When magnets are mentioned in the context of scrap recycling, the first image that usually comes to mind is a large lifting magnet attached to a crane, moving heavy piles of ferrous scrap. Over the years, lifting magnets have matured from heavy cast, copper wound units to lightweight, aluminum cast and fabricated units to meet the criteria of handling specific types of scrap.
The lifting magnet must be married to the cranes on which they are mounted and with the payloads they can carry. They all should be, and in most cases are, ruggedly built to withstand the physical abuse that is a normal part of their operation.
Particular attention should be paid to magnet external design, such as its case, bottom plate, lugs, chain sling and outlet box with appropriate lead wires and connectors. A typical cross-section is noted in Figure 1.
Internally, consideration should be given to the coil construction, the insulation used and the type of potting compound used to lock the coil in position. The coils of these magnets are normally wound for a 75 percent duty cycle, which means the unit will be on for three minutes out of four.
At the start of an operational day, a lifting magnet will provide the maximum lift, but after six to eight hours of operation, it will lift less. The reason is that as the coil heats, the resistance increases, providing less current and thereby reducing the magnet’s effectiveness. The magnet designer must take this into consideration, to minimize the drop.
Controllers for these magnets must be capable of handling the counter EMF voltage developed when switching to the D.C. side of the power source without damaging the coils, so select these carefully. Power take-off generators are now hydraulically driven, providing a compatible package for the hydraulically operated cranes.
MAINTENANCE
Lifting magnets are electric tools that, like other tools, require periodic maintenance to keep them in first class operating condition and to minimize costly repairs. Unfortunately, magnets are often looked upon as massive, indestructible objects and only receive attention when a problem occurs. Magnet operational problems are generally expensive, both in direct repair costs and in downtime. A regular planned maintenance program can keep problems, and their costs, to a minimum.
A regular inspection program will identify small problems and allow them to be corrected before they become big problems, allow you to plan major repair work so that it fits into your production schedule, and let you know which of your operating personnel may require additional training.
A planned maintenance program is not expensive. Regular inspections take only a short time. The program will pay for itself the first time a minor problem is detected and corrected before a major repair becomes necessary.
PRELIMINARY STEPS
Once you have committed to begin a maintenance program, some preliminary steps should be taken. Make one person responsible for managing the program. Your maintenance supervisor, yard foreman or other qualified individual should be assigned the task of overseeing the program, making sure that inspections are done properly and regularly and that necessary corrective actions are taken.
Do an inventory of your lifting magnets. Identify each by size, manufacturer, model number, serial number and date purchased. Assign your own number to your magnets. This will make future identification easier. A good way to do this is to weld the assigned number on the top of the magnet case. Gather product and maintenance information for each of your magnets. Keep the collected information in a file that is easily accessed.
Order at least a minimal quantity of parts for routine repairs. These parts should include lead sets, connectors, terminal box parts, chain pins and center pole bolts. If you have a number of identical magnets, you may wish to stock items such as center pole shoes, chains and other major items. Having these parts on hand will allow your personnel to make minor repairs quickly, saving you downtime.
Be sure that your maintenance personnel have the necessary tools to inspect your magnets and perform minor repairs. These tools should include ordinarily available hand tools like wrenches, sockets and screwdrivers. Also necessary to a maintenance program are a good quality volt-ohm meter for measuring could resistance and an insulation tester (megger) for testing coil insulation.
Organize a formal training session. Maintenance personnel, magnet operators and appropriate supervisory personnel should be included in the session. The agenda should include the "whys" and "hows" of your proper magnetic maintenance and operation.
INSPECTION PROCEDURE
Prepare a magnet maintenance log sheet for each of your magnets. Have your inspector perform a thorough initial inspection following the procedures below. Make necessary repairs immediately.
Remember: do not perform electrical tests on an energized magnet. To avoid accidentally energizing the magnet during the testing procedure, the magnet loads should be disconnected from the power cables prior to testing. Personnel should never stand or move under a lifting magnet for any reason or extend any portion of their bodies under a suspended or partially lifted magnet. To perform an inspection, the magnet should be placed on solid supports. Turn magnets upside down or tilt away from the inspector and solidly support to inspect the lower portions of the magnet.
The author is product manager, separation equipment, Walker Magnetics, Milwaukee.
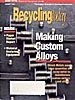
Explore the August 1997 Issue
Check out more from this issue and find your next story to read.
Latest from Recycling Today
- Gränges boosts profits and sales volume in Q1 2025
- RMDAS April figures show recycled steel price setback
- Steer World offers PEX plastic recycling machine
- New recycling grant program launches in Massachusetts
- Tire Recycling Foundation names executive director
- Dock 7 named 2025 Exporter of the Year at New Jersey International Trade Awards
- Waste Connections reports ‘better than expected’ Q1 results
- Commentary: How EPR is transforming the packaging industry