Whether the application is at an automobile shredder yard, a material recovery facility (MRF), a C&D recycler or a slag recovery operation, magnets are capable of performing somewhere within these operations to remove or hold ferrous material.
Magnets can range in size from 88.5 tons (used at a copper mine in Chile) to small magnetic head pulleys that are only 8 inches in diameter, meaning that there is bound to be a magnet sized to accommodate the needs of most operations.

In order to size magnetic equipment properly for your shredding system, your supplier will need to know some some valuable information about your setup, including:
1. Belt width;
2. Belt speed;
3. Capacity in tons per hour;
4. Percent of magnetic material in the infeed;
5. Material description and size range;
6. Material bulk density;
7. Degree of troughing;
8. Location of the unit; and
9. Smallest realistic size of ferrous material to be removed.
VARIETY SHOW. The magnets most commonly seen in recycling operations are the large diameter units used to lift tons of bulk scrap to load or to stockpile material. However, often overlooked are the magnetic pulleys that are used in conveyor applications, whereby the conveyor is transformed into a magnetic separation device.
In the separation system downstream from an auto shredder, suspended magnets remove ferrous material from residue conveyors, and shredder drum systems are the heart of the ferrous recovery operation. Finally, the eddy current separators and all-metal units recover the balance of nonferrous material. Many operators think that if they have a standard diameter head pulley in their present systems, they can ask for a magnetic pulley of the same size. However, this is not the case. The magnetic pulley has two functions; one is to drive the conveyor, just as a standard pulley does, but its second function is to remove ferrous material.
Let’s say you are running a belt at 250 feet per minute (FPM) on a 15-inch diameter standard pulley. If a 15-inch diameter magnetic head pulley was used in this application, magnetic material could be lost because the centrifugal forces may be in excess of the magnetic force allowed in the volume available for magnets contained within the enclosure. This application would call for a minimum of a 20-inch diameter magnetic pulley.
If the material is being introduced to the pulley at the 12 o’clock position, the pulley acts as a recovery device as it grabs, holds and carries the ferrous material. A magnetic pulley has one drawback, however, as it also has a tendency to entrap non-magnetic material, reducing the purity of the recovered ferrous. A magnetic head pulley is most effective when the percentage of ferrous in the feed material is no more than 30 percent or 35 percent ferrous.
Suspended separation magnets also require special selection criteria to provide optimum performance. Such a magnet is suspended either directly over a conveyor or above the head pulley trajectory because the material is in flight and directed toward the magnet face. Manually cleaned and self-cleaning units are available. Manually cleaned suspended magnets accumulate the ferrous material, which is then discharged into containers. The self-cleaning units will discharge the magnetic material either off to the side of the conveyor or forward of the base material trajectory.
BEAST OF BURDEN. The magnetic drums used in the ferrous recovery portion of a shredder’s downstream system are to be considered next. Whether you design this portion of the system with one drum, two drums or even three drums, how the material is presented to each drum is of major consideration. There are systems that use belt conveyors to feed primary or secondary drums, and there are systems that use oscillatory feeders to present the material to the drum.
Let’s assume that we have a shredder handling 50 TPH of average capacity. Most belt conveyors feeding the primary drum are flat belts with side skirts to confine the material. If the belt feeding the primary magnet is 60 inches wide and traveling at 250 feet per minute (FPM), the following would be true: 50 TPH x 2,000 PPT divided by 60 minutes/hour times 75 PCF equals 22 CFM (where 50 is the capacity in tons/hour, there are 2,000 pounds per ton, 60 minutes per hour, 75 pounds per cubic foot [PCF] of feed density and volume is measured in cubic feet per minute [CFM]).
What this means is the feed is pretty well distributed across the belt width. If you reduce the belt speed, the average depth increases and if you decrease belt width, the depth increases. By the same token, if an oscillatory feeder is used between the main conveyor and the drum, its speed might be only 35 to 50 FPM.
Now, if the feeder is the same width (60 inches) as the incoming conveyor, the material depth in the pan now increases to five times (at 50 FPM) or an average burden of 1.05 inches. Of course, we recognize that the particle size is greater (nearer to 4 inches), but it gives you some idea of the distribution of material on the belt or pan. The closer the average burden approaches the particle size, the more entrapment can occur with nonferrous material. Remember, the ferrous particles become magnets and attract each other. This is known as the stringing effect.
If the distance from the feed point is increased, then larger diameter drums are required.
