The description of an eddy current separator (ECS) sounds like the wrong answer to a science quiz: How can it use magnets to repel, rather than attract? And how can it affect nonmagnetic metals like aluminum?
Eddy current separators remove nonferrous metals such as aluminum, die-cast metal, and copper from nonmetallic material. Material is fed onto the conveyor belt of the separator, which moves it across the magnetic rotor where separation occurs. The two streams of material discharge into a housing which has a splitter to divide the nonferrous metal from nonmetallic material such as paper, plastic, wood, or auto shredder residue (ASR) – also called shredder fluff.
The key component is the magnetic rotor, which is a series of permanent rare earth magnets mounted on a support plate attached to a shaft. The magnetic rotor is surrounded by (but not attached to) a nonmetallic shell which supports the conveyor belt. This allows the rotor to spin independently and at a much higher speed than the nonmetallic shell and belt.
When a piece of nonferrous metal, such as aluminum, passes over the separator, the magnets inside the shell rotate past the aluminum at high speed. This forms eddy currents in the aluminum, which in turn create a magnetic field around the piece of aluminum. The polarity of that magnetic field is the same as the rotating magnet, causing the aluminum to be repelled away from the magnet. This repulsion makes the trajectory of the aluminum greater than that of the nonmetallics, allowing the two material streams to be separated.
Eddy current separators are widely used in the automobile shredding industry to separate nonferrous material from nonmetallics such as foam, plastic and carpeting found in auto shredder fluff.
PURCHASE CONSIDERATIONS
When considering the purchase of an eddy current separator, there are four important areas to consider: type of material to be sorted, size of material to be sorted, material configuration, and burden depth.
One of the easiest materials to separate is aluminum, due to its light weight and high conductivity. Copper can be separated because it has high conductivity, but it is more difficult than aluminum because of its heavy weight. Although they are nonferrous metals, stainless steel 302 and 304 are difficult to separate because of their high resistance to current flow. Die cast metal, or white metal, is another ideal candidate for eddy current separation. Its light weight and high conductivity allow the formation of high current and large force. There are other nonferrous metals, such as zinc, titanium, magnesium, bronze, and brass, which may be separable.
A large piece of nonferrous metal will generate more current and therefore more force for repulsion than a small piece. Generally speaking, ½-inch and larger pieces are separable. Smaller pieces may be separable under certain conditions and depending on the type of material. Air resistance to the small pieces can make separation difficult or impossible because the eddy current force is so small.
Nonferrous metal trapped in nonmetallic material may be impossible to separate. Small scraps of aluminum that are embedded or trapped in fabric, foam, or plastic usually are not recoverable. Copper wire covered with heavy insulation cannot be separated. And although aluminum cans are very easy to separate, a full soda can is not recoverable – the weight of the soda, or nonmetallic material, is much greater than the repelling force affecting the aluminum.
It is important to load the separator’s conveyor belt as uniformly and as lightly as possible. If large surges occur, nonferrous metal will be under other material. This can weigh it down and cause a decrease in its trajectory, which may result in the piece not making it over the splitter and not being recovered.
When using an eddy current separator on ASR, it is important to remove all possible ferrous metal from the material. Large pieces of steel can crush the wear cover of the rotor, and even small ferrous particles can accelerate wear on the rotor cover and the belt.
Auto shredders usually have one or two large diameter magnetic drums recovering ferrous after the car has been shredded. In addition, a magnetic head pulley should be installed. If large and strong enough, this pulley will remove almost all the ferrous material that is left.
Manufacturers also use a variety of designs to ensure that the magnetic rotor is not damaged from any ferrous debris that remains in the burden. One manufacturer has patented a heavy-duty triple shell for the rotor; another uses a Kevlar protective layer. Other features that keep ferrous from getting under the conveyor belt and onto the rotor include a four-pulley arrangement for the conveyor or an eccentric configuration for the rotor and shell.
In eddy current separators with a concentric rotor design, the magnet is placed in the center of the outer shell (pulley) so that the alternating magnetic field encompasses the whole 360 degrees of the shell. In eddy current separators with an eccentric rotor design, the magnet is located off-center so that the magnet only touches on a tangent of the outer shell. This design can result in more efficient discharge of ferrous materials, since they leave the magnetic field sooner. Eccentric rotors are usually adjustable.
BEYOND AUTOMOBILE SHREDDING
In addition to recovering nonferrous metals from auto shredder fluff, eddy current separators are also used for applications such as separating aluminum cans from municipal solid waste (MSW); removing metal contaminants from plastics; extracting metallic contaminants from glass cullet; and concentrating metallics in electronic scrap.
