Buddy Himes of Himes Service Co., based in Waco, Texas, has spent the past three decades either helping recyclers to avoid production problems or correcting existing problems for them if it’s too late for preventive equipment maintenance.
In his role installing, maintaining and servicing recycling equipment at paperstock plants and material recovery facilities (MRFs), Himes also has become convinced that good housekeeping is a critical part of maintenance and production efficiency.
In a presentation he has at times given to recycling companies and at recycling industry events, Himes touches on several aspects of plant maintenance.
AVOIDING BALER BLOWOUT
As much as the ultimate cost savings of maintenance is preached, Himes says he still receives questions that cumulatively lead to the question: "Is maintenance a bad word?"
He says some comments he receives along this line include:
• From production managers—I don’t like it but it’s necessary.
• From maintenance people—The first thing that gets cut is the maintenance budget.
• From maintenance people—I just don’t have enough time to do preventive maintenance because I’m too busy repairing broken down equipment.
Why else might maintenance be considered a "bad word?" Himes says other reasons he hears include added cost, the struggle to find qualified personnel to perform the work and the cost of inventorying spare parts.
Hiring an employee just for maintenance may not be sustainable, or, if one is hired, he or she may begin to take on other tasks that soon get in the way of the ideal maintenance schedule, Himes says.
"All these are valid statements and need to be addressed," he says. The good news, according to Himes, is that while "none of the basics [of maintenance] are new, technology and experience have helped us to work on the problem a little smarter."
And certainly, the pitfalls of ignoring maintenance remain severe, Himes says.
Regarding balers, Himes starts with shear knife clearance. "The knife blades on most balers should have a clearance between blades (called the gap) of one-sixteenth of an inch or less. If the blades are allowed to form a greater distance between them, it can cause severe damage to the baler."
Himes gives an example. "The force on the face of the platen (gather or main ram) is determined by the size of the cylinder, hydraulic pressure applied and the square area of the face. If brand X baler has a 12-inch main ram cylinder at 3,500 psi (pounds per square inch) and a 60-inch-by-30-inch (1,800-square-inch) face, it can develop 266 pounds per square inch on that face. If the gap is too large and a piece of material 1-inch square is wedged between the blades, it could point load the platen. All of the force that would normally be distributed over the complete face of the platen would now be directed to one spot."
What happens then? According to Himes, "The damages that have occurred due to this scenario are:
• The floor of the baler is pushed down, damaging the structure; the cost to repair can range from $20,000 to $30,000;
• The shear beam has bent up, and bolts are broken; the cost to repair is $40,000 to $60,000;
• The walls are bent in at the top as well, and the shear beam bends up; the cost to repair is $70,000 to $100,000."
He adds, "The downtime to order parts and do repairs may not be calculated, but it’s likely to be significant."
Himes concludes, "All of the above could have been prevented by performing scheduled maintenance on the baler."
While this scenario sounds frightening in theory, Himes says it is a summation of a real situation he encountered in the field. "The maintenance program was in place but was not being done because no one had the time, and production could not be stopped."
He adds, "In these cases the income from production [is always] well below the cost of poor maintenance."
What would have prevented the catastrophic baler breakdown was shimming the blades regularly (normally a two- to three-hour process). This would have cost considerably less than the alternative, notes Himes.
PEOPLE AND PARTS
Recyclers often waver on whether to build an in-house maintenance staff at all or to largely outsource the task.
A larger recycling plant is the likeliest to have one or more full-time dedicated maintenance people. Himes says, "The number of personnel will depend upon your facility size and the number of pieces of equipment you have to maintain."
He also notes that there are alternatives to a large maintenance force, which is part of the reason why firms such as Himes Service Co. have found a place within the recycling industry.
"In some cases it is more economical to bring in outside people to do major work and preventive maintenance," says Himes. "This can be a good way to keep your permanent staff down to size and still keep your equipment in good running shape."
Regarding how much money and time to allocate to spare parts, Himes says recyclers should start with the question, "What do you really need and what has someone convinced you that you just can’t get along without?"
As warehouse managers, some recyclers make better, well, recyclers, says Himes. "I have seen some parts that were put on the shelf that went bad; they had been sitting there way past their expected shelf life," he comments, citing O-rings as a common example.
Himes has his own views on parts that really are needed on the shelf and lists the following:
• Fuses (two of each size and type);
• Nuts and bolts, especially those that can be hard to get, including some metric sizes in the United States; and
• Critical parts for wire tiers.