The rule of thumb Walker Magnetics uses is as follows:
• 36-inch diameter – 6 inches to 8 inches;
• 42-inch diameter – 8 inches to 10 inches;
• 48-inch diameter – 10 inches to 12 inches;
• 60-inch diameter – 12 inches to 14 inches; and
• 72-inch diameter – 16 inches to 18 inches.
MATTERS OF SIZE. The smallest realistic ferrous material to be removed is of tremendous significance when selecting suspended separation magnets. Remember this about ferrous removal with magnets: "Small is Hard" but "Big is Easy." This means that it requires more magnetic strength to remove a small piece of ferrous, like a ½-inch-by-3-inch bolt, compared to a large piece of material, like a 1-inch-by-6inch-by-6-inch plate.
Shape also has a role in the magnetic separation of ferrous material. The following are relative figures for the strength required to remove various pieces of ferrous from a bare belt:
• Sphere, 85;
• Cube, 66; and
• Nut, 42.
You can see that it requires nearly twice the strength to remove a sphere shape than a nut shape.
The type of scrap being processed or shredded has an influence on material recovery. If the product being shredded takes the form of a dense sphere shape, it may be lost but later recovered by a magnetic pulley. Long pieces, such as leaf springs or pipe shapes, would be better processed by radial pole drums, which orient the material across the drum width rather than along the drum circumference.
The more we know about what you intend to shred or process provides us the opportunity to recommend the best equipment for the application.
MINING FOR NONFERROUS. Eddy current (EC) separation for nonferrous metals also requires some knowledge of feed devices. An eddy current separator for scrap recovery generally has variable belt speeds and variable rotor speeds. In most instances, the rotor speed is maintained at maximum speed because the number of pole cuts per minute influences the affect on the particle. The belt speed controls the volume of material on the belt introduced to the rotor.
Let’s say you want to treat 20 tons per hour of residue. You’d use a nominal belt speed of 200 FPM. Say you want to limit the average burden to ½ inch deep and the material density is assumed to be 40 PCF. The following is the appropriate calculation for the size of an EC unit: 20 TPH times 2,000 PPT divided by 60 minutes/hour times 40 PCF equals 16.7 CFM.
One-half inch of depth times 200 FPM divided by 12 inches per foot equals 8.3 square feet per minute.
Therefore, 16.7 CFM divided by 8.3 equals a 2-foot wide separator.
How about the feed arrangement to the unit? Normally, oscillatory feeders are used and they only travel at 35 FPM. With 4-inch to 6-inch high sides, you carry an average of burden of 2 inches: Two inches of depth times 35 divided by 12 inches equals 5.83 square feet per minute.
Therefore, 16.7 CFM divided by 5.83 SFPM (square feet per minute) equals a 2.86-foot wide feeder.
In this case, the feeder belt size would determine the width of the eddy current unit, about 2 ½ feet wide.
Initially EC units attributed part of their success to recovering stainless steel. But few people were aware of the problems encountered.
Type 300 Series stainless steel when work hardened, as it is in a shredder, changes characteristics from austenitic (non-magnetic) to martensitic (partially magnetic). If this has occurred to some of the stainless, then, using a rare earth rotor, the material would not be thrown but attracted and would end up in the ferrous or nonmetallic bin.
This factor led to the development of the all-metal sorting unit, which uses detection sensors to remove the final nonferrous metals.
Recyclers don’t just turn to magnets for their sorting capabilites, but also for their ability to lift material.
NEED A LIFT? As familiar as lifting magnets are to the scrap industry, a supplier of these units will want to know the type of material to be handled because different bulk densities will affect the load. The crane type and manufacturer is significant in specifying duty cycle and payload.
Scrap recyclers should keep the above criteria in mind when shopping for magnets to handle sorting and material handling tasks to select the most appropriate equipment.
The author is product manager and magnetic separation specialist for Walker Magnetics, Worcester, Mass., and can be reached at mormag@earthlink.net.
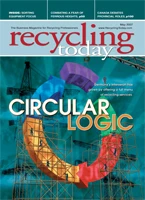
Explore the May 2007 Issue
Check out more from this issue and find your next story to read.
Latest from Recycling Today
- OnePlanet Solar Recycling closes $7M seed financing round
- AMCS launches AMCS Platform Spring 2025 update
- Cyclic Materials to build rare earth recycling facility in Mesa, Arizona
- Ecobat’s Seculene product earns recognition for flame-retardant properties
- IWS’ newest MRF is part of its broader strategy to modernize waste management infrastructure
- PCA reports profitable Q1
- British Steel mill subject of UK government intervention
- NRC seeks speakers for October event