An eddy current separator is typically installed at the end of the processing line to remove aluminum cans from MRF residue. More heavy-duty eddy current separators are also installed at MSW plants to remove aluminum cans from garbage.
Another application for eddy current separators is in removing contaminants from polyethylene terephthalate (PET) beverage containers. Shredded PET is processed over special eddy current separators to remove small, fingernail-sized aluminum fragments (from cans and bottle caps). Eddy current separators are also used to reduce metal contaminants in glass cullet.
These applications often involve separating smaller nonferrous metals (less than 1 to 1/2 inches). These materials usually respond better to very strong eddy current fields (3,000 to 5,500 gauss in the operating zone) and/or higher frequency eddy current fields. To obtain stronger eddy current fields requires more rare earth (RE) magnet material in the rotor assembly, and strong, stable quality RE magnets are expensive. But these higher priced units generate increased nonferrous metal recoveries or more value, so the increased payback offsets the higher equipment costs. High frequency eddy current separators use more magnetic poles and are often driven at higher rotations per minute.
Some of the newer rotor designs incorporate curved rare earth magnets and up to 22 poles for a frequency of 28600. This type of rotor design is very cost effective and offers excellent performance in separating smaller particles.
A typical eddy current separator will handle between 1 to 20 tons per hour per foot (TPH/F) of width; PET is 3/4 TPH/F, commingled MRF residue is 1 to 2 TPH/F, and glass cullet is 5 to 8 TPH/F. Product size, density or pounds per cubic foot, size and percentage of metals, and recovery required all affect eddy current separator capacity.
To determine the size – and therefore the cost – of an eddy current separator, consider the type and density of the material, tons per hour processed (including average and peak rates), and specific information about the application. Additional equipment may be required to complete the system, such as a magnetic separator, vibratory feeder, transfer conveyor, holding bins, and material handling equipment.
The price for a small rare earth eddy current separator for a MRF can start at $35,000, while a larger separator for more severe-duty applications can cost up to $160,000.
The section on auto shredder applications was contributed by William Barrett, director of new product development for Dings Co. Magnetic Group, Milwaukee. The section on applications beyond auto shredding was contributed by Al Gedgaudas, recycling equipment manager for Eriez Magnetics, Erie, Pa.
Enhancing Eddy Performance
There are certain basic procedures that will enhance the performance of an eddy current separator. The most important is to remove as much ferrous material as possible from the stream. Ferrous particles in the product will effect separation and could cause serious damage to the unit if unnoticed. The next step is to remove the fines (generally particles between 3/8 inch and ½ inch), which normally represent 20 percent to 40 percent (by weight) of the stream to be processed.
It is important when applying an eddy current separator that you size it properly. Don’t be concerned about the diameter or the width of the unit. The separator’s rated capacity should be the prime factor. Separators generally are available in widths ranging from 24 inches to 60 inches. However, it is not uncommon for a 48-inch wide unit to have a higher capacity than a 60-inch wide unit, as the effective distance that the eddy current’s range out from the surface of the belt varies depending on the manufacturer.
Some units achieve effective separation at a distance of 1 inch to 2 inches, while others operate well at 3 inches or more. This distance determines the depth of the burden that the unit can handle, and the depth of the burden generally is a factor in determining the unit’s rated capacity in tons per hour.
It is very important to spread the burden depth evenly across the width of the belt and reduce surges. A mechanical or vibratory feeder generally works best – feeding the unit directly off the end of a conveyor is not recommended. All eddy current machines have a specified working width. The strength of the magnetic flux (the eddy currents) is consistent across this width. Use it all – even when feeding the eddy current below its rated capacity, if the material is not distributed evenly across the working width, effective separation will not be achieved.
An eddy current separator can process both wet and dry material. However, there are advantages to processing dry material. Fines removal is less effective in wet material. Even if the wet fines pose no hazard to the rotor itself, the fines will build up on the belt surface, reducing the separator’s capacity by 50 percent or more. Also, processing wet material requires more maintenance and frequent inspections between maintenance. By Richard Grisier, manager of the Magnetics Division of Huron Valley Steel, Belleville, Mich.
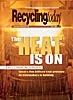
Explore the July 2001 Issue
Check out more from this issue and find your next story to read.
Latest from Recycling Today
- Athens Services terminates contract with San Marino, California
- Partners develop specialty response vehicles for LIB fires
- Sonoco cites OCC shortage for price hike in Europe
- British Steel mill’s future up in the air
- Tomra applies GAINnext AI technology to upgrade wrought aluminum scrap
- Redwood Materials partners with Isuzu Commercial Truck
- The push for more supply
- ReMA PSI Chapter adds 7 members