The primary task for a baler in any application is to squeeze together loose material into one solid, shippable unit.
In most cases, the material being compressed would prefer to retain its ‘memory,’ or stay in the relaxed condition it was in before being introduced into the baler.
The shredded paper created during the document destruction process doesn’t necessarily present a major ‘memory’ problem, like more rigid material can, but many of the shreds really would rather go it alone. This results in bales that can be rough around the edges and that can leave trails of small bits of paper when handled.
The object for those operating and supplying balers handling shredded paper is to produce bales that have integrity—that is, they stay in one piece and don’t threaten to fall apart during the shipping and handling process.
FALL-OFF
The trails of shredded paper that can shake loose from a finished bale have a name within the industry: fall-off.
When an operator baling shredded paper sees a noticeable amount of fall-off, that can be a pretty clear sign that the bales being produced do not have sufficient integrity. "You’re almost always going to have some fall-off—it’s difficult not to have," says Fred Johnson, vice president of sales at baler maker IPS, Baxley, Ga.
There are several steps baler operators can take to reduce or minimize their fall-off problem, equipment suppliers say. "Depending on the size of the finished shreds, some operators put cardboard headers in front of and behind the bales," says Johnson. The ability to use this technique depends on the style of the baler, Johnson notes.
Particle size plays a role in the fall-off script. "If the particle size is too small to allow the material to knit together when compressed, the bale will not have the strength to hold together during typical handling with a forklift and transportation to the mill," says Dan Glenn, national sales manager with AES (Advanced Equipment Sales), Franconia, Pa.
Safety First |
Trade groups connected to the recycling industry, such as the Institute of Scrap Recycling Industries Inc. (ISRI), have been taking the lead on preaching safety to member companies. The past several years have witnessed increased workplace injury incidents at recycling facilities, as a red-hot global commodities market has meant such facilities are handling more material and operating longer hours. Recyclers of shredded paper are among those who need to take notice of maintaining a safe workplace, says Fred Johnson, vice president of equipment supplier IPS Balers, Baxley, Ga. He advises buyers of processing equipment such as balers to make sure the machines they are purchasing meet safety and operating standards set by ANSI (the American National Standards Institute), www.ansi.org. “Make sure the equipment meets or exceeds those standards,” Johnson remarks. Additionally, Johnson says plant managers must be sure to provide proper safety equipment, such as gloves and glasses, and enforce their use. “A shredder is a machine that cuts, and safety is first and foremost on any of this,” he states. “I highly recommend that potential buyers have that at the front of their thinking.” |
Properly matching the cylinder size to the bale cross section is the most critical element in determining the density of the bale, Glenn says, adding that using a baler that exerts formidable pressure, measured by pounds per square inch, is also required. "It is very important to make sure that the side density pressure on an open-end baler is properly adjusted to allow the ram to achieve maximum compaction and still meet the speed requirements necessary to achieve the desired production level," Glenn remarks.
Johnson says "the amount of force on the press head" is a leading consideration. "That creates the density," he comments.
Maximum density is also desirable for shipping reasons, Johnson notes. "It’s critical to maximize the weights on what you’re shipping."
Trying to make too large of a bale of shredded paper is also a pitfall to be avoided. Johnson urges balers of shredded paper to consider a smaller charge box than they would use for whole paper. "A 30-inch-by-45-inch-high box is all in all a good bale size when you’re shipping shredded paper," he remarks.
With open-ended balers, keeping bales at a manageable length is also a key to trouble-free material handling and shipping. Bales that are too long can be more prone to becoming "banana" shaped and developing bows in the middle.
"If you’re trying to achieve a 60-inch-long bale, then tie it shorter—say 58 inches or so—because the wire will stretch," advises Johnson. He says a bale tied at 60 inches could possibly gain another 6 inches in post-tie stretching.
For baling shredded paper, Johnson also recommends using soft annealed wire as opposed to high-tensile wire commonly used with two-ram balers, as it provides the flexibility that will be required when stretching occurs, he says.