If experience has taught a recycler that a certain part requires a long lead time or if a part has a history of wearing out, those can also be reasons to keep something stocked, according to Himes. "Parts that have a history of breaking or being damaged easily need to be kept in stock," he adds, noting that this information needs to come from the people who are running the equipment.
GET WITH THE PROGRAM
Himes cautions, "A good preventive maintenance program involves more than just the maintenance personnel to make it work. The maintenance person along with the operations manager should plan scheduled downtime for preventive maintenance."
Only equipment that is taken care of can be part of a well-run, high-production system.
Himes cites the armed forces of the United States as having some of the best preventive maintenance plans going. Although taking all the precautions of the military "would be too costly for private use, some of the principles can be adopted," says Himes.
Among those principles: Everything is documented on each piece of equipment and vendors are located for each item before they need to be replaced. "You may never need to replace some items, but if you do, you will know where to get it and what the lead time is," says Himes.
For recyclers specifically, Himes says conveyors should be checked daily. "Check for debris around the shafts and pulleys, such as long strips of paper that can get wrapped up in gears, chains and shafts," he notes. "This can collect dirt and oil, causing the motor to work harder turning the belt. It can also be a fire hazard."
Conveyor belts can be checked for rips, cuts, broken or bent connector plates and signs of dry rot in fiber-type belts. Steel-belted conveyors can be checked for bent or broken plates, wings or cleats and the chains checked for wear on their sides. (This is also a clue that will indicate the belt is not tracking properly, notes Himes.)
"The upkeep of your conveyors is very important if you want them to last a long time," says the veteran service provider. "Most conveyors wear prematurely due to neglect."
MRFs in particular handle a variety of materials, some of which bring problems. "A lot of glass, sand, dirt and small abrasive material like that will cause conveyors to wear a lot faster than normal," Himes says.
"These and like materials cannot be separated out [before the front-of-system conveyors] in most cases, but they can be cleaned off the belt on a regular basis to help prolong the life of the conveyor," he adds. "The small material will get into hinged joints, chain linkage, bearing housing and sometime into the drive chain. By cleaning the belt off at regular intervals, wear can be reduced significantly."
PROPER DOCUMENTATION
Few people enjoy filling out paperwork, but documenting maintenance is critical in how it helps reduce costs, says Himes.
"I have been in plants where a bearing had just burned up," Himes recounts. "It was on a preventive maintenance program, and [the bearing] had been greased regularly for a number of years. But after time the preventive maintenance program was not documented, and slowly things started getting missed."
Losing focus over time is one way a program can slip. Losing a key person is another. In this same example, "A maintenance person left the company and did not tell anybody to grease the bearing at regular intervals," says Himes. "Well, the bearing lost its grease over time, got hot and burned up. It was an expensive bearing and cost a lot to replace. With good documentation, that bearing would have been greased no matter who had left."
Newer equipment with automated "smart controls" can help overcome this situation in some cases. "They have reminders to perform certain preventive maintenance functions—this is a great help," Himes comments. "Some preventive maintenance programs have been put on office computers and what needs to be done is printed out every day."
Himes says he realizes that setting up and maintaining the documentation can be difficult for recycling company managers who already feel overworked. But he states, "It is essential that good records are kept so that continuing problems can be addressed, corrected and eliminated."
Even though catastrophic failures can be a source of business for Himes Service Co., Himes is unrelenting in his message to recyclers regarding preventive maintenance. "If the equipment is checked whenever the schedule calls for, then the chance of having a catastrophic event happen is limited quite a bit. It really takes away a lot of that risk."
Equipment service provider Buddy Himes of Himes Service Co. can be contacted via e-mail at buddy.himes@himesservice.com.
Get curated news on YOUR industry.
Enter your email to receive our newsletters.
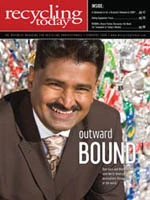
Explore the February 2009 Issue
Check out more from this issue and find your next story to read.
Latest from Recycling Today
- AF&PA report shows decrease in packaging paper shipments
- GreenMantra names new CEO
- Agilyx says Styrenyx technology reduces carbon footprint in styrene production
- SABIC’s Trucircle PE used for greenhouse roofing
- Hydro to add wire rod casthouse in Norway
- Hindalco to invest in copper, aluminum business in India
- Recycled steel price crosses $500 per ton threshold
- Smithers report looks at PCR plastic’s near-term prospects