In addition to the basic lifting magnets, belt magnets and the more sophisticated eddy current separators, there are other types of magnetic separators useful to the recycling industry. These include large diameter magnetic drums, along with electrostatic separators for metals and plastics.
MAGNETIC DRUM SEPARATORS
Large diameter (36-, 42-, 48-, 60-, and 72-inch diameter) magnetic drums have been used for many years in scrap metal yards to separate iron and steel from other materials. They reclaim ferrous materials from shredded car bodies, scrap metals, municipal solid waste, wood waste, slag, incinerator bottom ash, foundry sand, and minerals processing applications.
For example, a typical automobile shredder system uses magnetic drums to provide the initial separation of ferrous metal from a fragmentized auto, followed by a cross-belt magnetic separator and then a magnetic head pulley.
The large diameter magnetic drum separators consist of a fixed, but adjustable, magnetic element inside a heavy-duty outer shell with cleats that rotate around the element. The magnetic element is either a permanent or an electro-type. The ferrous material jumps to the drum shell where the cleats move it through the magnetic field and discharge it at the end of the magnetic arc.
The permanent non-electric magnetic drums are ideal for locations where electrical power is limited or unstable. The shell drive motor is the only electrical power required (typically 3 to 10 horsepower).
Most processors prefer electromagnetic drum magnets since they offer more bang for the buck. They are also safer since the magnetic field can be turned off when the plant is not operating or in a case of a ferrous jam. Permanent magnets, in comparison, are always on and require more safety precautions. Electro drum magnets are available in two designs: a radial pole shoe and an agitator type.
The electro agitator drum magnet uses a deep field rectangular-core pick up magnet to reach out and grab the ferrous material, and a second rectangular-core agitator to flip or agitate the ferrous, cleaning it of contaminants like loose mud, paper, fluff, and trash. A double drum scheme with counter rotation provides maximum cleaning.
Many magnetic drums are the older style non-agitating transfer design that uses a deep field radial pick up magnet and pole shoes to convey or transfer ferrous material around the drum shell to the discharge area. When used in top feed schemes, these drums will provide maximum recovery. This design can also be side fed for foundry type applications.
Steel minimills use more scrap metal than older integrated mills, but need very clean scrap containing few contaminants. The older style radial pole shoe drums optimize ferrous recovery but do not provide adequate ferrous cleaning. The all electro agitator type drum magnet cleans the steel more thoroughly. Often, retrofitting this type of drum to an existing system or mag stand will provide a product acceptable to the end user. The electro agitator design provides a cleaner ferrous from wet, sticky or muddy material. It also allows a processor to turn down the air in the air cascades and still get a valuable product.
Some electro agitator drums also provide 80 percent to 90 percent ferrous loading across the drum shell width as compared to less than 50 percent in the older pole shoe design (recognizable by the two or three shiny wear bands on the shell). This transfers more fragmented metal (frag) and lengthens drum shell life.
The smaller diameter magnetic drums typically process between 10 to 15 tons per hour per foot (TPH/F) of drum width, while the larger diameter drums handle up to 30 TPH/F of drum width. The actual rate varies with the type of product being processed.
With the variety of drum diameters and overall widths available, as well as the various options available, drum prices range from $30,000 for a smaller size drum to $100,000 for a larger drum with specialty options. While they are more expensive than suspended belt magnets, the drums’ minimal maintenance requirements (only two bearings to grease), durable construction, and longer service life make them the preferred choice in applications processing shredded car hulks, foundry sand, steel mill slag, and co-generation bottom ash applications.
By Al Gedgaudas, recycling equipment manager for Eriez Magnetics, Erie, Pa.
Electrostatic separators – separation technologies using the charging and decharging of particles for separation – have been used for some time for separating metal fractions from ore, different minerals and other products for concentrating one of these fractions. More recently, electrostatic separators have been developed for use in the scrap recycling industry.
It is possible to separate product mixtures – consisting of conductors and nonconductors – by a combination of electrostatic charging and decharging of the particles. A separation is only possible if the different product components of the product mixture are losing their charge at different speeds.
A typical application for this drum separation technique is the separation of very fine metal particles from equally fine plastic plastic by using a corona drum separator (see Figure 1). The mixture to be separated is fed onto a rotating drum with a vibratory feeder and is then electrostatically charged by a corona electrode, using voltages of 15,000 to 30,000 volts.
As a result of this charging, the particles stick to the drum’s surface due to electrostatic effects. Because of the rotation of the separation drum, the particles are then taken out of the electrostatic field and discharged on the surface of the earthed drum.
Metallic particles lose their charge very quickly and fall off the separation drum. Non-conductors (plastic particles) are good isolators. They lose their charge very slowly and stick to the drum longer. They fall off the drum at a different angle or stick on the drum surface until they are brushed off. To avoid mixing of the separated fractions, adjustable splitters are used to separate conductive and non-conductive products.
Modern electrostatic separators can be delivered with two or more separation drums in the first separation step. This allows for high material throughputs. But for physical reasons – because it is difficult to have a fine and even enough layer of material that is exposed to the corona field for long enough – separation is not usually complete during the first pass, so a second separation step is required. The system is generally set up so that the material falls directly onto a second set of drums.
For such separating units, fully automatic separation by using microprocessor controls, maximum security, transport of the separated product using auger feeders, integrated dust removal and optimum adjustability of all parameters influencing the separation results are standard.
Applications of electrostatic separators include demetallization of cable scrap, recycling of circuit boards, separation of aluminum from plastics in food containers, and recycling of automobile shredder residue (ASR).
By Dr. Rainer Kohnlechner, owner of HAMOS Electronik GmbH, Penzberg, Germany.
Plastic Separators
In addition to electrostatic separators for separating conductive from non-conductive material, there are also devices for electrostatic separation of non-conductive material. Applications in the plastics industry include removal of polyvinyl chloride (PVC) from polyethylene terephthalate (PET) flake, and removal of nylon and other plastic contaminants from various other feedstocks from both industrial and post-consumer sources.
Triboelectric separation is based on the ability of a particle to accept a surface charge as a result of a pre-charging mechanism. By making use of the different surface charges of materials in the plastics stream, the device can selectively pull away the particles to be sorted from the free-falling stream.
These systems can be set up in various ways. In one manufacturer’s machine, feedstock is introduced into the pre-charger to ensure maximum surface charging. Pre-charged particles are then allowed to fall vertically between two parallel sets of oppositely charged rotating electrodes. As the charged particles fall through the electric field, they are attracted to the oppositely charged electrode and separated. The adjustable splitter segregates the separated product streams into their respective hoppers. These machines can have capacities of up to 5,500 pounds per hour of material. By Robert Carver, recycling and plastics division manager for CARPCO, Jacksonville, Fla.
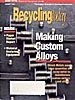
Explore the August 1997 Issue
Check out more from this issue and find your next story to read.
Latest from Recycling Today
- IDTechEx sees electric-powered construction equipment growth
- Global steel output recedes in November
- Fitch Ratings sees reasons for steel optimism in 2025
- P+PB adds new board members
- BlueScope, BHP & Rio Tinto select site for electric smelting furnace pilot plant
- Magnomer joins Canada Plastics Pact
- Out of touch with reality
- Electra names new CFO