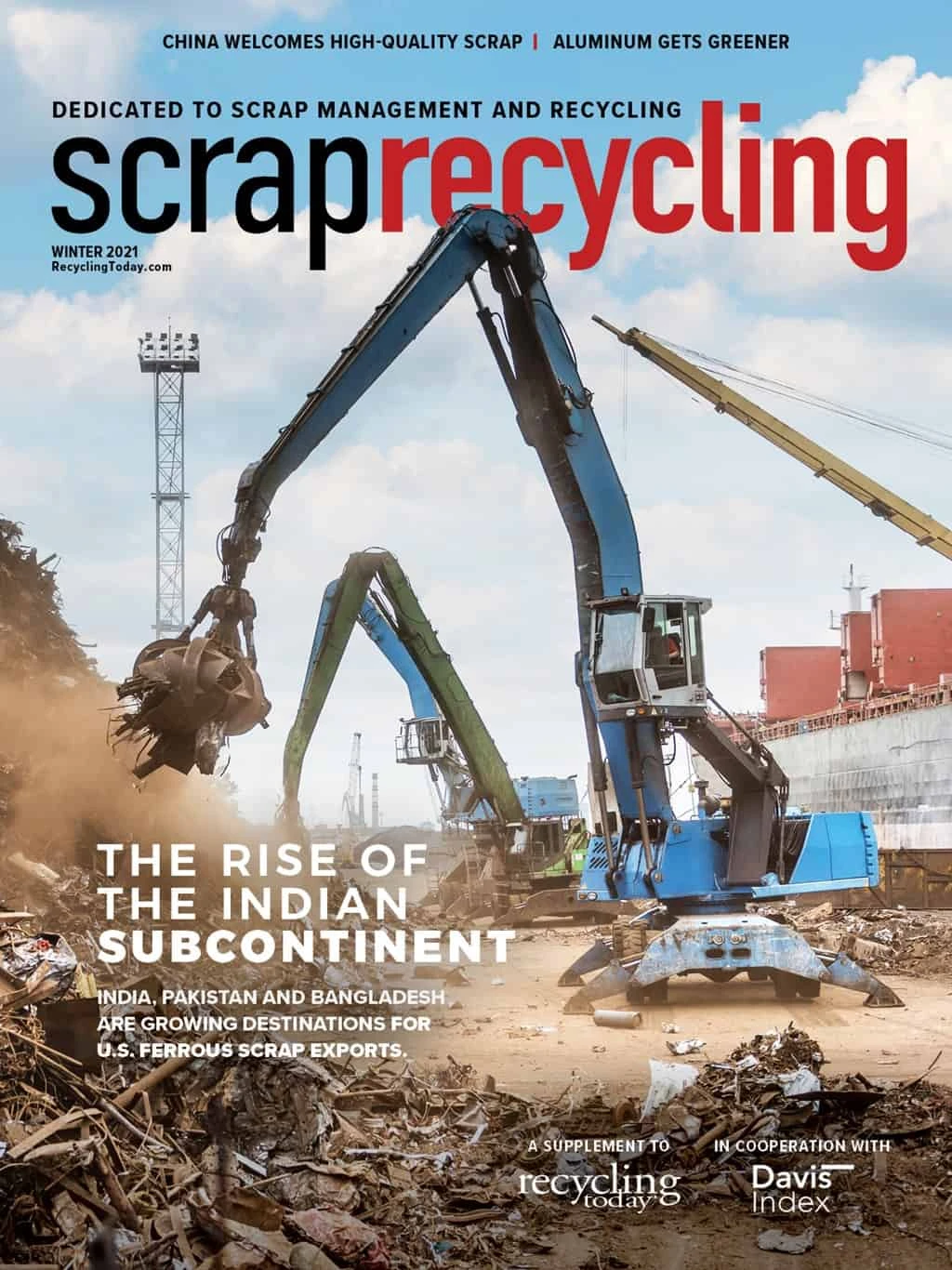
Explore the Winter 2021 Scrap Recycling Issue
Check out more from this issue and find your next story to read.
Latest from Recycling Today
- ReMA opposes European efforts seeking export restrictions for recyclables
- Fresh Perspective: Raj Bagaria
- Saica announces plans for second US site
- Update: Novelis produces first aluminum coil made fully from recycled end-of-life automotive scrap
- Aimplas doubles online course offerings
- Radius to be acquired by Toyota subsidiary
- Algoma EAF to start in April
- Erema sees strong demand for high-volume PET systems