Suspended belt magnets are large permanent or electro-magnetic separators that typically hang above belt conveyors or vibrating pan feeders in either an in-line or crossbelt position to recover ferrous metals from the material burden as it passes under the magnet. They are used in many industries to remove tramp iron or large pieces of ferrous metal from the material burden, protecting crushers and other processing equipment from damage. For the recycling industry, their task is to reclaim large amounts of ferrous material to be sold as a commodity.
Typical applications in recycling include removing sheet ferrous from automobile shredder fluff; ferrous cans from commingled household recyclables and municipal solid waste (MSW) at material recovery facilities (MRFs); iron from foundry sand; metals from construction and demolition (C&D) debris; and ferrous metals from boiler bottom ash.
Suspended box magnets for recycling are self-cleaning units consisting of the box magnet, a frame, pulleys, a motor drive, and a belt with cleats around the magnet to discharge the recovered ferrous material – hence the term "belt magnet." As the ferrous metal is attracted to the magnet, the cleats on the magnet’s belt move the iron out of the magnetic field where it is discharged (often over a splitter or divider) into chutes, roll-off bins, or take-away belt conveyors. Most belt magnets have a hemispherical shaped magnetic field, stronger in the center and weaker at the edges, which is ideal for trough belt conveyors and aids in discharging the collected ferrous material.
The box of the magnet can either have a permanent or electromagnetic element inside. Permanent magnets are built in various sizes good for suspension heights or magnet gaps of 4 inches to 14 inches, while electros are built in various sizes good for magnet gaps of 4 inches all the way up to 30 inches. Electromagnets are often preferred since they typically provide more magnet per dollar, especially at magnet gaps of more than 8 inches. The electros can also be turned off when the plant is not running or to free ferrous material if a jam occurs, making them safer in these situations.
Belt magnets provide a reasonably clean ferrous sort since they attract the steel or steel tin through gravity, allowing paper, trash or non-magnetics to fall free in the process. Magnetic pulleys, by comparison, will discharge any trash caught between the ferrous material and the pulley magnet.
MAINTENANCE
The maintenance item on belt magnets is the belt and self-cleaning system. Can lids; sharp ferrous metal; large, heavy pieces; and long angle, pipe or bars can cut, abrade, puncture, or rip the magnet’s self-cleaning belt. But measures can be taken to prolong the belt service life. Thicker belts (but not too thick or they can overload the bearings), urethane belts or urethane centerlane belts, and armor clad belts (belts with stainless steel slats and cleats bolted to the belt face) can help lengthen service life.
Since the iron gathers around the core area when it gets to the belt, only the center one-third to one-half of the belt needs to be protected. If wires and can lids are commonly processed, it may be a good idea to use molded or vulcanized rubber rather than stainless steel cleats, so that wire and lids are less likely to catch under the slats or cleats.
Also, having more belt cleats (i.e., cleats on 18-inch centers) reduces belt wear. Having fewer belt cleats (i.e., cleats on 36-inch centers) provide a cleaner ferrous sort, since the ferrous material tumbles in the magnetic field, allowing some trash to fall out before the cleat pushes the steel into the discharge zone.
Many recycling applications use picking belts operating at 40 to 60 feet per minute (FPM). In these applications, it is useful to have a cross-belt magnet installed between the belt conveyor idlers discharging ferrous material perpendicular to the conveyor belt travel. If the magnet is located over the discharge area, or "in-line", and the conveyor speed is less than 300 FPM, a non-magnetic (typically stainless steel) head pulley must be used because a steel pulley will be magnetized, lowering ferrous recovery.
In general, magnetic steel components such as chutes, framing, idlers, and pulleys should not be used within two to three feet of the magnet’s face and 1/2 to 1 foot of the magnet sides and top. Instead, non-magnetic manganese or stainless steel can be used in these areas.
Some belt magnets use multiple magnets inside the self-cleaning belt. The additional magnets clean the ferrous material by agitating or flipping it and shaking out trash. The additional magnets can also be designed to extend the ferrous discharge point, conveying ferrous material beyond adjacent equipment.
COSTS
Self-cleaning belt magnets vary in cost by the width and depth of the magnetic field required. Smaller sized permanent belt magnets can be purchased for less than $10,000; typical electro belt magnets for medium sized MRFs cost approximately $15,000 to $20,000; and larger belt magnets can cost $25,000 to $40,000 and up. The belt magnet’s advantage is that it focuses all the magnetic field generated within the box through the bottom plane or face of the magnet, allowing deep magnetic fields at reasonable prices.
If a belt magnet is undersized, this just means it is not reclaiming all of the available ferrous. Often magnetic head pulleys are installed downstream of belt magnets to remove the smaller ferrous materials. Magnetic head pulleys replace the drive pulley on a belt conveyor and are available in diameters of 8, 12, 15, 18, 20, 24, 30, 36, and 42 inches and belt widths from 8 inches to 72 inches. A small magnetic head pulley with shaft costs approximately $1,000, while the majority of magnetic head pulleys are priced between $3,000 and $8,000. Larger pulleys may cost as much as $35,000.
The author is recycling equipment manager for Eriez Magnetics, Erie, Pa.
Sidebar
Tips on Suspended Magnets
In selecting a suspended magnet (also called an overband or overhead magnet), consideration should be given to the particles to be removed, belt width, belt speed, tonnage or burden depth and the degree of troughing. Remember, this unit must be stronger and more effective on pick-up than the drums, to recover ferrous material previously missed.
The units are electrically wound for continuous 24-hour operation. In most cases, when installed up to a 10-inch suspension height, permanent magnets can do an effective job; however, when the suspension height exceeds this figure, electromagnets are better. Don Morgan, product manager, separation equipment, Walker Magnetics Group, Milwaukee.
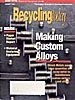
Explore the August 1997 Issue
Check out more from this issue and find your next story to read.
Latest from Recycling Today
- IDTechEx sees electric-powered construction equipment growth
- Global steel output recedes in November
- Fitch Ratings sees reasons for steel optimism in 2025
- P+PB adds new board members
- BlueScope, BHP & Rio Tinto select site for electric smelting furnace pilot plant
- Magnomer joins Canada Plastics Pact
- Out of touch with reality
- Electra names new CFO