Making optimum bales can also mean feeding the baler charge box properly. An important thing to consider, says Glenn, "is that the material is fed into the bale chamber such that it fills evenly and to the proper height before the ram moves forward."
The problematic properties of shredding baled paper are numerous enough that additional steps might still be necessary. "The addition of water misting into the baler feed chute can help improve the density of the bale and also help control some of the dust as the material falls into the baler," notes Glenn.
THE RIGHT TECHNIQUE
Adding moisture is exactly what happens to the tiny shred particles produced by Lockheed Martin Aeronautics Co. at its Marietta, Ga., facility.
According to Les B. Hicks, pollution prevention coordinator at Lockheed Martin’s Marietta facility, the classified information destroyed at the aerospace industry design facility must be shredded into what he describes as a "powder or cornmeal" consistency.
Documents that are securely collected "are offloaded into a chute and into a shredder" at a building on the Marietta corporate campus. "At the end of the process, there is a moisturizer that is applied, and then material is compressed and placed into 250-pound bags," says Hicks.
The compression and bagging is performed by a 25-horsepower 111-240 model baling machine made by Maren Engineering Corp., South Holland, Ill.
Hicks says the bagged shreds are recycled by FCL Recycling, based in Atlanta, after the company blends the material with whole office paper to create 1,200-pound bales that can be shipped to the Kimberly-Clark tissue mill in Lowden, Tenn.
These alliances have helped Lockheed Martin Aeronautics score environmental and bottom-line results.
"It used to be that no one wanted to tackle this process," says Hicks. "It went to the landfill before, but we get complete recovery now," he adds, crediting the United States Air Force for helping introduce the process to his company.
Johnson of IPS agrees that bagging such material makes sense. "When what you have is almost a mulch or a pulp, you need to look at bagging it or wrapping it in some form or fashion," he comments. "Otherwise, you’re going to have a tremendous amount of fall-off with that."
In addition to or as an alternative to adding moisture, using an air conveying system can also help to minimize the negative effects of dust that can plague the shredded paper environment.
"The smaller the particle size, the more material that will slough off the bale during handling, creating housekeeping issues," notes Glenn.
Operators face a challenge "controlling the dust generated during the dumping, shredding and conveying of the shredded material to the baler," Glenn says.
Air conveying or vacuum systems are commonly found at printing plants where paper cutting and trimming takes place and they can also make sense at shredding plants and at baling plants where shredded paper is handled. Shreds sucked in and conveyed by such systems can be directed to a smaller baler for maximum cost efficiency, IPS’s Johnson notes.
The positive results of using mist or air vacuums can tie into workforce health, fire prevention and the housekeeping and appearance of an operation.
Employing additional mechanical systems also means making sure employees understand them, Glenn advises, commenting that this is even the case when installing a new baler.
"Keep in mind that even if the baler has been properly sized, it will not function properly if the technician who starts up the baler is not properly trained and experienced to adjust the baler to achieve maximum results," he remarks. "The proper training of the operators and maintenance personnel is also critical in ensuring the proper operation of the baler for years to come," Glenn adds.
Very few suppliers or operators will claim that baling shredded paper is an art that can be perfected. But with the right attention and some capital investments, bales of shredded paper with lasting integrity can be produced safely and consistently.
The author is editor of Secure Destruction Business and can be contacted at btaylor@gie.net.
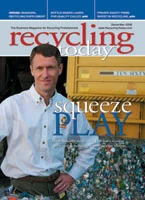
Explore the December 2006 Issue
Check out more from this issue and find your next story to read.
Latest from Recycling Today
- NWRA announces 2025 Driver of the Year, Operator of the Year winners
- The Scrap Show: Nanci Schuld of FE Trading Group LLC
- Call2Recycle Canada partners with RLG to advance battery collection
- Report delves into recovery opportunities for food-grade polypropylene
- Reimagining Supplier Payments in Metal Recycling: A Digital Leap Forward
- STEINERT Lithium Battery Detection and Removal from Waste Streams
- Driving the Future: Innovations in Waste & Recycling Technology
- Robin Wiener recognized for recycling leadership